Does the factory have an operator with extensive experience and computer proficiency to operate the automatic bending unit?
Some experts believe that the use of automated bending units should not lead to job cuts, but rather be seen as an opportunity for experienced bending workers to adopt robots over manual processes.
The transition from manual to automated bending operations may be similar to the experience of welders in sheet metal plants, who went from resisting to accepting automated welding.
There are also experts who argue that bending workers should stop relying on traditional manual methods and instead incorporate their knowledge into bending programs that guide robots or unskilled workers. Only qualified workers who are open-minded and willing to adopt new technologies can guarantee the success of an automated bending unit.
However, today's software is highly advanced and even first-line workers with limited experience can easily operate state-of-the-art bending units. Gone are the days when it took several days to teach a robot to perform simple bending operations on just 5,000 parts.
Which production tasks are best suited for the use of robots?
The suitability of using robots for bending operations depends on the specifics of the production scenario, but their scope of application is quite broad. Three specific production tasks are ideal for automation:
First, tasks that involve high volumes and repetitive operations can be time-consuming and lead to boredom and physical exertion for operators.
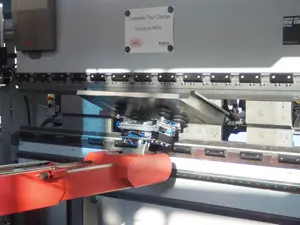
Figure 1
Secondly, small batch jobs that occur frequently as shown in the image. It's not just large batch jobs that are suitable for robotic bending; small batch recurring tasks are also suitable.
Third, tasks that require two people to lift extra-large pieces of material or that may pose a risk of injury to the operator.
In my opinion, tasks that do not exceed the robot's working radius and are within the press brake's load range are suitable for automation. The key to the automation unit is that one operator can supervise both the manual press brake and the automated unit.
It is highly beneficial for a worker to be able to perform bending tasks on both manual and automatic units. Robotic bending may require more setup time than manual bending, but the increase in productivity makes it worth the effort.
How long does it take to program?
In recent years, significant progress has been made in the field of automated bending programming technology. It is no longer necessary for automation unit programming to require in-depth robotics knowledge like engineering specialists.
With a CAD module, a programmer can send the data and the software will generate the bending order and operating instructions. While some may still require an actual bend test based on the recommendations, software developers argue that such tests may not be necessary.
The software program is now integrated with a 3D simulation module, allowing the simulation of robot and press brake movements before production instructions reach the machine. This simulation also allows detection and visual confirmation of bending order.
Additionally, the software can generate instructions (as shown in Figure 3) for clamping tool selection (as shown in Figure 2), robot movement, and final material picker.
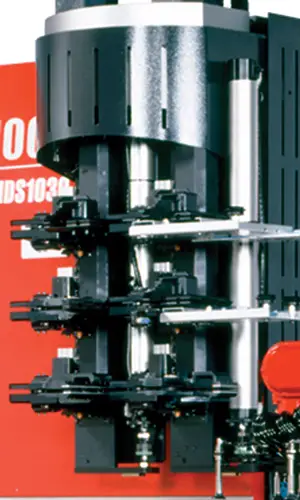
Figure 2
Due to advancements such as automatic clamping tool replacement devices, robotic press brakes can be quickly adapted to different production tasks.
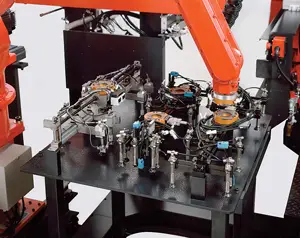
Figure 3
On a replacement bench, the robot is capable of replacing the final material picker in just 25 seconds. In many cases, programming can be done offline to ensure the automated bending unit remains uninterrupted.
What additional investment is required beyond investment in capital equipment?
You cannot discuss the topic of robotic automation without considering safety. The question at hand is whether a sheet metal factory is willing to invest in a physical fence or a more open and secure fence to ensure the safety of its workers. Two investment options are worth considering.
A security cover is the most economical option, but it takes up a significant amount of space, which can be problematic for the workshop layout. For example, the bending unit of a leading machine tool manufacturer occupies an area 12 meters long and 5 meters wide, including a feeding robot, but there is no space for a safety fence. In a cramped production workshop, it is a challenge to achieve automated production while ensuring safety.
Workers interested in safety railings should be aware that the automation unit may stop operation in unexpected situations. The problem with safety grilles is not that they should not be used, but that many people are unaware of the limits and some may accidentally trigger the safety grille light as they run their hands around the shop, thus turning off the folding unit.
However, safety fences are ideal for use in relatively open workshops and are most appropriate for companies that strictly limit access to the workshop and clearly mark the boundaries of the production area. The investment in quick-change fixture tools was mentioned earlier, and the next step in this investment should be to add an investment in the newly emerging automated mold library, as shown in Figure 4.
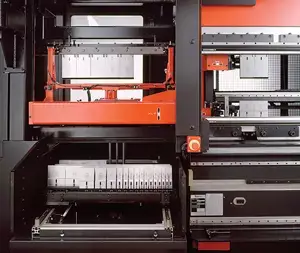
Figure 4
The latest generation of automatic bending units has a programmable mold installation and download system, eliminating the need for manual installation.
Once the program is programmed, the mold library is automatically installed and unloaded by the upper and lower die replacement device, which has a rotating disk that holds the mold and positions it for installation in one of the upper and lower fixtures.
How to determine the reasonable cost of a robot?
The main factor that affects the decision to buy a press brake is its actual working time. When an operator can handle two press brakes simultaneously, productivity improvements are evident.
However, investors should focus on using the equipment. If the automatic press brake shuts down frequently, it will not generate a return on investment despite continuous production of parts.
To improve device utilization, a company must optimize all aspects of the automation unit. In many cases, the preparation time is as long as the production and manufacturing time. An automated unit that does not have a quick-change device is ineffective.
How much faster can components be produced in the automation unit with a six-axis back gauge compared to the traditional two-axis back gauge? Improving the efficiency of a single process makes no sense if all processes are not smooth.
While it is important to consider the length of the production cycle, in many cases, shortening the cycle is not as effective as increasing the number of components produced in a shift or day.
The solution to the problem is to reduce the press brake's waiting time, so that it can operate for an extended period, significantly increasing production.