CNC machining is a pillar of industrial manufacturing due to its high functionality and precision, among other advantages. When producing a product, manufacturers may utilize one or more machining operations, such as: B. CNC turning and CNC milling operations.
The definition of CNC turning involves removing pieces of material while the part rotates against the cutting tool. This article describes CNC turning comprehensively – the process, the machines for the process, and its application. So without further ado, let's get started with this.
What is CNC turning?
CNC turning is a typical subtractive manufacturing process that uses a cutting tool to remove portions of a material from the exterior. The part rotates (continues to rotate) as the pieces are chipped until they reach the desired shape, diameter and size of the final product.
However, the cutting tool, usually a single-bladed end, is not rotatable. Instead, the part only rotates around the tool. CNC lathes are the typical machines used industrially for turning operations.
CNC turning is now suitable for cutting metals, wood, plastics and other polymers. As this process uses computer-generated programs and codes, the products also have high dimensional accuracy – one of their main advantages.
Understand the fundamentals of CNC turning
CNC turning operations can be quite complicated. However, after converting your CAD files into a CNC machine-readable program, you need to set up the machine to begin the turning process.
Turning involves twisting and turning a workpiece as the cutting tool begins to cut pieces of material from the outside. Normally the processed material is cylindrical or round. However, in some cases, especially when using a compatible adapter, turning can also work well on materials of different shapes.
The cutting tool continues to make cuts as the part rotates in the machine until it reaches the desired programmed shape. In particular, CNC lathes or turning centers have different tools in the turret, all controlled by computer programs and codes. However, machines that can hold more tools are more sophisticated and have more features, which makes them more suitable for complex projects.
Types of CNC Turning Operations
CNC lathes and lathes come in different versions. Some have unique cutting features, making them ideal for specific operations. Below is a brief description of the different types of CNC turning processes.
Turn straight
Longitudinal turning uses a cutting tool to uniformly reduce the diameter of a workpiece. The aim of this technique is to process the material to a specific thickness. Part of the material is removed quickly, avoiding deviations in the diameter of the product. It is sometimes called rough turning and requires additional finishing to achieve dimensional accuracy.
serrated
This process involves cutting irregular, angled, or intersecting line patterns into the surface of a workpiece. The process generally ensures a firm grip as the pattern increases friction. It is also suitable for making screws and nuts for threaded holes. In particular, the process may require specially designed serrated tools.
To the next
Cutting is a machining technique that involves making deep cuts into a material using a single-edge cutting tool to remove its internal components. As the name suggests, this involves making pieces or cutting a section from the original piece.
Taper turning
Taper turning involves gradually reducing the diameter of a material from one end to the other. The angular movement between the material and the cutting tool causes the transition and reduction in the diameter of the part. As with most turning operations, the final product is cylindrical in shape.
Threading
Threading is another CNC turning process in which a cutting tool is moved along the sides of the material and cuts threads into the external components of the part. Threads are spiral-shaped grooves with specific lengths and pitches.
piercing
During this turning process, a narrow cut – a groove – is created in the workpiece. This involves pressing the pointed tool head against the material, with the cut being the same width as the cutting tool. However, using multiple cutting tools, it is possible to produce larger diameter channels.
What materials are suitable for CNC turning?
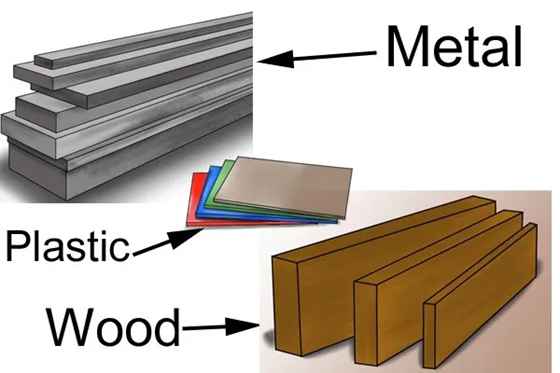
One of the main advantages of CNC machining is its compatibility with a wide range of materials. Likewise, most metal and plastic materials are ideal for CNC turning processes. They are:
- aluminum
- nylon
- copper
- steel
- Wood
- titanium
- LOOK
- Section
- Glass
- made of PVC
- Brass
- wax etc
Because each material has different structural integrity, different lathes or turning centers may be required with individual specifications such as feed rate and rotational speed.
Types of CNC lathes
Lathes are the typical turning machines. However, there are different types of these machines, each more suitable for certain turning operations. Four different types of CNC lathes are available for your machining projects.
Horizontal CNC lathes
These lathes have all the characteristics of a typical lathe, which makes them one of the most used machines for various industrial applications. However, they are suitable for both turning and drilling work. As it is also a CNC machine, it works with computer programs.
Vertical CNC lathes
Similar to a horizontal vise, but as you would expect, the main difference is the way the part is clamped. The material is positioned vertically – from below, before being twisted, spun and cut. Therefore, these machines are best suited for operations where space is limited. They are also best suited for heavy, robust parts.
Horizontal Turning Centers
Horizontal turning centers are closed devices with drilling and milling functions. As the name suggests, the turning center is oriented horizontally and tools are mounted on top as they rotate and cut the workpiece. The cuts are made by gravity.
