Aerospace Materials Service Environment
Aerospace materials must not only be able to withstand high stresses and inertial forces, but also withstand impacts and alternating loads caused by factors such as takeoff and landing, engine vibration, rapid rotation of parts, sudden wind and flight maneuvers.
Aircraft exposure to engine gases and solar radiation creates a high temperature environment, with increased flight speed leading to significant aerodynamic heating.
These materials are also subject to varying temperatures, including drops to around -50°C when flying at subsonic speed in the stratosphere, and even lower temperatures in polar regions during winter.
Metallic components and rubber tires are susceptible to embrittlement, while fuels and lubricants can have corrosive effects on metallic materials and swelling effects on non-metallic materials.
Furthermore, exposure to solar radiation, wind and rain erosion, and long-term storage in humid environments can accelerate the aging process of polymeric materials.
Selection and application of aerospace materials
Aerospace vehicles have been operating in the atmosphere or outer space for a long period. To ensure their high reliability, safety and optimal flight performance, they must be designed to operate effectively in challenging environments.
To achieve these objectives, it is essential to optimize the structure to meet aerodynamic, technological and maintenance requirements. However, it also requires the use of materials that have excellent characteristics and functions.
1. Material selection principle
In service, structural components must be capable of withstanding various types of external forces without exceeding the acceptable level of deformation or rupture within a specified period of time.
One of the design objectives in aerospace structures is to minimize their size and weight. In the past, the main focus was on the static strength of components, often neglecting or giving limited attention to their plastic strength. This resulted in catastrophic accidents.
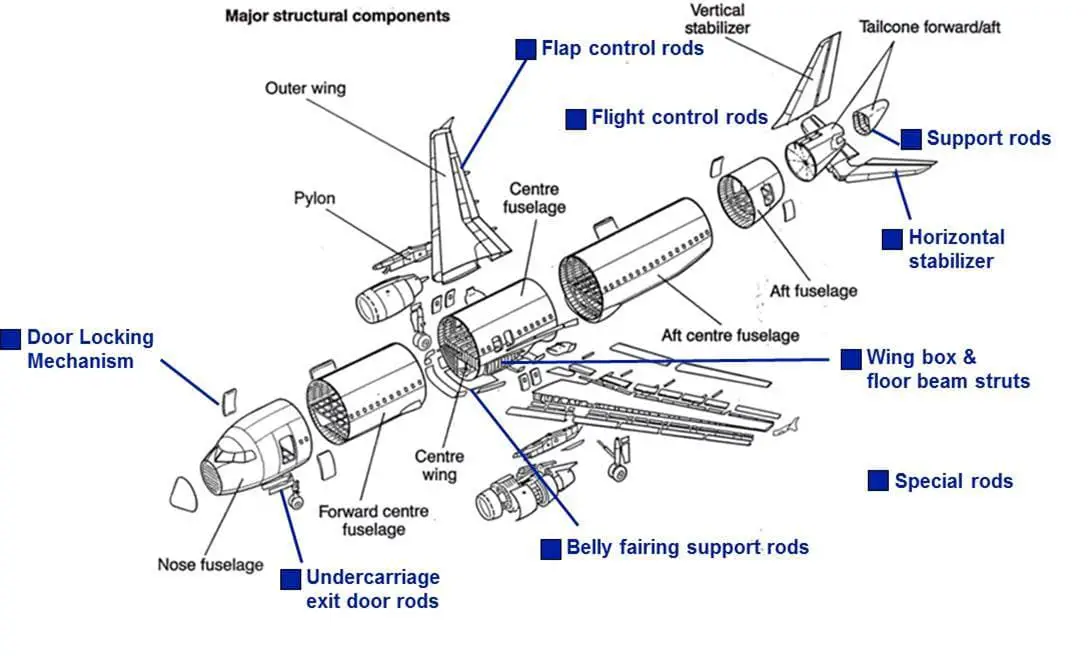
Main structural components of mainline aircraft
To ensure the safety of structural components and make full use of material performance, the design of aerospace structural parts has changed from a “strength design principle” to a “damage tolerance design principle” and evolved into a “ full life cycle project.” .
In the design phase, all aspects of a product's life cycle are taken into account and all relevant factors are comprehensively considered and optimized in the product design phase.
