The world's first laser was developed by American scientist Professor Theodore Harold Maiman using ruby in 1960. Since then, lasers have been used in various fields, contributing to the rapid development of science and technology in medical treatment, equipment manufacturing, measurement needs and remanufacturing. Engineering. The promotion of laser technology has accelerated the pace of social progress and led to significant achievements in the field of cleaning applications.
Compared with traditional cleaning methods such as mechanical friction, chemical corrosion and high-frequency ultrasound, laser cleaning can achieve fully automatic operation with the advantages of high work efficiency, low cost, no pollution to the environment, no damage to the substrate and a wide range of applicable materials. It fully complies with the processing concept of ecological and environmental protection, making it the most reliable and effective cleaning method currently available.
Cleaning is a necessary prerequisite for detecting and processing used machine parts. The use of laser cleaning technology can effectively control the morphology and surface roughness of the substrate, while improving the performance of the substrate after cleaning. It can also be applied to the manufacturing, surface treatment or remanufacturing of large parts.
Although laser cleaning has not entirely replaced traditional cleaning methods, growing national awareness about energy conservation and emission reduction in the manufacturing industry will lead to its gradual adoption due to its unique advantages. After 2020, when China's environmental protection laws and regulations became stricter and people's environmental and safety awareness increased, the types of chemicals that can be used in cleaning industrial production have decreased. Thus, finding a cleaner and non-destructive cleaning method has become a pressing issue.
Laser cleaning has the characteristics of non-grinding, non-contact, no thermal effect and suitability for all types of objects. It is considered the most reliable and effective solution to this problem. Additionally, laser cleaning can solve problems that traditional cleaning methods cannot solve.
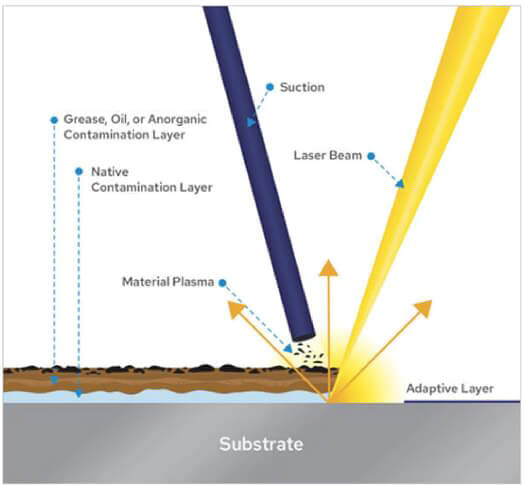
Laser cleaning principle
Introduction
When submicron pollution particles adhere to the surface of a workpiece, they often adhere very tightly, making them impossible to remove with conventional cleaning methods. However, cleaning the surface of the part with nano laser radiation is very effective.
Furthermore, laser cleaning is a non-contact cleaning method, making it very safe to clean precision parts or their fine parts and ensure their precision.
Therefore, laser cleaning has unique advantages in the cleaning industry.
But why can lasers be used for cleaning and why don't they damage the cleaned object? To answer these questions, we first need to understand the essence of lasers.
In short, lasers are no different from the light that accompanies us (visible light and invisible light) that surrounds us. However, the laser uses a resonator to focus the light in the same direction, making it more powerful and precise than simple wavelength and coordination.
Therefore, theoretically, all wavelengths of light can be used to form a laser. However, in practice, there are few media that can be excited, so the laser light source that can produce stable and suitable industrial output is quite limited.
Nd:YAG lasers, carbon dioxide lasers and excimer lasers are widely used. Nd:YAG lasers, in particular, can be transmitted through optical fibers and are best suited for industrial applications, making them widely used in laser cleaning.
Academically, laser ablation (the scientific name for laser cleaning) or light ablation is a process of removing materials from solid (or sometimes liquid) surfaces by irradiating them with a laser beam.
With low laser flux, the material is heated and evaporated or sublimated by the absorbed laser energy. At high laser flux, materials are often converted into plasma. Generally, laser ablation refers to the removal of materials with a pulsed laser, but if the laser intensity is high enough, materials can be ablated with a continuous wave laser beam.
