The large volume, new materials and spacious design of installed air ducts can make them susceptible to warping and cracking. This can lead to incomplete connections and air leaks, ultimately affecting the effectiveness of air conditioning systems.
To ensure the quality of production and installation of large-volume air conditioning ducts, the following aspects must be considered:
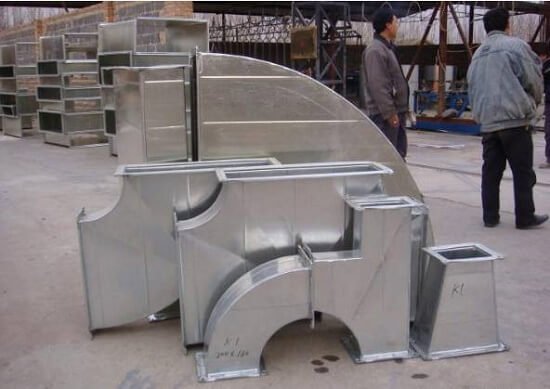
I. Application materials
The design of air conditioning ducts must meet specific requirements for optimal performance, such as flexural strength greater than 1.8 MPa, thickness of 2.6 mm for thermally insulated ducts, and thickness of 1.8 mm for uninsulated ducts.
To ensure the quality of construction materials, it is important to confirm the chosen brand with both the supervisor and the owner. Furthermore, the selected brand must have a good reputation and high performance standards.
When receiving incoming materials, strict inspections must be carried out in accordance with the material purchasing inspection procedures. This is to ensure that the materials used meet acceptable quality standards and provide reliable performance.
Ⅱ . Leaf cutting
Before cutting the sheet, align it correctly.
The basic types of lines include right angle lines, perpendicular bisectors, parallel lines, angle bisectors, right bisectors, circle bisectors, etc.
The unfolding method should employ the parallel line method, the radiation method and the triangular line method.
Depending on the geometric shapes and specifications of design drawings and large-scale drawings, the lines must be unwound separately.
Make sure the sheet is cut before cutting to avoid mistakes, and use a manual cutter to cut according to the scribe's shape.
Do not place your hands in the opening of the mechanical plate while cutting.
Do not place any tools or other items in the upper knife holder.
When adjusting the sheet, do not place your feet on the pedal.
When using fixed vibrating shears, hold the steel plate with both hands and keep them at least 5 cm away from the knife edge.
Make sure to apply even force when using the scissors.
The cutting line must be straight and the diagonal length error of the duct plate must be less than 0.5mm.
The step line must be 18-21mm deep, and the cut line must be at an angle of 90° with the surface of the plate, creating conditions for splicing the duct at an angle of 90°.
The straight section of the rectangular duct pipe must be accurate and the corner line must be straight.
The four end lines of each port of each air duct section (including tees, elbows, etc.) must be in the same vertical plane as the centerline of the pipe.
Number the cut boards so they can be easily assembled.
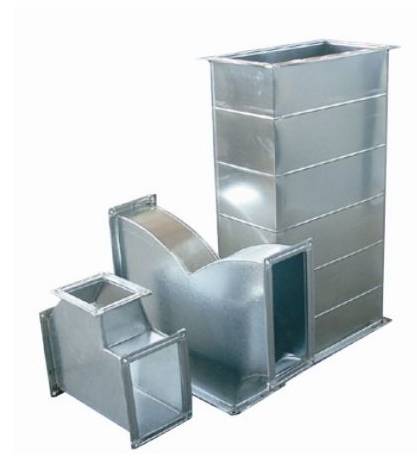
Ⅲ . Duct assembly
Based on the design requirements, the design department set up a small pipeline processing workshop on site to ensure the construction quality and facilitate the owner's site supervision and inspection.
1. Preparation of special glue
The special glue used for air duct assembly has several characteristics, including high bonding strength, non-flammability, water resistance, ease of construction and good adhesion to air duct materials.
This particular glue consists of powder and liquid components, with a 10:9 weight ratio between the two.
To ensure ideal consistency, the glue must not be too dry or too thin; It is recommended to have a slight fluidity. A mixer can be used to mix the components well.
