What is spray welding?
Spray welding involves heating a preheated self-soluble alloy powder coating to a temperature range of 1000-1300℃, melting the particles, floating the slag on the surface of the coating, and dispersing the boride and silicide in the coating. This process allows a good combination between the particles and the substrate surface.
The final deposit forms a dense metallic crystalline structure and creates an approximately 0.05-0.1 mm metallurgical bonding layer with the matrix. This bonding layer has a strength of about 400MPa, excellent impact resistance, wear resistance and corrosion resistance, while exhibiting a mirror-like appearance.
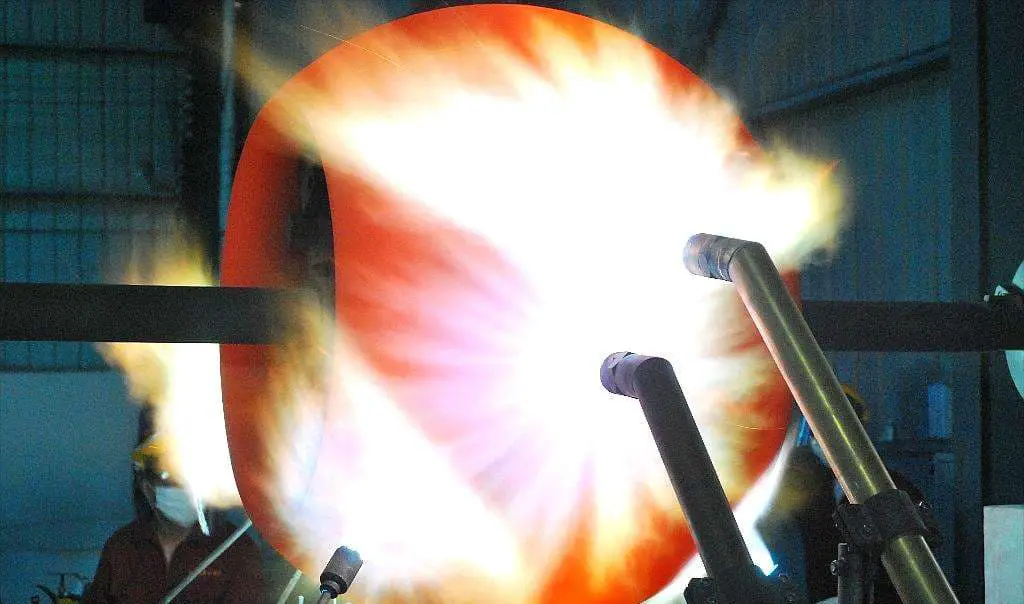
Advantage s of spray welding
Compared to spray coating, spray welding coating offers significant advantages. However, due to the high temperature that the matrix reaches during the reflow process, up to 900°C, greater thermal deformation may occur, leading to certain limitations in the scope of application of spray welding.
Parts and materials suitable for spray welding are generally:
① Vulnerable parts that require high surface hardness and good wear resistance under impact load, such as sander blades, crusher tooth plates, excavator bucket teeth, etc.
② Large vulnerable parts with simple geometries such as shafts, plungers, sliders, hydraulic cylinders and gutter plates.
③ Materials including low-carbon steel, medium-carbon steel (less than 0.4% carbon), structural steel containing less than 3% manganese, molybdenum and vanadium, nickel-chromium stainless steel, cast iron and other similar materials.
Self-fluxing Alloy Powder for Spray Welding
Self-fusing alloy powder is composed of nickel, cobalt and iron as base materials. Appropriate amounts of boron and silicon elements are added to serve as deoxidizing agents, slag formers, welding flux, and to reduce the melting point of the alloy. This type of alloy is suitable for remelting the coating with acetylene-oxygen flame.
There are many types of household self-fusing alloy powders available. Nickel-based alloy powders have strong corrosion resistance, oxidation resistance up to 650°C, and have strong wear resistance.
The cobalt-based alloy powder is characterized by excellent red hardness, allowing it to maintain good wear and corrosion resistance up to 700°C.
Iron-based alloy powder has superior resistance to abrasive wear compared to the other two types.
