What is plasma cutting?
Plasma cutting is a processing method that uses the heat from a high-temperature plasma arc to partially or completely melt and evaporate the metal in the cut part, and then uses the momentum of the high-speed plasma to remove the molten metal, forming the cut.
A plasma cutting machine is a machine that uses plasma cutting technology to process metal materials.
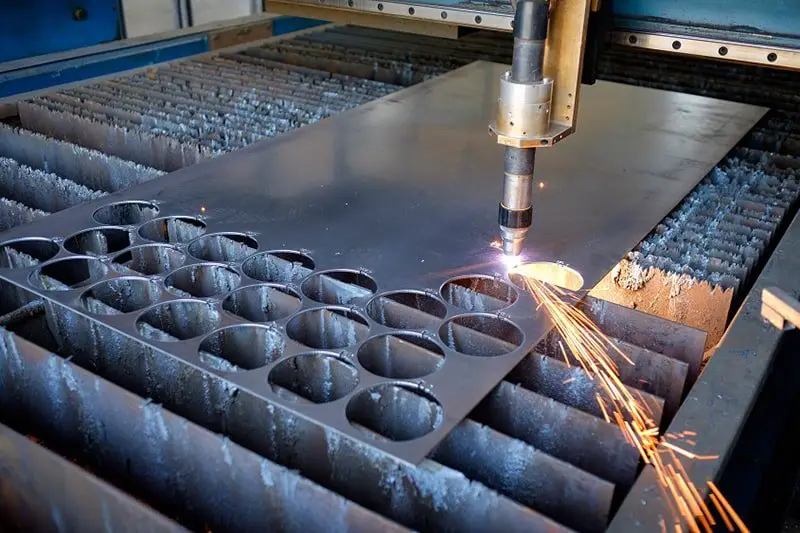
Industrial applications
Plasma cutting is a processing method that uses the heat generated by a high-temperature plasma arc to partially or completely melt and evaporate the metal in the cut, and uses the momentum of the fast-moving plasma to remove the molten metal and create the cut . This method is particularly effective for cutting non-ferrous metals such as stainless steel, aluminum, copper, titanium and nickel, which can be difficult to cut using oxygen cutting.
One of the main advantages of plasma cutting is its speed, especially when cutting thin sheets. Compared to oxygen cutting, plasma cutting can be up to 5 to 6 times faster when cutting common carbon steel sheets. The cut surfaces are smooth and clean, with minimal thermal deformation and a small heat-affected zone.
Plasma cutting machines are widely used in various industries such as automobiles, locomotives, pressure vessels, chemical machines, nuclear machines, general machinery, engineering machines, steel structures and transportation industries.
Working gases
The advancement of plasma cutting technology has had a major impact on the cutting characteristics, quality and speed of the plasma arc. The choice of the working gas (the medium that conducts and transports heat to the plasma arc, excluding the molten metal during cutting) is crucial in this regard.
Common working gases for plasma arc include argon, hydrogen, nitrogen, oxygen, air, water vapor and some mixed gases.

Plasma gas selection
The gas entering the plasma arc is called the ion stream.
Its main functions are the following:
- A. It plays a certain role of thermal insulation and insulation between the arc column and the inner wall of the nozzle hole, compresses the arc and ensures stable arc combustion.
- As a thermal conductor of the ionization medium and the arc, the cut metal is melted quickly.
- blow the molten metal into the crack to form a narrow, smooth crack.
- cooling protection for electrodes.
In light of the above effects of ionic gases, the following requirements must be taken into consideration when selecting gases:
- Easy arc initiation and stable arc: The gas should have low ionization potential and low thermal conductivity, and should have no cooling effect on the arc. Monatomic gas is better than diatomic gas in this aspect.
- Good arc compression property: The gas must have good thermal conductivity, high heat capacity and a strong cooling effect on the arc.
- Good heat transport capacity: The gas must have the ability to transfer heat effectively to the workpiece. Diatomic gas, with its higher ionization potential, generally has better heat transport capacity than monatomic gas with low ionization potential.
- Ability to generate great thrust: The gas must have great mass and density.
- Availability, affordable price and non-toxicity.
Some of the requirements listed above are contradictory, so the main requirements must be met based on specific circumstances. At present, the gases commonly used in plasma arc cutting include nitrogen, argon, hydrogen and their mixture gases, with nitrogen being the most commonly used.
Nitrogen is affordable and readily available, and its use is relatively safe. It is a diatomic gas that is endothermic when it decomposes at the high temperature of the arc.
N2->2N-1084000j/mol
When using plasma cutting, the type of working gas used can have significant impacts on the characteristics, quality and speed of the cut. Common working gases include nitrogen, argon, hydrogen and mixed gases. Of these, nitrogen is the most used due to its low cost and ease of availability, as well as its ability to create favorable conditions for cutting thick materials.
Nitrogen, being a diatomic gas, decomposes into nitrogen ions when exposed to high temperatures in the plasma arc, releasing the heat absorbed during decomposition. This allows the plasma arc to reach high temperatures over a wide range of lengths, making it ideal for cutting materials with high thermal conductivity and low liquid fluidity. The purity of nitrogen used in plasma cutting should not be less than 99.5% to avoid electrode oxidation and nozzle burnout.
Argon is a monatomic gas with a low ionization potential and stable arc combustion, but its high cost makes it a less practical option. Adding hydrogen to nitrogen or argon can improve the compression effect of the arc, resulting in a narrower and smoother cutting surface.
In air plasma cutting, compressed air is used instead of expensive gases, making it a more economical option. The high current cutting speed is much higher than that of flame cutting, and the cutting quality is also very good. For carbon steel sheets below 25mm, the cutting speed is 3 to 5 times faster, and for thin sheets of 5 to 10 mm, it is 6 to 8 times faster. Air plasma cutting has replaced flame cutting in many applications due to its cost-effectiveness and good cut quality.
