The level of mold technology and maintenance are crucial factors in improving processing quality, extending mold life and controlling equipment operating costs.
This post focuses on the common problems encountered when using NC turret punching dies and provides corresponding technical points and precautions for die maintenance.
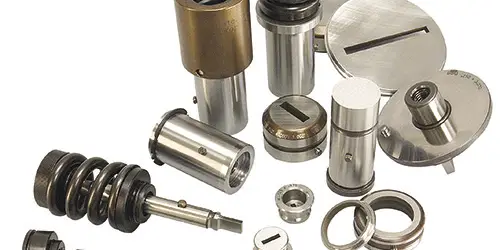
Common Usage Problems
Mold with matter
Mold with matter will cause waste recovery, and the influencing factors are:
(1) The sharpness of the die edge is crucial. The larger the edge fillet, the easier it is to cause waste rebound.
(2) A small mold entry module is more likely to cause waste rebound.
(3) Check whether the mold gap is reasonable.
(4) Make sure there is not too much oil on the surface of the processed board.
(5) Consider the fatigue damage of the die spring.
(6) Ensure adequate lubrication to prevent debris rebound.
Mold alignment
During use of a die, the amount of wear on each side of the punch core may vary. Certain areas may have large scratches and wear more quickly, while other parts may wear more slowly. This is particularly noticeable on thin and narrow rectangular matrices.
The main reasons for this problem are as follows:
(1) The turret design or machining accuracy of the machine tool cannot meet the requirements, especially the alignment of the die mounting base of the upper and lower rotary tables is not good.
(2) The design or machining accuracy of the mold cannot meet the requirements.
(3) The accuracy of the punch guide sleeve does not meet the required standards.
(4) The die gap is too large or too small.
(5) Due to prolonged wear and tear, the mold mounting base or mold guide sleeve may not be well aligned.
Spring fatigue damage
CNC turret punch die spring is often forgotten during use and maintenance.
Different punching equipment and dies require specific spring specifications. Springs have different performance and lifespan, so they need to be maintained or replaced regularly.
Ignoring this maintenance can cause material to become stuck in the mold or cause significant damage, such as to the mold and guide sleeve.
Technical points of correct use of the NC punching die
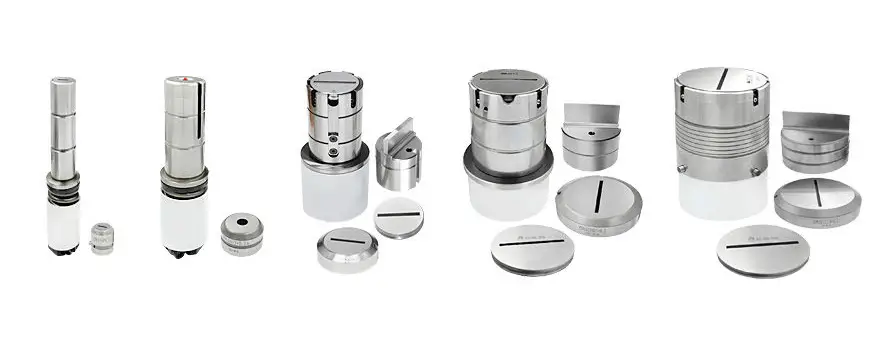
Optimal die clearance
Die clearance refers to the sum of clearance on both sides when the punch enters the lower die.
The choice of die gap depends on the plate thickness, material and stamping process. A corresponding die gap must be selected for each different plate thickness or material.
If the gap is too small or too large, it may damage the die and affect the punching quality.
Proper selection of die gap can ensure good punching quality, reduce burr and collapse, keep the sheet flat, effectively prevent material carryover, and extend the service life of the die.
Die clearance is mainly determined by checking stamping residue.
If the residue has a rough, wavy fracture surface and a small, shiny surface, it indicates that the gap is too large.
The angle between the fracture surface and the shiny surface is directly proportional to the gap.
The larger the gap, the more bending and fracture will occur during punching, and even a thin edge protrusion may appear.
Methods for eliminating and reducing adhesion
During the stamping process, the pressure and heat generated can cause fine sheet particles to adhere to the surface of the punch, which can affect the quality of the punch.
To prevent overheating and reduce friction, lubrication is commonly used.
If lubrication is not possible or residue rebound occurs, the stamping method with punches of the same size can be adopted alternatively. This allows each punch sufficient cooling time before use.
To remove any material stuck to the punch, a fine oil stone can be used for sanding. It is important to maintain a grinding direction consistent with the punch movement. Avoid using coarse abrasive cloth as it can roughen the surface of the punch and cause it to stick again.