2. Assembly process (straight tube)
2.1 Start by using a knife to cleanly cut the step-shaped thermal insulation layer from the side panel, ensuring that the position of the step is flat.
2.2 Apply special glue evenly and completely to the side panel steps. It is recommended to squeeze out a small amount of residual mud when the upper and lower plates are joined together.
2.3 To assemble the air duct, follow these steps:
- First, place the bottom panel on the group bracket.
- Second, insert the left and right panels into the edge of the bottom panel, offsetting them 100 mm from the length of the top and bottom panels. Then insert the top panel between the left and right panels.
- Third, securely tie the newly assembled air ducts with a strap. The spacing between strapping bands is generally around 600 mm.
- Protect the four corners with steel angles previously coated with release oil. The release oil is made from 1kg of saponified oil, 5kg of water and a small amount of diesel oil.
- For air ducts with a continuous straight section length exceeding 15 m, define an expansion joint to compensate for changes due to wet expansion and dry shrinkage.
2.4 Make sure that the internal angle of the four grouped air ducts is 90° and is in the correct position to avoid deformations that could affect the quality of the splice. Remove any excess glue that has been extruded and fill in the gaps.
2.5 Carefully remove the belt and remove any residual mud from the splicing seam, depending on the solidified state of the glue. If the glue sets too much, it may be difficult to remove any excess paste, and if it doesn't cure enough, the air duct may shake, affecting the strength of the seam.
To avoid these problems, it is important to remove the belt as soon as the glue reaches its initial strength and remove any residual mud, strictly controlling any air duct vibration. Generally, the air duct should be maintained at an ambient temperature of 10°C-20°C for 24 hours, above 0°C for 48 hours, and below 0°C for 72 hours to allow proper solidification.
However, during winter construction when time is short, relying solely on ambient temperature to promote solidification may not be feasible. To speed up the solidification process, we recommend using centralized stacking and heating to promote coagulation.
To do this, gather the air ducts to be spliced into one room and close all doors and windows. Install two electric heaters in the room and turn them on 24 hours a day to increase the internal temperature. Through this method, the temperature can be raised from -2°C to 11°C, reducing the solidification time of the air duct from 72 hours to 24 hours, and creating conditions to guarantee the construction period.
Production of attachments ó f the same cross section
Start by cutting the duct board to the appropriate size according to the drawing, and then cut 45-degree offset angles along the wind direction.
When folding the elbows and three heads in half, use the internal extrusion method instead of the external opening method. This means cutting a V-shaped seam on the inside of the sheet when you fold it in half.
Remove the foam from the middle and apply the appropriate proportion of glue before folding the sheet in half. In case of folding in half, it is better to squeeze out a little more glue.
Cut the side panel into the shape of a step, apply special glue to the position of the step and fix it with binding. Wipe off any remaining glue, fill any gaps, and let the assembly set on a flat spot.
Ⅳ . Duct lifting
Definition of hangers and supports for products
To ensure the stability of large-volume air ducts, the distance between bars should not exceed 2.0m.
The booms are made of 50×50×5mm angle steel, the hooks are made of Ф10 round steel, and expansion bolts are used to fix them to the load-bearing structure.
Reinforcement measures for large volume air ducts
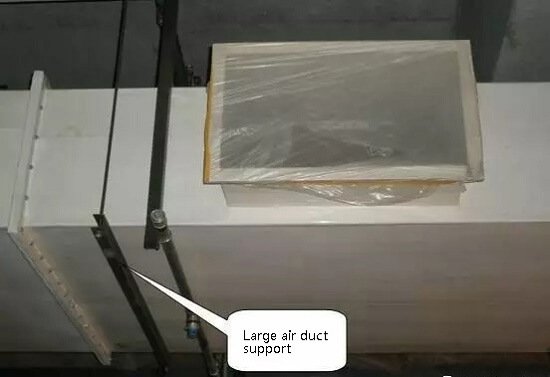
The process of producing and installing large volume air ducts now includes reinforcement to increase their resistance.
If the longest side of the air duct measures 800 mm or more but less than 1250 mm, reinforcing strips measuring 25×40 mm are attached to the four corners on the inside of the air ducts. These strips should be as long as the air ducts and applied with dense, even glue.
