The objective of mechanical lubrication is to reduce friction and wear between the contact surfaces of two relative moving parts, called friction pairs.
Proper lubrication can increase mechanical efficiency, ensure long-term reliable operation of machines, and conserve energy.
Machines with poor lubrication, at best, experience decreased power and increased wear; in the worst case, they can be damaged.
I. Concept of Friction and Lubrication
When two objects in close contact move relative to each other along their contact surface, a resistance is generated that makes this movement difficult; This phenomenon is known as friction and this resistance is called frictional force.
The relationship between the friction force and the vertical load is called the coefficient of friction. The laws of friction can be described as follows:
1. The friction force is proportional to the normal load: F∝W.
2. The friction force is independent of the surface contact, that is, it is not related to the size of the contact area.
3. The friction force is not influenced by the magnitude of the surface sliding speed.
4. Static friction (when movement tends to occur) F S is greater than kinetic friction F K that is, Fs > F K .
Frictional law formula:
F = f · W or f = F/W
Where:
- f — Friction force;
- W — Normal load, which is the load received by the contact surface.
In machines, a connection consisting of two parts that contact and move relative to each other is called a “kinematic pair” (also known as a “friction pair”), such as the slide and guide rail in machine tools; the ball and race in bearings; the bushing and shaft diameter in plain bearings and so on.
The operation of any machine depends on the relative motion of several kinematic pairs, and this relative motion inevitably results in friction.
Friction primarily causes unnecessary loss of energy and secondly, it produces heat, wear and even failure on the interacting surfaces of the rubbing pairs.
Wear is the continuous loss of material from the surfaces of kinematic pairs. This leads to changes in the size and shape of these pairs, resulting in damage. For example, as oil circulates inside a bearing, the bearing bore surface and shaft diameter gradually wear.
This wear increases clearance, generates heat and reduces machine precision and efficiency. Along with this comes the generation of impact loads, increased friction losses and an accelerated rate of wear, ultimately leading to machine failure.
Lubrication involves applying a lubricant to the surfaces of parts that move relative to each other. This application separates the two moving surfaces, ensuring that friction does not occur directly between the surfaces of the kinematic pair, but between the molecules within the lubricant.
Therefore, friction is the physical phenomenon that occurs when kinematic pairs move relative to each other, wear is a fact that accompanies friction, and lubrication is a critical measure to reduce both friction and wear.
II. Friction Classification

There are several methods for categorizing friction.
1. Classification Based on Movement State
Static Friction: This refers to the friction that occurs when one object tends to move relative to the surface of another. The resistive force in this case is known as static friction force.
The force of static friction varies with the external force applied to the object. Only when the external force overcomes the maximum static frictional force does the object begin to visibly move.
Kinetic Friction: This is the friction that occurs when one object moves relative to the surface of another. The tangential force that prevents the object from moving in this situation is known as the force of kinetic friction.
2. Classification Based on Contact Method
Sliding Friction: The friction that occurs when the contacting surfaces slide relative to each other is called sliding friction.
Rolling Friction: The friction that arises when an object rolls along the contact surface under the action of a torque is called rolling friction.
3. Classification Based on Surface Lubrication Status
Dry Friction: Refers to friction where there is no lubrication or moisture.
Fluid Friction: This is friction under fluid lubrication conditions. Here, the two surfaces are completely separated by a film of liquid oil and friction manifests itself as a result of the viscous fluid.
Limit Friction: This type of friction occurs when there is a very thin layer of lubricant on the friction surface. In this case, friction does not depend on the viscosity of the lubricant, but on the characteristics of the contact surface and the lubricant.
Mixed Friction: This refers to a transient state of friction, including semi-dry and semi-fluid friction. Semi-dry friction is a situation in which limit and dry friction occur. Semi-fluid friction is a condition in which both fluid and dry friction occur.
