In recent years, the concept of editing has evolved. The world has gone from simple editing processes and tools to more advanced and sophisticated ones. One of the most advanced machining processes available today is 5-axis machining.
However, sometimes when talking about special 5-axis CNC machining, the first impression that comes to most people's minds is: high technology, high price and difficult to use, but is 5-axis machining really like that?
Read on as we provide answers to this question and other important information about this issue.
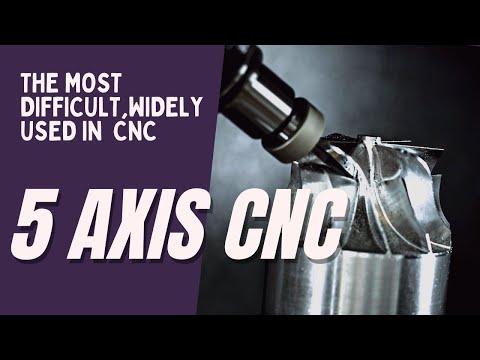
What is 5 axis machining?
This type of machining is based on a tool that moves in five different directions around which it rotates. It is a multi-axis subtractive manufacturing process in which the machine shapes the part material and moves in 5 directions or vertically.
Movement directions include This eliminates the need to manually reposition the part between operations. It also saves time and is ideal for producing highly complex parts that require precision.
What does the “5” on axis 5 mean?
5-in-5 axes means that 5-axis machining machines have two additional axes in addition to the traditional 3 axes of X, Y, and Z, giving them a total of 5 axes. The 4th axis is the A axis, which denotes rotation around the X axis, while the 5th axis is the B axis, which denotes rotation around the Y axis.
This additional axis improves the type of work a machine can perform and the level of detail it can cut.
Why use CNC for 5-axis machining?
5-axis machining is performed on a CNC machine. A 5-axis CNC machine offers three linear axes and two rotary axes that work together to produce highly complex parts. By adding a 5th axis to this machine, engineers and machinists can work on up to 5 faces of a part in a single operation.
5-axis CNC machining is beneficial to manufacturers because it saves manufacturing time and costs while ensuring products reach the market faster. Also note that the type and configuration of the CNC machine determines its overall speed and direction.
How does a 5 axis CNC machine work?
A 5-axis CNC machine works automatically with minimal human intervention. It uses rotating cutting tools to shape materials placed on the machine plate.
However, placing the material on the plate is the final step of the 5-axis CNC machining process. The first step in 5-axis CNC machining is to create a CAD design of the part and translate it into CAM. CAM or computer-aided manufacturing is a software that helps to generate an alphanumeric CNC language or G-code.
The next phase of the process is to send the G code to the 5-axis CNC machine. G code is very important because it contains instructions that direct the machine to the correct tool path and tool for machining.
Types of 5 Axis CNC Machines
There are some operations where 5-axis CNC machines can save you a lot of time and improve your current workflow. These machines come in various versions to meet the needs of the growing manufacturing industry. A unique difference in 5-axis CNC machines is the arrangement of the rotary axes.
head, head
In this type of CNC machine, the head houses the rotation axes. In this part, because the 5-axis apex is on a specific platform, you don't need to worry about the tool interfering with the machine spindle head. Another reason not to worry about interference is that this 5-axis apex moves across a fixed table that ensures the part stays in place.
This type of 5-axis machine design allows the tip to move around a specific part during machining. Therefore, head-to-head CNC machines are ideal for producing large parts. However, movement along the rotation axes is restricted in this design.
Table/header
There are also two axes of rotation in this configuration, one axis of rotation is located at the head and the other at the turntable. The head is where the axis of rotation is located and due to the position of this axis it has a restricted range. On the other hand, there is no limit to the range of the rotary axis placed on the table.
An advantage of this configuration over the head/head system is that there is no need to worry about reaching a certain limit, as the parts are constantly rotating. On the other hand, because the part or part rests on the axis of rotation, the design of the CNC machine limits the number of parts it can produce.
Table/desk
With this configuration, both axes of rotation are on the table. The range of the rotation axis is very limited here, but the range of the rotation axis is unlimited. This makes this type of machine ideal for processing undercuts. Additionally, the desk/desk arrangement has a minimal work area compared to other machine arrangements.
Additionally, it is slower than other machines because it is not equipped with the engines that make other machines faster. It is also less suitable for processing large or heavy components because it cannot support much weight.
Get a free quote!

Advantages of 5-axis CNC machining
The ability to work on 5 different surfaces of a part at the same time with this type of machining offers several advantages for many industries. These benefits range from cost efficiency to effective processing. Here are the main benefits of 5-axis CNC machining.