How to choose NC plasma cutting parameters
Various parameters of the plasma arc cutting process directly affect the cutting process stability, cutting quality and cutting effect.
The main cutting specifications are as follows:
1) Cutting current
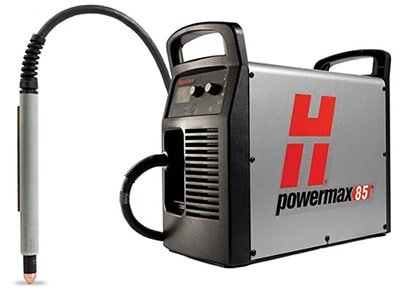
The most important parameter of cutting and cutting speed is the cutting process.
Impact:
- When the cutting current increases, the arc energy increases, the cutting capacity increases and the cutting speed increases;
- As the cutting current increases, the arc diameter increases and the arc becomes thicker, which makes the incision wider;
- If the cutting current is too high, the thermal load of the nozzle will increase, the nozzle will be damaged prematurely, and the cutting quality will naturally decline, even unable to cut normally.
Therefore, when preparing for plasma cutting, it is important to choose the appropriate cutting current and nozzle corresponding to the thickness of the material.
When selecting a power supply for plasma cutting, it is important to avoid choosing a power supply that is too large or too small.
Choosing a power supply that is too large is wasteful in terms of cost reduction, as it does not use the full amount of current.
On the other hand, choosing a power supply with very small current in an effort to save costs is also not ideal as it will not meet the required cutting specifications and may cause damage to the CNC cutting machine itself.
2) Cutting speed
The high temperature and energy of the plasma arc determine the cutting speed, which can be selected within the ideal range according to the equipment instructions or determined through experimentation. The cutting speed may vary depending on the thickness of the material, its properties (e.g. melting point, thermal conductivity, surface tension after melting) and the desired quality.
Maintaining cutting quality, cutting speed should be increased as much as possible to improve productivity and reduce deformation and heat-affected areas. If the cutting speed is not adequate, the opposite effect will occur, leading to increased slag adhesion and decreased cutting quality.
The following are the main manifestations:
If the cutting speed is increased moderately, the cutting quality can be improved, which means that the cut is slightly narrower, the cutting surface is smoother, and the deformation is reduced.
If the cutting speed is too fast, the cutting linear energy will be lower than the required value, and the cutting jet cannot blow the molten cutting material immediately, causing large drag. This results in slag hanging in the cut and the quality of the cut surface decreases.
When the cutting speed is very slow, because the cutting position is the anode of the plasma arc, to maintain the stability of the arc, the anode point or anode area must encounter a conductive current close to the closest cutting seam of the arc. At the same time, it transfers more heat radially to the jet, causing the cut to widen. The melted material on both sides of the cut collects and solidifies at the bottom edge, making cleaning difficult. Additionally, excessive heating and melting causes the top edge of the cut to become rounded.
At very low speeds, wide cutting can even cause the arc to extinguish. Therefore, good cutting quality and speed are inseparable.
3) AN RC voltage
It is generally believed that the normal output voltage of the power supply is the cut-off voltage for plasma cutting. Plasma machine normally operates at higher voltage for plasma arc, especially for air plasma cutting.
When current is constant, an increase in voltage improves arc enthalpy and cutting capacity. Higher enthalpy reduces jet diameter and increases gas flow rate, resulting in faster cutting speed and better cut quality.
No-load voltage and arc column voltage are important factors in plasma cutting power supply. The power supply must have a high enough no-load voltage to easily start the arc and maintain stable combustion of the plasma arc.
The no-load voltage is generally in the range of 120-600 V, while the arc column voltage is generally half the no-load voltage. Increasing the arc column voltage increases the power of the plasma arc, allowing thicker metal plates to be cut at a faster speed.
The arc column voltage can be adjusted by changing the gas flow rate and increasing the internal shrinkage of the electrode, but it should not exceed 65% of the no-load voltage to maintain the stability of the plasma arc.
4) Gas and workflow
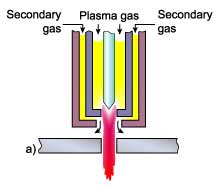
The working gas in plasma cutting includes cutting gas and auxiliary gas, and some equipment also requires an arc starting gas.
The appropriate working gas should be chosen based on the type of material to be cut, its thickness and the cutting method.
The cutting gas must not only form the plasma jet, but also effectively remove the molten metal and oxides from the cutting.
Having excessive gas flow can remove too much heat from the arc, causing the jet length to decrease and decreasing cutting capacity and arc instability.
If the gas flow rate is too low, the plasma arc may lose its straightness, resulting in shallower cuts and increased slag formation.
It is important that the cutting speed and gas flow rate are well matched.
The plasma cutting machine normally controls the gas flow rate. The gas pressure used to cut a given thickness of material should be chosen based on manufacturer data, but in special applications it may be necessary to determine through actual cutting tests.
The most commonly used working gases are argon, nitrogen, oxygen, air and H35 (a mixture of argon and nitrogen).
- Argon
Argon is unlikely to react with any metal at high temperatures and produce a stable plasma arc. The nozzle and electrode used have a long service life, but the argon plasma arc voltage is low, with limited enthalpy and cutting capacity. This results in a 25% reduction in kerf thickness compared to air cutting.
Furthermore, the surface tension of molten metal is higher in an argon-protected environment, about 30% higher than in a nitrogen environment, leading to more slagging problems. Even if a mixture of argon and other gases is used, there is a tendency for slag to stick. As a result, pure argon is rarely used for plasma cutting.
