Pressure casting is a metal casting process, which is characterized by the application of high pressure to the molten metal through the internal cavity of the mold.
The mold is generally made of alloy with higher strength, which is somewhat similar to injection molding.
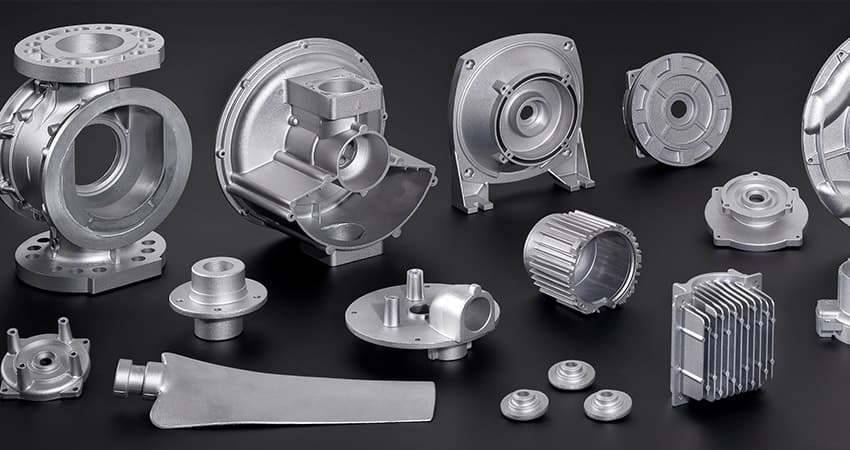
It brought unprecedented innovation to the world of printing.
After the large-scale industrialization of the printing industry, the traditional hand-pressed type was replaced by pressure casting.
Around 1900, the introduction of typesetting to the market further improved the automation technology of the printing industry, so that sometimes more than ten die-casting machines can be seen in newspapers.
With the continued growth of consumer products, Otto's inventions gained more and more applications.
People can use die casting to manufacture parts and products in large quantities.
In 1966, General Dynamics invented the precision die casting process, which is sometimes called double die casting.
Pressure casting process
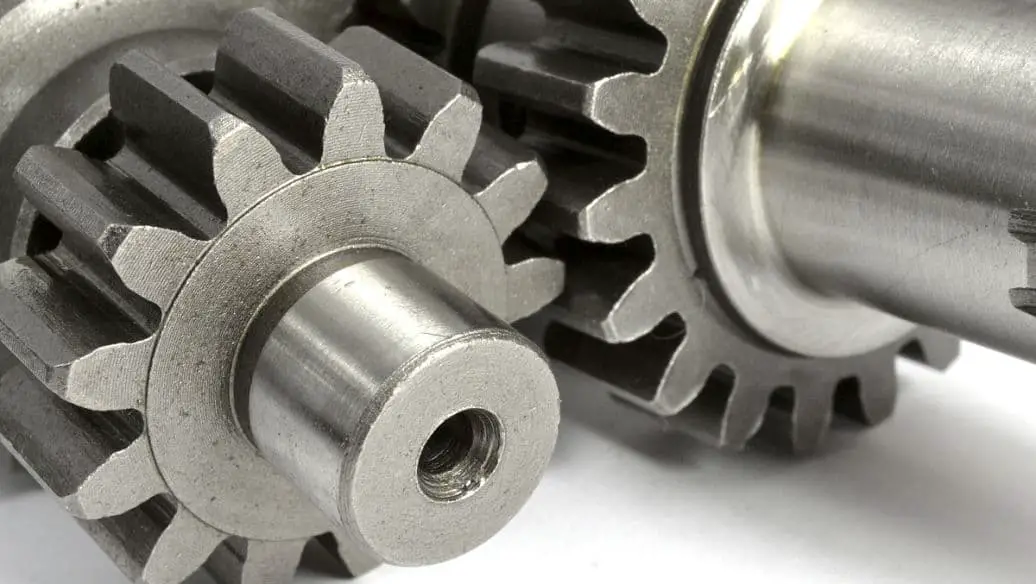
Cold chamber die casting can be used for metals that cannot be used in the hot chamber die casting process, including aluminum, magnesium, copper and zinc alloys with high aluminum content.
In this process, the metal must first be melted in an independent crucible.
A certain amount of molten metal is then transferred to an unheated injection chamber or injection nozzle.
These metals are injected into the mold by hydraulic or mechanical pressure.
Because the molten metal needs to be transferred to the cold chamber, the biggest disadvantage of this process is that the cycle time is very long.
