14Cr17Ni2 material belongs to the martensitic ferritic stainless steel category and has good corrosion resistance and high mechanical properties. It is resistant to oxidizing acids and organic acids in aqueous solutions.
This alloy is commonly used for manufacturing structural parts and fasteners that require corrosion resistance. Components are subject to tension, shear and impact and must not only have conventional mechanical properties but also good impact resistance.
However, hot processing of 14Cr17Ni2 is complicated and often results in unqualified mechanical properties. According to statistics, impact energy is mainly affected, which increases production costs, delays delivery times and causes unnecessary losses.
This post presents the results of experimental research that prove that 14Cr17Ni2 has obvious brittleness when quenching at medium temperatures. The phenomenon of brittle temperament was first discovered during World War I and was referred to as “Krupp disease.”
Small fluctuations in chemical composition can significantly impact the structure and properties of steel, and changes in carbon and chromium content have a significant effect on impact energy.
Therefore, in practical use, the composition must be controlled and adjusted according to the application conditions and requirements. Eleven furnace forged bars of 14Cr17Ni2 alloy with different chemical compositions were treated with the same heat treatment system, and Charpy impact tests of U-notch specimens were carried out.
The impact of different chemical compositions on impact energy was compared and analyzed. Furthermore, the Charpy impact test of U-notched samples was carried out after a forged bar furnace was treated with different tempering temperatures, and the impact of different tempering temperatures on the impact energy was compared.
Test materials and methods
11 14Cr17Ni furnaces 2 alloy forged rods with a diameter of 90 mm are used.
See Table 1 for chemical composition.
Table 1 Chemical composition of forged rod (% by weight)
Serial number: | W | Cr | No | Mn | Yes | s | P |
0.11~0.17 | 16~18 | 1.5~2.5 | ≤0.8 | ≤0.8 | ≤0.015 | ≤0.03 | |
1 | 0.15 | 16.1 | 1.77 | 0.56 | 0.28 | 0.0018 | 0.022 |
two | 0.14 | 16.2 | 1.77 | 0.56 | 0.28 | 0.0018 | 0.022 |
3 | 0.15 | 16.21 | 2.27 | 0.5 | 0.58 | 0.0018 | 0.02 |
4 | 0.16 | 16.3 | 2.23 | 0.37 | 0.054 | 0.0026 | 0.013 |
5 | 0.14 | 4:45 p.m. | 2.26 | 0.6 | 0.12 | 0.0004 | 0.022 |
6 | 0.14 | 4:46 p.m. | 2.27 | 0.62 | 0.15 | 0.0003 | 0.023 |
7 | 0.15 | 2:46 p.m. | 2.25 | 0.46 | 0.1 | 0.0024 | 0.012 |
8 | 0.14 | 4:47 p.m. | 2.3 | 0.34 | 2.3 | 0.0015 | 0.02 |
9 | 0.16 | 4:49 p.m. | 2.26 | 0.52 | 0.31 | 0.0018 | 0.013 |
10 | 0.15 | 16.5 | 2.23 | 0.24 | 0.51 | 0.0012 | 0.011 |
11 | 0.12 | 16.51 | 2.34 | 0.47 | 0.34 | 0.006 | 0.017 |
To examine the impact energy of 14Cr17Ni2 as a result of tempering temperature, a No. 10 forged rod was first heat treated at 990℃ for 1.5 hours using oil cooling. After quenching in oil, the rod was quenched by keeping it at temperatures of 300℃, 380℃, 400℃, 450℃, 520℃, 550℃, 600℃ and 680℃ for 4 hours and then cooled with water.
To investigate the effect of the chemical composition of 14Cr17Ni2 on impact energy, 11 furnace-forged bars were heat treated at 990°C for 1.5 hours using oil quenching, followed by tempering at 300°C and 520°C. , respectively.
The sample size for the Charpy pendulum impact test as per metal materials method GB/T 229-2020 was 55 mm × 10 mm × 10 mm with U-shaped notch and was carried out at room temperature in the longitudinal direction .
The metallographic structure was observed using an Olympus Gx71 metallographic microscope.
The corrosion agent used was a mixture of CuCl2 (5g), HCl (100ml) and ethanol (100ml).
Analysis of test results
Effect of tempering temperature on impact energy of 14Cr17Ni2
Figure 1 shows the impact energy of 14Cr17Ni2 under different tempering temperatures.
By comparing the relationship between different tempering temperatures and impact energy, it was found that within the tempering range of 300°C to 450°C, the impact energy of the material significantly decreases from 100J to 19J.
However, within the tempering range of 300°C to 680°C, the impact energy initially decreases and then increases. When tempering at 680°C, the impact energy increases to 78J, with the lowest point of impact energy at around 450°C at 19J.