When the long side of the air duct is more than 1250 mm, a reinforcing rib is used. This involves connecting a support column between the top and bottom plates of the air ducts. The support column is fixed to the upper and lower plates of the air ducts by means of Ф10 screw and nuts.
To ensure stability, an 80x80x5mm silicon-magnesium plate is used as a gasket on the inside and outside of the top and bottom plates. A plastic insulation covering is then applied externally.
The distance between the ribs should not be more than 1.5m.
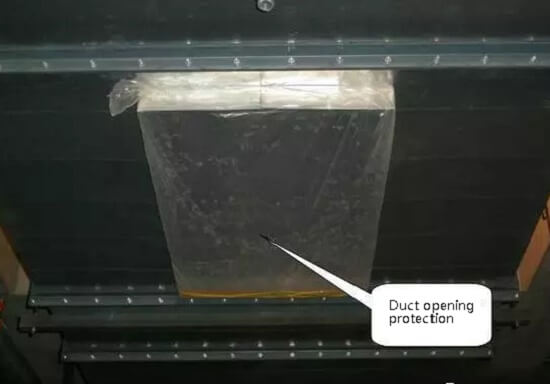
Elevation
Air ducts must not be lifted until they are fully solidified. Hoisted ducts can be connected up to a certain length in the ground and then hoisted into place. However, the length should not exceed 10m, as it may cause fracture if it is too long.
To lift the air duct, you can use a chain block or pulley. The following lifting steps must be performed:
First, select two reliable lifting points on the beam columns according to the specific site conditions, and then hang the chain block or pulley.
Then use a hemp rope to tightly tie the air duct. Typically, two ties are tied at 1/4 from both ends. It is important not to tie the rope directly to the air duct. Instead, a cushion of soft material should be provided where the hemp rope comes into contact with the corner of the duct to prevent deformation.
During lifting, it is strictly prohibited for people to stand under and on the lifted air duct. When the air duct is 200-300 mm above the ground, lifting should be stopped to carefully check the tension point of the chain block or pulley and the rope securing the air duct. Check that the buckle is secure and that the center of gravity of the air duct is correct. If everything is in order, continue hoisting.
For longer pipelines, the lifting speed must be carried out synchronously to avoid deformation of the pipeline due to excessive pressure in the intermediate pipeline.
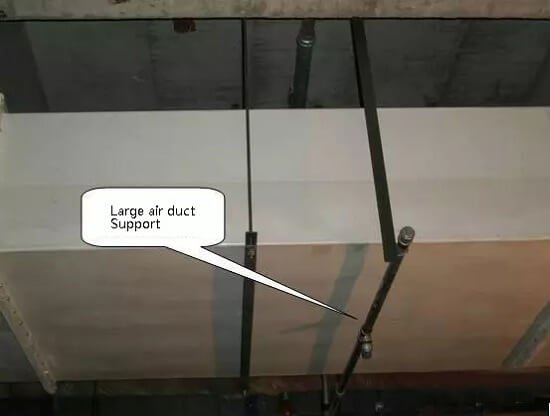
When lifting the air duct to the height of the scaffolding, the protruding part of the scaffolding must be rolled up to prevent the air duct from being punctured during lifting. This may cause damage to the protective layer, thermal insulation layer, and even air leakage.
After placing the air duct on the bracket and hanger, connect all trays and bars and make sure the air duct is stable before unlocking the rope.
Hoisted air ducts must be spliced promptly, taking care not to shake them too much during splicing. When working on the air duct, avoid stepping directly on it with your feet. Instead, use two wooden planks of approximately 1000 × 200 mm to pad the feet and alternate between them to increase the tension area and ensure safety.
After splicing, immediately clean up any remaining glue when it solidifies, check for gaps, and fill in the glue in time. Once the glue is completely solidified, inspect the duct with the supervisory unit and, after approval, attach the aluminum foil tape.
Pay attention to protecting the finished product after construction. Place a “Please pay attention to the protection of finished product” label in a visible place and regularly inspect and maintain it with workers.
1 comment
Buenos días:
Solicito información y precios para ductos de aire de 1200 mm rectangulares de 400 × 400 mm
Agradeceré si nos pueden cotizar 200 metros lineales.
Gracias