One of the most commonly used CNC machining techniques is milling. This process is ideal for manufacturing and surface finishing of parts. Enables high precision, reproducibility and production rates. Numerous industries utilize CNC milling, including automotive, aerospace, robotics, and medical.
This article will cover the CNC milling process as well as other milling basics such as definition, types of milling, essential tools, and how to save costs with this process.
Definition of milling
The term “milling” refers to any machining operation involving rotating cutters used in manufacturing to remove material from a part. Furthermore, it is an adaptable method that can create many shapes and surface treatments on different materials. Different types of machines are also used.
There are two types of milling operations: manual milling and automatic milling (CNC). Hand milling is the traditional method of shaping and manufacturing objects by hand, using hand tools and manually operated machines. Achieving the desired results depends mainly on the knowledge, skill and experience of the operator. Here we discuss CNC milling in detail. Keep reading.
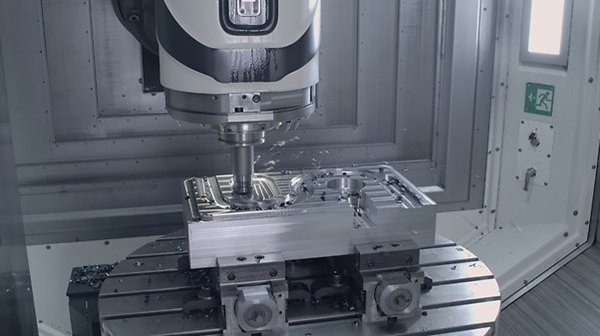
What is CNC milling?
What is CNC milling? CNC milling is a common machining technique in which the process is controlled by computer-controlled devices. Milling involves using a rotating tool to cut materials such as plastic, metal or wood. In CNC milling, the computer controls the spindle speed and feed rate, the order in which tools are used, and the tool path of each cutter.
The rotation of the cutting tool depends on the type of CNC milling machine and its level of development. Most CNC machined parts can achieve high tolerances between +/-0.001″ and +/-0.005″. Some machines can even achieve tolerances of up to +/-0.0005 inches.
There are also several axis milling operations, from 3-, 4-, and 5-axis milling to multi-axis milling. In 3-axis milling, movement occurs in the X, Y, and Z axes. In contrast, 5-axis milling machines move and produce in the linear X, Y, and Z directions and rotationally in the A and B directions, more complicated parts.
Basics of CNC milling spindles
CNC milling machines work with two main axes: linear axes and rotary axes.
Linear axes
CNC machines are based on the Cartesian coordinate system, which is widely used in mathematics and computer-aided design (CAD) software. Three linear axes in this system are perpendicular to each other and intersect at the origin.
These are the X, Y, and Z axes. These axes describe the direction of a cutting tool. The X axis is the movement that moves from left to right parallel to the cutting tool. The Y axis is the movement perpendicular to the cutting tool, moving from front to back. On the other hand, the Z axis is the movement from bottom to top.
Axes of rotation
The name “rotational axes” comes from their connection to rotation. Furthermore, the relationship between the rotational and linear axes becomes clear, as these rotations always rotate around one of the three linear axes. There are three axes of rotation and their relationship generally looks like this:
The A axis, or tilt axis, is the tilt or rotation around the X axis. The B axis is the rotation around the Y axis, the C axis is the rotation around the Z axis.
How does CNC milling work?
It is important to provide a complete view of the milling process. This will give you a comprehensive view of how it works. Generally, the CNC milling process occurs in three phases:
1. Design the CAD files
In the first phase, you create a virtual representation of the desired product using CAD software. You can use various CAD-CAM programs to develop the G-code required for machining. It is important to translate the CAD design into a CNC programming language as the machine understands it.
You can review and modify the code to adapt it to the machine's capabilities. The software also allows production engineers to simulate the entire milling process. This allows you to check for design errors and avoid creating complex models that are very difficult to edit.
The operator also needs a technical drawing containing information such as:
- Dimensions and critical characteristics of a part
- Tolerances
- Construction lines
- Wire specification
- Finishing Settings
2. Setting up the milling machine
Although CNC milling machines cut parts automatically, some aspects of the process require a machine operator. For example, an operator needs to clamp the workpiece on the worktable and attack the spindle cutting tools.
Modern milling machines have live tool functions. Therefore, you can change tools during the milling process. This reduces the number of interruptions that occur during the process. However, initial setup and program checks are still required before starting the process.