Spray welding process
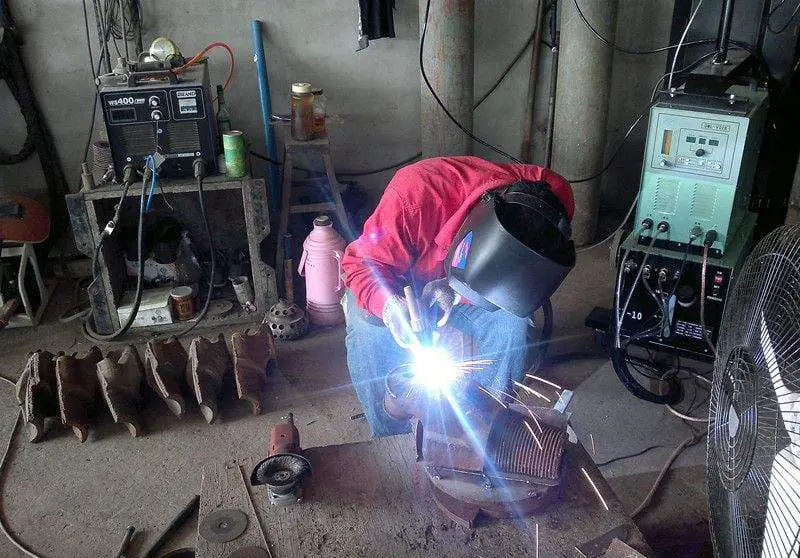
The spray welding process is essentially similar to spraying. However, in spray welding, an additional reflow process is performed during the powder spraying procedure.
Spray welding comprises two types: one-step spray welding and two-step spray welding.
Before starting the process, the following points need to be taken into consideration:
① The carburizing or nitriding layer present on the surface of the part must be removed during pretreatment.
② The preheating temperature of the workpiece should be 200-300°C for common carbon steel and 350-400°C for heat-resistant austenitic steel. A neutral or weak carbon flame should be used for preheating.
It is important to note that the thickness of the sprayed layer reduces approximately 25% after remelting. Therefore, this factor must be taken into account when measuring the hot layer thickness after spraying.
One-step spray welding.
The one-step method involves alternating between spraying and fusing one section at a time using the same spray gun.
Medium and small spray welding guns are available for selection.
Before starting, preheat the piece and apply a 0.2mm protective layer, sealing the surface well to prevent oxidation.
Start spraying and melting from one end, keeping a distance of 10-30 mm.
Heat the protective layer partially in sequence until the melt begins to wet without flowing. Repeat the process, pulverizing and melting the powder until it reaches the predetermined thickness and the surface presents a “mirror” reflection. Then continue expanding forward until the entire surface is covered with the spraying and welding layer.
If the thickness is insufficient, repeat the process.
The one-step method is suitable for small parts or small areas that require spray welding.
Two-step spray welding method.
The two-step method involves first applying the spray coat and then melting it again.
High-power spray guns such as SpH-E welding and spray guns are used to completely melt the alloy powder in the flame and create a layer of plastic deformation deposit on the surface of the workpiece.
Iron-based powder should be pulverized using a weak carbon flame, while neutral or weak carbon flames should be used for nickel and cobalt-based powders.
Each powder spray layer should be less than 0.2mm thick and repeated spraying should achieve the desired reflow thickness of generally 0.5-0.6mm.
If a thick layer of spray welding is required and remelting is not sufficient, it can be sprayed and remelted several times.
Reflow is the key process in the two-step method and must be performed immediately after spraying.
A soft, high-powered flame of neutral flame or weak charring flame should be used.
The spraying distance should be about 20-30mm and the angle between the flame and the surface should be 60°-75°.
Starting about 30mm away from the coating, the remelting speed must be controlled appropriately and the coating must be heated until a “mirrored” reflection of the coating appears before remelting the next part.
During remelting, it is necessary to avoid excessive melting (i.e. cracking of the mirror surface), runoff of the coating metal, or oxidation of the surface due to excessive local heating time.
During multilayer remelting, the previous layer must be cooled to about 700°C and the surface slag must be removed before secondary spraying.
Refusion should not be done more than three times.
Cooling of the workpiece.
Medium and low-carbon steel parts, low-alloy steel parts and thin-layer welding iron castings with simple shapes can be naturally cooled in air.
However, for iron castings with thick welding layer and complex shape, alloy steel castings with high manganese, copper and vanadium content and parts with high hardness, should be buried in lime pits for slow cooling.
