Ultra high strength friction screw can reduce weight and increase installation space by decreasing its own size while maintaining the same clamping force. This optimization of function and volume in connected parts leads to an overall reduction in equipment weight and an improvement in performance.
What is a high strength friction screw you may ask? Allow me to explain.
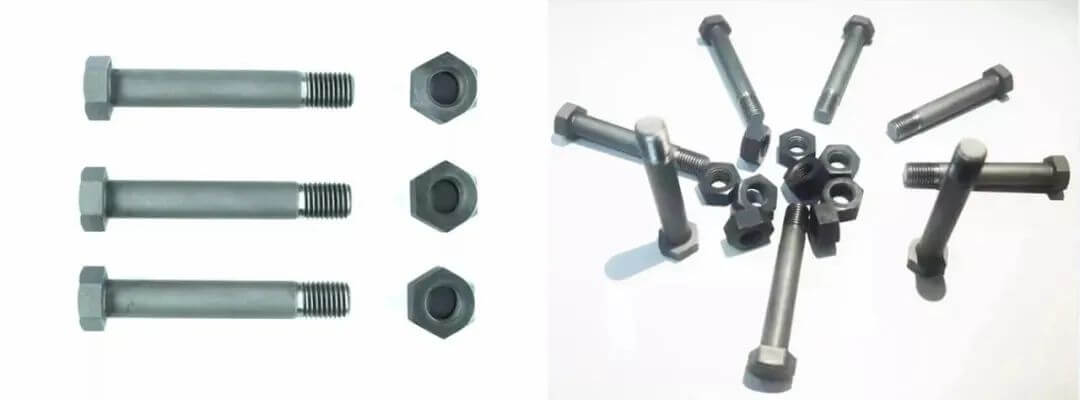
Grade 16.8 and 19.8 physical fasteners
1. What is High Strength Screw ?
A high strength bolt is also known as a high strength friction bolt, abbreviated as HSFG. In construction, the term “high-strength bolt” is often used as an abbreviation for “high-strength friction bolt.”
However, in daily communication, the words “friction” and “adhesion” are often omitted, leading to misunderstandings about the basic definition of a high-strength friction screw among many engineers and technicians.
Myth 1:
Are screws with a material grade greater than 8.8 “high strength screws”?
The main difference between high strength screws and normal screws is not the strength of the materials used, but the form of tension they can withstand. High-strength bolts are designed to apply preload and use static friction to resist shear, while normal bolts may not have these capabilities.
It is important to note that in the British standard specifications, high strength bolts (HSFG BOLT) refer to grades 8.8 and 10.9 (BS EN 14399 / ASTM-A325 and ASTM-490), while regular bolts include grades 4.6, 5.6, 8.8, 10.9, 12.9 and others (as specified in Table 2 of Clause 11 of BS 3692).
Thus, it is clear that the strength of the material is not the only factor that distinguishes high-strength screws from normal screws.
Table 2 Strength Grade Designations of Steel Bolts and Nuts
Designation of the degree of resistance | 4.6 | 4.8 | 5.6 | 5.8 | 6.8 | 8.8 | 10.9 | 12.9 |
Tensile strength R i min.N/mm 2 |
400 | 400 | 500 | 500 | 600 | 800 | 1000 | 1200 |
Yield Stress R and min.N/mm 2 |
240 | 320 | 300 | 400 | 480 | – | – | – |
Stress at permanent defined limit R 0.2 N/mm 2 |
– | – | – | – | – | 640 | 900 | 1080 |
2. What is the strength of high strength screws?
According to GB50017, calculate the tensile and shear strength of a single grade 8.8 common class B bolt and a grade 8.8 high strength bolt.
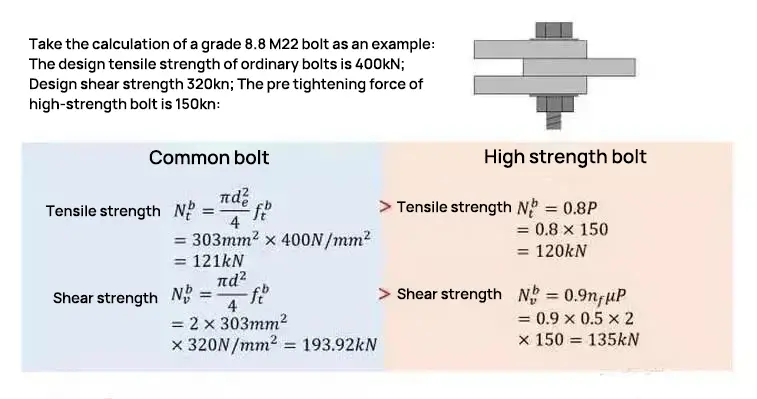
To answer the question of where the “strength” of high-strength bolts lies, it is important to first understand the design working conditions and elastic-plastic deformation laws for ordinary and high-strength bolts.