- Hydrogen
Hydrogen is commonly used as an auxiliary gas in combination with other gases. For example, the popular gas H35 (35% volume hydrogen, the rest is argon) is one of the most effective gases in plasma arc cutting, which owes much of its power to hydrogen.
Hydrogen significantly increases the arc voltage, resulting in a high-enthalpy plasma jet. When combined with argon, the cutting ability of the plasma jet is significantly improved.
Argon and hydrogen are commonly used as cutting gas for metal materials thicker than 70mm. By further compressing the argon + hydrogen plasma arc with a water jet, greater cutting efficiency can be achieved.
- Nitrogen
Nitrogen is a commonly used working gas. When operating under higher supply voltage, nitrogen plasma arc exhibits better stability and higher jet energy compared to argon.
When cutting materials with high liquid metal viscosity, such as stainless steel and nickel-based alloys, the amount of slag at the bottom edge of the cut is minimal.
Nitrogen can be used alone or in combination with other gases. For example, nitrogen or air are often used as the working gas in automatic cutting.
These two gases have become the standard for high-speed cutting of carbon steel.
In some cases, nitrogen is also used as the starting gas for oxygen plasma arc cutting.
- Oxygen
Oxygen can increase the cutting speed of low carbon steel.
Using oxygen for cutting results in imaginative cutting modes such as flame cutting.
A high-temperature, high-energy plasma arc results in faster cutting speed, but it must be combined with the use of high-temperature oxidation-resistant electrodes and anti-impact protection to extend the electrode life during the arc process.
- Air
Air is approximately 78% nitrogen by volume, making air cutting a creative method for cutting slag and nitrogen. Air also contains about 21% oxygen.
Due to the presence of oxygen, cutting low carbon steel with air is also very fast. Furthermore, air is the most cost-effective working gas.
However, when air cutting is used alone, problems such as slag adhesion, cutting oxidation and nitrogen build-up may arise.
In addition, the short service life of the electrode and nozzle will also affect work efficiency and increase cutting costs.
5) Nozzle height
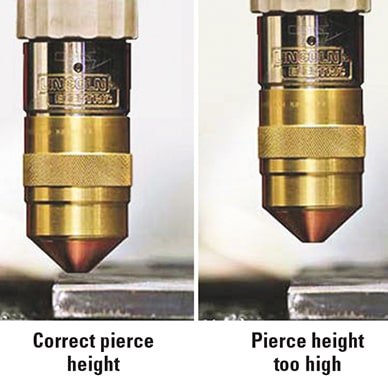
Nozzle height refers to the distance between the end face of the nozzle and the cutting surface and is a component of the total arc length.
Typically, the distance varies from 4 to 10 mm.
Similar to the electrode, it is crucial to maintain an adequate nozzle height to maximize plasma arc cutting efficiency. Otherwise, cutting efficiency and quality will be reduced or the cutting nozzle may burn out.
Because plasma arc cutting typically uses power supplies with constant current or external steep drop characteristics, the current remains relatively unchanged even as the nozzle height increases. However, this results in an increase in arc length and a corresponding increase in arc voltage, thus improving arc power. At the same time, the greater length of the arc exposed to the environment also results in increased energy loss from the arc column.
These two factors often conflict with each other, reducing effective cutting energy and cutting capacity. This is often indicated by a weakened cutting jet blowing force, increased residual slag at the bottom of the cut, excessive melting and a rounded top edge.
Additionally, the diameter of the plasma jet expands as it exits the nozzle, and increasing the nozzle height will result in a wider cut. Therefore, it is advantageous to choose the lowest possible nozzle height to improve cutting speed and quality.
However, if the nozzle height is too low, it may result in the double arc phenomenon.
When using an external ceramic nozzle, the nozzle height can be adjusted to zero, with the end face of the nozzle in direct contact with the cutting surface, resulting in better performance.
5) Bow Power
To achieve high-pressure plasma arc cutting, cutting nozzles are designed with a smaller diameter, longer channel length and improved cooling, which increases the current passing through the effective section of the nozzle, resulting in an increase in power density of the arc. .
However, this also increases the power loss of the arc. As a result, the actual effective power for cutting is less than the power supply output power, with a loss rate typically between 25% and 50%.
Some methods, such as water-compressed plasma cutting, have a higher energy loss rate, which must be considered when designing cutting process parameters or calculating cutting costs.
For example, most metal plates used in industry are less than 50 mm thick. Conventional plasma arc cutting in this thickness range generally results in a cut with a wide top and narrow bottom, which decreases incision size accuracy and increases the amount of subsequent processing.
When the oxygen and nitrogen plasma arc is used to cut carbon steel, aluminum and stainless steel, the perpendicularity of the final edge is better with increasing material thickness in the range of 10 to 25 mm. However, when the plate thickness is less than 1 mm, the incision angle error increases from 3 to 4 degrees to 15 to 25 degrees as the plate thickness decreases.
This phenomenon is believed to be caused by an unbalanced heat input from the plasma jet onto the cutting surface, which means that the energy release from the plasma arc at the top of the cut is greater than that at the bottom. This energy imbalance is closely related to several process parameters, such as the degree of compression of the plasma arc, the cutting speed and the distance between the nozzle and the part.
Increasing the arc compression degree can make the high-temperature plasma jet longer and create a more uniform high-temperature area, and increasing the jet speed can reduce the width difference between the top and bottom of the incision.
However, overcompression of the conventional nozzle often leads to a double arc, which not only consumes the electrode and nozzle, but also decreases the cutting quality.
Furthermore, too high a cutting speed and too large a nozzle height can result in an increase in gap width.