Process Difference Between Spraying and Spray Welding
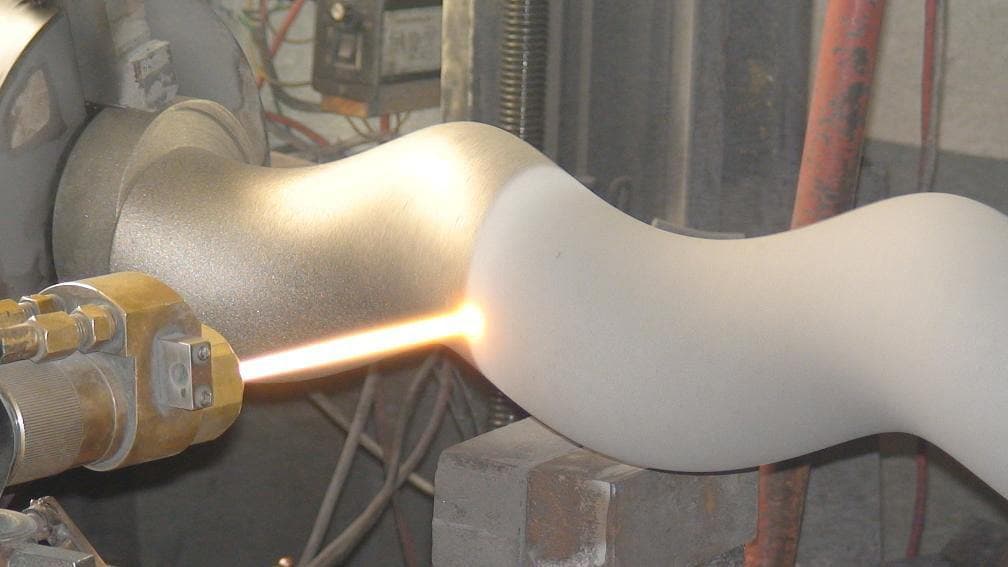
The combination of spray layer and spray welding layer with base metal is different.
When heating nickel-coated aluminum with a sprayed flame beam, an exothermic chemical reaction occurs and sandblasting rust removal reaches Sa3, RZ>50 μm. The carbon steel surface forms a mechanical bond coating with a micrometallurgical bond bottom layer and a working layer, which also produces an “anchor hook” effect. In contrast, the bond between the spray welding layer and the substrate is purely a metallurgical bond coating.
Different spraying materials require the use of self-fusing alloy powder for spray welding, while spraying requires low self-fusing powder, which is not necessarily self-fusing alloy powder.
Various self-fusing alloy powders can be used for both spray and spray welding, but spray powder does not have self-fusing. Therefore, it can only be used for spraying and not for the spray welding process.
The workpiece is heated differently during spraying and spray welding, and the preheating temperature before spraying is also different. As a result, the microstructure and properties of the part after spraying are also different.
The coating density also differs, as the spray welding layer is dense, while the spray coating has some pores.
Furthermore, the load-bearing capacity is different. Generally, spray coating can withstand contact over large areas and is mainly used on lubricated work surfaces, contact surfaces and other working conditions with less stress. However, spray welding coating can withstand large impact forces, extrusion stresses or contact stresses.