Deep ultraviolet excimer lasers are mainly used for optical ablation. The laser wavelength for optical ablation is about 200 nm.
The depth of absorption of laser energy and the amount of material removed by a single laser pulse depend on the optical properties of the material, the laser wavelength, and the pulse length.
The total mass of each laser pulse removed from the target is generally called the ablation rate. The characteristics of laser radiation, such as the scanning speed of the laser beam and the coverage of the scan line, will significantly affect the ablation process.
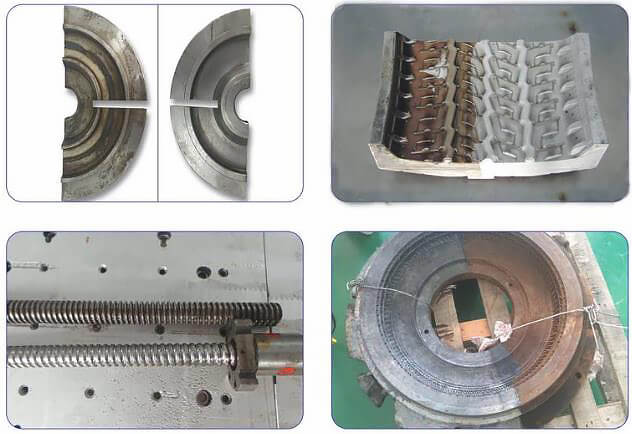
Effect of tire mold laser cleaning
Laser cleaning principle
In the mid-1980s, scientists such as Beklemyshev and Alrn conducted research on laser cleaning, combining laser technology with cleaning technology in response to actual work needs. This led to the development of the technical concept of laser cleaning.
As we know, the binding force between pollutants and the matrix can be categorized into covalent bonds, double dipoles, capillary action and van der Waals force. If this force can be overcome or destroyed, the decontamination effect can be achieved.
Laser cleaning uses the characteristics of a laser beam, such as its large energy density, controllable direction and strong convergence ability, to destroy the binding force between pollutants and the matrix or directly vaporize pollutants. This reduces the binding force between pollutants and the matrix, thus cleaning the surface of the part.
The schematic diagram of laser cleaning is shown in Fig.
When the pollutant on the surface of the part absorbs the laser energy, it overcomes the force between the pollutant and the substrate surface through rapid gasification or instantaneous thermal expansion. As a result of increased heating energy, pollutant particles vibrate and fall from the surface of the substrate.
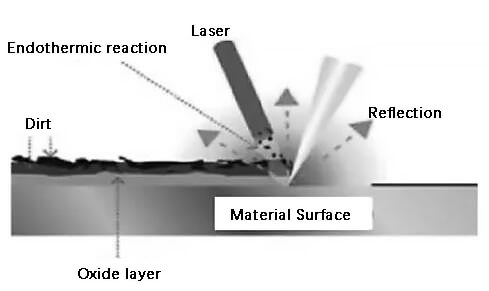
Figure 1 Schematic diagram of laser cleaning
The entire laser cleaning process is divided into four steps:
- Laser gasification and decomposition
- laser blasting
- Thermal expansion of polluting particles
- Substrate surface vibration and pollutant separation
When applying laser cleaning technology, it is important to consider the laser cleaning limit of the object being cleaned and select the appropriate laser wavelength to achieve the best cleaning effect.
Laser cleaning not only allows changes to the grain structure and orientation of the substrate surface without damaging it, but also allows control of the substrate surface roughness, improving the overall surface properties.
The cleaning effect is mainly influenced by the characteristics of the laser beam, the physical parameters of the substrate and dirty materials, and the absorption capacity of dirt to radiate energy.
At present, laser cleaning technology includes dry laser cleaning technology, wet laser cleaning technology and laser plasma shock wave technology.