There are vertical and horizontal cold chamber pressure casting machines.
Vertical die casting machines are generally small machines, while horizontal die casting machines have various models.
Casting Mold
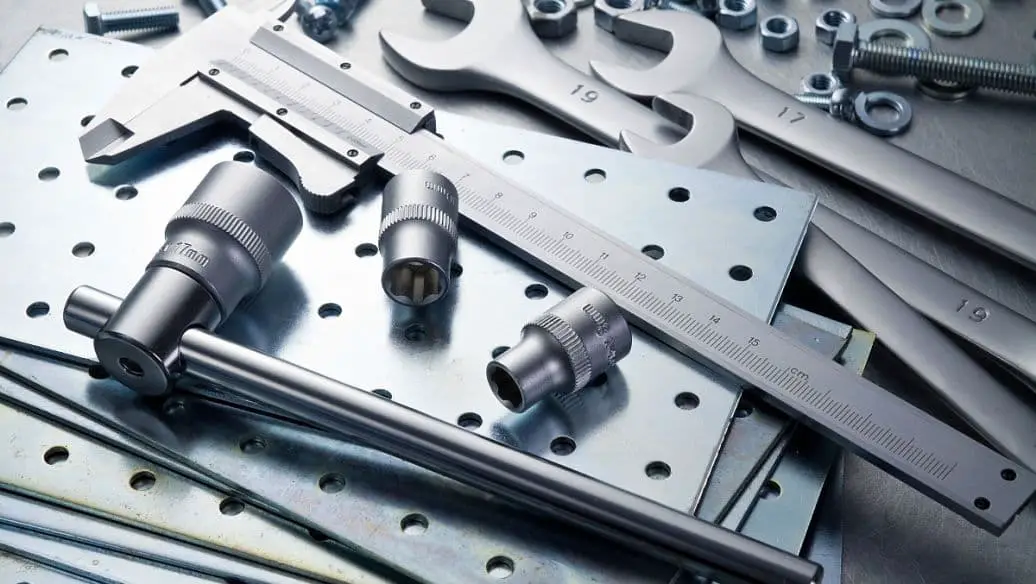
Advantages of casting
The advantages of die casting include excellent dimensional accuracy.
Generally, this depends on the casting material. The typical value is that the error is 0.1 mm for the first 2.5 cm size and the error increases by 0.002 mm for every 1 cm increase.
Compared with other casting processes, its casting surface is smooth and the fillet radius is about 1-2.5 microns.
A casting with a wall thickness of about 0.75 mm can be manufactured in relation to the sandbox or permanent mold casting method.
It can directly fuse internal structures such as wire sleeves, heating elements and high-strength bearing surfaces.
Other advantages include that it can reduce or avoid secondary machining, fast production speed, casting tensile strength of up to 415 MPa, and can cast high fluidity metals.
Disadvantages of casting
The biggest disadvantage of pressure casting is the high cost.
Casting equipment, molds, and mold-related components are expensive compared to other casting methods.
Therefore, it is more economical to produce a large number of products when making pressure castings.
Other disadvantages include: this process is only applicable to metals with high fluidity, and the melt mass must be between 30g and 10kg.
In normal pressure casting, there are always pores in the last batch of castings.
Therefore, no heat treatment or welding can be carried out because the gas in the gap will expand under the action of heat, resulting in internal microdefects and surface peeling.
Casting Feature
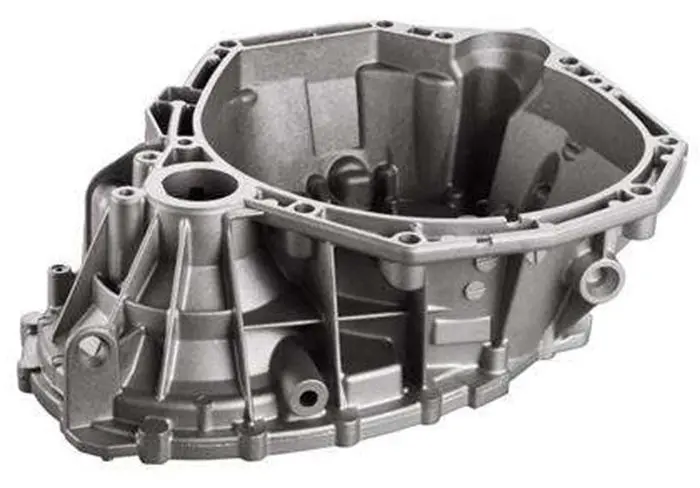
Pressure casting, briefly called pressure casting, is a casting method in which the molten alloy liquid is poured into the pressure chamber to fill the steel mold cavity at high speed, and the alloy liquid is solidified under pressure to form a casting.
