What is press brake bending?
Press brake bending involves the elastic deformation of sheet metal under the pressure of the upper or lower die of a press brake, followed by plastic deformation.
At the beginning of the plastic bending, the sheet is free to bend. With the pressure of the upper or lower die applied to the plate, it gradually adapts to the inner surface of the V-groove of the lower die, with the bending radius and bending force arm decreasing.
This continues until the upper and lower dies are in full contact at the end of the stroke, forming a V-shape, known as flexure.
In general, press brake bending is a process technology that modifies the plate or plate angle by exerting pressure on it.
Bending is an incredibly widespread application, visible wherever sheet metal is used, and it can be said to affect all aspects of life. The purpose of a press brake is to bend flat sheets into a variety of three-dimensional parts needed for practical applications.
How is this achieved? By placing the sheet metal horizontally in the lower die, positioning it using a back gauge, and pressing the metal into the V-groove of the lower die with the upper die to achieve the desired bend angle, the flat sheet is transformed into a three-dimensional part. , as shown in the Figure below.
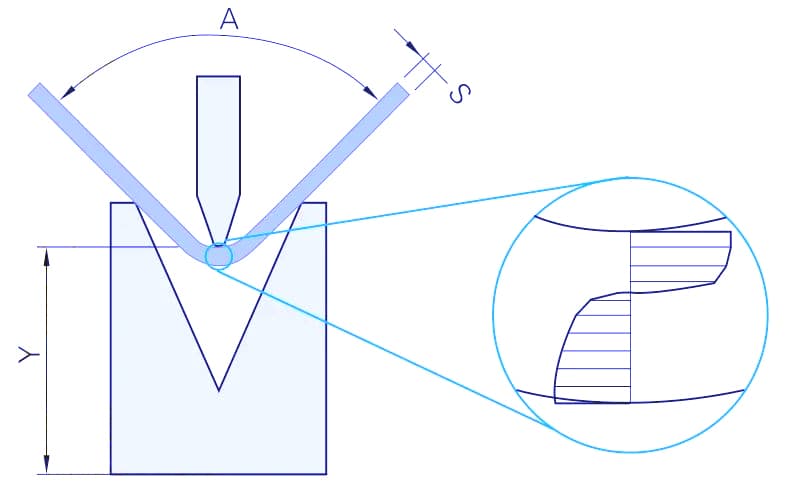
Working principle of press brake
The upper and lower dies are mounted on the upper and lower working tables of the press brake, respectively. The relative movement of the work tables is driven by hydraulic transmission, and their shape, in combination with the upper and lower dies, allows the formation of plate bending.
Bending Principles
Bending is essentially a cold deformation process that bends sheet metal into a specific shape. It is a pressure processing method carried out at room temperature, capable of bending metallic materials, non-metallic materials and composite materials.
In this processing method, the part is machined based on the bending mold and hydraulic equipment. The dimensional accuracy of the bent parts is guaranteed by the upper and lower molds and bending equipment.
The forming process is as follows: At a given sheet size, the upper mold applies a bending force, a reactionary force forms a bending moment at the support point of the lower mold, forcing the sheet to deform. The final bending angle of the sheet is determined by the depth at which the upper mold enters the opening of the lower mold.
The main working parts of a CNC press brake consist of a back gauge, an upper die and a lower die.
The back gauge is a workpiece that controls the location of the bend line, while the upper and lower dies are used to control the bending angle and inner radius of the workpiece. Whether the workpiece is qualified or not is mainly determined by these three parties.
Fundamental principles of bending with a press brake
1) The external angles must be folded before the internal angles.
2) Special shapes (referring to shapes other than 90°) must be bent before standard shapes.
3) The previous flexion step must not influence or interfere with subsequent steps.
4) Appropriate positioning references should be considered for future steps when bending in the initial stages.
Press brake warp speed
During bending, the ram of a press brake can move downward at different speeds depending on the work phase to bend correctly without injuring the operator.
There are four different phases:
PHASE 1 – FAST SPEED, up to the plate.
This is a fixed speed that cannot be controlled by the program. The upper chambers of the cylinders receive a high flow of oil at low pressure directly from the tank, so that the ram falls freely, taking advantage of its own weight.

After V-shaped bending, the inner surface of the bent part of the part undergoes compressive deformation, while the outer surface undergoes tensile deformation.
The greatest deformation occurs at the surface of the material and decreases as the plate thickness increases.
There is a neutral line, called the XX line, which is neither compressed nor stretched.
To determine the position of the neutral layer, consider the following:
If the IR (internal radius) of the part is 5 times greater than the plate thickness, the neutral layer is positioned in the center of the plate thickness.
If the RI of the part is 5 times less than the thickness of the plate, the position of the neutral layer shifts inward as the RI decreases, with the thickness of the bend position moving to t.
The relationship between the neutral layer radius (represented by P) and IR can be described as follows:
- R≥5t, P-IR=0.5t
- R<5t, P-IR=(0.25-0.4)t
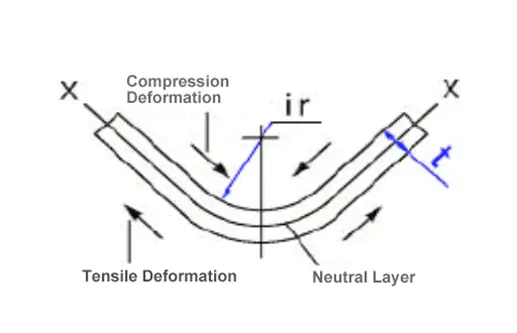
1) Return the press brake ram to the home position and reduce the pressure gauge value to the lowest value that only moves the ram.
2) Place two blocks of equal height on the table, preferably under the left and right cylinders.
3) Switch the hydraulic press brake to “motion adjustment” mode, remove the upper and lower dies and any other accessories, raise the mechanical block to its highest position and disconnect the coupling on the mechanical block drive shaft gear.
4) Carefully place the ram on the two blocks (the bottom face of the ram mold must touch the blocks).
Related Security Strategy
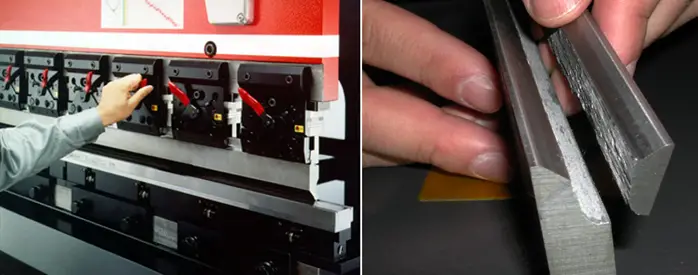
Incorrect installation of tools
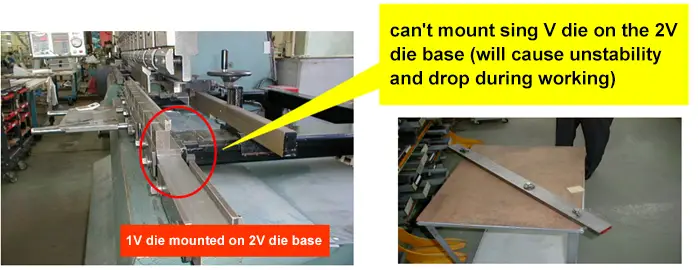