What is tempering?
Tempering is a heat treatment process. In the case of steel, quenching involves heating it to a temperature above its critical temperature Ac3 (for hypoeutectoid steel) or Ac1 (for hypereutectoid steel), holding it for a certain period to allow complete or partial austenitization, and then rapidly cooling it below Ms (or close to Ms for isothermal) at a rate faster than the critical cooling rate, allowing transformation into martensite (or bainite).
Tempering is also used to refer to heat treatment processes that involve solution treatment or rapid cooling for materials such as aluminum alloys, copper alloys, titanium alloys, and tempered glass.
Quenching methods in the heat treatment process
Quenching is a heat treatment method that involves heating steel above its critical temperature, holding it there for a certain period, and then cooling it at a rate greater than the critical cooling rate to obtain a predominantly unbalanced structure. martensitic (although bainite or a single-phase austenite can also be obtained as required).
Quenching is the most widely applied method in steel heat treatment processes.
There are approximately four basic processes in the heat treatment of steel: annealing, normalizing, quenching and tempering.
Ringing
This involves heating the workpiece to an appropriate temperature, holding it there for a period dependent on the material and size of the workpiece, and then slowly cooling it (slower cooling rate). The objective is to bring the internal structure of the metal to or near equilibrium, achieving good process performance and use performance, or preparing the structure for further quenching.
Normalizing
After heating the part to a suitable temperature, it is cooled in air. The effect of normalizing is similar to annealing, but produces a finer structure. It is commonly used to improve the cutting performance of materials and sometimes used as a final heat treatment for parts with less demanding requirements.
Temperament
To reduce the brittleness of steel parts, those that have been quenched are kept at a temperature above room temperature, but below 710°C, for a long period before cooling. This process is known as tempering.
Tempera
This is a heat treatment process that involves heating the part to austenitize it and then cooling it appropriately to obtain a martensite or bainite structure. Common methods include water quenching, oil quenching, and air quenching.
Annealing, normalizing, quenching and tempering are the “four fires” in integral heat treatment. Quenching and tempering are closely related, they are often used together, and both are indispensable.
There are ten tempering methods in the heat treatment process, which are:
- Single medium quenching (using water, oil or air);
- Quenching interrupted;
- Hammertemperage;
- Tempering below the Ms point;
- Bainite isothermal quenching;
- Composite tempering;
- Pre-cooled isothermal quenching;
- Delayed cooling quenching;
- Extinguishing self-temper;
- Jet quenching.
1. Single medium quenching (water, oil, air)
In this process, the part is heated to quenching temperature and then quickly cooled by immersion in a quenching medium. This is the simplest quenching method and is commonly used for simple shaped carbon steel and alloy steel parts. The choice of tempering medium is based on factors such as heat transfer coefficient, hardenability, size and shape of the parts.
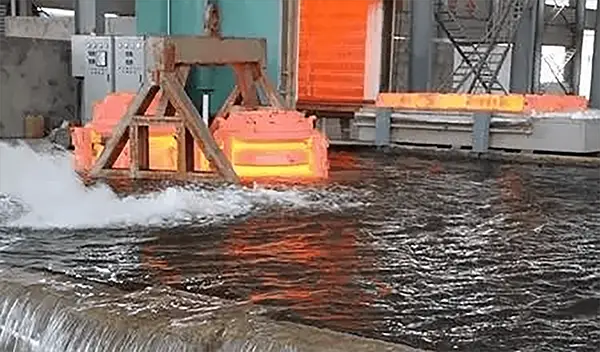
Fig. 1 Single medium quenching (water, oil, air)
2. Quenching interrupted
In the heat treatment process, the part that has been heated to the quenching temperature is rapidly cooled to the point near the start of martensite (MS) in a strong cooling medium. The part is then slowly cooled to room temperature in a slower cooling medium, which creates a range of different quenching temperatures and optimal cooling rates.
This method is used for complex shaped parts or large parts made of high carbon steel, alloy steel and carbon tool steel. Common cooling media include water-to-oil, water-to-nitrate, water-to-air, and oil-to-air. Water is typically used as the rapid cooling medium, while oil or air is used as the slower cooling medium. Air is used less frequently.