The main characteristics of pressure casting, different from other casting methods, are high pressure and high speed.
① The molten metal fills the mold cavity under pressure and crystallizes and solidifies under higher pressure. Common pressure is 15-100mpa.
② The metallic liquid fills the mold cavity at a high speed, generally 10-50 m/s, and sometimes more than 80 m/S (the linear velocity of the mold cavity introduced through the inlet – the inlet velocity).
Therefore, the metal liquid filling time is extremely short, about 0.01-0.2 seconds (depending on the size of the casting).
Die casting is a precision casting method. The dimensional tolerance of die casting castings is very small and the surface accuracy is very high.
In most cases, castings can be assembled and applied without turning, and threaded parts can be cast directly.
From common camera parts, typewriter parts, electronic calculator parts, decorations and other small parts, as well as complex vehicle parts such as automobiles, locomotives and aircraft, most of them are made by die casting.
Form of Casting Failure
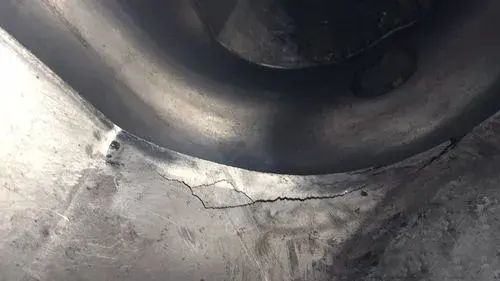
D image
During die casting production, the mold is repeatedly subjected to cooling and heating, and the forming surface and its interior deform, which leads to repeated cyclic thermal stresses, resulting in secondary damage to the structure and loss of toughness, which which leads to the appearance of microcracks and continues to expand.
Once the cracks expand, the molten metal will be compressed and repeated mechanical stress will accelerate crack growth.
Therefore, on the one hand, the die must be fully preheated at the beginning of casting.
In addition, in the pressure casting production process, the mold must be maintained in a certain working temperature range to avoid early cracking failure.
At the same time, it is necessary to ensure that no internal causes occur before the mold is put into production and during manufacturing.
Because in actual production, most mold failures are thermal fatigue crack failures.
F fragmentation
Under the action of injection force, the mold will initiate cracks at the weakest part, especially when the writing or electrical machining marks on the molding surface of the mold are not polished, or when the corners of the molding are clear, fine cracks will appear first .
When there are brittle phases or coarse grains at the grain boundaries, it is easy to fracture.
However, when brittle fracture occurs, the crack grows rapidly, which is a very dangerous factor for matrix fracture failure.
Therefore, on the one hand, all scratches and electrical machining marks on the mold surface must be polished, even if they are in the casting system.
Furthermore, it is necessary that the matrix materials used have high strength, good plasticity, good impact toughness and fracture resistance.
C corrosion
As mentioned above, commonly used casting alloys include zinc alloy, aluminum alloy, magnesium alloy and copper alloy, as well as pure aluminum casting.
Zn, Al and Mg are relatively active metal elements, which have good affinity with mold materials, especially Al is easy to bite into the mold.
When the mold hardness is high, the corrosion resistance is better, but if there are weak points on the mold surface, the corrosion resistance is unfavorable.
There are many factors that lead to mold failure, including external factors (such as casting temperature, whether the mold is preheated, how much water agent coating is sprayed, whether the tonnage of the die casting machine matches, whether the pressure pressure casting is too high, the speed of the internal gate is too fast, the opening of the cooling water is not synchronized with the pressure casting production, the type and composition of the Fe casting material, the size and shape of the casting, wall thickness, type of coating, etc.).
There are also internal causes (for example, the metallurgical quality of the mold material itself, the forging process of the blank, the design rationality of the mold structure, the design rationality of the passing system, the internal stress generated during machining of the mold machine (electric machining), the mold heat treatment process, including various corresponding accuracy and cleanliness requirements).
If there is early mold failure, it is necessary to find out what internal or external causes are for future improvements.
However, in actual production, corrosion is only local in the mold, for example, the parts directly washed by the gate (core and cavity) are prone to corrosion, and the parts with soft hardness are prone to sticking to the aluminum alloy.