Spray welding application
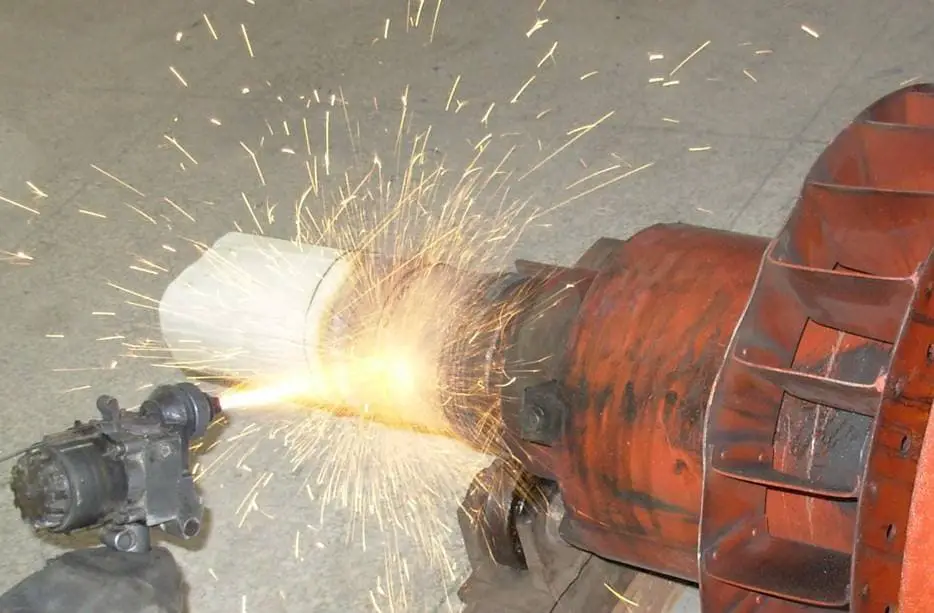
(1) The surface load on parts made of various carbon steels and low-alloy steels is significant, especially under impact loads.
For parts with bond strength between coating and substrate of 350-450N/mm 2 spray welding hardness HRC150 ≤ 65, coating thickness ranging from 0.3 to several millimeters and surface roughness of the spray welding layer after grinding reaching Ra0.4-0.1 μm above.
(2) When used in corrosive media, the coating must be compact and free of pores.
(3) The original surface design of the part adopts quenching, carburizing, nitriding, hard chrome plating and other processes, requiring the surface to have high hardness.
(4) The working environment of the workpiece is poor, such as strong abrasive wear, erosion wear, cavitation, etc.
(5) The oxyacetylene flame alloy powder spray welding process is suitable for surface reinforcement or repair of various carbon steel and low alloy steel parts, but some characteristics of the part materials must be observed.
When the coefficient of linear expansion of the base material is very different from that of the alloy spray welding layer, that is, less than 12 × 10 -6 /℃ or greater than 12 × 10 -6 /℃, this process should be used with caution to avoid cracking.
If the content of elements with high oxygen affinity in the base metal is greater than 3%, such as tungsten and molybdenum, the total content of aluminum, magnesium, cobalt, titanium, molybdenum and other elements is greater than 0.5%, or the sulfur content in steel is higher, it will also cause difficulties for spray welding.
This occurs because these materials generate a dense and stable oxide film under the action of oxygen, blocking the wetting effect of the molten alloy on the base.
During remelting, the liquid alloy will roll like beads, like “drops of sweat”.
Therefore, when using the spray welding process, attention should be paid to the adaptability of this process to the sprayed base material.
(6) Metal materials that can be spray welded without special treatment:
① Carbon structural steel with carbon content ≤ 0.25%.
② Structural steel alloy with total Mh, Mo, V, Cr and Ni content <3%.
③ 18-8 stainless steel, nickel stainless steel, gray cast steel, malleable iron, ductile iron, low carbon pure iron, red copper.
(7) Metal materials that require slow cooling after spray welding at 250-375 ℃ must be preheated:
① Carbon structural steel with carbon content >0.4%;
② Manganese, molybdenum and vanadium alloy structural steel with total nickel content > 3%;
③ Structural alloy steel with chromium content ≤ 2%;
(8) Metal materials requiring isothermal annealing after spray welding:
① Martensitic stainless steel with chromium content ≥ 13%;
② Nickel-molybdenum alloy structural steel with carbon content ≥ 0.4%.
After determining the spray welding process, the selection of one-step or two-step spray welding process should be based on the following conditions:
(1) If the workpiece requires local repair and the spray welding position cannot tolerate large heat input, use the one-step spray welding process. For example, repair of local scars on various machine tool guides can be done through this process.
(2) If the surface of the part is complex or irregular, such as sprockets, gear tooth surfaces, screw feeders, etc., use the one-step spray welding process.
(3) For large parts that are difficult to heat as a whole, such as locomotive and tram wheels, the one-step spray welding process should be used.
(4) For general shaft parts that can rotate on the machine tool, use the two-step spray welding process.
(5) The hardness of the coating should be as close as possible to the surface hardness of the original design. For example, if the original design surface hardness is HRC≥55, which was achieved through quenching processes or chemical treatment, the “hard coating” powder, such as Ni 15 Ni 60 Fe 65 or Wc composite powder, should be used.