Materials must not only have high specific strength and stiffness, but also have certain fracture resistance and impact resistance, fatigue resistance, high and low temperature resistance, corrosion resistance, aging resistance and mold resistance, as well as indicators of improved performance.
Different material selection criteria are applied to different load areas, with materials chosen based on the specific requirements of each component. For high load areas, resistance criteria are used and high resistance materials are selected. For medium load areas, stiffness criteria are used and materials with high elastic moduli are chosen. In low load areas, dimensional stability is the primary consideration to ensure components are larger than the minimum critical size.
When selecting and evaluating structural materials, appropriate test methods for mechanical properties (tensile, compression, impact, fatigue, low-temperature impact) should be selected based on service conditions and stress states. A comprehensive consideration of material strength, plasticity and toughness should be made for different fracture modes, including ductile fracture, brittle fracture, tension fatigue, creep fatigue, stress corrosion cracking, hydrogen embrittlement, neutron irradiation embrittlement, etc. .
For members in tension, the stress distribution must be uniform at both the surface and the core, and the selected material must have uniform structure and performance, with good hardenability for large members.
For members subject to bending and torsional loads, there is a large difference in tension between the surface and the core, and materials with low hardenability can be used.
Fatigue limit and notch sensitivity are important evaluation criteria for material selection for components under alternating loads.
For components exposed to corrosive environments, factors such as corrosion resistance, sensitivity to hydrogen embrittlement, tendency to stress corrosion and resistance to corrosion fatigue are important evaluation indicators for material selection.
Structure stability must be considered for materials used in high-temperature service, and low-temperature performance must be taken into consideration for low-temperature service.
Weight reduction has practical significance for improving aircraft safety, increasing payload and endurance, improving maneuverability and range, and reducing fuel or propellant consumption and flight costs. The faster the aircraft speed, the more significant the weight reduction becomes. For example, reducing the weight of a fighter by 15% could result in a 15% reduction in taxi distance, a 20% increase in range and a 30% increase in payload.
For short-term expendable aircraft such as missiles or launch vehicles, it is necessary to achieve equivalent functions with minimum volume and mass, seeking to maximize material performance and selecting the smallest possible safety margin to ensure absolute reliability throughout its service life. .
2. Main aerospace materials
Reducing structural mass can be achieved by reducing density by 30%, which is more than strength by 50%.
Aluminum alloys, titanium alloys and composite materials are the main materials used in aerospace structures due to their high specific strength and rigidity, which can improve the payload, maneuverability and endurance of aircraft while reducing costs of flight.
The use of ultra-high-strength steel (with a yield strength greater than 1380 MPa) in aerospace engineering is limited to less than 10%.
For modern aircraft such as supersonic fighter jets, the amount of ultra-high-strength steel is stable at 5% ~ 10%, the tensile strength is 600 ~ 1850MPa, sometimes as high as 1950mpa, and the fracture strength K EU c = 78 ~ 91MPa·m 1/2 .
High-strength corrosion-resistant steel is typically used for the fuselage load-bearing structure in actively corroding environments, while carbon-free corrosion-resistant steel is used for components in aircraft equipped with hydrogen fuel engines using liquid hydrogen and half hydrogen.
The main structural materials used in aircraft fuselages in the 21st century are aluminum alloys, including 2XXX series, 7XXXX series, and aluminum-lithium alloys. Adding lithium to aluminum alloys can improve their strength and reduce their density, thus increasing their specific strength and stiffness.
Aluminum-lithium alloys have been used in large transport aircraft, fighter planes, strategic missiles, space shuttles, and launch vehicles, and are used in components such as projectiles, load-bearing components, liquid hydrogen and oxygen storage tanks. liquid, piping and payload adapters. They are considered a promising material for aerospace development.
Third- and fourth-generation aluminum-lithium alloys no longer prioritize low density and have better overall properties. Compared with third-generation aluminum-lithium alloys, fourth-generation alloys have higher static strength (especially yield strength) and fracture toughness, while maintaining crack growth rate, fatigue performance, corrosion performance, and modulus of equivalent elasticity.
