I. Principle of linear motors
Linear motors are devices that directly convert electrical energy into linear mechanical motion without any intermediate conversion mechanisms. They can be considered rotary engines that have been cut radially and unfolded in a flat plane.
Also known as linear motors or linear actuators, the most common types are flat, U-channel and tubular. The typical coil configuration is three-phase, with brushless phase switching achieved through Hall effect sensors.
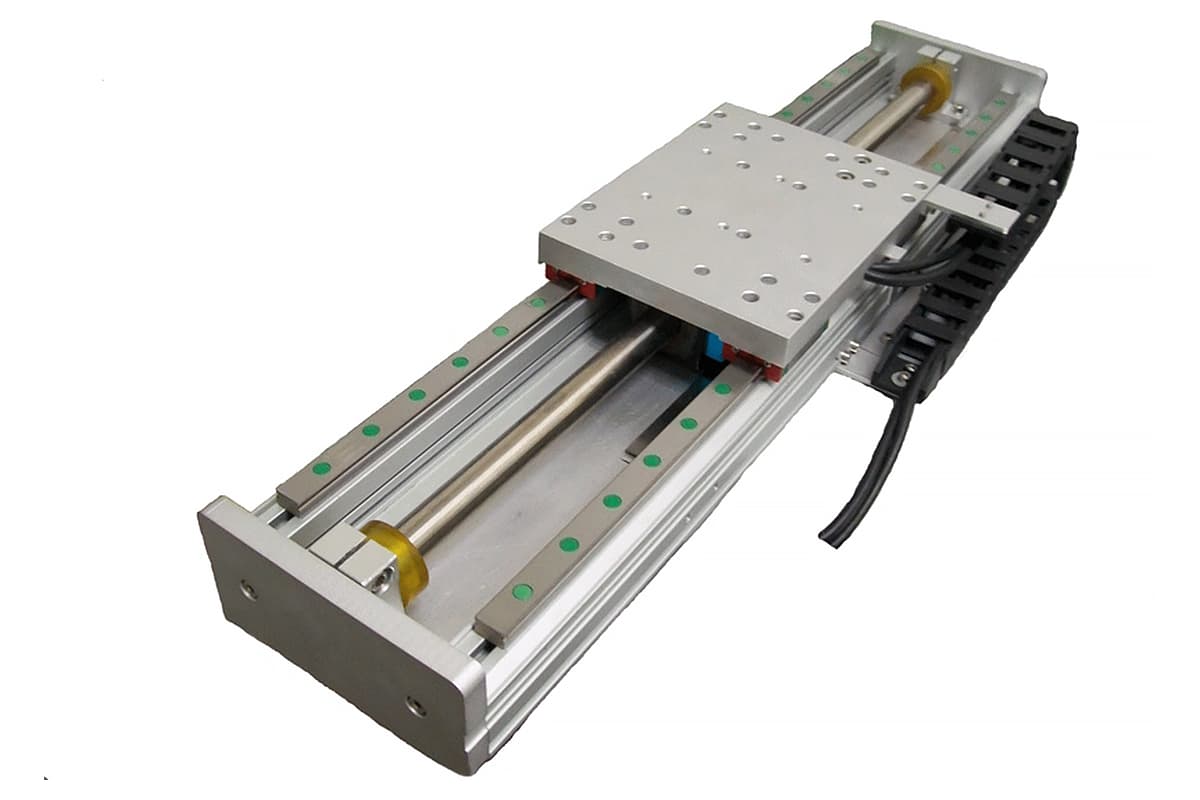
Linear motors are often described simply as rotary motors that have been unwound, operating on the same principle. The forcer (rotor) is made by compressing coils together with epoxy material; The magnetic track consists of magnets (usually high-energy rare earth magnets) fixed to steel.
The motor forcer includes coil windings, Hall effect sensor circuit boards, thermal regulators (temperature sensors that monitor temperature), and electronic interfaces. In rotary engines, the forcer and stator require rotating bearings to support the forcer and maintain the air gap of the moving parts. Similarly, linear motors need linear guides to maintain the position of the force in the magnetic field produced by the magnetic track.
Just like encoders mounted on the shafts of rotary servomotors to feedback position, linear motors need linear encoders to directly measure load position, thus improving load positioning accuracy.
The control of linear motors is similar to that of rotary motors. Just like brushless rotary motors, the forcer and stator are not mechanically connected (brushless).
Unlike rotary motors where the forcer rotates and the stator remains fixed, in linear motor systems both the magnetic track and the impulse coil can move (most positioning systems have a fixed magnetic track and an impulse coil mobile). In engines with moving impulse coils, the weight of the impulse coil and the load are very small.
However, this requires highly flexible cables and their management systems. In motors with moving magnetic tracks, not only the load but also the weight of the magnetic track must be supported, eliminating the need for a cable management system.
Similar electromechanical principles are used in linear and rotary motors. The same electromagnetic forces that produce torque in rotary motors generate linear thrust in linear motors.
Therefore, linear motors utilize the same control and programmable settings as rotary motors. The shape of linear motors can be flat, U-channel or tubular, depending on the specific requirements and working environment of the application.
The operating principles of linear motors can be categorized into two main types: one where the motor (moving part) travels within a magnetic field, known as a maglev linear motor, and another where the motor remains stationary within the magnetic field and is driven by the electromagnetic force, known as electromagnetic impulse linear motor.