6) Electrode shrinkage
The term “internal shrinkage” refers to the distance between the electrode and the end face of the cutting nozzle. Maintaining an adequate distance allows good compression of the arc at the cutting nozzle, resulting in a plasma arc with concentrated energy and high temperature for effective cutting.
If the distance is too small or too large, the electrode will burn excessively, the cutting nozzle will burn, and the cutting capacity will be reduced. Typical internal shrinkage is 8 to 11 mm.
Electrode selection and polarity:
The electrode used in plasma arc cutting must have low burning loss to ensure the stability of the cutting process. Tungsten, which has a high melting point, still has significant burning loss and cannot guarantee a stable cutting process.
Adding a small amount of low ionization potential elements such as thorium to tungsten significantly reduces the burning loss of thorium tungsten electrode. This is because the thorium tungsten electrode has strong thermal electron emission, causing most of the energy at the electrode end face to escape as electrons, thus lowering the temperature of the electrode end face.
In addition, the thorium tungsten electrode has a weak effect on oxygen, reducing its loss due to high-temperature burning. The commonly used thorium tungsten electrode contains 1.5% to 2.5% thorium. However, thorium is radioactive, so non-radioactive cerium tungsten or lanthanum tungsten electrodes are widely used as alternatives.
In plasma arc cutting, direct polarity is commonly used, connecting the thorium tungsten rod to the negative electrode and the workpiece to the positive electrode. This benefits the thermal emission of electrons, stabilizes the combustion of the isoelectric arc and reduces the electrode burning loss.
Cutting method
In addition to the general form of plasma cutting methods, derived forms include water compression plasma cutting.
The most commonly used methods are general plasma cutting and air plasma cutting.
General cut
General plasma cutting does not require shielding gas, as the working gas and cutting gas are expelled through the same nozzle. When starting the arc, a small flow of ionic gas is expelled as a means of ionization. During the cutting process, a stream of air is also expelled to remove the molten metal.
Air cut
In general, air plasma cutting uses compressed air as the ionizing gas. This method is economical and has a convenient source of gas. The compressed air is heated, decomposed and ionized in the arc, creating oxygen that cuts the metal and produces an exothermic chemical reaction that accelerates the cutting speed. Fully ionized air plasma has high enthalpy, leading to large arc energy and fast cutting speed.
Cutting equipment
The plasma cutting system mainly consists of a gas supply unit, water unit, power supply and cutting torch. The water-cooled torch also requires a circulating water cooling unit.
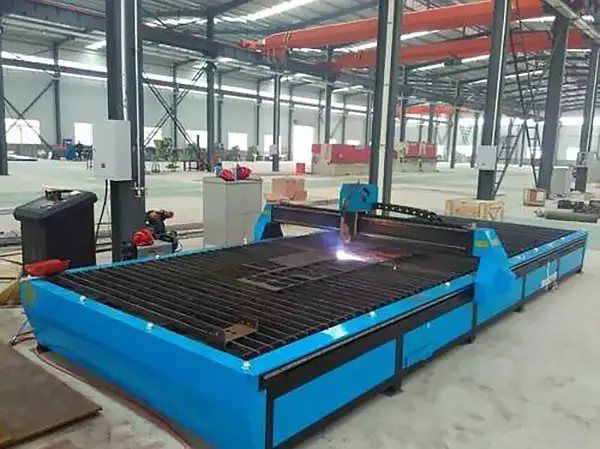
(1) Air Supply Unit
The main equipment of the air supply device for air plasma arc cutting is an air compressor with a power of more than 1.5 kW, and the required air pressure is between 0.3-0.6 MPa. If a different gas is required, bottled gas can be used after decompression.
(2) Power supply
For plasma cutting, a DC power supply with a steep drop or constant current characteristic is used. To ensure satisfactory arc starting and stabilization effect, the no-load voltage of the power supply is generally twice as high as the arc voltage. A typical clipping power supply has a no-load voltage of 350-400 V.
(3) Cutting Gun
The design of the cutting gun depends on the current level of the cutting gun. For cutting guns rated below 60 A, an air-cooled frame is typically used, while for those above 60 A, a water-cooled frame is used. The electrode in the cutting gun can be made of pure tungsten, thorium tungsten, tungsten bell rod or a built-in electrode. Cast tungsten is a preferred electrode material as it is simple to use and can cut all types of non-metallic materials.
Security protection
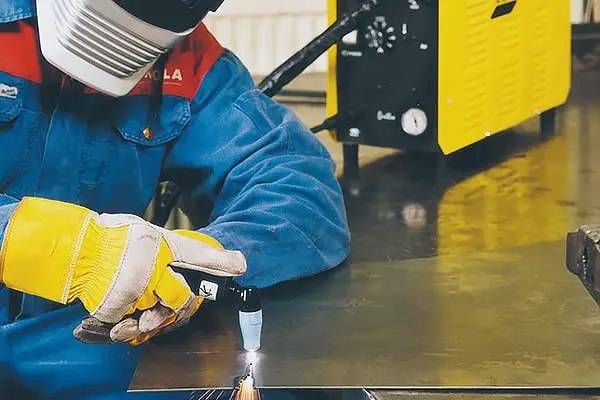
The bottom of a plasma cutting setup must be equipped with a water tank. During the cutting process, the piece must be submerged in water to minimize the toxicity of smoke to human health.
It is important to avoid direct visual exposure to the plasma arc during plasma cutting. Safety glasses and a face mask must be worn to prevent eye and skin burns from intense arc light.
Plasma cutting generates a large amount of toxic gas, so adequate ventilation and the use of multi-layer filter masks are crucial to minimizing exposure.
Additionally, it is important to wear protective clothing, such as a towel, gloves, and foot protection, during plasma cutting to avoid burning your skin from sparks.