1. Machining complex shapes
The additional axis of this machine facilitates the processing of highly complex designs and geometries. Machining difficult angles and arcs, which was previously possible with various specialized devices, has also become possible with 5-axis CNC machines. Additionally, this machine's ability to turn parts during a single operation allows desired geometries to be achieved without the use of complex machines or devices.
2. High precision and repeatability
Manual editing operations require additional settings for optimal editing. However, these additional settings often introduce variability and errors into the design, causing machine operators to lose alignment during machining. However, 5-axis CNC milling requires minimal adjustments, eliminating the possibility of errors and improving accuracy.
Additionally, with most 5-axis CNC machines used by machinists today, there is no need to manually reposition the part during machining. This guarantees better machining tolerances. Additionally, the use of shorter cutting tools in some machine configurations improves tool life and ensures repeatability.
3. Effective configuration operations
Setting up a 5-axis CNC machine is relatively easier than setting up a 3-axis machine. The reason for this is that 5-axis CNC machines allow you to machine five surfaces at the same time. Furthermore, 5-axis machines allow you to machine contour parts with a unique structure. However, traditional 3-axis machines require multiple settings to work on multiple surfaces.
4. High quality surface finishing
The surface finish of a 5-axis CNC machine is smoother due to the additional axes. These additional axes bring the part closer to the cutting tool, making it easier to obtain the desired shapes. Additionally, shorter cutting tools can be used for machining.
Shorter cutting tools experience little or no vibration, reducing the number of marks on the surface of finished products. Furthermore, vertical machining improves spindle utilization when machining angular surfaces.
5. High production efficiency
5-axis machining can effectively reduce machining time and non-productive time of parts. It has a wide spindle speed and feed range, allowing the machine to deliver great and powerful cutting performance. 5-axis CNC enters an era of high-speed machining. The rapid movement and positioning of 5-axis machining and high-speed cutting processing shorten the delivery time for semi-finished products.
Disadvantages of 5-axis CNC machining
5-axis machining offers many advantages and is very important in parts manufacturing. However, not everything is good with 5-axis machining as it also has some disadvantages. Below are the disadvantages associated with 5-axis machining:
1. High cost
The costs of purchasing a 5-axis CNC machine are significantly higher than those of a 3-axis machine. The same applies to the software required to operate this machine. Furthermore, the maintenance of 5-axis CNC machines is more difficult than the maintenance of CNC machines. Therefore, cost is one of the biggest disadvantages of using 5-axis CNC machines for machining.
2. Programming complexity
The programming required for 3-axis machines is different from that required for 5-axis machines. This is mainly due to the addition of two rotational movements, which complicates the trajectory of the synthetic movement formed.
For example, when programming the 5 axes, the respective movement of each axis should be taken into account to avoid collisions and interference. Achieving better surface quality and precision also requires more complex programming.
3. Requires a high level of operator competence
The latest technology is used in 5-axis CNC machining. Therefore, to make the most of the machine, a highly qualified technical operator is required. However, using a highly skilled operator also increases labor costs.
What kind of parts can be machined with a 5-axis machining center?
Many different parts can be produced using 5-axis CNC machining. These parts often have complex geometries and complicated shapes. Here are some parts you can machine using 5-axis machining.
Complex surface parts
Parts with complex surfaces are parts commonly found in various fields, including aviation, space, electronics, etc. It is difficult to obtain these complex surfaces with ordinary CNC machine tools. Common complex surfaces that can be produced using 5-axis machining include spherical surfaces, turbine engine blades, ship propellers, impellers, etc.
disk parts
5-axis CNC machining is also ideal for machining UAV parts. It is suitable for processing sheet and plate parts, especially those with front distribution holes or radial holes. It is also suitable for making engine covers. It is important to note that applying 5-axis CNC machining to such parts requires the use of a horizontal or vertical machining center. The machining center chosen depends on the respective hole direction.
Box type parts
Using common machining tools for box-shaped parts is relatively difficult due to the multiple clamping and alignment required. The ability of a 5-axis machine to machine multiple surfaces simultaneously facilitates the production of high-precision box-shaped parts.
Special molded parts
Special shaped parts are irregularly shaped parts. For example, workpieces with mixed points, surfaces and lines. Machining these parts with conventional machining is difficult or almost impossible because the clamping pressure is difficult to control during the process. However, with 5-axis machining, it is easier to complete the process with a multi-station point.
Difference between 5-axis and 3+2-axis machining
Most people don't know that there are differences between 5-axis machining and 3+2-axis machining, or even between 3-, 4-, and 5-axis CNC. In 5-axis machining, the cutting tool rotates continuously along the 5 axes.
In 3+2 axis machining, however, the machine runs a 3-axis program with the cutting tool locked at an angle. Furthermore, the locking angle depends on the two axes of rotation.
