Abstract:
Non-metallic inclusions play a crucial role in determining many properties of steel and have a significant impact on the processing and use of steel products.
This article provides an overview of the latest developments in the origin and classification of non-metallic inclusions and summarizes the research work carried out in recent decades.
It highlights the dynamic conditions of inclusion formation and the effect of current casting conditions on the composition, quantity and size distribution of inclusions.
The study of inclusion denaturation focuses on steel types such as radial wire steel, spring steel, and bearing steel to achieve the desired size and shape of inclusions.
Furthermore, measures must be taken to prevent clogging of the continuous casting nozzle by flocculent flow.
With advances in electron microscopy, the distribution characteristics of inclusions are now more clearly understood. The exciting field of “oxide metallurgy” has also been addressed in the context of inclusion engineering.
Finally, the article addresses improving inclusion characteristics and the challenges of carrying out a quantitative analysis.
Over the past few decades, notable progress has been made in controlling inclusions in steel, largely due to a deeper understanding of the interplay between thermodynamics, the composition of molten steel slag, and the steelmaking process. This allows the optimization of inclusions and processes to improve the properties of the steel.
However, there are still some important challenges that need to be faced and the process of controlling and optimizing inclusion must be continually improved.
1. Introduction
It wasn't until fifty years ago that people started paying attention to the study of non-metallic inclusions (NMIs) in steel. At that time, it was believed that these inclusions were the result of corrosion of refractory materials and the presence of various mold flows and top slags.
However, despite its importance, the study of inclusions was not as widely recognized as it is today. This was because physical metallurgists generally focused on studying metallic phases rather than non-metallic phases such as inclusions in steel.
As demand for high-performance steel with severe service conditions increased, the correlation between the type, size and distribution of NMIs and steel performance became more apparent. This has led to a growing interest in studying the origin, characteristics and behavior of inclusions in the casting and processing of steel products.
Since the 1980s, significant progress has been made in the control and quantitative analysis of NMIs, and the impact of these inclusions on steel properties has been widely researched. Inclusion control engineering has become a crucial aspect of casting, with the aim of achieving desired inclusion characteristics through proper process design and steel production.
In this article, we cover the origin and control of NMIs, the behavior of inclusions during machining, the quantitative analysis and distribution characteristics of inclusions, and the latest developments in inclusion control engineering. However, we have not delved into the influence of inclusions on steel properties, as this is an extensive and rapidly growing field.
For those interested in exploring this topic further, Kiessling's classic books and the International Clean Steel Organization conferences and articles, held every 3-5 years and sponsored by the Hungarian Mining and Metallurgical Association, are valuable sources of knowledge. .
2. Origin and classification of non-metallic inclusions
2.1 Classification of non-metallic inclusions
With continuous advancements in modern steel technology, it is observed that oxidation reactions and refining methods are employed to eliminate harmful elements from steel.
These impurities, such as sulfur from coal and coke, can penetrate liquid iron and steel, but their solubility in solid steel solutions is quite limited.
During solidification, molten steel passes from the crystallization front to liquid steel, eventually forming low-melting compounds such as “FeO” and “FeS” or eutectics that contain both compounds. As a result, this steel is unsuitable for hot working processes such as rolling and forging.
The oxides, sulfides, and alloying elements (such as Mn) in steel exhibit a complex relationship. However, to produce high-quality steel, the dissolved oxygen and sulfur content of molten steel must be reduced.
Elements such as Mn, Al, Si can be used as alloying elements in steel, as they have a high affinity for oxygen and can be deoxidized in molten steel. These deoxidized elements become non-metallic oxide inclusions.
On the other hand, steel contains sulfur and the solubility of Ca and Mg in steel is minimal. Its affinity for rare earths and S is high enough to form non-metallic sulfide inclusions with low melting points.
As a result, most of the sulfur in the steel is eliminated through refining and enters the slag, while the remaining sulfur precipitates sulfide inclusions during solidification.
