If this is the first time you have encountered the term “press brake,” you may not be familiar with its meaning and may not immediately associate it with a machine used to bend sheet metal.
So, let's start by defining what a press brake is.
A press brake is a metalworking machine designed to bend sheets and plates, primarily steel, by clamping the workpiece between a corresponding punch and die, forming predetermined bends. This tool is fundamental in the metal-mechanical industries, frequently used in the production of components for vehicles, aircraft and construction equipment.
What is a press brake?
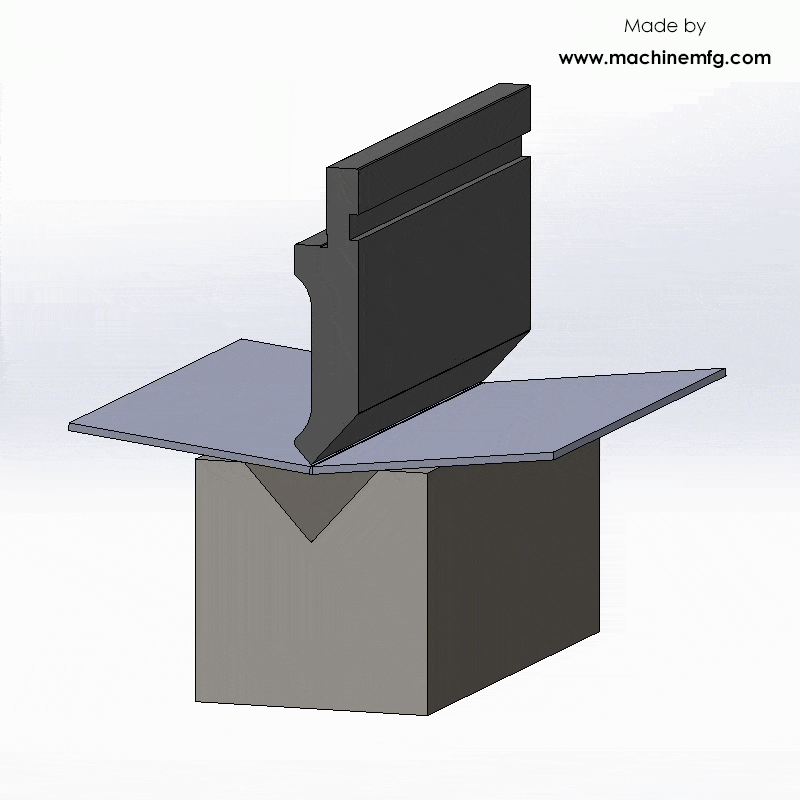
In the metalworking industry, a press brake refers to a specialized machine tool designed to bend sheet metal and sheet materials, with sheet metal being the most commonly used material.
This machine tool employs a clamping technique in which the part is clamped between a punch and a die that correspond to each other, allowing the creation of precise and precise bends.
Related reading: What is press braking?
Types of press brakes
Currently, there are five types of press brakes widely used on the market, each with its own advantages, disadvantages and usage scenarios.
Of course, the hydraulic press brake is still the most popular today. Following are the five main types of press brakes:
Mechanical press brakes operate using a flywheel and crank mechanism to generate the force needed to bend the metal. They are known for their speed and accuracy.
Hydraulic presses use hydraulic cylinders to generate the force needed to bend metal. They are known for their power and versatility.
Pneumatic press brakes employ compressed air to generate the force needed to bend the metal. They are known for their speed and ease of use.
Electric press brakes use an electric motor to generate the force needed to bend the metal. They are known for their precision and energy efficiency.
Manual press brakes require the operator to manually apply the force necessary to bend the metal. They are known for their simplicity and affordable price.
What does a press brake do?
A press brake is a vital machine in the metallurgical industry, employed to bend and shape metal sheets or plate materials. This machine uses a hydraulic or mechanical press to apply force to the upper punch and lower die, which in turn changes the metal to a desired angle or shape.
Press brakes can be operated manually or using a computer numerical control (CNC) or numerical control (NC) controller, allowing for more precise and complex bending operations. These controllers allow the operator to input specific bending parameters such as angle and bend depth, resulting in highly accurate and repeatable results.
To better understand how a press brake works, we recommend watching the following video.
After watching the video mentioned above, I'm sure you now have a more comprehensive understanding of the purpose and functionality of a press brake.
Why is it called a press brake?
As we delve deeper into the topic of press brakes, a common question that comes up is why they are called “press brakes” instead of simply being called press brakes.
In modern times, the term “press brake” is used to describe a hydraulic press brake designed specifically for bending sheet metal.
However, the origins of the term may not be immediately clear to everyone.
Like many, I was also perplexed by the use of the term “folder”. This made me question whether the term was an accurate description of the hydraulic press brake.
After conducting extensive research on the subject, I finally discovered the answer.
It is important to note that the term “press break” is incorrect, as nothing is being broken or shattered.
So why is it called a press brake? Let's explore this question in more depth.
“Press Brake” Development
It is commonly understood that the word “brake” in modern usage means to slow down or stop. However, in the 15th century, the definition of “brake” was very different. It was used to describe an instrument for crushing or hitting.
Over time, the term “brake” became associated with the machine used to crush grains. Therefore, when referring to a machine used for pressing, the term “brake press” has emerged as the simplest term to use.
Over time, the two terms became synonymous and started to have the same meaning.