This indicates that the material presents obvious brittleness upon quenching. The temperature range for this tempering brittleness is 350°C to 550°C, and the tempering temperature has a significant impact on the impact energy of the material.
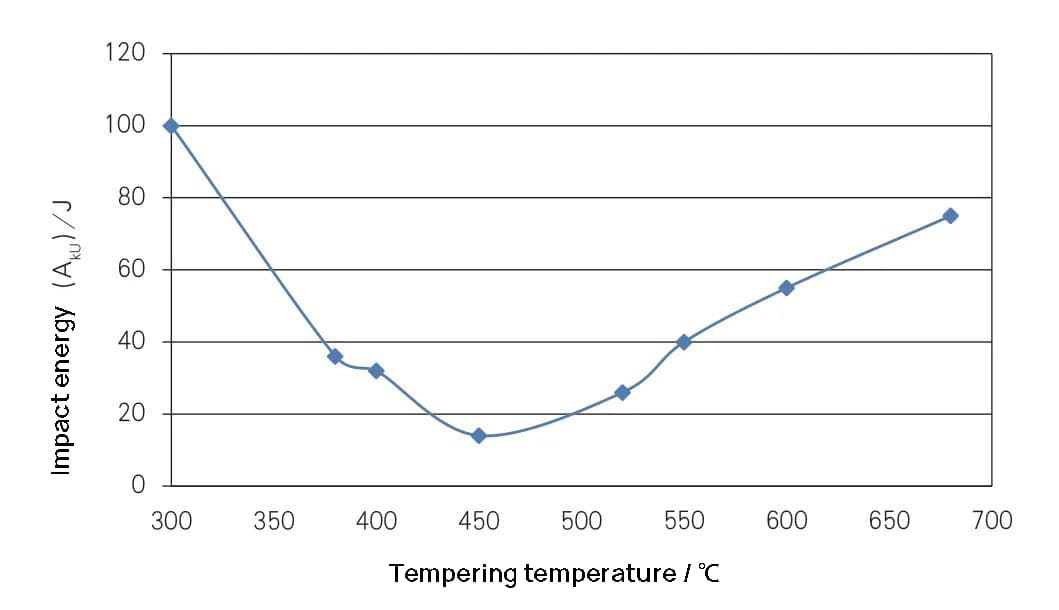
Fig. 1 Impact energy of 14Cr17Ni2 at different tempering temperatures
By comparing the macroscopic fracture morphology under different tempering temperatures (Fig. 2 and Fig. 3), it can be seen that the fracture tempered at 520℃ exhibits a typical intergranular brittle fracture. This is characterized by numerous shiny surfaces, each of which corresponds to a grain boundary.
On the other hand, the macroscopic morphology of the fracture surface tempered at 600 ℃ shows ductile fracture, characterized by transgranular fracture and river pattern. This is evident by the presence of clear dimples and shear edges on the fracture surface.
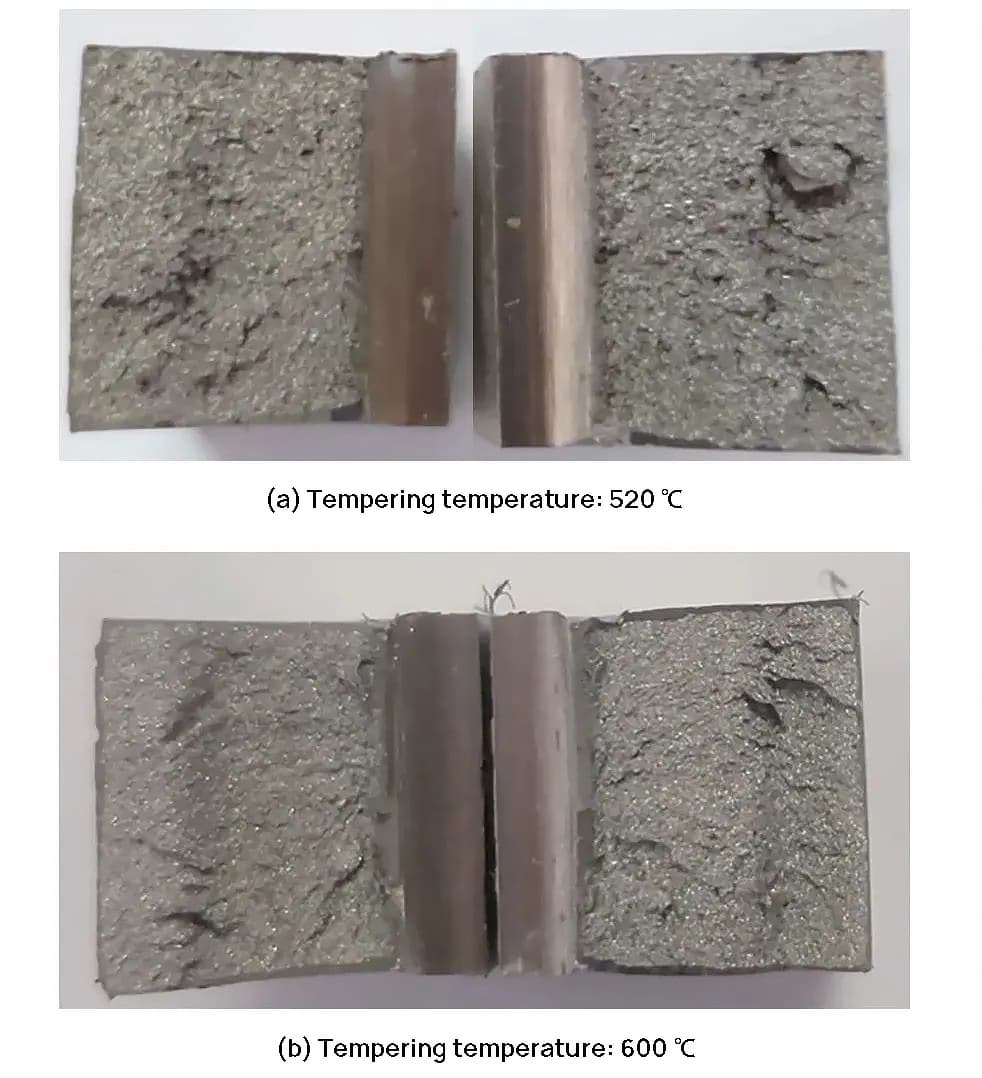
Fig. 2 Fracture macromorphology under different tempering temperatures
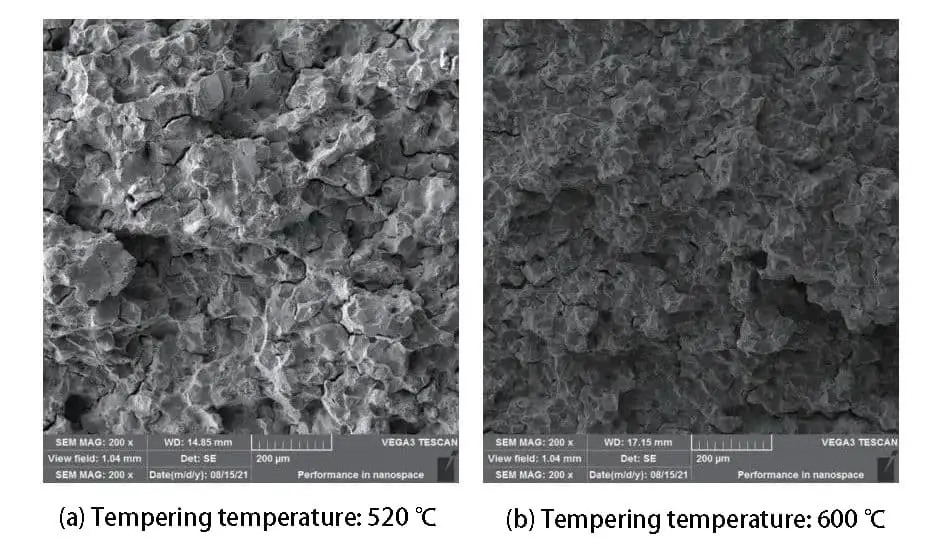
Fig. 3 Fracture morphology under different tempering temperatures
The microstructure of 14Cr17Ni2 after quenching is composed of martensite and ferrite.
After tempering, martensite undergoes decomposition and formation of carbides, while ferrite remains unchanged.
When tempering at temperatures between 200°C and 300°C, carbide precipitation in the matrix structure gradually increases and remains finely dispersed, resulting in high impact energy.
At 350°C, a limited amount of carbides precipitates at grain boundaries.
Between 400°C and 550°C, the amount of carbides precipitated between the laths and grain boundaries increases significantly, leading to a dispersed distribution along the laths and grain boundaries.
This increased precipitation of carbides at grain boundaries leads to a significant decrease in the impact energy of the steel and a notable tendency toward brittleness and intergranular fracture.
When the tempering temperature exceeds 600°C, carbides begin to dissolve and the brittleness of the steel is reduced.
Effect of chemical elements on the impact energy of 14 C r17 N i2
14Cr17Ni2 steel is a type of martensitic ferritic stainless steel. Its tempered state structure is composed of martensite, delta ferrite and retained austenite.
During tempering, M23C6 carbides precipitate from martensite and delta ferrite and accumulate at grain boundaries. This results in the decomposition of martensite into temperate sorbite.
Figure 4 shows the metallographic microstructure at various impact energies. It can be observed that the metallographic microstructure with impact energies of 52J and 35J has particle size grade 5. However, the latter presents a greater number of carbide particles precipitated at the grain boundaries.