These non-metallic inclusions can be classified into two categories based on their type: the chemical composition of the inclusions (such as oxide and sulfide inclusions) and the stage of inclusion formation.
Solidification marks the limit point in the inclusion formation phase. Inclusions formed before solidification are known as primary inclusions, while those formed during and after solidification are called secondary inclusions.
In addition to these classifications, other commonly used categorizations can also be confusing, such as the origin of inclusions. Inclusions formed during the steel manufacturing process (such as oxide and sulfide inclusions) are classified as “endogenous” inclusions, while those originating from external sources (such as refractory chips and mold dust) are called “exogenous” inclusions.
In general, there are only a few exogenous inclusions of large particles that remain independent of the molten steel for a long period of time and do not react with it. This has changed from the past, when such large particle inclusions were believed to come from the refractory and casting mold. However, in modern steel, these large particle inclusions have been significantly reduced.
Some students may mistakenly believe that exogenous inclusions are the most important non-metallic inclusions, but this does not mean that the interaction between molten steel and refractory is insignificant. The presence of these inclusions in the steel indicates that molten and refractory steel are impacted. If the definition of exogenous inclusions is expanded to include secondary oxidation and mold dust involvement, it will provide a more appropriate definition of exogenous inclusions.
However, there is still debate over the classification of these inclusions, as they can change during the casting process and it is not always clear which process is involved.
Finally, a common method of classifying non-metallic inclusions is based on their size, dividing them into macro inclusions and micro inclusions. The classification proposed by Kiessling is often used, where inclusions that cause instantaneous damage to steel products during processing or use are considered macroinclusions.
It should be noted that the size classification of inclusions is subjective and it is difficult to randomly define inclusions into macro and micro based on size.
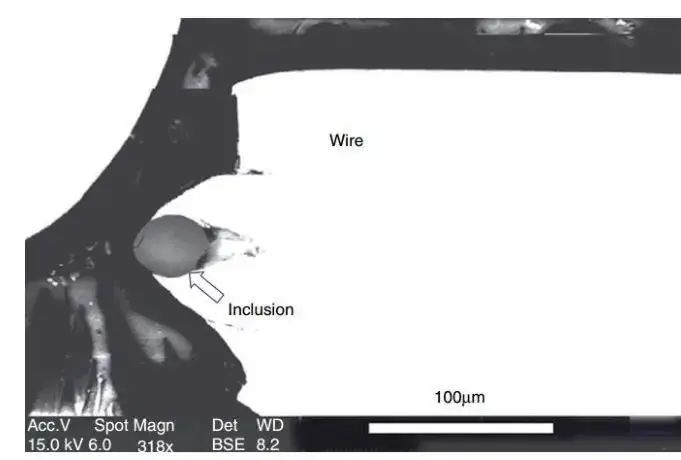
Fig. 1 Fracture of the tire's radial wire during drawing due to the existence of large particles in the hard phase.
The inclusion is indicated by an arrow, and the photo was taken using the scanning electron microscope backscatter technique.
2.2 Thermodynamic Basis
The high temperature during steel manufacturing brings the inclusion formation reaction closer to the equilibrium state. As a result, thermodynamics has become a crucial tool for understanding inclusions.
For a long time, the thermodynamic basis of inclusion formation has been a focus of research. However, thermodynamic formation data related to inclusions in aluminum oxide remain inconsistent and contradictory, making it an area worthy of further study.
Aluminum is commonly used as a deoxidizer in steel production, and the thermodynamic calculation of inclusions generated during the process is not problematic. However, the smelting process of new-generation steel materials with high aluminum and manganese content introduces uncertainty.
The situation becomes more complex when the dissolution of Mg and Ca in steel is extremely limited. Despite this, thermodynamic data related to these elements are still widely studied in the steelmaking process.
In recent decades, thermodynamic calculation has been applied to solve complex problems in the production and smelting of iron and steel. However, conventional calculation methods still struggle to resolve these issues.