(6) Highly worn non-conjugate surfaces such as impellers, mud pump casings, rock loader blade teeth, spiral feeder surfaces, etc. should be made of high hardness composite powders such as Ni 15 Ni 60 Faith 65 or Wc.
(7) Workpieces that cannot be processed on lathes and grinding machines but need to be processed can only be done manually with files and other tools. For example, repairing local scars on the surface of the machine tool guide rail requires the use of only low hardness spray welding powders such as SH, F 103 Ni 15 etc.
(8) Differences between spray welding and arc coating processes:
During the spray welding process, the bond between the spray welding layer and the matrix is a solution diffusion metallurgical bond, while the surface uses a fusion metallurgical bond.
The matrix does not melt during the spray welding process, but there is a dissolution effect between the spray welding layer and the matrix, resulting in a mutual solution diffusion zone between the two.
Since the matrix is insoluble, the spray welding layer will not be diluted by the base material. Therefore, the dilution rate is extremely low, ensuring good performance of the spray welding layer.
In contrast, the overlay welding matrix is melted and the dilution rate of the overlay welding layer is high. The performance of the welding layer can only be guaranteed if the welding overlay is too thick, making it difficult to guarantee the edges and corners of the part contour. This can lead to common defects such as undercuts and corner collapses. However, spray welding does not have such defects.
Features of spray welding of cast iron parts
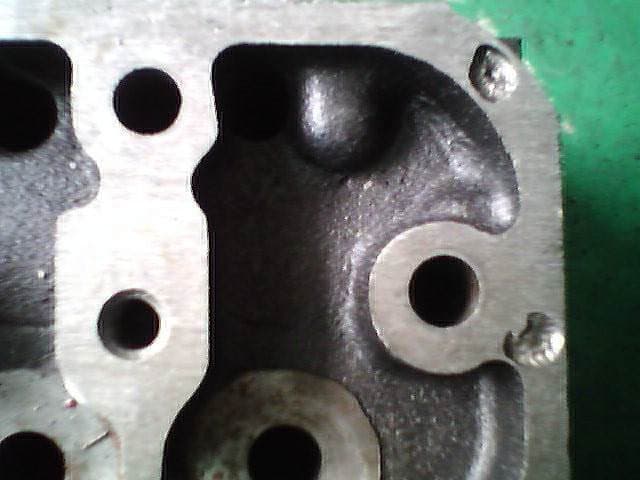
(1) Cast iron is an iron-carbon alloy with a carbon content greater than 2%. It is widely used in various industries, typically containing 2.5% to 4% carbon, 1% to 3% silicon and small amounts of manganese, sulfur, phosphorus, etc.
Cast iron has a high carbon content, low strength and is sensitive to temperature changes. During welding repair, it experiences local heating, large temperature differences and rapid cooling rates. As a result, welding cast iron is challenging.
The poor weldability of cast iron leads to several problems during welding repair:
(2) The welding repair part can easily develop a white microstructure that is hard, brittle and difficult to machine. Such a structure also tends to crack easily.
(3) Rapid heating and cooling rates during welding repair can cause thermal stress cracking. Furthermore, the presence of impurities such as sulfur and phosphorus in cast iron increases the likelihood of cracks during weld repair.
(4) Porosity and slag inclusion are also common problems. Due to the high carbon content, more impurities and rapid cooling rates in the welding repair process, gases and oxides cannot precipitate and float over time, leading to the formation of porosity or slag inclusion in the weld zone.
Fortunately, one-step spray welding with oxygen-acetylene flame alloy powder can solve these problems satisfactorily.
(5) The melting point of the alloy powder used in spray welding is lower than that of the matrix. During remelting, the cast iron matrix does not melt, thus avoiding the problem of dilution of the spray welding layer and the creation of a semi-molten zone. Consequently, correct spray welding does not produce a white microstructure in the weld repair area, facilitating processing.
Additionally, because the matrix does not melt, it naturally prevents impurities such as sulfur and phosphorus from melting into the spray welding layer, which helps prevent cracking.
(6) The one-step spray welding process involves less heat input to the substrate and has a smaller thermal effect on the substrate, making it more effective in controlling thermal stress cracking. The low heat input is particularly advantageous when repairing parts with high dimensional accuracy.