Casting issues
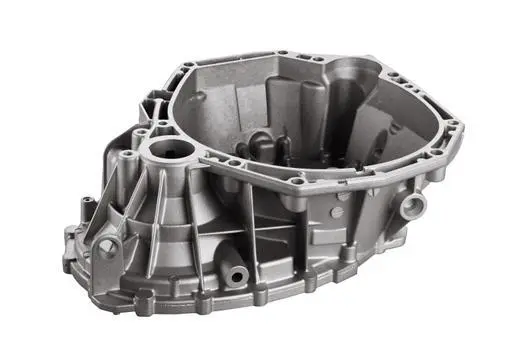
Pouring overflow
Requirements for mold in horizontal casting machine with cold chamber:
① The inner diameter of the pressure chamber should be selected according to the specific pressure required and the fullness of the pressure chamber.
At the same time, the deviation of the inner diameter of the gate sleeve should be appropriately enlarged by a few threads compared with the deviation of the inner diameter of the pressure chamber, so as to avoid the problem of punch jamming or serious wear caused by different shafts of the gate sleeve and the inner diameter of the pressure chamber, and the wall thickness of the gate sleeve should not be too thin.
The length of the sprue bushing should generally be shorter than the injection punch delivery handle so that the paint can be removed from the pressure chamber.
② The inner holes of the pressure chamber and sprue bushing should be finely ground after heat treatment, and then ground along the shaft direction.
The surface roughness should be ≤ Ra0.2 μ m.
③ The diverter is connected to the cavity forming the casing.
Its concave depth is equal to the depth of the channel, its diameter corresponds to the internal diameter of the sprue bushing and it has an inclination of 5° along the demolding direction.
When the liner introduction type channel is used, the volume of the effective length of the pressure chamber is reduced and the fullness of the pressure chamber can be improved.
Mold Requirements
① The cold horizontal mold channel inlet should generally be located at the position above 2/3 of the inner diameter of the upper part of the pressure chamber, so as to prevent the metallic liquid in the pressure chamber from entering the channel prematurely and starting to solidify in advance under the action of gravity.
② The cross-sectional area of the channel should be gradually reduced from the inlet channel to the inlet.
To expand the cross section, negative pressure will occur when the molten metal flows, which is easy to suck the gas on the parting surface and increase the swirl in the molten metal flow.
Generally, the section at the outlet is 10-30% smaller than that at the inlet.
③ The corridor must have a certain length and depth.
The purpose of maintaining a certain length is to stabilize and guide the flow.
If the depth is not enough, the temperature of the molten metal will drop quickly;
If the depth is too deep, condensation will be very slow, which will not only affect productivity but also increase the amount of recycled materials.
④ The cross-sectional area of the channel must be larger than that of the inlet to ensure the metal pouring speed into the mold.
The cross-sectional area of the main channel must be greater than that of each branch channel.
⑤ The two sides of the bottom of the runner should be rounded to avoid early cracking, and the two sides can be made with a slope of about 5°.
Runner surface roughness ≤ Ra0.4 μm.
Ingate
① The parting surface should not be closed immediately after the molten metal enters the mold, and the overflow groove and exhaust groove should not directly impact the core.
The flow direction of molten metal after entering the mold should be filled from thick wall to thin wall along the cast ribs and fins as much as possible.
② When selecting the inlet position, the molten metal flow should be as short as possible.
When multi-wire ingate is used, it is necessary to prevent multiple molten metal wires from converging and colliding with each other after injection, which will cause eddy current inclusion, oxidation inclusion and other defects.
③ The internal gate of thin-walled parts must be appropriately smaller than that of thick parts to ensure the required filling speed.
The inner gate configuration should be easy to cut and the casting body should not be damaged (eat meat).
Overflow Tank
① The overflow groove should be easy to remove from the casting and should not damage the body of the casting as much as possible.
② When setting an exhaust slot in the overflow slot, pay attention to the position of the overflow port to avoid blocking the exhaust slot too early and making the exhaust slot ineffective.
③ It is not allowed to set multiple overflow ports or one overflow port that is too wide and thick in the same overflow tank, so as to prevent cold liquid, slag, gas, paint, etc. from entering the overflow tank. in the molten metal back into the mold cavity of the overflow tank and causing casting defects.