In some chemical and petroleum refining equipment, the working conditions of friction pairs may be complex, such as operating at high speed, high temperature, or harsh conditions such as low temperature and vacuum. The friction and wear characteristics under these conditions have unique and different characteristics.
III. Causes of friction
There are several explanations for the phenomenon of frictional force generated when contacting surfaces move relative to each other. A comprehensive summary reveals the following points:
Machine parts that undergo relative movement are generally processed and have smooth surfaces. However, in reality, no matter how precise the processing, the surface of a component can never be “absolutely” smooth. Under a microscope, it is always irregular, with high and low points, as shown in Figure 1.
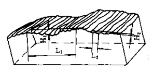
When the protrusions and recesses on the friction surface, under load and in close contact, interlock like the teeth of a cogwheel, collisions occur between these protrusions during the relative motion of the two contacting surfaces, thus preventing their relative motion.
Furthermore, due to the load-bearing capacity and the close contact of the two friction surfaces, the surface is supported by several protrusions. The distance between the two surfaces at the fulcrums is extremely small, within the range of molecular forces. When the surfaces move relative to each other, the protrusions must also move, which means overcoming the molecular forces at the fulcrums.
Furthermore, both the collision points and the support points support extreme pressures, leading to severe deformation of the metal surfaces in these locations, causing the protrusions of one surface to become embedded in the other. Both collisions and plastic deformation result in localized instantaneous high temperatures, and the rupture of bonded points consumes energy.
The combined effect of all these factors manifests itself as friction.
4. Dress
The phenomenon of continuous loss of material from the working surface of an object, due to the relative movement of the surface, is called wear.

The wear process of mechanical parts during normal operation is generally divided into three stages, as shown in Figure 2.
(1) Running-in stage (also known as softening stage): The new surface of the friction pair has a certain roughness, with a relatively small actual contact area. During the running-in stage, the surface gradually softens and the actual contact area progressively increases, decreasing the wear rate, as indicated by segment OA in Figure 12-2. Light wear during the break-in stage is intentionally used to define stable wear conditions during normal operation.
By choosing a reasonable running-in procedure, selecting appropriate friction pair materials and machining processes, and using lubricating oil with active additives (running-in oil), the running-in period can be shortened. The oil must be changed as soon as break-in is complete.
(2) Steady Wear Stage: During this stage, wear occurs at a slow and steady rate, as shown by segment AB in Figure 12-2. The slope of this segment indicates the wear rate and the time on the x-axis represents the wear-resistant life of the part.
(3) Severe wear stage: After point B in Figure 12-2, the wear rate increases sharply, leading to a decrease in mechanical efficiency, increased power and loss of lubricating oil, loss of precision, abnormal noise and vibration , rapid increase in the temperature of the friction pair and, finally, failure of the part. There are also times when the following situations occur:
ⅰ After transitioning to the stable wear stage, the part experiences minimal wear over a long period of time, with no obvious severe wear stages, resulting in a longer service life.
ⅱ There is no noticeable wear during the running-in and steady-wear stages, but severe wear occurs when the surface layer reaches its fatigue limit.
ⅲ Under severe wear conditions, the part directly passes into the severe wear stage after the running-in stage, preventing the machine from operating normally.
Based on the destruction mechanism of wear and the surface wear condition of mechanical parts, wear can be classified into several types.
1. Adhesive wear
Adhesive wear refers to the phenomenon where material from one surface is transferred to another due to solid phase adhesion during the relative movement of friction pairs. This can lead to serious jamming of the friction pairs.
2. Abrasive wear
Abrasive wear is the phenomenon where hard particles or protrusions cause loss of material during the friction process.
3. Fatigue surface wear
Surface fatigue wear occurs when two contacting surfaces roll or slide in combination, causing material loss due to fatigue on the material surface under alternating contact pressure stress. Gear pairs, bearings, wheel rails and rims, and cam pairs can produce surface fatigue wear.