It is important to note that the high frequency and electromagnetic radiation generated by the high frequency oscillator during plasma cutting can have harmful effects on the body, and some long-time practitioners have reported symptoms of infertility. Although the medical and industrial communities have not reached a definitive conclusion on this matter, it is still advisable to take protective measures.
How to Choose C NC Plasma Cutting Machine
1. Price
When considering purchasing a plasma cutter, it is important to take the budget factor into consideration. Ignoring the budget can result in choosing a product that goes over budget, even if it meets the desired specifications.
Plasma cutters are currently divided into two categories: domestic and imported. Home plasma cutters have three specifications: low, medium and high, and are generally acceptable to most users.
Imported plasma cutters are much more expensive, with prices several times or even dozens of times higher than those of domestic competitors. Consumables such as cutting nozzles and electrodes are also more expensive.
Although imported plasma cutters offer better cutting results compared to domestic models of the same specification, their high cost and ongoing expenses can make them difficult to accept by many companies.
2. Cutting thickness
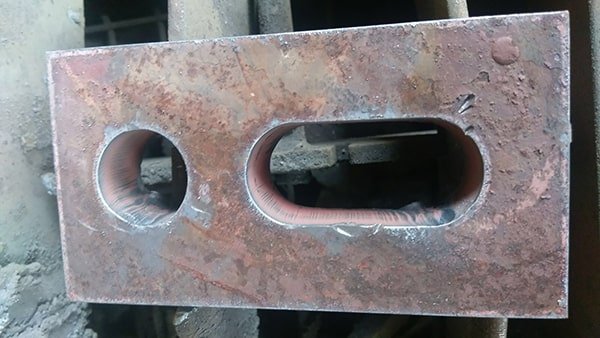
No matter the type of plasma used, it has its own ideal cut size range. It is commonly known that low-power plasma is more suitable for cutting thin sheets. However, if the plasma power is too high, it is not suitable for cutting thin sheets.
At present, domestic 40-60A plasma cutting is widely used to cut steel plates below 2mm, while imported plasma is used occasionally but in limited quantities due to its high cost. It is important to note that for steel sheets below 2mm, only high-speed desktop plasma cutting machines are suitable and other models such as portable and gantry type are not.
If the steel plate is thicker than 2 mm, it is not restricted and can be cut using portable or gantry machines. For steel sheets between 2-16 mm, portable and gantry machines can be used. However, for thicknesses of 25 mm or more, only gantry machines are suitable.
3. Cutting materials
It is widely known among personnel involved in metal processing that plasma cutting is the preferred method for cutting stainless steel and other alloy materials. On the other hand, carbon steel sheets are mainly cut by flame cutting method. Therefore, when it comes to stainless steel, it is essential to have a plasma cutting machine. It cannot be cut using the flame cutting method.
Advantages of NC plasma cutting machine
1. Better cutting quality
Cut quality is mainly affected by factors such as slag, heat affected zone, top fillet and cutting angle. Among these, plasma cutting surpasses flame cutting in terms of slag and heat-affected zone, as there is no residual slag on the edge of plasma cut parts and the heat-affected zone is significantly smaller.
2. S cum
The plasma process involves using high-temperature charged gas to melt metal and blow the molten material away from the cutting surface. On the other hand, flame cutting uses the chemical reaction between oxygen and steel for cutting, resulting in the production of slag or iron oxide slag.
Because of these differences in technology, plasma cutting produces less foam and adhered foam is easier to remove. This foam can be easily eliminated without crushing or additional processing, reducing the time required for secondary processing. This results in greater productivity as fewer grinding operations are required.
3. Heat affected zone
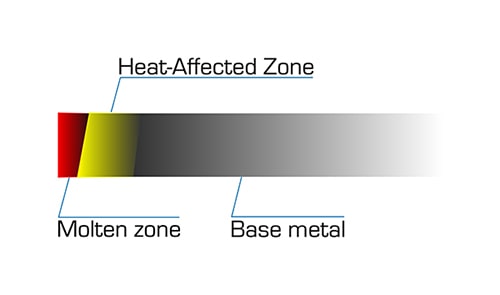
The size of the heat affected zone (HAZ) is a critical factor in metal cutting. When metal is exposed to high temperatures, it can change its chemical structure, causing the edge to darken (take on a tempered color) and deform. If the heated edge is not removed, the part may not be suitable for secondary welding.
The speed at which the torch moves directly impacts the size of the heat-affected zone. Plasma cutting is known for its rapid cutting ability, which results in a smaller heat-affected zone, reducing the time required for secondary processing to remove the heated edge.
Flame cutting users may also notice the color of the fire. Although the heat-affected zone is not visible from the outside, the color of the temper can be seen and can change the color of the metal. As with the heat affected zone, rapid plasma cutting results in a smaller area of fire color.
4. Greater productivity
With CNC plasma cutting and drilling speeds up to 8.5 times faster than flame cutting, significant productivity gains can be achieved, not to mention time saved in preheating and secondary processing.
5. Lower cost per piece
When evaluating costs, it is essential to distinguish between operating costs and the cost per piece or meter. To determine the actual cost of cutting a part, it is important to consider several factors, such as operating cost per meter and cost per part.
Operating cost per meter is calculated by dividing the total cutting cost per hour by the total length that can be cut in one hour. Costs involved in cutting include consumable parts, electricity, gas, labor and sustainability expenses. On the other hand, the cost per part is determined by multiplying the total cutting length required to produce a part by the operating cost per meter.
Because the plasma cutting system operates faster, it is able to produce more parts in a given time, significantly reducing the cost per part. For manual cutting, it is advisable to calculate the cost of each job or task to accurately assess cost savings. Job cost can be calculated by multiplying the operating cost per hour by the total time required to complete the task.