3. Manufacturing of components
As mentioned previously, CNC milling uses rotating tools that cut chips when they come into contact with the workpiece. The desired shape is created by continuously rotating the tool. The process may involve different operations depending on the type of raw material and the desired shape of the final product.
The first steps involve using larger tools to carve the material into a rough shape. More precise parts are then produced by changing tools. Precision CNC milling is achieved in the final stages and requires unsurpassed surface roughness and technical tolerances.
Various CNC milling operations
A CNC milling center can produce various complex features with high precision. Such features include threads, chamfers, grooves, etc. However, creating these features requires several milling operations such as:
Roll milling
This process is also known as face milling and uses a horizontal milling machine. The cutting tool therefore has an axis of rotation parallel to the work table. In face milling, different cutters with different shapes and orientations are used depending on the desired result. A combination of a wide cutter (with fast feed) and finer cutting teeth (with faster cutting speed) is a good choice in terms of cost-benefit. It also guarantees better surface finishes and high quality final products.
Front milling
This type of milling uses cutting tools with teeth on the sides and ends. The side teeth do the main work of cutting, while the other teeth at the tip help with surface finishing. Face milling is usually done after face milling because it can create complex contours and leave a high-quality surface.
Angle milling
This is one of the best milling operations for creating grooves, chamfers, grooves and other complex features. Traditional 3-axis mills use different cutters – dovetail mills for angled slots or tapered cutting heads for chamfering. The axis of the cutter is usually perpendicular or aligned with the cutting surface.
Shape milling
This milling operation uses special tools to create more complex contours. Concave and convex cutters are the most common here. With their help, surface contours, rounded edges and round recesses can be created in just one cut.
Other milling operations
In addition to the above milling operations, CNC milling machines can also perform other types of special milling operations, such as:
Profile milling : here the tool creates a cutting path along an angular or vertical surface on the blank bar. This process uses a profile milling tool that can be parallel or perpendicular to the surface of the part.
Gang milling : This is a subcategory of shape milling that involves using multiple cutters simultaneously to create patterns. Cutters often come in different shapes, sizes, or widths. You can perform similar or different operations to create more complex features or complicated parts in less time.
Portal milling : This milling process allows a machine tool to machine two or more parallel parts with a single cut. Two cutters are arranged on both sides of the workpiece to mill both sides on the same machine spindle.
Important CNC milling tools in machining process

Although many CNC milling tools are used, not all of them are essential. Here are some of the main milling tools used.
Faucets
Taps are used to cut threads in materials such as metal or plastic. They come in various shapes and sizes and include manual and automatic faucets. In conjunction with milling machines, threaded holes can be created. Additionally, this milling tap tool is ideal for use with softer materials such as plastic, brass, copper and aluminum.
pierce
Circular holes can be drilled in wood and metal using drill bits attached to milling machines. They come in a variety of shapes and sizes, including flat and twist drills.
Furthermore, drill bits are essential in CNC milling to accurately form tapered holes before drilling, thus preventing incorrect drilling.
End mill
Cutting tools for drilling and milling are called end mills. They are made from materials such as carbide or high-speed steel and are available in various sizes and shapes. They can also be used for a variety of cutting applications, including side, face, ramp, plunge and grooving milling, and are essential for cutting large volumes of material.
Components of a CNC milling machine
Here we analyze the components that make up CNC milling machines. Although new milling machines are somewhat complex, we will stick to traditional milling centers to provide a fair overview. The essential components of milling machines are:
1. Frame
This main structure supports the machine and gives it strength and stability. It has a removable base and columns. The machine head is an essential part of the structure for mounting the main spindle and prevents vibration or shaking during machine operation. This prevents machining errors and extends the life of the cutting tool.
2. CNC Control Panel
It can be called the “nervous system” of milling centers. It consists of the various electronic components required to control the various cutting operations through programming functions. The main components of the control panel are the CNC monitor and programming buttons. Most CNC routers have easy-to-access control panels for easy editing.
3. Axes
CNC milling machines have X, Y and Z axes. Depending on the configuration, additional rotation axes (A, B and C) are also available. Programming is usually done using G code on the CNC control.
4th column
This part of the machine provides structure and support for other components of the mill. It comes with an attached base and can contain internal components that support the CNC milling process. Such internal features include coolant and oil reservoirs.