Speed is the main advantage of 5-axis machining over 3+2-axis CNC machining. The difference in speed is due to the fact that in 3+2 axis machining the machine must be constantly stopped and restarted to ensure ideal tool alignment. In 5-axis CNC machining, there are no stops, as machining is done in a single operation.
Strategies to Make the Most of 5-Axis CNC
Since most operators are unaware of all the features of a 5-axis CNC machine, here are some strategies that can help you make the most of a 5-axis CNC machine.
Choose the right software and controls
Before choosing a 5 axis CNC milling machine, you need to get the right information. To do this, you must analyze project data for precision and accuracy. It is also important to review the design process before transferring the CAD design to the CAM equivalent.
With the right information, you can select the ideal CAD/CAM software and controls to complete your design task. The software is simulation software to monitor part size, interference and tool length.
Furthermore, with this information it is possible to carry out a cost analysis to ensure that the correct and most cost-effective process is used for the job.
Choose a tool recognition system
Using the wrong tool for the job increases the risk of mistakes. Furthermore, the wrong tool would easily wear out or break during processing, increasing production costs and reducing product quality. One way to reduce this is to use a tool recognition system. This system helps you analyze which tool to use, ensures it is the right tool for the job, and minimizes errors.
Avoid collisions
Collisions result in faulty components or a damaged machine. Fortunately, there are software tools that can mitigate this risk. How does this work? This software simulates the design process and often detects the collision before it occurs so that the design command can be changed. There are many software of this type, but among the most popular are Predator and ModuleWorks.
Industrial applications that benefit from 5-axis CNC
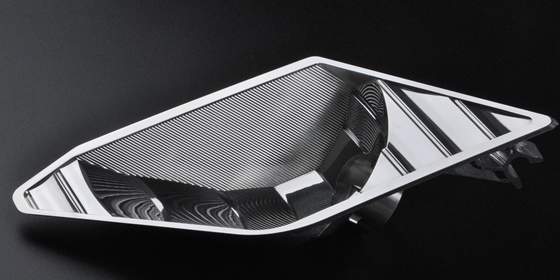
5-axis CNC machining offers numerous benefits to the industry, from reduced human error to high quality and consistent products. Several industries use this type of machining to produce their products and components, but the most important are:
Medical industry
Because the failure of a part during a surgical procedure, test or diagnosis of a disease can spell disaster, precision and accuracy are of utmost importance in this industry. 5-axis CNC machining is used in the medical industry to produce research equipment, MRI machines, surgical implants, medical instruments and orthotics.
Electronic equipment
Electronic devices are an essential part of our daily lives as they are part of commercial and consumer goods. 5-axis CNC machining facilitates the production of even the smallest components necessary for the proper functioning of these electronic devices. It is used in the production of electronic boxes, semiconductors, hardware, metal fins, heat sinks and circuit boards.
Energy industry
To avoid catastrophic failures, energy industry parts must meet demanding standards and specifications. If the parts used in this industry do not fit, this often leads to the failure of entire systems, which leads to lost sales for the affected companies. This industry uses 5-axis machining to produce drills, pistons, rods, cylinders and valves.
aerospace industry
This industry requires parts with compound shapes and contoured edges. The use of complex geometric shapes also makes 5-axis machining the preferred process for machinists in this industry. Additionally, 5-axis machining facilitates the production of high-quality parts and allows industry standards to be met.
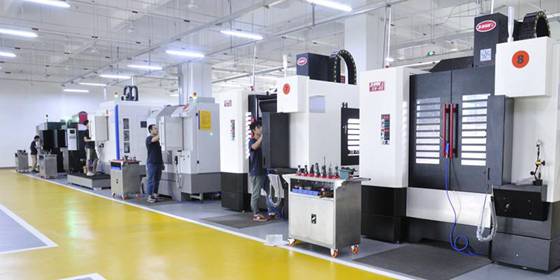
Get started with 5-axis machining at WayKen
5-axis CNC machining makes the machining process easier, faster and more economical. It also improves precision and accuracy. However, to make the most of this process, you need an expert.
Concluding
5-axis CNC machining allows the production of complex parts with high-quality surface finishes. Although the initial cost is high, this processing helps save time and money in the long run. Due to the high-precision parts, this is a machining process that has applications in a variety of industries, including aerospace, electronics, and medical.
Common questions
What language do 5 axis CNC machines use?
The basic machine code for 5 axis CNC machine is G code. G code contains a series of instructions to control the machine's cutting tool.
What materials are used in 5 axis CNC machining?
You can use almost any material on a 5-axis CNC machine. However, common materials include metals such as aluminum, brass, copper, titanium and steel, as well as plastics such as polypropylene, ABS, PC, nylon, POM, etc.