Casting Mold Design
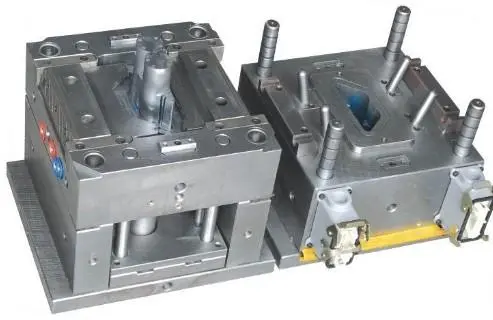
On the premise of meeting product function, reasonably design castings, simplify casting die structure, reduce casting costs, reduce casting defects, and improve the quality of castings.
Because the injection molding process is derived from the die casting process, the die casting design guide is very similar to the plastic part design guide in some aspects.
For detailed design of castings, please refer to the book “product design guide for manufacturing and assembly” published by China Machine Press.
F islet
(including corners) the casting drawing often indicates requirements such as unmarked R2 fillet.
We must not ignore the role of these unmarked fillets in mold opening, and we must not make clear corners or fillets that are too small.
The casting fillet can make the metal liquid fill smoothly, make the gas in the cavity discharge in sequence, reduce the stress concentration, and extend the life of the mold. (It is not easy for the casting to have cracks or various defects due to inadequate filling).
For example, there are many clean corners on the standard crankcase mold.
Relatively speaking, the brother crankcase mold is better open nowadays, and there are also many heavy crankcases.
Release slope
It is prohibited to have artificial side indentations in the demolding direction (generally castings are stuck in the mold during mold testing, and local indentations are caused by drilling, hard chiseling, etc. when the mold is handled by incorrect methods).
Roughness
The molding parts and pouring system must be carefully polished as necessary and must be polished along the demolding direction.
Now the entire process of entering the molten metal into the casting system from the pressure chamber and filling the cavity takes only 0.01-0.2 seconds.
To reduce resistance to the flow of liquid metal and minimize pressure loss, a high surface finish is required.
At the same time, the heating and erosion conditions of the casting system are relatively poor, and the worse the finish, the easier it is to damage the mold.
5. Hardness of the molded part of the mold: aluminum alloy: about HRC46°, copper: about HRC38°.
During processing, the mold should try to leave room for repair, reach the upper size limit, and avoid welding.
Mobility
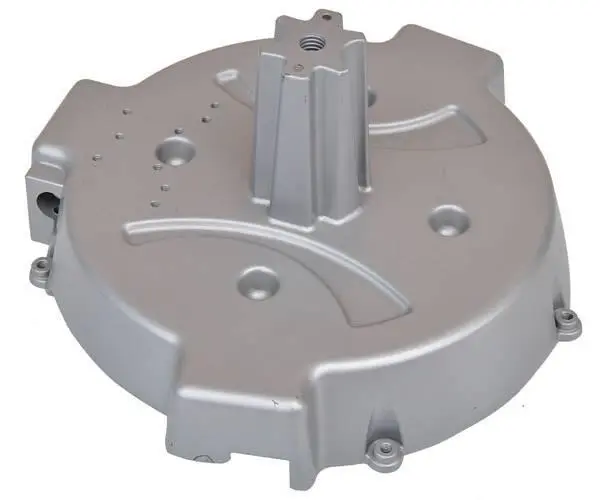
Fluidity refers to the ability of the alloy liquid to fill the mold.
Fluidity determines whether the alloy can cast complex castings.
The eutectic alloy has the best fluidity in aluminum alloy.
There are many factors that affect fluidity, mainly the composition, temperature and solid particles of metal oxides, metal compounds and other pollutants in the alloy liquid, but the fundamental external factors are pouring temperature and pouring pressure (commonly known as head leakage).
In actual production, when the alloy is determined, in addition to strengthening the melting process (refining and slag removal), it is also necessary to improve the casting process (sand mold permeability, exhaust and metal mold temperature), and increase the casting temperature without affecting the casting quality to ensure the fluidity of the alloy.
Precautions for casting molding conditions:
Die casting machine, die casting alloy and die casting die are the three main elements of die casting production, none of which are indispensable.
The so-called pressure casting process consists of using these three elements organically and comprehensively, so as to produce qualified castings with good appearance, internal quality and dimensions in accordance with the requirements of drawings or agreements in a stable, rhythmic and efficient manner. , and even high quality castings.
Material melting temperature, mold temperature and melting temperature during injection;
Finally, the condition of the cast products must be repaired to obtain perfect products.