5. Work table
This component is the solid base that allows the part to be fixed. In other words, it holds the rod, vise, or jig in place. Depending on the milling machine used, the part can be adjusted vertically, horizontally or in both directions. Most work tables use T-slots to ensure easy clamping of the workpiece.
6. Spindle
The spindle consists of a conical section for positioning tool holders. It also has a rotating assembly and a shaft for attaching the cutting tool. Depending on the type of milling machine, the spindle can be positioned horizontally or vertically.
7. Arbor
This is the spindle component that is inserted into the spindles of horizontal milling machines. They allow the assembly of multiple machine tools. Mandrels are available in various lengths and diameters depending on required specifications.
8. Aries
This machine part is typically found on vertical milling machines. It is usually fixed to the column that supports the spindle. The operator can adjust the ram to assume different positions during the milling process.
9. Machine tool
This is the component that removes the material. Depending on the milling specification, different tools are available for milling. They differ in arrangement, number, spacing between teeth, diameter, length and geometry.

Types of CNC milling machines
There are different types of CNC milling machines that are suitable for different purposes. These machines include:
Vertical milling machines
This vertical milling machine has three axes of movement. It has a table that serves as a spindle and work surface. As the name suggests, the spindle axis of a vertical milling machine is oriented vertically. Additionally, the spindle holds the shaft of the cutters while they rotate. There are two classes of vertical CNC milling machines.
- bed mill : In a bed mill, the table moves only perpendicular to the spindle axis. The spindle, on the other hand, rotates in front of its axis.
- Turret mill : The turret mill has a stationary spindle and a table that can move parallel and perpendicular to the spindle axis. The quill, a feature of certain turret mills, raises and lowers the milling tools. The turret mill is more versatile.
Horizontal milling machines
Spindle axis alignment distinguishes a vertical milling machine from a horizontal milling machine. The spindle axis is aligned horizontally.
Longer or heavier parts are better suited to horizontal milling machines. The rotary table on many horizontal milling machines allows the machine to grind at different angles.
Knee type
The work table of these machines is vertically adjustable and has a fixed spindle. The knee supports you while lying in the saddle. The knee can be raised or lowered. Examples of knee milling machines are floor-mounted horizontal tabletop milling machines.
Type of planer
They are somewhat similar to bed milling machines. Their work tables are arranged along the Z and Y axes. The spindle can move in the X, Y and Z axes. However, various machine tools can be supported by face milling machines.
Bed type
In benchtop milling machines, the work table is attached directly to the base of the machine. Movement of the workpiece along the Y and Z axes is prevented.
Furthermore, bed milling machines can be classified as simplex, duplex or triplex machines. Duplex and triplex machines use two and three spindles respectively, while simplex machines, as the name suggests, have only one spindle that moves in the X or Y direction.
Various multi-axis milling machines
These machines can move along different axes and mill at different angles. Common multi-axis milling machines can be:
3-axis milling
With 3-axis vertical milling machines, the table can be moved in the X and Y directions. These machines allow parts to be positioned relative to the cutting tool. The operator can then add the Z axis by lowering the cutting tool. CNC tools guarantee simultaneous movements of the three axes, providing the flexibility necessary for your needs.
4-axis milling
All these mills have three shafts, as mentioned above. But here another axis is added – the A axis. Adding another axis allows the table to rotate around the X axis. This provides space for face milling without the need to reposition the workpiece.
5-axis milling
Everything that applies to 4-axis milling applies here, but with an additional B axis. This addition helps the table rotate around the Y axis. 5-axis CNC milling machines are more expensive than the options discussed above, but they allow you to produce complex parts in a single operation. They do not require additional settings and are compatible with power tools.
6-axis milling machines
6-axis milling machines are not yet standard due to their high cost. They have fixed work tables with complete freedom of movement of the cutting head. This means the head can move in and around the X, Y and Z axes.
How much does a milling machine cost?
The cost of a milling machine is one of the factors that affect the cost of CNC machining. However, these costs vary depending on the complexity of the machine. For example, basic 3-axis vertical or tool-making milling machines cost between $50,000 and $80,000. In contrast, basic 5-axis milling machines cost between $100,000 and $400,000.