Titanium alloys have a higher specific strength than aluminum alloys and are used in aircraft components such as airframe, guide rail and flap support, engine base, landing structure parts, and heating parts such as exhaust hood and fire shield. For supersonic aircraft with Mach numbers greater than 2.5, the surface temperature can reach 200 to 350°C, and titanium alloys can be used as coating.
High-purity, high-density titanium alloys prepared by rapid solidification/powder metallurgy methods have good thermal stability and maintain their strength at 700°C, similar to their strength at room temperature. The developed high-strength and high-toughness β-type titanium alloys were selected by NASA as the matrix material for SiC/Ti composite materials used in aircraft fuselage and wing panels.
The proportion of titanium alloys used in aircraft is gradually increasing, with 20% used in civil aviation fuselages and 50% in military aircraft fuselages.
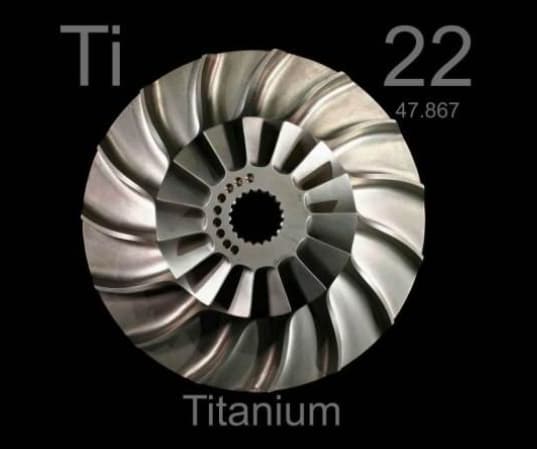
Metal matrix composites, high temperature resin matrix composites, ceramic matrix composites and carbon/carbon composites are playing an increasingly important role in the aerospace industry.
Carbon/carbon composite materials combine the refractory properties of carbon with the high strength and stiffness of carbon fibers. They have excellent thermal stability and conductivity, as well as high strength and toughness at 2500°C with a density that is only a quarter of that of high-temperature alloys.
Hybrid composites have gained significant attention, such as adding glass fiber to carbon fiber composites to improve impact performance or adding carbon fiber to glass fiber reinforced plastics to increase stiffness.
Layered composite materials are also becoming more widely used in aerospace engineering, such as the use of 3% GLARE, a new laminate, in the A380. Laminate is a composite material made by stacking two different materials together under pressure.
A laminate typically consists of a top panel, a top bond layer, a core material, a bottom bond layer, and a bottom panel. Its strength and rigidity are higher than that of the individual panel or core material. It has been used in transport and fighter aircraft.
GLARE laminate is formed by hot pressing multiple thin sheets of aluminum and unidirectional fiberglass pre-impregnated with epoxy adhesive under pressure or in a hot pressing tank, as shown in Figure 1. The aluminum sheets must be properly pre-treated to facilitate adhesion to the pre-impregnated fiber layer.
Table 1 shows the types of commercially produced GLARE laminates, which can be formed into sheets of different thicknesses as needed. Fibers can have 2, 3, 4 layers or more, and their content and direction can meet the requirements of the table. Each type of GLARE laminate can have different formats and be adjusted to meet specific needs.
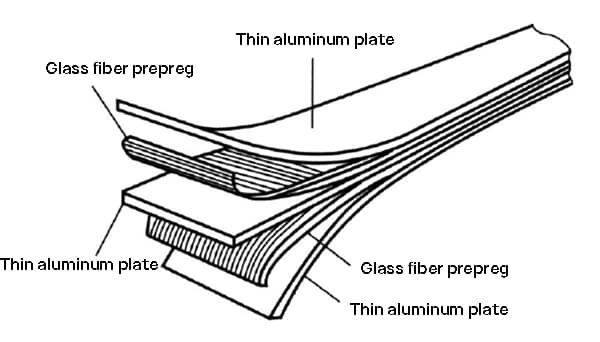
Fig. 1 Schematic diagram of the glossy laminate
Table 1 types of commercially available blinding laminates
Laminate |
aluminum layer |
Fibrous layer |
Typical density / (g/ cm3 ) |
||
aluminum product |
Single layer thickness/mm |
guidance |
Single layer thickness/mm |
||
BRIGHT1 GLARE2 BRIGHT3 GLARE4 BRIGHT5 BRILLIANT6 |
7475-T76 2024-Q3 2024-Q3 2024-Q3 2024-Q3 2024-Q3 |
0.3~0.4 0.2~0.5 0.2~0.5 0.2~0.5 0.2~0.5 0.2~0.5 |
Unidirectional Unidirectional 0°/ 90° orthogonal 0°/ 90°/0° orthogonal 0°/ 90°/90°/0° orthogonal +45° / – 45° orthogonal |
0.25 0.25 0.25 0.375 0.5 0.25 |
2.52 2.52 2.52 2.45 2.38 2.52 |
The splicing technology of GLARE laminates solves the problem of limited board width. As shown in Figure 2, there is a narrow seam between the same layer of aluminum plates, with joints between different layers located at different positions. These joints can be connected to other layers of aluminum plates through fiber layers, allowing the manufacture of wall plates or the entire fuselage skin with excellent resistance to fatigue, corrosion and fire, eliminating the need for holes for rivets and the resulting stress concentrations. .