When considering flame cutting, it is necessary to take into account the preheating time and the extended time for secondary processing, as these add to the total time required to complete the job.
6. Greater profitability
The lower cost per part of the plasma system directly results in greater profitability. Each piece cut with this method can generate cost savings, thus increasing the profit margin. The greater the number of parts that can be cut per hour, the greater the overall increase in profits.
7. Easier to use
For those using flame cutting, it takes time and practice to master adjusting the chemical parameters of the flame and maintaining the chemical balance of the flame. On the other hand, Hypertherm's Powermax series operates with compressed air, eliminating the need for mixing or regulating gases.
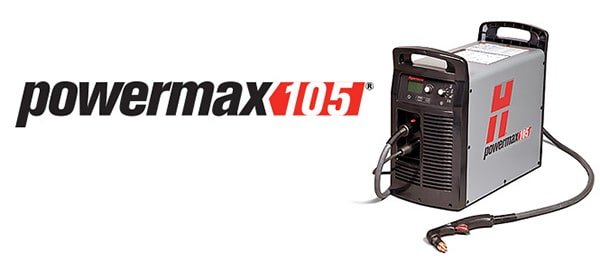
If you are using a CNC mechanical plasma system or automatic gas console, all parameters are pre-set by the manufacturer and there is no need for manual gas adjustment.
Additionally, the Powermax portable plasma system has drag cutting capability, which allows the operator to move the torch along the metal surface without having to maintain a specific distance, a crucial aspect in flame cutting.
Additionally, plasma cutting systems are easier to use, with their simple control devices making it easier for operators to learn and cut according to patterns and patterns, especially those with curves. Ease of use results from the lack of gas adjustment and drag cutting capability.
8. Greater flexibility
The plasma system is capable of cutting any conductive metal, including stainless steel, aluminum, copper and brass, while the flame cutting machine is limited to cutting low carbon steel only through the chemical reaction between oxygen and iron. The plasma system is also versatile and can be used to plan, mark or even cut rusted, painted or stacked metal.
Furthermore, the plasma system is capable of slot cutting or steel mesh cutting, which is a challenge for flame cutting.
9. Greater security
The fuel used in flame cutting is a mixture of oxygen and gas, with the most commonly used fuels being acetylene, propane, MAPP, propylene and natural gas. Among these, acetylene is the most used as it produces a higher flame temperature and faster drilling speed compared to others. 'However, acetylene is an unstable and highly flammable gas, very sensitive to high pressures, temperatures and even static electricity. An acetylene explosion can cause tens of thousands of dollars in property damage and result in serious injury to bystanders.
On the other hand, some plasma systems, such as Hypertherm's Powermax series, operate with compressed air and do not require the use of flammable gases. Hypertherm's HPR and HSD plasma systems can also use a variety of gases, including air, oxygen and nitrogen, which are more stable and do not require special treatment.
It should be noted that all forms of thermal cutting produce some odor and noise, but water cutting machines and CNC plasma cutting systems can significantly reduce the odor and noise produced. On the other hand, flame cutting should not be carried out underwater due to the risk of explosion.
Safety guarantee in plasma cutting machine operation
(1) Operators must wear protective equipment, including masks, welding gloves, hats, dust filter masks, and sound-insulating ear protectors. It is strictly prohibited to look directly into the plasma arc without wearing protective glasses, and bare skin must not come into contact with the plasma arc.
(2) When cutting, the operator should stand on the side where the wind is blowing, as this may reduce the air intake area below the table.
(3) If the no-load voltage is too high during cutting, check the electrical ground, ground connection, and insulation of the torch lead. Isolate the bench from the ground or install an off-load circuit breaker in the electrical control system.
(4) The high-frequency generator must be equipped with a shield. The high-frequency circuit must be cut off immediately after the high-frequency arc is struck.
(5) The use of thorium and tungsten electrodes must comply with article JGJ33-2001 of 12.7.8.
(6) Personnel involved in cutting operations must wear protective equipment in accordance with regulations and take safety measures to prevent electric shock, falling from a height, gas poisoning and fire.
(7) Electric welding machines used on site must be protected from rain, moisture and sun and equipped with fire-fighting equipment.
(8) When welding or cutting at high altitudes, the seat belt must be fastened, fire prevention measures must be taken around and under the welding and cutting areas, and a designated supervisor must be assigned.
Plasma cutting machine daily maintenance
1. Mount the cutting torch correctly
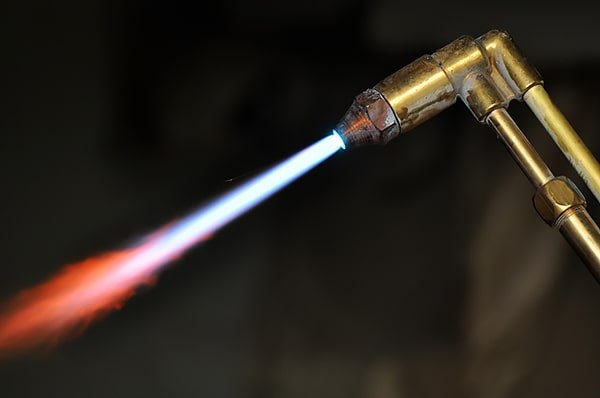
Ensure correct and careful installation of the cutting torch to ensure proper fit of all parts and adequate flow of cooling gas and air. Place all components on a clean piece of flannel to prevent dirt from sticking to them.
2. Consumable parts should be replaced in time before being completely damaged
Consumable parts should not be replaced after they are completely damaged because seriously worn electrodes, nozzles and vortex rings can produce an uncontrollable plasma arc, which can easily cause serious damage to the cutting torch.
Therefore, when a decline in cut quality is first noticed, consumables should be inspected immediately.