Dry laser cleaning
Pulsed laser cleaning is a process in which a laser beam is directed at the part, increasing the energy absorption temperature of the substrate or surface pollutants. This causes thermal expansion or thermal vibration of the substrate, which separates the pollutants.
There are two cases in which this method can be applied:
First, when surface pollutants absorb the laser and expand, they separate from the substrate.
Secondly, when the substrate absorbs the laser, it produces thermal vibration, leading to the separation of pollutants from the substrate.
Wet laser cleaning
Wet laser cleaning involves applying a liquid film to the surface before irradiating the workpiece with a pulsed laser. The laser heats the liquid film, causing it to vaporize quickly.
During vaporization, a shock wave is generated that dislodges polluting particles from the substrate.
This method is limited by the requirement that the matrix not react with the liquid film, thus restricting the range of applicable materials.
Laser Plasma Shock Wave
Laser plasma shock wave cleaning technology involves producing a spherical plasma shock wave when breaking through the air medium during laser irradiation.
The shock wave acts on the surface of the substrate and releases energy to remove pollutants, without damaging the substrate, as the laser does not impact it directly.
This technology can effectively clean pollutant particles as small as tens of nanometers and is not limited by laser wavelength.
In actual production, various test methods and related parameters must be selected based on specific needs to ensure high-quality cleanliness of workpieces.
During the laser cleaning process, evaluating the efficiency and quality of surface cleaning is crucial to determining the effectiveness of the technology.
The advantage is
Compared with traditional cleaning methods such as mechanical friction cleaning, chemical corrosion cleaning, strong liquid-solid impact cleaning and high-frequency ultrasonic cleaning, laser cleaning offers several advantages.
2.1 Laser cleaning is a “green” cleaning method that does not require the use of any chemical agents or cleaning solutions. The waste produced during cleaning is mainly solid dust, small in volume, easy to store and recyclable. This makes it possible to tackle environmental pollution caused by chemical cleaning.
2.2 Traditional cleaning methods are often contact cleaning, which exerts mechanical force on the surface of the cleaned object, causing damage to the surface, or the cleaning medium is stuck to the surface, causing secondary pollution. Non-grinding, non-contact laser cleaning can solve these problems.
2.3 Lasers can be transmitted through optical fiber and can work together with a manipulator and a robot for long-distance operation. They can clean parts that are difficult to access using traditional methods, ensuring personnel safety in some dangerous locations.
2.4 Laser cleaning can remove various types of pollutants on the surface of various materials and achieve a level of cleanliness that cannot be achieved by conventional cleaning methods. It can also selectively clean the pollutants on the surface of the material without damaging it.
2.5 Laser cleaning is highly efficient and saves time.
2.6 Although the one-time investment in purchasing a laser cleaning system is high, the cleaning system can be used stably for a long time with low operating costs and only hourly electricity charges.
P principle
The pulsed Nd:YAG laser cleaning process depends on the characteristics of the optical pulse generated by the laser and is based on the photophysical reaction resulting from the interaction between a short, high-intensity pulsed laser beam and a pollution layer.
The physical principle can be summarized as follows:
a) The emitted laser beam is absorbed by the contaminated layer of the surface to be treated.
b) The absorption of a large amount of energy creates a rapidly expanding plasma (a highly ionized unstable gas) that generates shock waves.
c) The shock wave breaks down pollutants into fragments and removes them.
d) The pulse width of the light must be short enough to avoid heat build-up that could damage the treated surface.
e) Experiments show that if there are oxides on the metal surface, plasma occurs on the metal surface.
Plasma is generated only when the energy density exceeds the threshold, which depends on the contaminated or oxide layer removed.
If the energy density exceeds this limit, the base material may be damaged.
To clean the substrate effectively and at the same time ensure its safety, the laser parameters must be adjusted according to the situation so that the optical pulse energy density is strictly between the two limits.
Each laser pulse removes a certain thickness of the pollution layer. For thicker contamination layers, multiple cleaning pulses are required.
The number of pulses required to clean the surface depends on the degree of surface contamination. An important result of both limits is self-control of cleaning.
