Concept
Photosensitive resins refer to resins that undergo chemical polymerization or cross-linking after exposure to specific light radiation, facilitated by photoinitiators, causing curing of the monomers or oligomeric base. Typically, among various types of light radiation, ultraviolet (UV) radiation has an activation energy closest to that required for chemical polymerization reactions.
Hence, photosensitive resins are commonly cured using UV light and are often called UV sensitive resins, UV curable resins, shadowless UV adhesives, photoresists, etc. Each photosensitive resin product has different components and responds to specific wavelengths, typically between 250-400 nm.
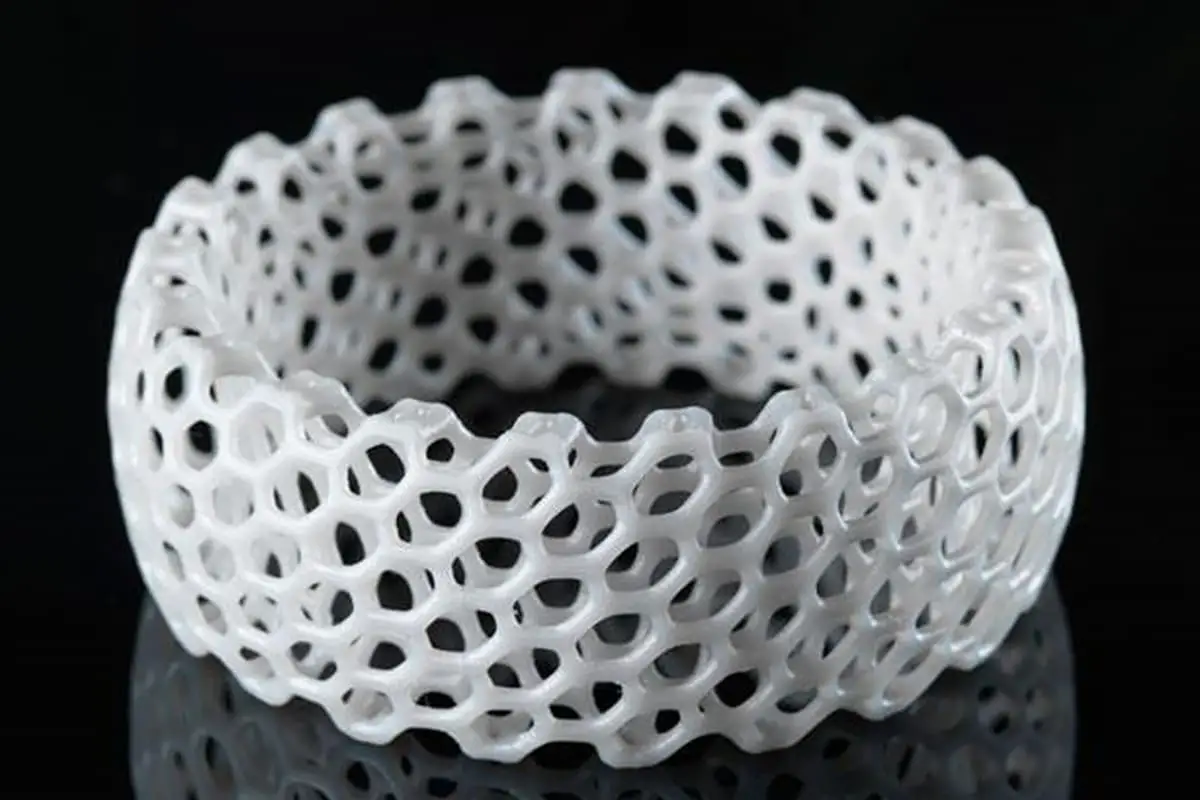
It is important to note that UV light can be dangerous, damaging tissues and cells, and the ozone produced when it reacts with air can also affect the operating environment. Consequently, researchers are exploring photosensitive resins that cure under visible light or blue light, leading to the publication of invention patents for blue light-sensitive resins.
Composition
Photosensitive resins are mainly composed of a photosensitive prepolymer, a photoinitiator (or photosensitizer) and a diluent.
(1) Photosensitive prepolymer
Photosensitive prepolymer, also known as oligomer, is a low molecular weight prepolymer capable of photocuring, with a molecular weight typically between 1,000-5,000. It serves as the base material for photosensitive resin materials and is the decisive factor in their final performance.