3. Clean the cutting torch connection thread
When replacing consumable parts or carrying out daily maintenance and inspection, it is necessary to ensure that the internal and external threads of the cutting torch are clean. If necessary, the connection threads must be cleaned or repaired.
4. Clean the contact surface between the electrode and the nozzle
In many cutting torches, the contact surface between the nozzle and the electrode is a charged contact surface. If there is dirt on these contact surfaces, the cutting torch will not work properly.
5. Check gas and cooling gas every day
Check gas and cooling air flow and pressure every day. If the flow is insufficient or there is a leak, turn off the machine immediately to eliminate the fault.
6. Avoid cutting torch collision damage
To avoid collision damage to the cutting torch, it is necessary to program correctly and avoid overloading the system. Installing an anti-collision device can effectively prevent damage to the cutting torch during a collision.
7. The most common causes of cutting torch damage
① Cutting torch collision.
② Destructive plasma arc due to damage to consumables.
③ A destructive plasma arc caused by dirt.
④ Destructive plasma arc caused by loose parts.
8.Precautions
① Do not lubricate the cutting torch.
② Do not abuse sealing ring lubricant.
③ Do not spray splash-proof chemicals while the protective cover is still on the cutting torch.
④ Do not use a manual cutting torch as a hammer.
Plasma Cutting Machine Operation Precautions
1.1 To reduce energy consumption and improve nozzle and electrode life, “low quality” cutting should be used when cutting thinner parts.
1.2 When the “cutting thickness selection” switch is set to “high quality”, non-contact cutting type cutting (except in special cases) should be used, and water cutting torch should be preferred.
1.3 When the “thickness selection” switch needs to be changed, the host power switch must be turned off first to avoid damage to the parts.
1.4 When installing, disassembling or moving the host, the power supply must be turned off first to avoid accidents.
1.5 The power switch of the host machine must be turned off before the host accessories and components can be installed and removed (such as cutting torch, cutting ground wire, electrode, nozzle, distributor, pressure cap, protective cover, etc. ) . Avoid repeatedly and quickly opening the torch switch to avoid damage to the arcing system or related components.
1.6 When it is necessary to start arc cutting from the middle of the part, stainless steel up to 20 mm thick can be drilled and cut directly.
The method is as follows:
Place the cutting torch at the starting point of the cutting seam and position the cutting torch nozzle axis at an angle of about 75° to the plane of the workpiece. Then turn on the cutting torch switch to start arc piercing.
At the same time, slowly adjust the angle between the nozzle axis and the workpiece surface until the cut workpiece is adjusted to 90°.
After cutting the workpiece, it can be cut normally along the direction of the cutting seam.
However, if the thickness is greater than the above, it is necessary to drill a small hole (diameter not limited) at the starting point of cutting to start arc cutting from the small hole. Otherwise, it is easy to damage the cutting torch nozzle.
1.7 The mainframe has a continuous work rate of 70% (when the “cut thickness selection” switch is set to a low level, continuous work can be close to 100%).
If the continuous working time is too long and the temperature of the main motor is too high, the temperature protection system will automatically shut down and must be cooled down for about 20 minutes before it can continue to work.
1.8 If the compressed air pressure is less than 0.22 MPa, the equipment will immediately enter the protective shutdown state.
At this time, the gas supply system must be renovated. After troubleshooting, the pressure can be returned to 0.45 MPa.
1.9 If the three-phase input power supply is out of phase, the main motor will not operate properly and the red “phase loss indication” light on some models will illuminate.
It is necessary to eliminate the fault before normal cutting.
1.10 For water-cooled machines, the water tank must be filled with tap water and the water pump power plug must be connected.
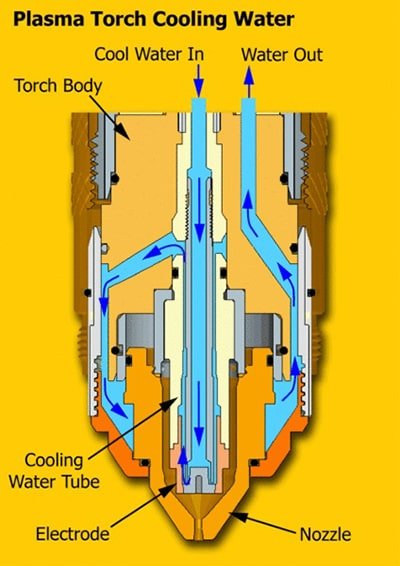
1.11 Set the power switch to the “start” position. If the “insufficient air pressure” indicator is on, adjust it to 0.45 MPa as necessary, then the indicator should be off. The direction of rotation of the fan must correspond to the direction of the signal. The water pump direction of the water cooler must also meet the requirements, otherwise the “insufficient water pressure” indicator light will light up and the inlet power phase must be adjusted.
1.12 According to the thickness of the workpiece, rotate the “cutting thickness selection” switch to the corresponding position and select the appropriate cutting torch. The cutting torch has different specifications, from small to large, according to the range of use. Do not exceed the rated current range or it will be damaged. Place the cutting torch at the starting point of cutting the workpiece and press the torch switch. If the torch does not light once, press the torch switch again. The arc opening is successful and cutting begins.
1.13 Every four to eight hours of operation (the interval time depends on the dryness of the compressed air), the drain screw of the “air filter pressure reducer” must be loosened to drain the accumulated water, in order to avoid excessive water entering the machine or cutting torch and causing failure.
1.14 When the water cooling system is in poor circulation, the main engine will be in the protective shutdown state. At this time, it must be checked and resolved according to the methods described in the relevant chapters. After the water pressure returns to normal, the water-cooled cutting torch can continue to be used.