Light pulses with an energy density greater than the first threshold will remove contaminants until the base material is reached.
However, as its energy density is lower than the failure limit of the substrate material, the substrate will not be damaged.
P practical application
Laser cleaning is a versatile technique that can effectively remove organic and inorganic contaminants such as metal corrosion, metal particles, dust, etc. Below are some practical applications of this technology, which has already reached a high level of maturity and is widely used.
4.1. Mold cleaning:
Every year, tire manufacturers around the world produce hundreds of millions of tires. During the production process, tire mold cleaning must be efficient and effective to minimize downtime.
Traditional cleaning methods, such as sand blasting, ultrasonic cleaning or carbon dioxide cleaning, require the mold to cool for several hours before being transported to cleaning equipment. This process takes a lot of time and can easily compromise the accuracy of the mold. Furthermore, the use of chemical solvents and the resulting noise can raise concerns about safety and environmental protection.
The laser cleaning method offers a solution to these challenges. As the laser can be transmitted through optical fiber, it has great flexibility of use. Additionally, the laser cleaning method can be combined with fiber optics to direct light to hard-to-reach areas of the mold, making cleaning easier. Additionally, the laser cleaning process does not gasify the rubber, eliminating the risk of toxic gas emissions and ensuring a safe working environment.
Laser cleaning technology for tire molds has been widely adopted in the European and American tire industries.
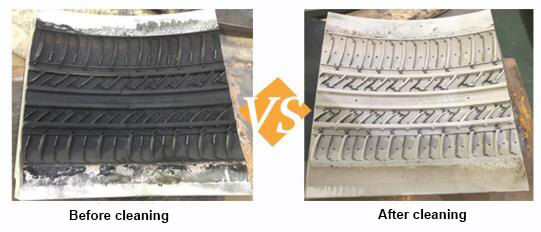
Effect of laser tire cleaning
Although the initial cost of laser cleaning equipment is high, the benefits of reduced downtime, preventing mold damage, improving safety, and reducing raw material usage can quickly offset this investment.
According to a cleaning test carried out on a tire company's production line, a set of large truck tire molds can be cleaned online using laser cleaning equipment in just 2 hours.
Compared to traditional cleaning methods, the economic benefits of using laser cleaning are clear.
In the food industry, the non-stick elastic film on molds needs to be replaced regularly to maintain hygiene. Laser cleaning, which does not require chemical agents, is also suitable for this application.
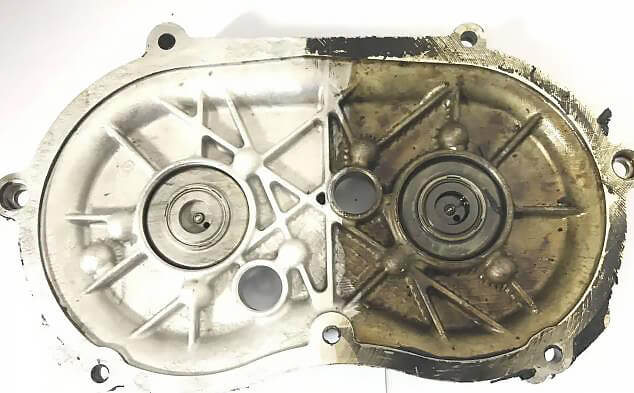
Mold cleaning effect
4.2. Cleaning weapons and equipment:
Laser cleaning technology is widely used in gun maintenance.
The laser cleaning system is an efficient and quick way to remove rust and contaminants, as well as allowing selective removal, resulting in an automated cleaning process.
Compared to chemical cleaning, laser cleaning not only provides a higher level of cleaning, but also minimizes surface damage to the objects being cleaned.
Furthermore, by adjusting different parameters, a dense oxide protective film or metal fusion layer can be formed on metal surfaces, increasing their strength and corrosion resistance.
Finally, the waste generated by laser cleaning is environmentally friendly and the process can be carried out remotely, reducing the risk of health hazards for operators.