The main types of photosensitive prepolymers include acrylate-modified epoxy resins, unsaturated polyesters, polyurethanes, and thiol-ene light-cured resin systems.
(2) Photoinitiators and photosensitizers
Photoinitiators and photosensitizers promote the initiation of polymerization during the curing process, but they differ significantly. Photoinitiators participate in the reaction by creating active species, such as free radicals or cations, by absorbing light energy, and are consumed in the process. Photosensitizers act more like catalysts, transferring energy without being consumed.
Photoinitiators can be classified into three categories based on their initiation mechanism: free radical type, cationic type and hybrid type (incorporating both mechanisms). A typical free radical photoinitiator is 2-hydroxy-2-methyl-1-phenyl-1-propanone (CAS-1173), and common cationic photoinitiators include ferrocenium and iodinium salts.
The mechanism of photosensitizers involves energy transfer, hydrogen abstraction and charge transfer complex formation. The main photosensitizers include benzoin, Michler ketone, thioxanthone and benzophenone derivatives.
(3) Reactive diluents
Reactive diluents mainly refer to low molecular weight epoxy compounds containing epoxy groups that can participate in the curing reaction of epoxy resins, becoming part of the cross-linked network structure of the cured epoxy.
Based on the number of reactive functional groups per molecule, reactive diluents can be categorized into monofunctional, difunctional, and polyfunctional diluents.
Examples include monofunctional diluents such as styrene (St), N-vinyl pyrrolidone (NVP), vinyl acetate (VA), butyl acrylate (BA), 2-ethylhexyl acrylate (EHA), and hydroxyethyl (meth)acrylate ( HEA, HEMA, HPA); difunctional diluents such as 1,6-hexanediol diacrylate (HDDA), tripropylene glycol diacrylate (TPGDA) and neopentyl glycol diacrylate (NPGDA); and the polyfunctional diluent trimethylolpropane triacrylate (TMPTA), among others.
Generally, the greater the number of functional groups in a diluent, the faster the photopolymerization rate, the greater the degree of cross-linking, the better the hardness and wear resistance, but the greater the shrinkage rate. The types of functional groups mainly include acryloyloxy, methacryloyloxy, vinyl and allyl, with the reactivity upon photopolymerization decreasing in the order of: acryloyloxy > methacryloyloxy > vinyl > allyl.
Photopolymerization Principles
The activation energy produced by irradiation can cause the breaking of C = C bonds in photosensitive prepolymers (monomers or oligomers), forming functional groups. Simultaneously, it can induce the radicals in the photoinitiators to undergo chemical polymerization or cross-linking reactions with the aforementioned functional groups.
As a result, the small molecular chains of the resin matrix are intertwined into larger molecular chains or even into three-dimensional network molecular chains, as illustrated in Figure 4-63. The resin thus transitions from a liquid to a solid state. It should be noted that oxygen generally hinders the aforementioned polymerization or cross-linking reactions in most photosensitive resin matrices.
The CLIP process effectively exploits this characteristic to prevent the resin from curing against the vat.
Types of photosensitive resins
Photosensitive resins can be classified into different types based on various categorization methods.
(1) Classification by type of solvent
Based on the solvent used, photosensitive resins can be divided into solvent-based and water-based categories. Solvent-based photosensitive resins are hydrophobic and can only be dissolved in organic solvents, not water.
Common solvent-based photosensitive resins include UV polyether acrylates. Water-based photosensitive resins are hydrophilic, capable of being decomposed or dispersed in water. These resins contain a number of hydrophilic groups and unsaturated groups, which make water-based photosensitive resins hydrophilic, such as water-based polyurethane acrylates.
(2) Classification by Properties
Transparent Photopolymer Resin: This resin is naturally transparent and can be polished to a semi-transparent or completely transparent finish. It is mainly used for visual and structural verification of various products, allowing for highly detailed and cost-effective surface finishes.
Solid Color Photopolymer Resin: The natural color of the resin is solid and its surface can be polished, painted or electroplated. It is mainly used for structural verification of products, enabling extremely fine and cost-effective surface finishes.
High temperature photopolymer resin: The natural color of the resin is solid and is mainly used for products that require a certain level of high temperature resistance. It can withstand temperatures of up to 100-110°C, slightly higher than standard photopolymers.
High Tenacity Photopolymer Resin: Typically yellowish-green in color, this resin has a slightly higher tenacity than standard photopolymers, allowing for slight flexing.
In the domain of desktop 3D printers, fused deposition modeling (FDM) printers currently dominate in terms of price and versatility, gaining widespread popularity both nationally and internationally.