In addition, the use of oxygen-acetylene flame heating, which is slower than electric welding cooling, is also helpful in preventing cracking and deformation.
(7) The alloy powder used in spray welding contains strong deoxidizing elements such as boron and silicon. These elements protect other dust elements from oxidative burning and reduce oxides on the surface of the matrix, thus preventing the formation of pores and slag inclusion.
(8) The spray welding layer has a compact and flat structure, is well formed, has no undercuts, and only requires a small amount of processing. This results in material savings and high efficiency. Spray welded cast iron parts generally use SH F103, Ni15 nickel-based alloy powder, etc. However, iron-based alloy powder has a high melting point, high brittleness, significant impact on the matrix, and poor performance.
(9) During spray welding, the main purpose of preheating the part is to remove moisture from the surface of the part and generate some thermal expansion. This reduces the temperature difference, thus minimizing thermal stress and promoting better bond strength of the spray welding layer.
Preheat temperatures generally range from 250-300°C for steel, 450-500°C for austenitic stainless steel, 350-400°C for nickel-chromium stainless steel, and 250-300°C for low-alloy steel and cast iron. For small parts and easily oxidized steel, the preheating temperature is lower.
The thickness of the spray welding layer depends on the thermal expansion and cold contraction characteristics of the workpiece after spraying. Shrinkage after remelting is typically around 25-30%. Therefore, when determining coating thickness, machining tolerance and part diameter before spraying must be taken into consideration, along with shrinkage.
The spray coating thickness is calculated as follows: Coating thickness before remelting = (spray welding layer thickness + machining tolerance) ÷ (1-0.3).
Related reading: How to weld cast iron?
Circumstances in which the spray welding process cannot be used.
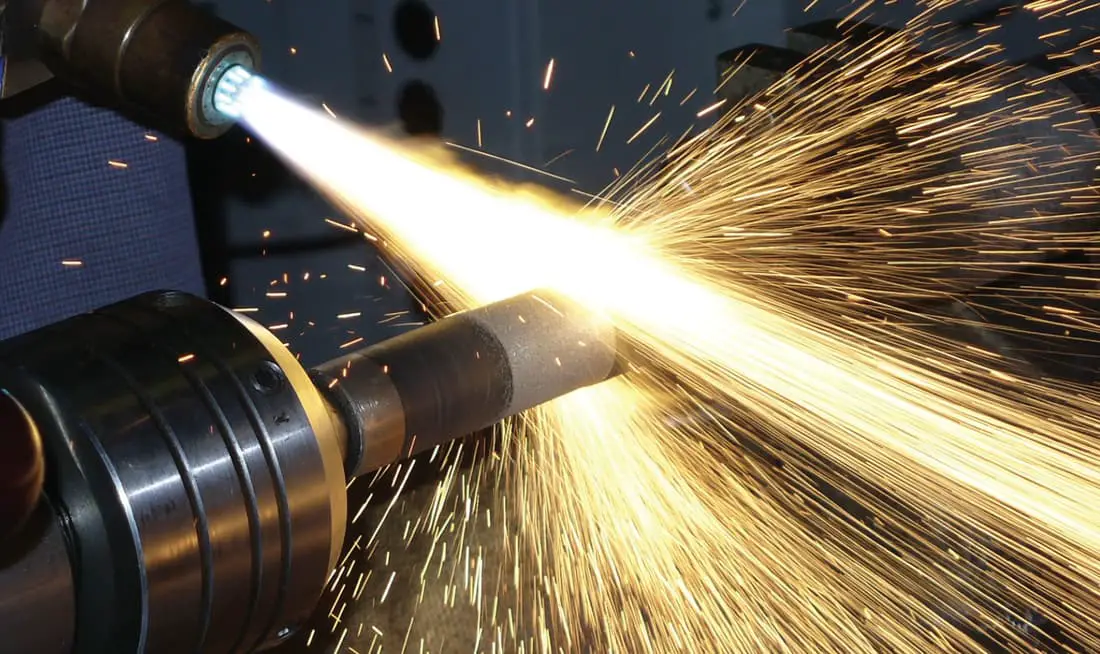
(1) Materials with a lower melting point than alloys, such as aluminum and its alloys, magnesium and its alloys, brass and bronze.
(2) The workpiece is a slender shaft or a very thin plate that must not deform.