By studying the design failure limit state, we can see that although the design values of tensile and shear strength may be higher for common bolts under the same grade, the true strength of high-strength bolts lies in their ability to withstand more extreme loads. without fail.
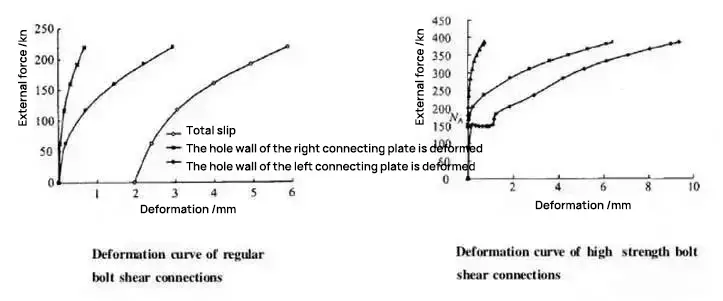
Stress-strain curves of common screws and high-strength screws under working conditions
Limit state in design failure
For a common bolt connection, the bolt itself undergoes plastic deformation that exceeds the design limit, resulting in bolt shear. During this process, relative slip occurs between the connecting plates before the bolt begins to bear shear. This results in elastic-plastic deformation and shear force support.
In contrast, for a high-strength bolted connection, the static friction between the effective friction surfaces is the initial factor supporting the shear force.
As the load increases, the friction force may become insufficient to resist the shear force and the static friction force is overcome. This results in relative displacement of the two steel plates, which is considered a flaw in design considerations.
However, even when this occurs, the screw shank may still use its own elastic-plastic deformation to support shear when it contacts the connecting plate.
Myth 2:
Is high load capacity a high strength bolt?
According to calculations for a single bolt, the design tensile and shear strength of high-strength bolts is lower than that of ordinary bolts. However, the true strength of high strength bolts lies in the design properties of the joint.
When the joint is in normal working condition, no relative slip is allowed, which means that the elastic-plastic deformation is minimal and the stiffness of the joint is high. This results in a high safety reserve for the joint, even if the number of screws cannot be reduced compared to a design using common screws.
High-strength bolts are suitable for use in main beams and other positions that require high joint stiffness, which aligns with the basic seismic design principle of having “strong nodes and weak members”.
Therefore, the strength of high strength bolts is not found in the design value of their load capacity, but rather in the great rigidity, high safety performance and strong damage resistance of their designed joints.
3. Comparison between high strength screws and common screws
Due to different design stress principles, there are significant differences in the methods used for construction inspection of common bolts and high-strength bolts.
Inspection requirements for common screws and high-strength screws
Screw | Common 8.8 | High strength 8.8 | ||||||
Standard | BS3692 | ISO898 | Trial value of a batch | BS4395-1 | ISO891 | Trial value of a batch | ||
Stretching | Yield strength | MPa | 640 | 885 | 635 | 817 | ||
Tensile strength | MPa | 830 | 959 | 827 | 944 | |||
Extensibility | % | 12 | 29 | 12 | 24 | |||
Percentage reduction in area | 52 | 53 | 52 | 58 | ||||
AKV | J. | – | – | 30J | 33J | |||
Chemical analysis | R | R | R | R | ||||
Hardness Test | CDH | 23-34 | 29.8 | 25-34 | 28.9 | |||
HV10 | 256-335 | 294 | 260-330 | – | ||||
Loading force | kN | 212 | – | 207 | – |
The mechanical performance requirements for ordinary screws of the same type are slightly higher than those for high-strength screws.
However, high strength screws have a higher requirement to accept impact energy compared to ordinary screws.
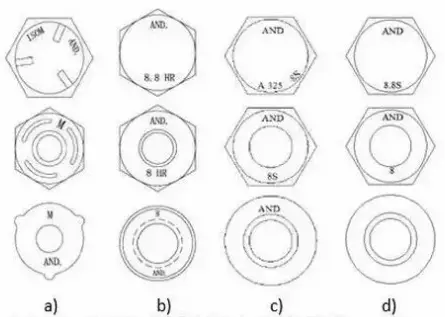
- The. Identification of pairs of high-strength screw connections, screws, nuts and washers of British standard grade 8.8 (BS4395);
- B. Identification of pairs of high-strength screw connections, screws, nuts and washers of British standard grade 8.8 (BSEN14399);
- w. Identification of pairs of high-strength threaded connections, screws, nuts and washers of the American standard Grade 8.8 (ASTM A325);
- d. Identification of common screw connection pair, screws, nuts and washers of British standard grade 8.8 (BS3692).
Marking common and high-strength screws is a basic method for identifying screws of the same type on site. It is also necessary to distinguish between high strength bolts according to British and American standards, as the calculation of torque values may differ.