The presence of these carbides at the grain boundaries significantly reduces the impact energy of the steel, making it more brittle and subject to intergranular fractures.
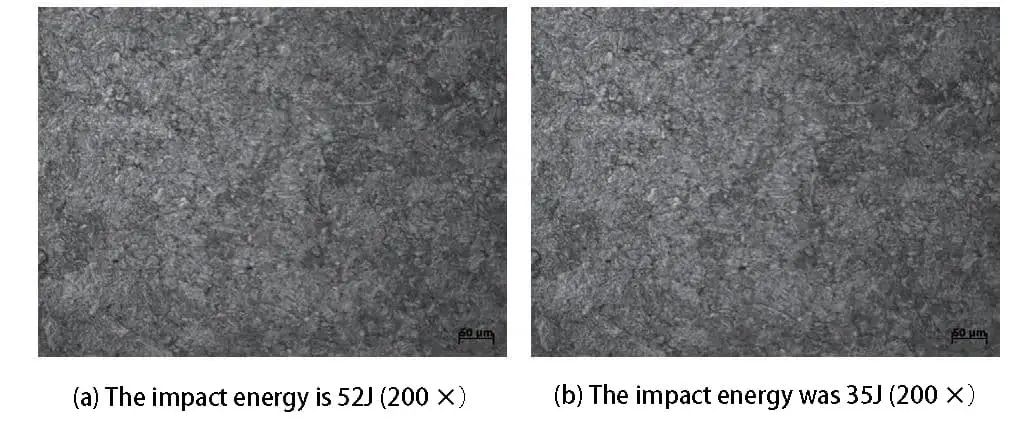
Fig. 4 Metallographic microstructure corresponding to different impact energies
The primary alloying elements in 14Cr17Ni2 are C, Cr and Ni, while Si and Mn have minimal impact on the structure and properties of the steel. The presence of Ni has no significant effect on temper brittleness. The impact energy of 14Cr17Ni2 forgings is mainly determined by the C and Cr content, as chromium carbide influences the impact energy.
This is demonstrated in Figure 5, which shows the impact energy of 14Cr17Ni2 with varying levels of C and Cr. The impact energy at both 300°C and 520°C shows a similar trend, reinforcing the conclusion that the impact energy of the raw materials is the main factor.
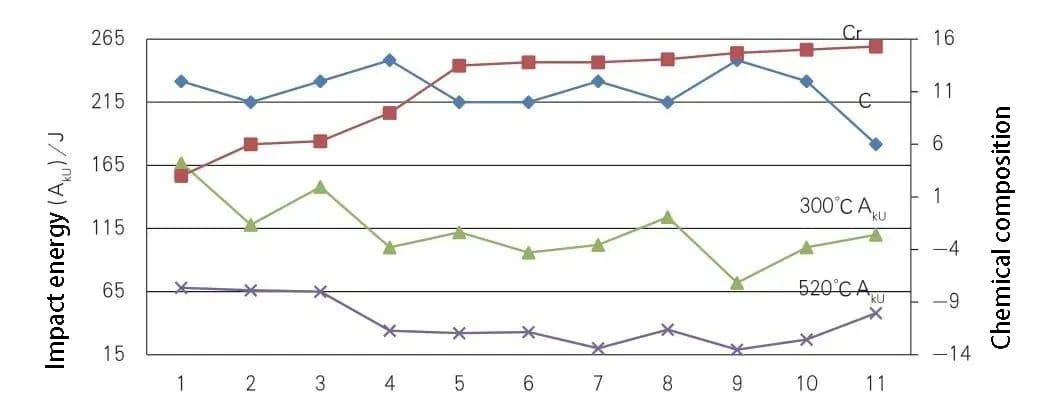
Fig. 5 Impact energy of 14Cr17Ni 2 with different C and Cr contents
It is evident from Figure 5 that the impact energy of 14Cr17Ni2 generally decreases as the Cr content increases. However, when the Cr content remains constant, the impact energy decreases as the C content increases.
Conclusion
(1) The impact energy of 14Cr17Ni2 in the tempering range of 300 ℃ to 680 ℃ tends to decrease first and then increase. The lowest point of impact energy occurs at around 450 ℃, and the impact value is generally low in the range of 350 ℃ to 550 ℃, lower than 39J (GJB 2294A-2014).
This indicates that the material exhibits significant brittleness upon tempering and that the tempering temperature has a significant impact on its impact energy. The temperature range of 350℃ to 550℃ is considered the temper brittle temperature range for the material.
(2) The fluctuation of the chemical composition of raw materials greatly affects the impact energy of 14Cr17Ni2. As the content of elements C and Cr increases, the impact energy of the material shows a general decreasing trend.
(3) To ensure the impact energy of 14Cr17Ni2 when tempered at 350-540 ℃, the content of C and Cr elements in the raw material must be strictly controlled.