(3) The original design requirements of the part are very strict and the metallographic structure cannot change.
(4) Nickel-chromium-molybdenum alloy steel with high hardenability.
(5) Martensitic steel with high chromium content and chromium content greater than 18%.
(Note: High-precision spray welding can be performed on long shafts with an outer diameter of more than 28 mm and a length of less than 8 m.)
Key Points of Spray Welding Process for Iron Castings
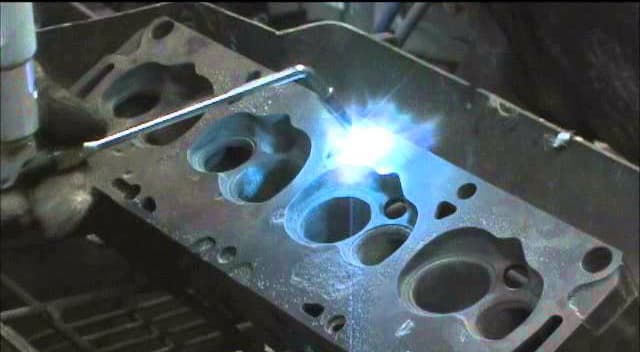
① There are many parts in vehicles and mechanical equipment made of cast iron, and various problems are inevitable during manufacturing or use. The oxygen acetylene flame spray welding process is not only an effective way to strengthen cast iron, but also an ideal means to repair various defects and damages such as sand holes, air holes, wear and other damage in castings.
② Spray welding is mainly used to repair local defects of iron castings, which vary in size and depth. It is suitable for one-step spray welding. Small power spray guns should be used as much as possible to reduce heat input to the substrate, depending on the part parts and welding repair required. Generally, QH-1/h, QH-2/h, QH-4/h, etc. are selected.
③ During spray welding, nickel-based alloy powder (Ni-B-Si series) should be preferred due to the poor weldability of cast iron parts. The melting point of nickel-based alloy powder is generally 950 ~ 1050 ℃, and the matrix does not melt during remelting. At the same time, the low carbon nickel-based powder spray welding layer has low hardness and good plasticity. The stress relaxation of spray welding is helpful in preventing cracking, which is extremely important for unskilled operators.
④ When selecting spray welding specifications, factors such as cast iron material, size of defective parts and working condition requirements should be considered. It is important to ensure the required flame energy and, at the same time, minimize heat input to the substrate. Appropriate oxygen and acetylene gas pressure limits must be followed, and the spraying and melting distance must be adjusted appropriately during powder spraying and remelting to control heat input.
⑤ Small local defects such as air holes and sand holes can be repaired by welding without preheating before spray welding. The heating area around the spray welding layer should be minimized to make the high temperature area as small as possible.
⑥ For the repair of small and deep local defects, continuous spray welding is suitable. This method has a high powder deposition rate, rapid thickness growth and high efficiency, but requires qualified operation technology to coordinate the powder feeding amount with the spraying and melting speed to achieve uniform spraying and penetration.
⑦ For large and deep defects, intermittent spray welding can be used to prevent an increase in thermal stress due to excessive heating of the substrate. Electric welding and spray welding can also be used, and welding rods can be used to fill the bottom and top parts for spray welding. If the wall thickness of the casting is large, pre-sprayed wire planting can be used to increase bond strength, prevent the spray welding layer from detaching from the base metal, and eliminate some of the thermal stress of spray welding. spray.
⑧ Large and complex castings for spray welding often experience high thermal stress, therefore measures must be taken to reduce stress build-up during spray welding, such as using heating stress reduction methods and the symmetry method of subsection. Preheating before welding and slow cooling after welding can also achieve good results.
⑨ It is important to control the reflow temperature during spray welding. If the temperature is too high, the alloy elements may burn, the die may overheat and even melt, resulting in carbon from the cast iron entering the spray welding layer. This increases the carbon content, hardness and reduces plasticity, which can cause greater thermal stress leading to the formation of cracks. However, if the reflow temperature is too low, it may lead to ash inclusion or impenetrability and affect the bond strength. Operators should pay attention to the condition of the coating surface during reflow and remove the reflow gun immediately as soon as the “mirror reflection” is displayed, indicating that the powder has melted and the slag has floated. Recast parts must not be reheated.