Surface fatigue wear is classified into expansive and non-expansive types. Expansive surface fatigue wear may occur due to slightly poor plasticity of the material or improper selection of lubrication when the alternating pressure stress is high.
4. Delamination wear
The theory of delamination wear suggests that when two sliding surfaces come into contact, they transfer normal and tangential forces through the contact points. The microprotrusions of the harder surface cause plastic deformation of the softer surface during sliding.
Repeated force transfers and increased plastic deformation of the surface cause voids to appear in the subsurface (10 ~ 100 μm deep). Voids are likely to occur at grain boundaries in metallography or at the interfaces of contained impurities. Under repeated forces, the voids enlarge and connect with adjacent voids to form cracks.
Influenced by tangential forces, cracks develop in directions parallel to the surface. When the cracks reach a certain length, they extend to the surface, causing the surface layer to peel off and form long, fine wear debris.
5. Electrical erosion wear
Electrical erosion wear occurs mainly in rotating electrified equipment. Due to the electrified state of the equipment, there is a potential difference between the shaft neck and the bearing.
This potential difference can lead to superficial damage to the friction surface for several reasons. Surface damage caused by electrical erosion wear typically manifests as pitting corrosion.
6. Corrosive Wear (also known as Corrosive Mechanical Wear)
When friction occurs in a corrosive environment, a chemical reaction occurs on the friction surface, generating reaction products.
Generally, these reaction products adhere loosely to the surface and are easily worn away in the subsequent rubbing process.
The newly exposed metal surface then generates additional reaction products. This cycle continues, gradually wearing away the metal surface. Corrosive wear requires the occurrence of corrosion and friction.
7. Wear and tear
Frictional wear is caused by vibrational slip with an amplitude range of 10-7 to 10-5 mm and generally occurs on parts at mechanical joints (such as screws, splines, etc.). These parts wear out due to vibrational loads.
8. Erosion
Erosion refers to the damage suffered by the surface of an object after impact with a particle-laden fluid.
Erosion is a major problem for components operating at high speeds, for example carbon fiber reinforced plastic turbine blades, which are highly dense and strong. The leading edge of the blade must be highly resistant to erosion.
V. Lubrication

Lubricating oil (agent) is introduced between the contact surfaces of several friction pairs that undergo relative movement.
This forms a film of lubrication between the two friction surfaces, separating the original dry friction surfaces from direct contact and converting the dry friction into friction between the lubricating oil (agent) molecules.
This reduces friction, reduces wear and extends the life of mechanical equipment – this is lubrication.
1. Lubrication Requirements
Lubrication requirements vary depending on the function, working conditions and nature of each friction pair. In summary, the following points are considered:
(1) Select the appropriate lubricating oil depending on the working conditions and the functional nature of the friction pair.
(2) Determine the correct lubrication method and approach based on the working conditions and functional nature of the friction pair, and distribute the lubricating oil to each friction surface in a defined manner.
(3) Maintain good lubrication management.
2. The role of lubricating oil
The purpose of using lubricating oil is to lubricate the friction parts of machines, reducing friction resistance, preventing seizure and wear and minimizing energy consumption to increase mechanical efficiency. In addition, there are other practical benefits, summarized below:
(1) Reducing friction. The introduction of lubricating oil between the friction surfaces can decrease the coefficient of friction, thus reducing frictional resistance and conserving energy consumption. Lubricating oil viscosity and film thickness play a crucial role in minimizing friction under fluid lubrication conditions. The chemical properties and activity of lubricating oil (additives) become extremely important when limiting lubrication conditions arise due to an increase in metal-to-metal contact points at the friction interface.
(2) Reduction of adhesive wear of mechanical parts. Surface fatigue wear and corrosion wear are closely related to lubrication conditions. The inclusion of antioxidants and anticorrosive agents in lubricants can help suppress corrosion wear, while the addition of oil and pressure resistance agents can effectively reduce adhesive wear and surface fatigue wear.