The Old English verb “brecan” and its Middle English form “breken” were the predecessors of the Modern English verb “break”. They intended to violently divide solid objects into parts or destroy them.
The term “bridle” is closely related to “bridle” and has its origins in the 15th century, where it was used to describe a crushing or beating instrument. It eventually became associated with the machine used to crush grain, and later the term “brake press” was coined to describe the machine used to press and bend sheet metal.
Interestingly, in modern sheet metal bending, the Middle English verb “to break” or “to break” is used to refer to bending, changing direction, or deviating. Even a beam of light can be “broken” using a mirror.
Therefore, it can be said that the verb “brake” in the context of a press brake refers to a machine that bends sheet metal.

You may be curious as to why the term “press brake” includes the word “press.”
In the 13th century, “presse” was used as a noun meaning “to crush or crowd together.” Later, in the 14th century, “press” was used to refer to a device for pressing clothes or squeezing juice from grapes and olives.
Over time, “press” evolved to mean “a machine that applies force by squeezing.” For sheet metal manufacturers, the punches and dies that exert force on the sheet metal to bend it were called “presses.”
This is where the term “brake press” originated.
Different types of sheet metal bending machines are named based on the power source that powers the machine, the tools used to bend the metal, and the type of bend produced. For example, a leaf brake uses an upward-swinging leaf to bend the metal.
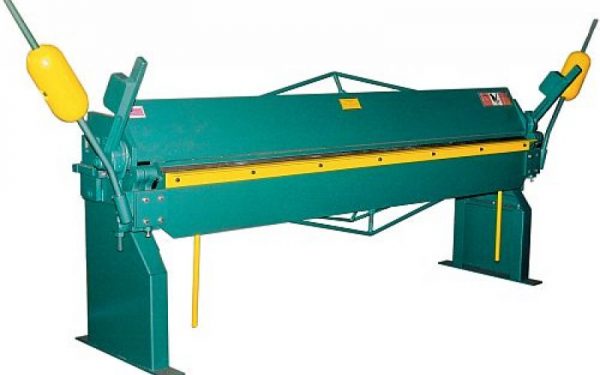
A box brake, also commonly known as a pan brake or finger brake, is a machine tool primarily used to form boxes or pans from sheet metal. This is achieved by bending the metal around the segmented fingers that are attached to the machine's upper jaw.
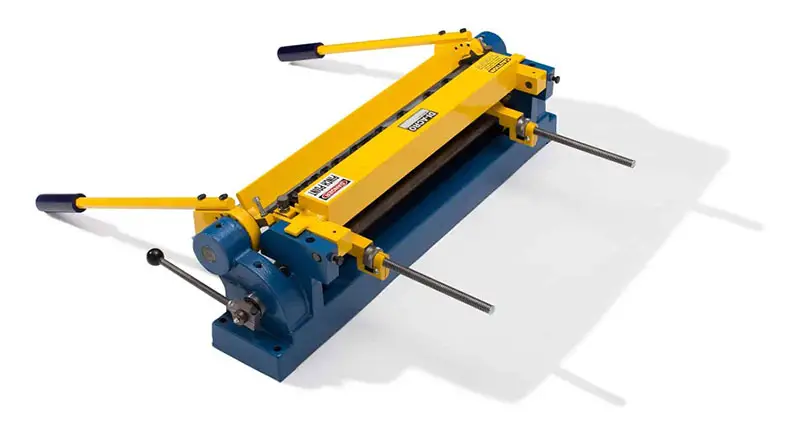
A press brake performs bending using punches and dies.
See too:
- Press Brake Dies (Tools): The Definitive Guide

Advancements in technology have led to the creation of different types of press brakes, which include manual press brakes, mechanical press brakes, hydromechanical press brakes, hydraulic press brakes, and electromechanical press brakes. Despite the different names, the term “press brake” still refers to the machine used to bend, as illustrated in the video below.
Brake Press vs Brake Press
The terms “Brake Press” and “Brake Press” are often used interchangeably to refer to the same machine. A press brake is a machine used to bend metal sheets and plates, most commonly sheet metal. It forms predetermined curves by clamping the workpiece between a corresponding upper tool and lower die. There are several types of press brakes, including hydraulic, synchronous-hydraulic, electric and hybrid nut brakes.
Press brakes use a similar mechanism to stamping presses to manipulate the shape of a workpiece, but press brakes are designed exclusively for metal parts. In recent years, hydraulic and CNC press brakes have gained momentum among manufacturing companies.
So whether you call it a “Brake Press” or a “Brake Press,” they refer to the same machine used to bend and deform metal parts.
Conclusion
Now that we better understand what a press brake is and why it is called as such, those looking for more comprehensive information on press brakes can consult the definitive guide to press brakes. This guide covers in-depth details about different types of press brakes, their working principles, tools, applications, training, programming and also provides valuable tips.