3. Tempering
The steel is austenitized and then immersed in a liquid medium (salt bath or alkaline bath) with a temperature slightly higher or lower than the upper martensitic point of the steel for a specific time. The steel is then removed for air cooling, and the subcooled austenite slowly transforms into martensite.
This method is generally used for small parts with complex shapes and strict deformation requirements. High-speed steel and high-alloy steel tools and dies are also commonly hardened using this method.
4. Graded martensitic hardening method below the Ms point
The part is cooled rapidly in the bath when the bath temperature is lower than the MS point (martensite start) and higher than the MF point (martensite finish). This results in the same result as using a larger bath size.
This method is commonly used for steel parts of large size and low hardenability.
5. Isothermal quenching of bainite
The part is quenched in a lower bainite temperature bath for isothermal treatment, causing the formation of lower bainite. This process is normally carried out by keeping the piece in the bath for 30 to 60 minutes.
The isothermal quenching of the bainite process consists of three steps:
- Austenitizing treatment
- Cooling treatment after austenitizing
- bainite austempering
This method is commonly used for small-sized parts made of alloy steel and high-carbon steel, as well as ductile iron castings.
6. Composite tempering
Martensite with a volumetric fraction of 10% to 30% is obtained by quenching the part below the MS point, followed by isothermal treatment in the lower region of the bainite.
This method is commonly used for alloy tool steel parts.
7. Pre-cooled isothermal quenching
This quenching method is also known as step-up austempering. The process involves first cooling the parts in a bath with a lower temperature (above MS) and then transferring them to a bath with a higher temperature to undergo the isothermal transformation of the austenite.
This method is suitable for steel parts with low hardenability or large dimensions, as well as parts that must be austempered.
8. Quenching by naked cooling
In the precooled isothermal quenching process, parts are precooled to a temperature slightly above Ar3 or Ar1 using air, hot water, or a salt bath. Then, single-medium quenching is carried out.
This method is often used for parts with complex shapes, significant thickness differences, and minimum deformation requirements.
9. Self-tempering
The quenching and self-tempering process involves heating all the workpieces, but only immersing the parts to be hardened (usually the workpieces) in a quenching liquid for cooling during quenching.
As soon as the shine of the unimmersed parts disappears, the quenching process is immediately removed for air cooling.
This method allows heat to be transferred from the center to the surface to temper it and is commonly used for tools that must withstand impacts such as chisels, punches, hammers, etc.
10. Jet quenching
The quenching method of spraying water onto the workpiece can be adjusted in terms of water flow depending on the desired quenching depth. Jet quenching prevents the formation of a vapor film on the surface of the workpiece, which results in a deeper hardened layer compared to normal water quenching.
This method is mainly used for localized surface tempering.
Purpose of tempering
The purpose of quenching is to induce the transformation of supercooled austenite into martensite or bainite, resulting in a martensitic or bainitic structure. Subsequent tempering at different temperatures can significantly increase the stiffness, hardness, wear resistance, fatigue resistance and toughness of steel, meeting the diverse requirements of various mechanical parts and tools. Quenching can also satisfy special physical and chemical properties, such as ferromagnetism and corrosion resistance of certain special steels.
Quenching is a metal heat treatment process that involves heating a metal part to an appropriate temperature, holding it there for a period, and then rapidly cooling it by immersing it in a quenching medium. Commonly used quenching media include brine, water, mineral oil, and air. Quenching can improve the hardness and wear resistance of metal parts, and is widely used in various tools, molds, measuring tools and wear-resistant parts (such as gears, rollers, carburized parts, etc.).
Through quenching and subsequent tempering at different temperatures, the metal's strength can be greatly improved and its toughness and fatigue resistance reduced. This process can achieve a balance of these properties (comprehensive mechanical performance) to meet different usage requirements.
In addition, quenching can also impart certain physical and chemical properties to steels with special performance, such as increasing the ferromagnetism of permanent magnetic steel, improving the corrosion resistance of stainless steel, etc.