To ensure safe load transfer, a reinforcing layer can be added to the splice, such as a layer of metal plate or a layer of fiberglass pre-impregnated with resin.
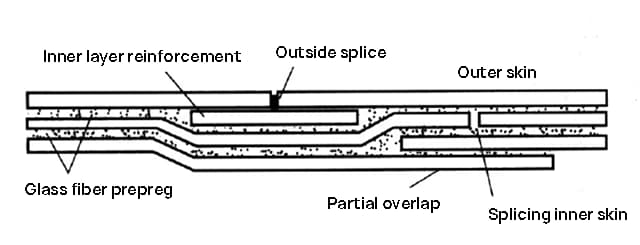
Fig. 2 Glossy laminate splicing diagram
Honeycomb sandwich composite materials are composed of a sandwich core and a skin (panel). The skin may be made of aluminum or carbon/epoxy composite materials, while the sandwich core resembles a honeycomb and is composed of a series of hexagonal, quadrilateral, or other shaped cells made of metal, fiberglass, or other materials. composites. The top and bottom surfaces of the sandwich are glued or welded to the thinner panels.
The core material of aluminum honeycomb sandwich composites is made by gluing aluminum sheets in different ways and forming honeycombs of various specifications through stretching. The performance of the core material is mainly determined by the thickness of the aluminum foil and the size of the cells.
These materials have high specific strength and stiffness, good impact resistance, vibration reduction, microwave transmission and strong designability. Compared with riveted structures, structural efficiency can be increased by 15% to 30%.
Honeycomb sandwich structures can be used for various wall panels, such as wing surfaces, cabin surfaces, cabin covers, floors, engine covers, muffler plates, thermal insulation plates, satellite star shells, antennas paraboloids, bottoms of rocket propellant storage tanks, and more. However, honeycomb sandwich structures are susceptible to corrosion in certain environments.
When subjected to impact, the honeycomb sandwich will undergo permanent deformation and separate from the skin.
3. Analysis of aerospace materials
Table 2 shows the percentage of structural materials used in military aircraft in the United States. The trend is that the use of composite materials and titanium alloys will gradually increase, while the use of aluminum alloys will decrease.
Table 2 Percentage of Structural Materials for US Military Aircraft
Type | Steel | turns on | titanium alloy | Combined material |
F-16 | 5 | 8 | two | 3 |
F-18A/B | 15 | 50 | 12 | 9.5 |
F-18C/D | 16 | 50 | 13 | 10 |
F-18E/F | 14 | 31 | 21 | 23 |
F-22 | 5 | 16 | 41 | 24 |
F-35 | – | – | 27 | 36 |
F117 | 5 | 20 | 25 | 10 |
B-1 | 9 | 41 | 21 | 29 |
B2 | 6 | 19 | 26 | 38 |
Chapter 17 | 12.3 | 69.3 | 10.3 | 8.1 |
Table 3 shows the breakdown of materials used in typical mainline aircraft. The B787 has 50% composite materials and the A350 has 52% composite materials. The use of composite materials is becoming a trend in the aerospace industry due to their ability to reduce weight, increase damage resistance, provide corrosion protection and increase durability.