(3) Cooling effect. Lubricating oil can alleviate friction and absorb, conduct and dissipate heat, thereby reducing the temperature rise caused by friction from mechanical operation.
(4) Anti-corrosion effect. When a friction surface is covered with a lubricant, it can prevent or avoid corrosion and rust caused by air, water droplets, steam, corrosive gases and liquids, dust, oxides, etc. of the oil film retained on the metal surface and also depends on the composition of the lubricant. The use of certain surfactants as rust inhibitors can increase the rust resistance of the lubricant.
(5) Insulating properties. The electrical resistance of refined mineral oil is high, just as the electrical resistance of electrical insulating oil used as electrical insulating material is 2×10¹⁶Ω/mm² (water is 0.5×10⁶Ω/mm²).
(6) Force transmission. Oil can serve as a means of transmitting static force, such as hydraulic oil in automobile cranes. It can also act as a means of transmitting energy, such as automatic transmission fluid.
(7) Vibration reduction. The lubricating oil absorbed on the metal surface has low inherent tension, therefore it has the ability to absorb shock when the friction pair is subjected to impact load. For example, automobile shock absorbers use fluid damping (converting mechanical energy into fluid energy).
(8) Cleansing effect. Lubricating oil (grease) forms a seal on certain exposed parts, preventing moisture or debris from entering.
3. Various lubrication states
According to the lubrication state on the surface of the friction pair, the types of lubrication can be divided into: fluid lubrication, boundary lubrication and mixed lubrication, as shown in Figure 3.

(1) Fluid lubrication.
The liquid lubricant is applied between two friction surfaces, the lubricating oil completely separates the two friction surfaces, transforming dry metal-to-metal friction into internal friction within the liquid. This is fluid lubrication (see Figure 4).
The advantage of fluid lubrication is that the internal frictional force of the liquid lubricant is small, typically ranging from 0.001 to 0.01, just one thousandth of that of direct metal-to-metal contact. The conditions for achieving fluid lubrication are:

(a) There must be relative movement between the friction surfaces.
(b) In the direction of surface movement, the oil layer should form a wedge.
(c) The lubricating oil must have a certain adhesive force with the friction surface. This is related to the properties of the oil. When the lubricating oil moves with the friction surface, it must have a certain internal friction force, that is, it must have a certain viscosity.

Using a sliding bearing to form fluid lubrication as an example, as shown in Figure 5. When the shaft is not rotating (Figure 5a), the lubricating oil on the contact surface of the shaft and the bearing is completely squeezed out. As the shaft begins to rotate in the direction of the arrow (see Figure 5b), due to the adhesive force between the shaft surface and the shaft, and the internal friction in the oil layer, the entire wedge-shaped oil layer in the The bottom right part of the bearing is moved forward with the shaft, as if a wooden wedge were inserted into a narrow slot to force the gap open, forcing the shaft to lift and deflect slightly to the left.
As the shaft rotation speed increases, the shaft position also increases further and the eccentricity decreases (as in Figure 5c). When the rotational speed of the shaft is infinitely large, the centers of the shaft and the bearing must coincide (add Figure 5d).
The thickness of the oil layer between the friction surfaces of the shaft and bearing is determined by the load supported by the shaft and the size of the internal friction of the oil layer. The size of the internal friction of the oil layer depends on the viscosity of the oil and the relative speed of the shaft and bearing movement.
It can be represented by the bearing characteristic factor G:
G = η·N/P
Where: η is the viscosity of the lubricating oil;
- N is the bearing speed (P·s);
- P is the load on the projected area of the shaft (N/m2).
The direct relationship between the G value and the thickness of the lubricating oil, a lower G value results in a thinner oil layer and vice versa, a thicker oil layer is formed. Therefore, using the G value, it can be determined whether a sufficiently thick oil layer can be formed to ensure fluid lubrication.