When common steel is heated above its critical temperature, the structure that existed at room temperature will transform entirely or largely to austenite. Subsequently, the steel is quickly cooled by immersion in water or oil, causing the austenite to transform into martensite. Martensite has the highest hardness compared to other steel structures. Rapid cooling during quenching causes internal stress in the workpiece, which, when great enough, can cause distortion, twisting, or even cracking of the workpiece. Therefore, a suitable cooling method must be chosen.
Based on the cooling method, quenching processes can be divided into four categories: single liquid quenching, double medium quenching, graduated martensite quenching and isothermal bainite quenching.
Tempering process
The tempering process includes three stages: heating, holding and cooling. Here, principles for selecting process parameters for these three steps are introduced using steel quenching as an example.
Extinguishing Heating Temperature
Based on the critical phase transformation point of steel, heating during quenching aims to form fine and uniform austenitic grains, obtaining a fine martensitic structure after quenching.
The quenching heating temperature range for carbon steel is shown in the “Quenching Heating Temperature” figure. The quenching temperature selection principle shown in this figure also applies to most alloy steels, especially low alloy steels. The heating temperature of hypoeutectoid steel is 30-50°C above the Ac3 temperature.
Chinese Degree | Critical point /℃ |
Quenching Temperature /℃ |
|
To him | A is (A cm ) | ||
20 | 735 | 855 | 890~910 |
45 | 724 | 780 | 830~860 |
60 | 727 | 760 | 780~830 |
T8 | 730 | 750 | 760~800 |
T12 | 730 | 820 | 770~810 |
40cr | 743 | 782 | 830~860 |
60Si2Mn | 755 | 810 | 860~880 |
9CrSi | 770 | 870 | 850~870 |
5CrNiMo | 710 | 760 | 830~860 |
3Cr2W8V | 810 | 1100 | 1070~1130 |
GCr15 | 745 | 900 | 820~850 |
Cr12MoV | 810 | / | 980~1150 |
W6Mo5Cr4V2 | 830 | / | 1225~1235 |
From the figure “Quenching Heating Temperature”, we can see that the state of steel at high temperature is in the single-phase austenite region (A), so it is called full quenching. If the heating temperature of hypoeutectoid steel is higher than the Ac1 temperature and lower than the Ac3 temperature, then the previously existing proeutectoid ferrite is not completely transformed into austenite at high temperature, which is incomplete (or subcritical) quenching. The quenching temperature of hypereutectoid steel is 30-50°C above the Ac1 temperature, this temperature range is in the austenite and cementite dual phase region (A+C).
Therefore, the normal quenching of hypereutectoid steel still belongs to incomplete quenching, and the structure obtained after quenching is martensite distributed in the cementite matrix. This structure has high hardness and high wear resistance. For hypereutectoid steel, if the heating temperature is too high, much of the proeutectoid cementite will dissolve, even dissolve completely, so the austenite grains will grow and the carbon content of austenite will also increase.
After quenching, the large martensite structure increases the internal stress in the microregions of the tempered steel, increases the number of microcracks and increases the part's tendency to deform and crack. As the carbon concentration in austenite is high, the martensite point drops, the amount of retained austenite increases, and the hardness and wear resistance of the part decreases. The quenching temperature of commonly used steels is shown in the figure “Quenching Heating Temperature”, and the table shows the quenching heating temperature of commonly used steels.
In actual production, the choice of heating temperature needs to be adjusted according to specific conditions. For example, when the carbon content in hypoeutectoid steel is at the lower limit, when the furnace load is large, and when it is desired to increase the depth of the quenching layer of the workpiece, the upper limit temperature can be chosen; If the shape of the part is complicated and the deformation requirements are strict, the lower limit temperature should be adopted.
Temper retention
The tempering maintenance time is determined by several factors, such as equipment heating mode, part size, steel composition, furnace load amount and equipment power. For full hardening, the purpose of holding is to cause the internal temperature of the part to converge evenly.
For all types of quenching, the holding time ultimately depends on obtaining a good quench heating structure in the required quenching area. Heating and holding are important steps that affect quenching quality. The state of the structure obtained by austenitization directly affects the performance after quenching. The austenite grain size of steel parts is generally controlled in 5 to 8 levels.