However, composite materials also have disadvantages, such as high cost, limited impact resistance, lack of plasticity, greater technical difficulty, low maintenance and difficulty in recycling. As a result, the use of composite materials has not increased on the A320neo and B737MAX compared to the A320 and B737.
Table 3 Proportion of typical mainline aircraft materials (%)
Type | aluminum alloy | Steel | titanium alloy | Combined material | Other |
B373 | 79 | 12 | 5 | 3 | 1 |
B747 | 79 | 13 | 4 | 3 | 1 |
B757 | 78 | 12 | 6 | 3 | 1 |
B767 | 80 | 14 | two | 3 | 1 |
B777 | 70 | 11 | 7 | 11 | 1 |
B787 | 20 | 10 | 15 | 50 | 5 |
A300 | 76 | 13 | 4 | 5 | two |
A310 | 74 | 8 | 5 | 6 | 7 |
A320 | 66 | 6 | 5 | 15 | 8 |
A330/A340 | 66 | 5 | 5 | 16 | 8 |
A380 | 61 | 5 | 5 | 22 | 7 |
A350 | 20 | 7 | 14 | 52 | 7 |
MD-82 | 74.5 | 12 | 6 | 7.5 | – |
MS-21 | 33 | 5 | 19 | 38 | 5 |
Chapter 919 | 63 | 8 | 8 | 21 | – |
Most cabin sections of manned spacecraft are made of aluminum alloys, titanium alloys, and composite materials. For example, the space shuttle's orbiters are constructed primarily of aluminum alloys, while the thrust structure supporting the main engine is made of Qin alloy. The main structure of the middle fuselage is composed of a metal matrix composite material reinforced with boron fiber reinforced aluminum alloy, and the cargo compartment door is made of a special paper honeycomb sandwich structure with material graphite fiber reinforced epoxy resin composite as panel.
Ablative materials are used on the outer surface of the missile head, the spacecraft's reentry capsule, and the inner surface of the rocket engine. Under heat flow, these materials can undergo physical and chemical changes, including decomposition, melting, evaporation, sublimation and erosion. This results in the consumption of mass from the surface of the material, which removes a large amount of heat, preventing the heat flow during re-entry into the atmosphere from entering the aircraft and cooling the combustion chamber and rocket engine nozzle.
To maintain the appropriate temperature in the cabin, thermal radiation protection measures are taken for the reentry section. The outer shell is made of high temperature resistant nickel-based alloy or beryllium plate, and the inner structure is composed of heat-resistant alloy. The outer layer and inner structure are filled with materials with good thermal insulation properties, such as quartz fiber and glass fiber composite ceramics.
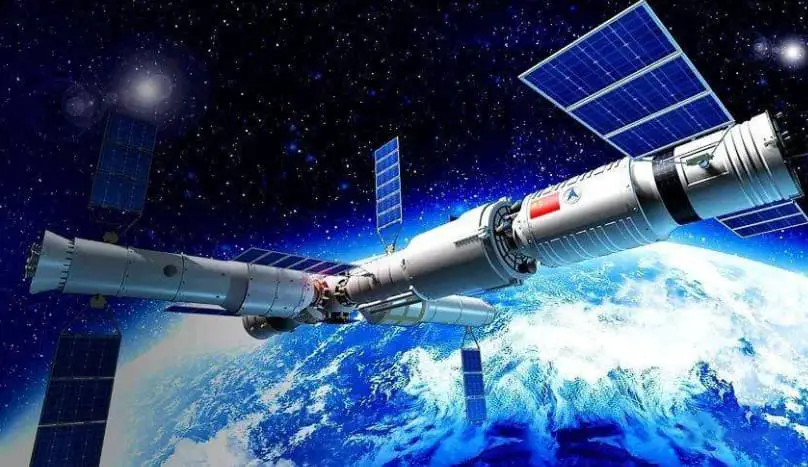
Conclusion
With the implementation and continuous advancement of space projects such as human spaceflight, lunar exploration, deep space exploration, high-resolution satellites, high-speed vehicles, reusable vehicles and mobile space vehicles, new and more demanding requirements are being imposed on materials, offering new opportunities and driving the development of new aerospace materials.
Significant advances have been achieved in the independent assurance of key raw materials and engineering applications in the area of materials.