(1) Maglev Linear Motor
The principle behind the maglev linear motor involves the use of magnetic fields to suspend the motor in the air, thus achieving contactless and frictionless movement. This type of linear motor mainly includes permanent magnet synchronous linear motors (PMSLMs) and electromagnetic suspension linear motors (EMSLMs).
PMSLMs exploit the interaction between the magnetic field produced by permanent magnets and the stator magnetic field to suspend the motor. The main advantages of PMSLMs are their simple structure, low cost and stable operation.
However, the magnetic field strength is limited due to the presence of permanent magnets, resulting in relatively lower thrust and speed.
EMSLMs use magnetic levitation force generated by electromagnetic fields to suspend the engine. Its main advantage is the greater intensity of the magnetic field, leading to relatively greater thrust and speed. However, EMSLMs have a more complex structure and higher costs.
(2) Electromagnetic Impulse Linear Motor
The electromagnetic impulse linear motor operates by using electromagnetic force to move the motor within a magnetic field. This category mainly includes alternating current linear motors (ACLMs) and direct current linear motors (DCLMs).
ACLMs are powered by the electromagnetic force generated by alternating current to move the motor. The main advantages of ACLMs are simplicity, low cost and stable operation. However, the characteristics of alternating current limit its momentum and speed.
DCLMs use the electromagnetic force generated by direct current to move the motor. The main advantage of DCLMs is their greater thrust and speed, but they have a more complex structure and are more expensive to implement.
II. Characteristics of linear motors
Before practical and affordable linear motors were available, all linear motion had to be converted from rotating machines using ball screws, roller screws, belts or pulleys. For many applications, especially those involving heavy loads and vertical drive shafts, these methods are still best.
However, linear motors have many unique advantages over mechanical systems, such as very high and very low speeds, high acceleration, virtually zero maintenance (no contacting parts), high precision, and no backlash.
Completing linear motion with just a motor, without gears, couplings or pulleys, makes sense for many applications, eliminating unnecessary parts that reduce performance and shorten mechanical life.
1) Simple structure.
Tubular linear motors directly produce linear motion without intermediate conversion mechanisms, greatly simplifying the structure, reducing motion inertia, and significantly improving the dynamic response and positioning accuracy. This also increases reliability, saves costs and simplifies manufacturing and maintenance. Your primary and secondary can directly become part of the engine, a unique combination that further showcases these advantages.
2) Suitable for high-speed linear motion.
Because there are no restrictions on centrifugal force, common materials can reach higher speeds. Furthermore, if air or magnetic cushions are used to maintain the distance between the primary and secondary, there is no mechanical contact during movement and therefore no friction or noise. This means that transmission parts do not show wear, greatly reducing mechanical losses and preventing noise from cables, wire ropes, gears and pulleys, thus increasing overall efficiency.
3) High utilization of primary windings.
In tubular linear induction motors, the primary windings are pancake shaped, with no end windings, resulting in high winding utilization.
4) No transverse edge effects.
Transverse effects refer to the weakening of the magnetic field at boundaries due to transverse breaks. Cylindrical linear motors do not have transverse breaks, so the magnetic field is uniformly distributed circumferentially.
5) Easily overcome one-sided magnetic attraction.
The radial traction forces cancel each other out, practically eliminating the problem of unilateral magnetic traction.
6) Easy to adjust and control.
By adjusting the voltage or frequency, or changing the secondary material, different speeds and electromagnetic pulses can be achieved, suitable for alternative low-speed operations.
7) Strong adaptability.
The primary core of the linear motor can be encapsulated with epoxy resin, providing good corrosion and moisture resistance, making it suitable for use in humid, dusty and harmful gas environments. Furthermore, it can be designed in different structures to meet different needs.
8) High acceleration.
This is a significant advantage of linear motor drives compared to other screw, synchronous belt and rack drives.
III. Linear Motor Applications
Linear motors, known for their efficiency, precision and high speed, are widely used in various fields.
- Transport
In the transport sector, linear motors are mainly used in high-speed trains, subways and elevators. For example, German maglev trains utilize magnetic levitation linear motors, resulting in higher speeds and reduced noise levels.
Furthermore, linear motors can be integrated into the drive systems of electric vehicles to improve their performance.
- Industrial manufacturing
In industrial manufacturing, linear motors are primarily used in CNC machine tools and robots. For example, tool feed systems on CNC machine tools are driven by linear motors, offering greater machining precision and fast response times.
Furthermore, linear motors can be applied to conveyor belts and handling robots in automated production lines, thus increasing productivity.
- Medical field
In the medical field, linear motors are mainly applied in medical imaging devices, such as CT scanners and MRI machines. These devices require precise control of the scanning range and speed of x-rays or magnetic fields, and linear motors provide high accuracy and speed control, increasing diagnostic accuracy and efficiency.
- Scientific research
In scientific research, linear motors are prominently used in particle accelerators and astronomical telescopes. For example, the accelerator rings of the Large Hadron Collider (LHC) employ linear motors, which allow for greater acceleration capabilities and more stable operational performance.
Furthermore, linear motors can be used in the automatic focusing systems of astronomical telescopes, improving the precision and efficiency of observations.