Steel Grade | Isothermal temperature /℃ |
Isothermal time /min |
Note | Isothermal temperature /℃ |
Isothermal time /min |
65 | 280-350 | 10-20 | GCr9 | 210~230 | 25-45 |
65 minutes | 270-350 | 10-20 | 9SiCr | 260-280 | 30-45 |
55Si2 | 300-360 | 10-20 | Cr12MoV | 260-280 | 30-60 |
60Si2 | 270-340 | 20-30 | 3Cr2W8 | 280-300 | 30-40 |
T12 | 210~220 | 25-45 |
Quench Cooling
To make the high-temperature phase of steel – austenite, transform into the low-temperature metastable phase – martensite during the cooling process, the cooling speed must be greater than the critical cooling speed of the steel. During the part cooling process, there is a certain difference between the cooling speed of the surface and the core. If this difference is large enough, it may cause the part with a cooling rate greater than the critical cooling rate to transform into martensite, while the core that is lower than the critical cooling rate cannot transform into martensite.
To ensure that the entire cross section turns into martensite, a quenching medium with sufficient cooling capacity needs to be selected to ensure that the core of the part has a high enough cooling speed. But if the cooling speed is large, the internal stress caused by uneven thermal expansion and contraction inside the workpiece may cause deformation or cracking of the workpiece. Therefore, considering the above two conflicting factors, it is important to reasonably choose the quenching medium and cooling method.
The cooling step is not only to obtain a reasonable structure for the parts, achieving the required performance, but also to maintain the accuracy of the size and shape of the parts. It is a fundamental link in the tempering process.
Part hardness
The hardness of the quenched part affects the quenching effect. The hardness of the quenched part is generally determined by its HRC value measured by a Rockwell hardness tester. The HRA value can be measured for thin hard steel plates and surface-hardened workpieces, while for hardened steel plates with a thickness of less than 0.8 mm, surface-tempered parts with a shallow layer, and hardened steel bars with a diameter of less than 5mm, one surface Rockwell hardness tester can be used to measure your HRC values.
When welding carbon steel and certain alloy steels, quenching can occur in the heat-affected zone and become hard, which is prone to cold cracking. This is something to avoid during the welding process.
Due to the hardness and brittleness of the metal after quenching, the residual surface tension generated can cause cold cracking. Tempering can be used as one of the methods to eliminate cold cracks without affecting hardness.
Quenching is best suited for use with parts of small thickness and diameter. For larger parts, the quenching depth is not sufficient and carburizing presents the same problem. At this time, consider adding alloys like chromium to steel to increase strength.
Quenching is one of the basic means of strengthening steel materials. Martensite in steel is the hardest phase in iron-based solid solution structures, so steel parts can obtain high hardness and high strength by quenching. However, martensite is very brittle and there is a large internal quenching stress within the steel after quenching, so it is not suitable for direct application and must be tempered.
Various types of tempering methods
Single medium quenching: The part is quenched in one medium, such as water or oil. The advantages are simple operation, easy mechanization and wide application. The disadvantage is that quenching in water causes high stresses, making the part subject to deformation and cracking; Oil quenching has a slow cooling rate, small quenching diameter, and is difficult to quench large parts.
Medium Double Quenching: The workpiece is first cooled to about 300℃ in a medium with strong cooling capacity, and then cooled in a medium with weaker cooling capacity. This method can effectively reduce the internal stress due to martensitic transformation and reduce the tendency of the part to deform and crack.
Quenching Stage: The piece is tempered in a low-temperature salt bath or alkaline bath, with a temperature close to the Ms point. The piece remains at this temperature for 2 to 5 minutes and is then cooled in air.
Isothermal quenching: The part is quenched in an isothermal salt bath, the temperature of the salt bath is at the bottom of the bainite zone (slightly higher than Ms). The piece remains at the same temperature for a long time until the bainite transformation is completed and is then cooled in air.
Surface Quenching: Surface quenching is a method of partially quenching the surface layer of a steel part to a certain depth, while the core remains unquenched.
Induction hardening: Induction heating uses electromagnetic induction to generate eddy currents in the workpiece for heating.
Cryogenic Quenching: This involves immersion in an ice water solution with strong cooling capacity as a quenching medium.