Casting die working temperature selection principle:
1) The mold temperature is too low, the internal structure of the casting is loose and it is difficult to exhaust air, which makes forming difficult;
2) The mold temperature is very high and the internal structure of the casting is dense, but the casting is easy to be “welded” to the mold cavity, and it is difficult to remove the casting after adhering to the mold.
At the same time, too high a temperature will expand the mold itself and affect the dimensional accuracy of the casting.
3) The mold temperature should be selected within an appropriate range. Generally, after testing is appropriate, constant temperature control is good.
Precautions for casting molding conditions can be summarized as the following two aspects:
*Material melting temperature, mold temperature and melting temperature during injection;
Casting Technique
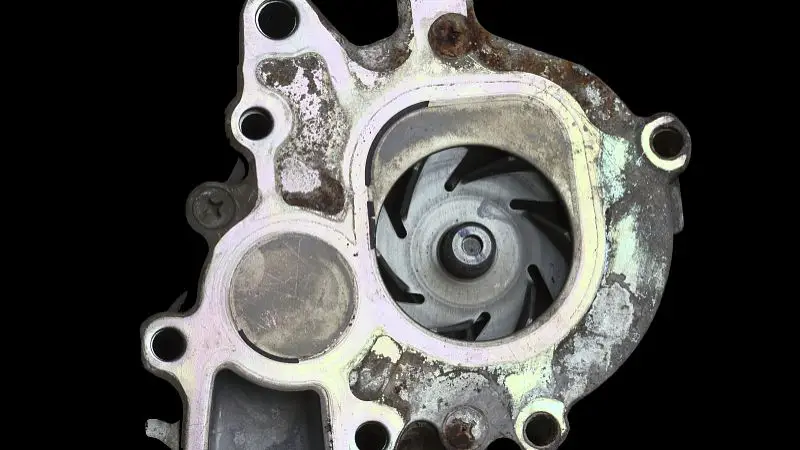
Die casting is one of the most advanced metal forming methods.
It's an effective way to get less and no chips. It is widely used and develops rapidly.
The size and weight of the casting depend on the power of the die casting machine.
Due to the increased power of the die casting machine, the shape and size of the casting can vary from a few millimeters to 1-2m;
Weight can vary from a few grams to tens of kilograms.
Aluminum castings with a diameter of 2m and a weight of 50kg can be cast abroad.
Die casting is no longer limited to the automobile industry and instrument industry, but has gradually expanded to other industrial sectors such as agricultural machinery, machine tool industry, electronics industry, national defense industry, computer technology, medical equipment, watches, cameras, diary hardware and other dozens of industries, specifically: automotive parts, furniture accessories, bathroom accessories (sanitary ware), lighting parts, toys, shavers, tie clips, electrical and electronic parts, belt buckles, watch cases, metal ornaments, locks, zipper, etc.
In the aspect of die casting technology, new technologies such as vacuum die casting, oxygenated pressure die casting, dense and high-speed die casting and the application of soluble cores have emerged.
It will play a very good role in promoting China's pressure casting industry.
Development
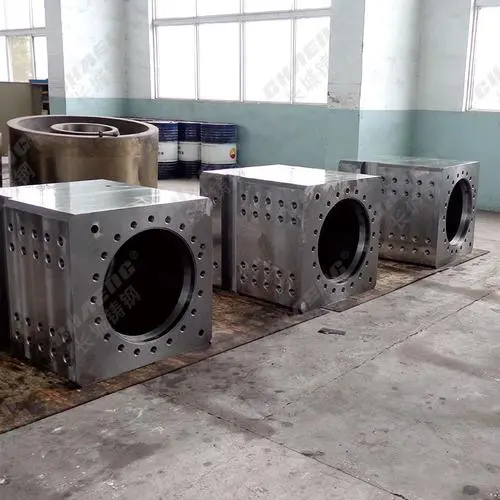
The production of die-cast parts requires pressure casting machines and equipment. Die casting machines are the basis of die casting production.
The technical level of the pressure casting equipment determines the quality and level of the castings.
Therefore, to promote the development of the pressure casting industry, we must give priority to the development of pressure casting equipment.
China is a big country in die casting, but its level of production technology and industrial equipment still need to be improved.
China's 12th Five-Year Plan clearly indicates that the main task of the development of the casting industry is to give priority to the development of important technical equipment, including “casting units of large-tonnage die-casting machines”, with the aim of providing support of equipment for technological updating of pressure casting companies.
The development of pressure casting technology and equipment will help improve the level of pressure casting machinery and equipment, so as to improve the quality and technical level of castings and promote the development of the die casting industry.