However, when greater precision and better surface detail are required, low-cost stereolithography (SLA) and digital light processing (DLP) 3D printers have a clear advantage. The increasing availability of affordable SLA and DLP 3D printers has spurred the evolution of photopolymer materials technology.
(3) Common photopolymer resins for stereolithography 3D printing
General-purpose resin: Initially, 3D printing resin manufacturers sold their proprietary materials, but as market demand grew, several resin manufacturers emerged, including MadeSolid, MakerJuice, and Spot-A. Initially, desktop resins were limited in color and performance, with materials typically only available in yellow and clear.
Recent developments have expanded color options to include orange, green, red, yellow, blue, white and more.
Rigid Resin: Photopolymer resins used in desktop 3D printers tend to be brittle, prone to breaking and cracking. To solve these problems, many companies began to produce more robust and durable resins.
For example, Formlabs introduced a new Tough Resin material that strikes a balance between strength and elongation, giving 3D printed prototypes better strength and impact resistance. This is particularly useful for prototyping precision components or quick-fit connectors.
Moldable resin for precision casting: Traditional precision casting processes can be complex and time-consuming, and mold constraints often limit design freedom. This is especially true when compared to 3D printed wax patterns, which do not require making molds for the wax models.
Moldable resins have low expansion and require complete burning of the polymer during the casting process to leave an impeccably shaped final product, as any plastic residue can cause defects and deformations in the casting. Equipment manufacturers like SprintRay and specialty materials producers like Fun ToDo offer these resins.
Domestic company Su-Cheng Technology also launched CA resin for precision casting. Figure 4-64 shows some investment casting models made with this type of resin.
Flexible resin: Manufacturers of flexible resins include Formlabs, FSL3D, Spot-A, Carbon and Su-Cheng Technology. These resins have medium hardness and are wear-resistant and can be stretched repeatedly. This material is used in parts such as hinges, friction devices, and components that require repeated stretching. Figure 4-65 shows models made of flexible resin.
Elastic Resin
Elastic resin is a material that exhibits excellent elasticity under high-strength extrusion and repeated stress. Formlabs flexible resin is a very soft rubber-like material that becomes very flexible when printed with thinner layers and highly elastic and impact resistant with thicker layers. Its potential applications are limitless.
This new material is poised to revolutionize the manufacturing of hinges, bumpers, seamless contact surfaces, etc., catering to those with imaginative ideas and designs. Figure 4-66 shows a model made of elastic resin.
High Temperature Resin
High temperature resin is undoubtedly a focal point of research and development among many resin manufacturers. This is because the problem of aging of these plastics has been a challenge in the progress of the resin from consumer to industrial applications. Cyanate ester resin has a thermal deflection temperature of up to 219°C, maintaining good strength, stiffness and long-term thermal stability at high temperatures.
It is ideal for molds and mechanical parts in the automotive and aerospace industries. The current challenge for high-temperature resin materials is to achieve a thermal deflection temperature (HDT) of up to 289°C (552°F). Formlabs also showcased its latest high-temperature material.
Biocompatible Resin
Formlabs Dental SG material for desktop 3D printers complies with EN-ISO10993-1:2009/AC:2010 and USP Class VI standards, ensuring safety and environmental friendliness for human tissues. Due to the translucency of the resin, it can be used in surgical materials and as guides for surgical drills. Although designed for the dental industry, this resin is also applicable in other areas, particularly the medical sector.
Ceramic Resin
Ceramics created by photopolymerization of pre-ceramic monomers using UV light exhibit uniform shrinkage and virtually no porosity. After 3D printing, this resin can be sintered to produce dense ceramic parts. The ultra-high-strength ceramic material produced with this technology can withstand temperatures exceeding 1700°C.
The predominant ceramic photopolymerization techniques on the market involve the uniform dispersion of ceramic powder in a light-cured solution through high-speed stirring, creating a ceramic paste with a high solids content and low viscosity.
This paste is then directly solidified layer by layer in a photopolymerization molding machine to accumulate the green ceramic body, which is subsequently dried, bonded and sintered to obtain the final ceramic parts.
Day resin
Daylight resin is a fascinating type of resin that, unlike those cured under ultraviolet light, can solidify under normal daylight. This eliminates dependence on UV light sources, allowing the use of a liquid crystal display for curing. This resin promises to significantly reduce the cost of 3D printing through photopolymerization and has a very promising outlook.