Vertical Turning Centers
This device works as a combination of a horizontal turning center and a CNC milling machine. Due to its design, the rotating chuck is close to the ground – which makes working with large parts easier.
The different components of a lathe
Although there are different lathes, they have virtually similar components. So let's take a quick look at each element of a typical lathe.
1. CNC Control Panel
Control panels are more or less the brains of machines. They refer to the control house where machinists and technicians enter computer programs and codes. The CNC control panel has a series of buttons to control all device operations, including starting, entering new programs, and ending a project.
2. Spindles
The spindles are the heart of the head. It is the axis of rotation of a spindle lathe. Counterpoint also often has spindles.
3. Heads
The heads serve as clamps that hold other components of the lathe in place. They contain, among other things, gears, spindles, mandrels and control levers.
4. Counterpoints
The opposite end of the headstock is the tailstock. It is a non-rotating tip suitable for drilling work.
5. Beds
The bases are the most important part of any lathe, as all other components such as headstock, chuck, tailstock, etc. Furthermore, it is a large horizontal structure that can be expanded to accommodate huge parts.
6. Chuck
The chuck is another important component of the lathe. Helps hold (grasp) material for editing.
7. Promotions
The slide is located between the head and tailstock and contains other components such as saddle, cross slide and skirt. It acts as a guide for the cutting tool as it cuts the outside of the workpiece.
8. Cutting Tools
Cutting tools include tool inserts that remove pieces of material during turning. Often, the cutting and turning process depends on the type of cutting tool present on the lathe.
9. Tool Tower
The tool turrets are the tool holders of the lathe. The size and shape of a typical tool revolver determines the number of tools it can carry.
10. Pedals
The pedals help to quickly open and close the tailstock or chuck.
5 Common Types of Turning Tools
We have already established that there are different turning processes. Therefore, there are different turning tools that are best suited for each operation. Let's briefly look at some of these tools.
1. Coping tools
These are lathes suitable for cutting flat surfaces perpendicular to the axis of rotation of the material. During the process, the tool holder fixes the cutting tool in the slide, which then cuts perpendicular to the axis of rotation.
2. Thread Cutter
This cutting tool is suitable for making external and internal cuts in a material. Furthermore, as the name suggests, they are ideal for cutting threads on lathes.
3. Drill rods
Boring bars are not actually turning tools. Instead, they are single-edge tools suitable for making internal cuts in a workpiece. The devices essentially increase the diameter of an existing hole.
4. Channel Tools
Grooving tools are suitable for cutting channels (grooves) and features such as O-rings in a workpiece. Furthermore, they are ideal for creating contours in a material that allows you to gut different pieces with an excellent fit for each piece.
5. Knurled Tools
These turning tools are equipped with special designs and patterns to improve the adhesion of the workpiece. When pressed against the material, they imprint their serrated patterns. Therefore, they are useful in making handles for household appliances, screws, nuts, etc.
CNC turning applications
CNC turning and machining processes are extremely useful for many areas of manufacturing. Below we take a quick look at the applications of turning operations.
Auto Industry
CNC turning is widely used in the production of automotive components that help improve vehicle operation. The process is compatible with the production of metal components, such as cylinder blocks, and plastic components, such as panel components.
Electrical industry
CNC turning is suitable for producing circuit boards and other electrical components. As it is an extremely precise machining process, the products are electronically efficient and meet all requirements and specifications.
aerospace industry
The aviation industry requires processes such as turning and CNC machining due to their high dimensional accuracy. They are suitable for constructing steel parts for bus and aircraft fasteners and internal components.
Wayken CNC Turning Capability
We are also an ISO 90001:2015 certified company, so you can be assured that all of our products meet high industry standards. At the same time, we offer solutions adapted to your needs at competitive prices. Plus, with our DFM analysis we can offer you professional advice to improve your design.
Upload your CAD files today to receive an instant quote >>
Concluding
CNC turning is an important manufacturing technique with a wide range of applications across diverse industries. It has long been an important industrial manufacturing technique thanks to its high versatility, dimensional accuracy and suitability for large-scale production.
By reading this detailed article, you should have a complete understanding of what the process involves. Therefore, you know when to apply the technique in your production.
Common questions
What are the machining axes on lathes?
CNC lathes can come in several configurations that are best defined by the movement of the axes. This includes the following:
- 2 axes: typical of a typical lathe; the X and Y axes.
- 3-axis: Rotary drills work along the X, Y, and Z axes.
- 4-axis: includes the usual two axes and additional Y and A axes.
- 5-axis: Movement in five directions: X, Y and Z with A and B axes.
- Multi-axis: An automatic sliding lathe can have more than nine different axes.
What is the difference between turning and milling?
Turning involves turning a part against a single-edged, non-rotating cutting tool, while milling uses rotating cutters to remove components from a stationary part. Although turned products are often cylindrical or conical, milling end products have flat surfaces.
What are the three main movements in turning operations?
When rotating, the following movements occur:
- Rotation: When rotating, the workpiece rotates and rotates continuously while the cutting process takes place.
- Extended Motion: Tools are arranged parallel to the material in a straight motion that results in machining.
- Penetration: Cutting tools cut pieces of material as they penetrate, which can determine the depth of the cut.