However, it should be noted that as the types of lubricated components, geometric configurations and machining accuracy are all different, there is no minimum value of G to ensure fluid lubrication. Generally speaking, when the sliding speed is high and the load is light, oil with lower viscosity should be chosen; when the sliding speed is low and the load is heavy, oil with higher viscosity should be selected.
(2) Limit Lubrication
Fluid lubrication is ideal, but aside from bearings and guides with relatively low contact pressure intensities, achieving fluid lubrication is challenging.
When mechanical operation occurs at an extremely low speed (e.g. checking the speed of movement at 0.1 cm/s) and the surface friction load is substantial, even using highly viscous lubricating oil, it is difficult to generate a sufficient G value to form a complete rotation. layer of oil between the friction surfaces, necessary to guarantee the level of fluid lubrication.
At such times, even if the fluid lubrication film is damaged, a very thin oil film (about 0.01 μm) remains on the contact surface. This thin layer of oil has a unique bonding force with the friction surface, forming a “film” that continues to protect the friction surface to some extent.
This lubrication state is called boundary lubrication (as shown in Figure 6), and the film formed is called boundary film. As the boundary film thickness is minimal, the surface texture properties of the friction surface can significantly influence the lubrication conditions.

Based on different structural forms, boundary films can be categorized into two types: adsorption films and reaction films.
Adsorption films are formed by the adsorption of polar lubricant molecules onto the friction surface, while reaction films are generated through the chemical reaction of additives, such as sulfur, phosphorus and chlorine in the lubricant, with the friction surface.
If the load is extremely high, overcompression at the peak points of the friction surface can lead to rupture of the adsorption film, resulting in direct metal-to-metal contact and causing dry friction.

(3) Semi-fluid lubrication (mixed lubrication)
The lubricating film formed on the friction surface is damaged locally, causing the oil to become irregular and discontinuous. This results in simultaneous occurrences of liquid lubrication, boundary lubrication and underlubrication on the friction surface, called semi-fluid lubrication, as shown in Figure 7.
The main causes of semi-fluid lubrication include excessive loads, frequent speed and load changes, improper lubricant selection and rough friction surfaces.
The three aforementioned lubrication states frequently alternate during machine operation, rarely existing independently; there is only a distinction between primary and secondary states. These conditions change with changes in oil volume, oil properties, and other factors.
Therefore, it typically strives to improve lubricating conditions by increasing oil supply and pressure, improving oil properties, and selecting appropriate viscosity.
SAW. Classification of lubricating oils
Lubricating oils can be categorized into various types based on different usage requirements. According to the General Classification of Petroleum Products and Lubricants GB498-87, petroleum products and lubricants are divided into six main categories. The classification principle is based on the main characteristics of petroleum products.
Category names are determined by a letter prefix to the name in English that reflects the main characteristics of each type of product, with lubricants and related products designated as class “L”. Due to the wide variety and wide application of lubricants and related products, categorizing them all as class “L” based on the general classification of petroleum products can lead to numerous inconveniences.
Therefore, “L” class products are divided into 19 groups according to their main application scenarios. Each group has a separate classification standard. The detailed classification of a group is determined by the product type, but the type must meet the main application scenario required by the group. The grouping of class “L” products is shown in Table 1.
Table 1:
Category | Application Scenario | Category | Application Scenario |
A | Total Loss System | P | Pneumatic tools |
B | Demoulding | P | Thermal Conduction |
W | Gears | R | Temporary corrosion protection |
D | Compressors (including refrigerators and vacuum pumps) | T | steam turbines |
AND | Internal combustion engines | you | Heat treatment |
F | Spindles, bearings and clutches | X | Scenarios for grease lubrication |
G | Guides | s | Other application scenarios |
H | Hydraulic Systems | Z | Steam Cylinders |
M | metal processing | s | Application scenarios of special lubricants |
N | Electrical insulation |