1.15 When working in a cold environment, it is important to note that when the ambient temperature is below freezing point, the water cooling method should not be used for cutting. Otherwise, the circulating water cooling system will not work properly and the water cooling cutting torch may be damaged.
Preparation before the operation
2.1 After connecting the equipment (pay special attention to the safety ground wire), check carefully and proceed to the next operation if everything is normal.
2.2 Close the power supply switch to supply power to the host. Note: The input AC current is about 65A, which should not be too small; otherwise, the host will not be able to function properly. Check whether the main engine fan meets the requirements; otherwise, adjust the input power phase until the steering direction is consistent.
2.3 Turn the “on/off switch” of the host to the “on” position. At this time, the “power indicator” light should be on. However, the “phase lack indicator” light must not be on; otherwise, the three-phase power supply has a phase loss phenomenon, which needs to be checked and resolved.
Note: If the main motor housing is not properly connected to the safety ground wire, the phase loss indicator may display erroneous results.
2.4 Supply air to the main engine and set the “gas test” and “cut off” switches to the “gas test” position. At this time, compressed air must be ejected from the cutting torch nozzle. After a three-minute test, the red “insufficient air pressure” light should not illuminate.
Check whether the pressure gauge indication value on the “air filter reducer” should not be less than 0.42MPa. Otherwise, it indicates that the air source pressure is less than 0.45 MPa or the flow is less than 300L/min. It could also be that the air supply piping is too small and the air pressure drop is too large.
If there are problems above, please check and resolve them. Also, pay attention to whether the “air filter pressure reducer” is out of balance. If so, it should be readjusted.
The adjustment method is as follows:
Turn the handle clockwise to increase the pressure, otherwise it will decrease. Adjust the indication value on the pressure gauge to 0.42 MPa. If the air supply is normal, the “insufficient air pressure” indicator light will go out. At this time, place the “cut” and “gas test” switch in the “cut” position.
3.1 Contactless manual cutting:
3.1.1 Contact the cutting torch roller with the workpiece and adjust the distance between the nozzle and the workpiece plane to 3-5mm (when the host machine is cutting, adjust the “selection” switch thick” for high level).
3.1.2 Turn on the cutting torch switch to ignite the plasma arc. After cutting the workpiece, move in the cutting direction at medium speed. The cutting speed is: cutting is the premise, which should be fast and not slow. Too slow will affect the quality of the incision and even break the arch.
3.1.3 After cutting, turn off the torch switch and the plasma arc will be extinguished. At this time, compressed air will be ejected to cool the cutting torch. After a few seconds, spraying will stop automatically. Remove the cutting torch and complete the entire cutting process.
3.2 Manual contact cutting:
3.2.1 When the “thickness selection” switch is set to low gear, it can be used when cutting thin sheets on a single machine.
3.2.2 Place the torch nozzle at the starting point of the workpiece to be cut, turn on the torch switch, light the plasma arc, cut the workpiece, and move evenly along the direction of the cutting seam.
3.2.3 After cutting, open and close the torch switch. At this time, compressed air is still ejecting. After a few seconds, spraying will stop automatically. Remove the cutting torch and complete the entire cutting process.
3.3 Automatic Cut:
3.3.1 Automatic cutting is mainly suitable for cutting thick parts. Select the “thickness selection” switch position.
3.3.2 After removing the cutting torch roller, the cutting torch is firmly connected to the semi-automatic cutting machine, and there are connecting parts in the attached accessories.
3.3.3 Connect the power supply of the semi-automatic cutting machine and install the guide rail or radius rod according to the shape of the workpiece (if the guide rail is used for linear cutting, if the circular or circular arc is cut , the radius rod must be selected).
3.3.4 If the torch switch plug is removed, replace the remote control switch plug (provided in the supplied accessories).
3.3.5 Adjust the walking speed according to the thickness of the part. The “reverse” and “forward” switches of the semi-automatic cutting machine are placed in the cutting direction.
3.3.6 Adjust the distance between the nozzle and the workpiece to 3~8mm, and adjust the center position of the nozzle to the starting range of the workpiece cutting seam.
3.3.7 Turn on the remote control. After cutting the workpiece, turn on the switch of the semi-automatic cutting machine to cut. In the initial stage of cutting, you should pay attention to the cutting seam at any time and adjust it to the appropriate cutting speed. And pay attention to whether the two machines work normally at any time.
3.3.8 After cutting, turn off the remote control and power button of the semi-automatic cutting machine. So far, the entire cutting process is completed.
3.4 Manual circular cutting:
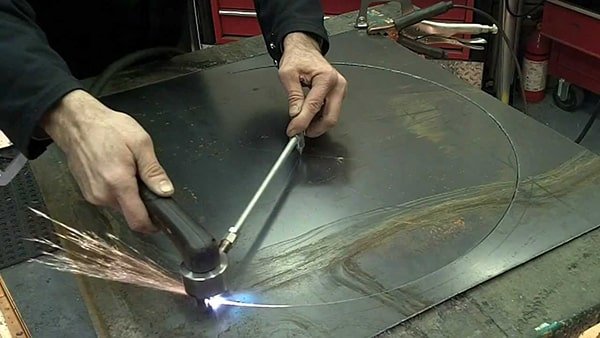
Based on the material and thickness of the workpiece, select single machine or parallel machine cutting mode and choose the corresponding cutting method. Screw the crossbar into the screw hole on the cutting torch bracket.
If the length of one part is not enough, it can be connected to the required radius length one by one. After that, the distance between the cutting torch tip and nozzle can be adjusted according to the workpiece radius length (consider the slot width).
When adjustment is complete, tighten the top set screw to prevent loosening and loosen the cage knurled screw.
At this point, the workpiece can be cut into a round shape.