Measures to avoid deformation of the sheet when drilling many holes
When a board is drilled with multiple holes, it may cause deformation of the board. This is caused by the build-up of shear stress during each punching action, resulting in the material around the hole deforming downwards. This creates tensile stress on the top surface and compressive stress on the bottom surface.
Drilling a few holes does not significantly affect the quality of the board. However, when numerous holes are drilled, the tensile and compressive stresses on the upper and lower surfaces accumulate at a certain point, leading to unevenness and deformation of the material.
To avoid this deformation, the hole punching sequence needs to be changed. Drilling alternate holes and then returning to drill the remaining holes can effectively reduce stress build-up during sequential stamping in the same direction.
Although this punching method also produces tension, it compensates for the tension of the front and rear hole groups, preventing deformation of the sheet metal.
Avoid drilling very narrow strips
When using a die to cut a board with a width less than its thickness, the punch will bend and deform due to lateral force. On the other hand, wear will worsen due to the small gap. In severe cases, the lower die will be scratched or both the upper and lower dies will be damaged.
Furthermore, when cutting a very narrow strip, the sheet will not be completely cut, but will tend to bend in the opening of the lower die or even get caught on the side of the die.
To avoid this type of die wear, it is advisable to avoid narrow strips with very small step widths, especially those that are less than 2.5 times the sheet thickness.
If narrow blanking cannot be avoided, the use of a return plate or a fully guided die is recommended.
Molds of different materials should be selected for plates of different materials
Surface hardening of a punch typically involves techniques such as titanium plating and nitriding. The resulting hardening layer is not only a surface coating, but also a part of the punch matrix with a molecular structure ranging in thickness from 12 to 60 μm.
By subjecting the punch to surface hardening, die wear can be reduced when working with special materials such as stainless steel plates. However, it should be noted that surface hardening of the matrix does not extend its service life. Maintenance methods for surface-hardened punches remain conventional, such as adequate lubrication, timely grinding, and operation in accordance with regulations.
Despite being hardened, the punch can still be sharpened using the usual techniques.
Hardened punches can be used in the following cases:
- Drilling soft or viscous materials (such as aluminum);
- Diluted abrasive materials (such as epoxy glass sheets);
- Diluted hard materials (such as stainless steel);
- Frequent impact;
- Abnormal lubrication.
Maintenance knowledge
Maintenance in use
(1) Molds must be regularly cleaned and lubricated and inspected for dirt before installation and use. Lubricating oil or stamping oil should be applied to the sliding parts and cutting edges of the die at regular intervals during production. After production, the mold must be carefully inspected and cleaned. After cleaning, apply anti-rust lubricating oil, seal the mold and store it to keep it clean for future use.
(2) When installing male and female dies on the rotary table, they must be installed strictly in accordance with the installation process to ensure that the installation direction of the male and female dies is consistent. Arrays with specific installation direction requirements must be installed carefully to avoid accidents due to installation errors.
(3) Soft metals such as aluminum or copper should be used as the operating tool when installing the mold. Using an operating tool with excessive hardness may cause damage to the mold during the installation process, resulting from bumping, crushing or other actions.
During transport, the mold must be handled carefully to avoid damage to the cutting edge and guide. When replacing the mold and grinding, safety must be a priority before and after turning on the equipment to prevent damage to the equipment, mold and personnel.
Maintenance after use
(1) Immediate grinding :
The amount of edge grinding in a punch die is limited, and when the edge is worn, it must be ground immediately. Continuing to use a worn edge will accelerate wear, reduce punch quality, and shorten die life.
Practice has proven that it is crucial to determine the appropriate grinding time and not wait until it is necessary to grind. Regular micro-grinding can reduce cutting force, ensure good part quality and double the die life. Furthermore, mastering the correct grinding method can also help improve the life of the die.
To prevent the mold from cracking or annealing due to overheating, it is essential to add the high-quality coolant required by the manufacturer during grinding.
After grinding, it is necessary to remove the edge burrs with an oil stone and grind the edge into a flat fillet with a radius of 0.03 ~ 0.05mm to avoid cracking. In addition, the surface of the cutting edge cannot be magnetic and demagnetization must be carried out to prevent material blocking. Finally, demagnetize the punch and spray it with lubricating oil to prevent rust.
(2) Replace the spring immediately:
During the mold maintenance process, it is common for the spring and other elastic components to be neglected, although springs are prone to damage such as fractures and deformation.
It is crucial to promptly replace any damaged springs with ones that match the same specifications and model. Failure to do so may cause problems with mold functionality or even damage the mold due to incompatible parts.
(3) Check whether fasteners are loose or parts are damaged at any time.
Regularly check the condition of the mold installation base accessories and other parts to avoid damage. Any play or displacement must be promptly detected and corrected to avoid accidents that could damage the mold or cause other problems.