Similarly, production-level 3-axis vertical milling machines cost between $150,000 and $300,000, while production-level 5-axis milling machines cost more than $500,000. These are rough estimates and depend on factors such as:
- Machine weight and size (measured in X/Y/Z displacement)
- Machine configuration (3, 4, 5 or 6 axes)
- Machine speed
- Performance
- Other options available, e.g. B. Coolant pressure, chip conveyor, automatic tool changer, robot parts loader, etc.

Tips for cost migration in the CNC milling process
Here are some professional suggestions that can help reduce the cost and time of your CNC milling project.
Work with viable materials
Processing time, i.e. the time required to produce a product, is as crucial to cost savings as material selection. The raw material and part design are the main elements that determine processing time.
Additionally, machining complex part designs with extremely precise dimensions is difficult and expensive. Choosing materials that are as easy to work with as possible will help you solve this problem. By choosing machinable materials such as brass, aluminum and low-carbon alloys, you can also reduce the time spent machining. Hard metals like steel are more difficult to machine and easily lead to tool failure.
Use tight tolerances for critical functions only
When it comes to CNC fine machining, specifications are crucial. However, tighter tolerances in part design have a significant impact on production costs.
For general characteristics, it is recommended to continue to allow standard tolerances. If necessary, you can set tolerances for some important features and functions. Also ensure that the hole sizes for routing remain consistent. Deeper and smaller holes require more time to machine and can lead to tool breakage and therefore higher production costs.
Reduce setup time and number of setup processes
Each machined part goes through one or more processes. Each process requires multiple preparations, including machine and material setup, component clamping (if necessary), CAM programming (which varies depending on the cutting, milling, and drilling processes), and more. Therefore, reducing the number of installations will help avoid all the chaos and costs.
Additionally, most parts can be completed in six configurations or less. If possible, reduce the number of steps required to one or two. Setup time is cut in half or even reduced further with fewer configurations. This technique also allows you to machine CNC machined parts faster and more accurately.
Keep inside corners at a standard radius
Internal corners are also subject to the requirements of the standard specifications. Milling internal corners to small, precise radii is expensive, time-consuming and requires specialized equipment, especially when working with very small cutters. This is because parts typically undergo vertical milling operations by CNC machines.
For most machined parts, a suitable inside corner radius is 3 mm or ⅛ inch. Consequently, maintaining traditional radii can save configuration time and costs on non-critical resources.
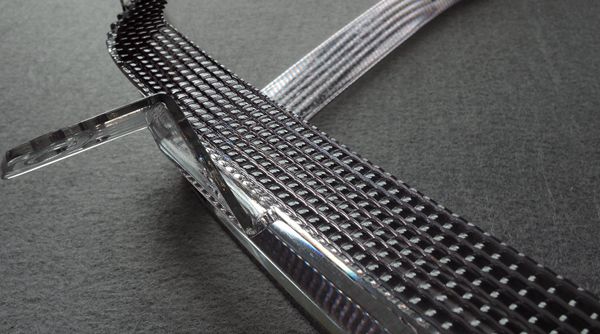
Common materials for CNC milling operations
CNC milling works with a wide variety of materials. Material selection depends on the needs and specifications of your applications. The most common materials include:
Metal materials for milling
- aluminum alloys
- stainless steel
- Structural steel
- Tool steel
- Brass
- copper alloys
- titanium alloys
Plastics for milling
- POM
- Section
- nylon
- Polycarbonate
- LOOK
- PTFE (Teflon)
- Polyethylene
- PMMA (acrylic)
- HDPE
- made of PVC
- Polypropylene
Advantages and disadvantages of CNC milling in parts production
The CNC milling process is essential for several industrial processes due to its advantages. However, there are also disadvantages that must be taken into account. Here are some of the advantages and disadvantages of this manufacturing technique.
Advantages of CNC milling
Accuracy and precision
The nature of CNC milling operations leaves minimal room for error, ensuring greater accuracy and precision. This technique can be used to produce parts that meet precise technical specifications and tolerance requirements.
Most CNC machined parts can achieve high tolerances between +/- 0.001″ and +/- 0.005″, with some even reaching +/- 0.0005″. Automating the process also limits human error. Even if surface treatment is required, micro-milling can remove some thickness to avoid compromising the dimensions of the part.
Efficiency and repeatability
CNC milling centers offer high production performance due to automation. Modern milling machines can produce parts faster and with consistent quality and finish.
Wide material compatibility
This process is suitable for a wide range of materials, including metals, plastics, glass and wood. This further increases its versatility and makes it perfect for a variety of applications.