In terms of cost, common screws are approximately 70% cheaper than high-strength screws. Given the comparison of their acceptance requirements, it can be concluded that the additional cost for high strength screws is to guarantee their performance in terms of impact energy (toughness).
4. How to improve the fatigue strength of screws ?
Regardless of the complex loads they support, the most common form of failure in high-strength bolts is fatigue failure.
As early as 1980, experts studied 200 cases of failures in bolted connections and found that more than 50% were due to fatigue failures.
Therefore, it is crucial to improve the fatigue strength of high-strength bolts.
Fatigue fracture of screws has the following characteristics:
- The maximum stress that causes fatigue fracture is significantly less than the strength limit of the material under static stress, and even less than the yield point.
- Fatigue fracture results in a sudden, brittle fracture without any noticeable plastic deformation.
- Fatigue fracture is the result of the accumulation of microdamage over time.
For screws, the main forms of failure are plastic deformation of the threaded part and fatigue fracture of the screw. Of these, most damage occurs as follows:
- 65% on the first thread connected with the nut
- 20% on the transition between the thread and the polished rod
- 15% on the fillet between the screw head and the screw.
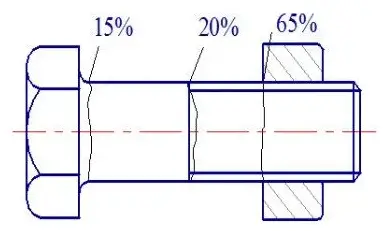
1. Optimize design to reduce stress concentration
Strictly control the final size of the screws to eliminate stress concentration:
The. Use large transition fillets
B. Cutting the discharge groove

w. Undercut at the end of the line
d. Optimizing the inclination angle of the screw head can also effectively reduce the stress concentration
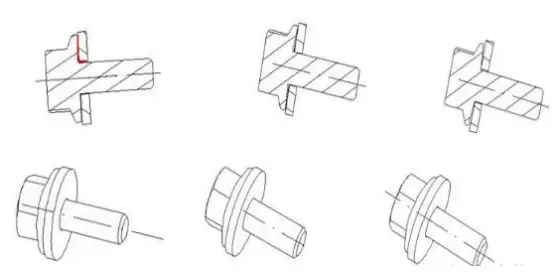
It is. Use reinforced line
The main differences between a reinforced thread and a common thread are the smaller diameter (d1) of the external thread and the radius of the root transition thread (R).
The main features of a reinforced thread include a larger minor diameter (d1) compared to a common thread, an increased root transition fillet radius (R), and a reduction in stress concentration in the screw.
There are specific requirements for the root transition fillet radius (R) in a reinforced thread, with R+ = 0.18042P and rmin = 0.15011P, where P is the pitch. In contrast, there are no such requirements for a common thread, which may even have a straight section.
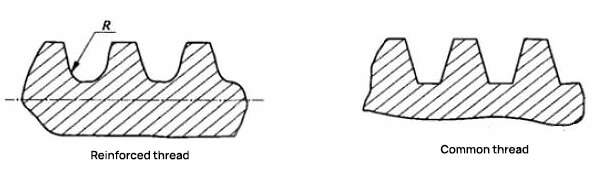
2. Improve the manufacturing process
Improving control of heat treatment and surface treatment processes during screw manufacturing can effectively increase the fatigue resistance of screws.
The. Heat treatment
Bolts undergo heat treatment followed by rolling to produce significant residual compressive stress, which slows the formation and growth of cracks and increases their fatigue resistance. It is important to avoid decarburization during heat treatment and compare the fatigue strength of screws with and without surface decarburization.
The presence of decarburization leads to the oxidation of carbon in the layer, resulting in a reduction of cementite in the metallographic structure and lower strength and hardness compared to normal structures. Typically, the fatigue strength of bolts decreases by 19.8% under surface decarburization conditions.
B. Phosphating
The phosphating treatment of the screw surfaces serves to prevent rust and ensure stable friction during assembly. Furthermore, it can also reduce wear and tear.
In the thread rolling process, reducing the friction between the thread rolling wheel and the screw thread can positively impact the stress distribution in the screw thread after rolling and reduce the surface roughness of the thread.
3. Set the appropriate preload
The tension in a common bolt connection is carried primarily by the first three tensioned threads. When the initial preload is substantial, plastic deformation occurs locally at the roots of some threads, leading to residual stresses at those roots. This residual compressive stress increases the fatigue resistance of the threads.
Furthermore, the plastic deformation of the threads improves stress distribution and reduces contact pressure, also increasing the fatigue resistance of the threads. The greater the preload, the better the bolted connection can resist separation and preload relaxation. This results in greater effective fatigue resistance of the bolted connection.
Therefore, increasing the pre-tightening force in a bolted connection improves its ability to resist fatigue failure under cyclic external loads and reduces the risk of fatigue failure due to vibration and impact forces or limited overload.