Partial Hardening: This involves hardening only those parts of the part that need to be hardened.
Gas Cooling Quenching: Specifically refers to heating in a vacuum and quenching in high-velocity circulating negative pressure, normal pressure, or high-pressure inert neutral gas.
Air-cooling quenching: This involves using forced airflow or compressed air as the cooling medium for quenching.
Brine Quenching: This involves using a salt water solution as a cooling medium for quenching.
Organic solution quenching: This involves using an aqueous organic polymer solution as a quenching medium for quenching.
Spray Quenching: This involves using a liquid jet stream as a cooling medium for quenching.
Hot bath quenching: This involves quenching the part in a hot bath, such as molten salt, molten alkali, molten metal, or high-temperature oil.
Double liquid quenching: After the workpiece is heated to form austenite, it is first immersed in a medium with strong cooling capacity, and when the organization is about to undergo martensitic transformation, it is immediately transferred to a medium with weak cooling capacity to cooling.
Pressurized quenching: After heating the part to form austenite, it is quenched under specific clamping, with the aim of reducing quenching cooling distortion.
Complete hardening: This involves complete hardening of the workpiece from the surface to the heart.
Isothermal quenching: The workpiece is rapidly cooled to the bainite transformation temperature range to maintain isothermality after heating to form austenite, allowing the austenite to become bainite.
Quenching Stage: After heating the piece to form austenite, it is immersed in an alkaline bath or salt bath with a temperature slightly higher or lower than the M1 point for a certain time, and after the entire piece reaches the medium temperature, it is removed to air cooling to obtain martensite.
Subtemperature quenching: Hypoeutectoid steel parts are quenched after being austenitized in the Ac1-Ac3 temperature range to obtain martensite and ferrite structures.
Direct Quenching: This involves directly quenching the part after carburizing.
Double Quenching: After carburizing the part, it is first austenitized at a temperature higher than Ac3 and then quenched to refine the core structure. It is then austenitized at a temperature slightly higher than Ac3 to refine the structure of the carburized layer.
Self-cooling quenching: After the workpiece is rapidly heated for local or surface austenitizing, the heat from the heating area spreads on its own to the unheated area, causing the austenitized area to cool quickly.
Tempering application
Quenching is widely used in the modern mechanical manufacturing industry. Important parts in machines, especially steel parts used in automobiles, aircraft and rockets, have almost all undergone quenching. To meet the diverse technical requirements of various parts, various hardening processes have been developed. For example, depending on the parts to be treated, there is total, partial and superficial tempering; depending on whether the phase transformation is complete during heating, there is complete quenching and incomplete quenching (for hypoeutectoid steel, this method is also called subcritical quenching); According to the content of phase transformation during cooling, there are stage quenching, isothermal quenching and underspeed quenching.
Furthermore, due to the characteristics and limitations of each quenching method, they are all used under certain conditions, among which induction heating surface quenching and flame quenching are the most commonly used. Laser beam heating and electron beam heating are rapidly developing high-energy density heating quenching methods. Because they have some characteristics that other heating methods do not have, they are attracting attention.
Surface hardening is widely used on machine parts made of medium carbon hardened steel or ductile iron. Because medium carbon tempered steel can maintain comprehensive mechanical properties in the core and high hardness (>HRC 50) and wear resistance on the surface after pretreatment (tempering or normalizing) and then surface quenching. For example, machine tool spindles, gears, diesel engine crankshafts, camshafts, etc. In principle, surface hardening can be carried out on gray cast iron based on pearlitic ferritic iron, ductile iron, malleable cast iron, alloy cast iron, etc., which are equivalent to the composition of medium carbon steel. The process performance of ductile iron is the best and it also has comprehensive and high mechanical properties, which is why it is the most widely used.
After high-carbon steel is surface quenched, although the surface hardness and wear resistance are improved, the plasticity and toughness of the core are relatively low, so surface quenching of high-carbon steel is mainly used for tools, measuring tools and high cold temperatures. hardened rollers that withstand small impacts and alternating loads.
Because the strengthening effect is not significant after surface quenching of low carbon steel, it is rarely used.