4.3. Removing old aircraft paint:
In Europe, laser cleaning systems have been widely used in the aviation industry for a long time.
Aircraft surfaces need to be repainted after a certain period, but before this happens, the old paint must be completely removed.
Traditional mechanical paint removal methods can easily damage the metal surface of the aircraft and pose a threat to flight safety.
However, by using various laser cleaning systems, the paint layer on the surface of an Airbus A320 can be completely removed in two days without causing any damage to the metal surface.
4.4. Cleaning the exterior wall of the building:
With China's rapidly growing economy, more and more skyscrapers are being built and the challenge of cleaning their exterior walls is becoming more and more prevalent. The Laserlaste laser cleaning system offers an effective solution for cleaning external walls of buildings using optical fibers up to 70 meters long.
This system can effectively clean all types of pollutants from various surfaces such as stone, metal and glass, resulting in cleaning efficiency several times higher than conventional cleaning methods.
It can also remove black spots and discoloration from various stone materials used on building exteriors.
Experiments using the laser cleaning system on buildings and stone slabs in Songshan Shaolin Temple have shown that laser cleaning has a highly positive effect on protecting ancient buildings and restoring their appearance.
4.5. Cleaning in the electronics industry
The electronics industry uses laser technology for oxide removal. Precision decontamination is crucial in this industry, making laser oxide removal an ideal solution.
Before soldering a circuit board, it is necessary to completely remove any oxides from the component pins to ensure optimal electrical contact. This process should not damage the pins.
Laser cleaning is able to meet these requirements and is highly efficient. In fact, a single pin only needs to be exposed to the laser once for effective decontamination.
4.6. Precision degreasing cleaning in the precision machinery industry:
In the precision machinery industry, it is often necessary to remove esters and mineral oils used for lubrication and corrosion resistance of parts. This is typically done using chemical methods, but chemical cleaning often leaves residue.
Laser deesterification is an alternative that can completely remove esters and mineral oils without damaging the surface of the parts. This is achieved through the use of a shock wave.
The shock wave is formed by the explosive gasification of the thin layer of oxide on the surface of the parts, leading to the removal of pollutants and not by mechanical interaction.
This laser cleaning method is widely used in the aerospace industry for complete deesterification of mechanical parts.
It can also be applied to the machining of mechanical parts to remove oil esters.
4.7. Pipeline cleaning in nuclear power plant reactor:
The laser cleaning system is also used to clean pipes in nuclear power plant reactors.
Using optical fibers, a high-power laser beam is introduced into the reactor to directly remove radioactive dust, resulting in easy-to-clean materials. Furthermore, remote operation ensures personnel safety.
In conclusion, laser cleaning plays a crucial role in many fields, including automobile manufacturing, semiconductor wafer cleaning, precision parts processing and manufacturing, military equipment cleaning, building exterior wall cleaning, cultural artifact protection, cleaning of circuit boards, precision parts processing and manufacturing, LCD cleaning, chewing gum residue removal and more.
Main cleaning methods
There are four main laser cleaning methods:
① Laser Dry Cleaning Method, also known as Pulsed Laser Direct Radiation Decontamination.
② Laser + Liquid Film Method, which involves depositing a layer of liquid film on the surface of the substrate and then decontaminating it with laser radiation.
③ The Laser + Inert Gas Method, which involves blowing inert gas onto the surface of the substrate while laser radiation is being applied. Once the dirt is removed from the surface, it is immediately expelled by the gas to prevent re-pollution and oxidation.
④ After the dirt is removed by the laser, it is cleaned with a non-corrosive chemical method. This method is only used to clean stone cultural relics.
The first three methods are the most used, while the fourth method is only used in specific cases.
Laser cleaning technology has been applied internationally to stone materials for more than ten years. In China, the application of laser cleaning technology to stone materials began later due to the high cost of laser equipment.
Despite the high cost, laser cleaning technology has many advantages over traditional cleaning methods, and as the technology continues to improve and equipment becomes more widely available, it is expected to play a significant role in the cleaning industry. cleaning of stone materials.