Less labor intensive
The automation and high performance of CNC milling machines significantly reduces the amount of labor required for the process. These machines also allow for motorized tools, allowing tool changes without interrupting operations. The process would require very few operators.
Cost benefit
CNC milling machines produce complex products faster and more accurately. This shortens production time. Furthermore, the lower workload further reduces process costs.
Disadvantages of CNC milling
High machine costs
The initial investment costs for CNC milling machines are higher than for traditional manual devices. This can increase overall manufacturing costs.
Requires intensive operator training
Not everyone can operate CNC milling machines. From designers to programmers and machine operators, adequate training is required to make the most of the process.
High maintenance effort
Milling machines require constant maintenance to ensure their proper functioning and increase the useful life of the tools. This increases downtime when using milling machines.
Which industries use CNC milling for their applications?
Numerous industries benefit from the advantages and diverse application possibilities of CNC milling. Here are some of its industrial applications:
aerospace industry
The milling process is also suitable for producing aerospace parts from materials such as aluminum and titanium. These materials are durable and lightweight, ensuring precise machining of desired components.
Auto Industry
Products for the automotive industry must be efficient and precise. Therefore, CNC milling is suitable for producing interior panels, transmission shafts, cylinder heads, gearboxes, exhaust parts, suspension components, etc.
Medical industry
Medical and surgical instruments often have unique designs that require optimal precision. Therefore, CNC milling is one of the best methods to produce such components. This way, designs are preserved and efficiency and productivity increase.
Consumer products
CNC milling can also be used to produce multifunctional components. This includes bolts and nuts, gears and shafts, flanges, etc. The process is suitable for small and large series production.
Alternative methods for milling operations
Grind
Compared to milling, grinding can remove harder materials and produce products with finer finishes and tighter tolerances. Many parts are CNC machined before grinding, but some grinding operations are performed entirely from the raw material using a technique known as abrasive machining. When little metal needs to be removed and surface smoothness and dimensional accuracy are critical, grinding is often preferred over milling.
Plan or model
The costs of purchasing a milling machine are significantly higher than those of a planer or shaper, which can also be used to process parts of the same size. Additionally, setup times are typically longer and the cost of milling tools can be up to 50 times higher than other types of equipment.
Planing uses single-edge cutting tools to remove material from the workpiece. It is also great for efficiently removing large amounts of material in a linear motion. However, this process makes it difficult to machine precision parts.
I emphasize
This machining technique uses a sharp, hardened, serrated tool to remove material from a workpiece evenly, continuously, and precisely. Broaching involves using a tool with raised teeth of varying sizes to accurately remove a specific amount of material with each pass.
Broaching is sometimes more economical than milling when processing large quantities, but it also has disadvantages. Some of the disadvantages are that the machining process is slower and a little more demanding when machining tougher or harder materials. Additionally, machine setup can be time-consuming compared to milling.
Future trends in CNC milling
Modern production today relies heavily on CNC milling, and as technology advances, more trends and developments will emerge in this area. One of the most recent advancements is the increasing versatility of the CNC router, making it ideal for working with a wider range of materials.
Additionally, CNC milling machines and software are becoming more affordable and easier to use. This is due to the increase in the computational power of CNC machines, reducing human intervention. Additionally, workstations with more powerful processors can help speed up the modeling and design work needed to create the models that CNC mills use as the basis for their operation. Each link in the chain has benefited from technological developments and the associated time savings.
Choose WayKen for your CNC milling projects
When you work with us, calculating your CNC machining cost will be easy. We will analyze your project and give you feedback in the shortest possible time. Contact us now!
Concluding
CNC milling is suitable for many high-value applications, regardless of complexity. This cost-effective manufacturing process also saves a lot of time and ensures operational efficiency and shorter time to market.
Common questions
What is the difference between CNC milling and turning?
The difference is in how it works. In CNC milling, the part is held in place while the cutting tool rotates to shape the part. CNC turning, on the other hand, uses a stationary cutting tool and a rotating workpiece.
What products can you make with CNC milling machines?
Milling machines can produce any product as long as it can be designed. You can get standard and special parts regardless of the complexity of their geometry.
How much does CNC milling cost?
The cost of CNC milling is influenced by several factors, including raw material, part design, type of milling machine, production volume, and post-processing. Each element plays a unique role in determining the cost of your CNC milling project.