Many literatures have discussed the application of thermodynamic calculation in various aspects of iron and steel production and smelting, as well as related inclusion problems.
3. Formation, removal and control of inclusions
Classifying inclusions into primary and secondary can be useful in discussing their formation and removal. In principle, it is possible to eliminate primary inclusions in steel.
However, secondary inclusions form during solidification and cannot be removed. The best thing that can be done is to modify them to minimize their negative impact on the steel.
3.1 Primary inclusions
3.1.1 Nucleation and structure of inclusions
Starting from the perspective that the primary inclusions formed in liquid steel are closely linked to the thermodynamic process, two fundamental aspects are taken into consideration: their nucleation and the structures that result from it.
In general, when a deoxidizer is added to molten steel, it will nucleate quickly. This is because high supersaturation is observed during the addition and dissolution of the deoxidizer. Sigworth and Elliott conducted a thorough evaluation of silicon nucleation conditions and found that supersaturated dissolved oxygen is a requirement.
However, Miyashita's research and industrial observations have not demonstrated clear supersaturation during silicon deoxidation in steel production. Miyashita also compared dissolved oxygen and total oxygen and found that the rate of reduction of total oxygen is determined by the rate of removal of deoxidized products, as illustrated in Figure 2.
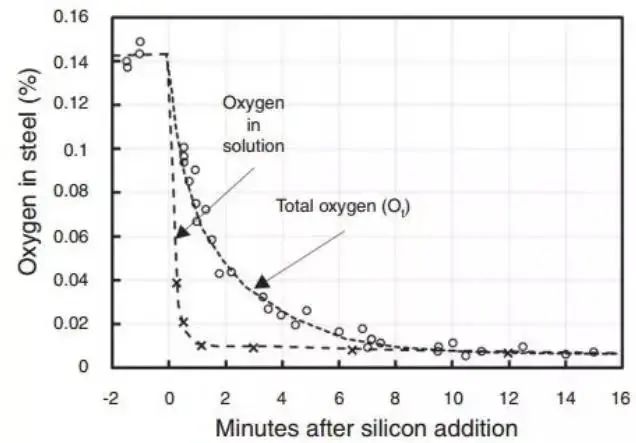
Fig. 2 Total oxygen and dissolved oxygen in steel after deoxidation of silicon in the molten bath are measured as a function of time.
In many studies on deoxidation, the difference between the total oxygen content and the dissolved oxygen content in steel depends on the amount of oxide inclusions generated. This key finding is demonstrated in Figure 3.
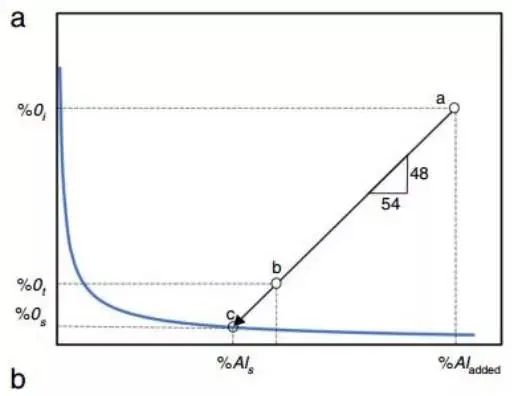
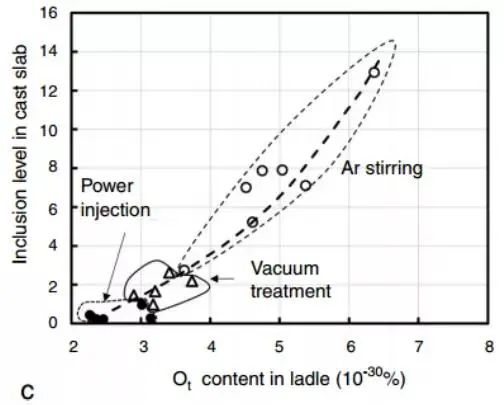
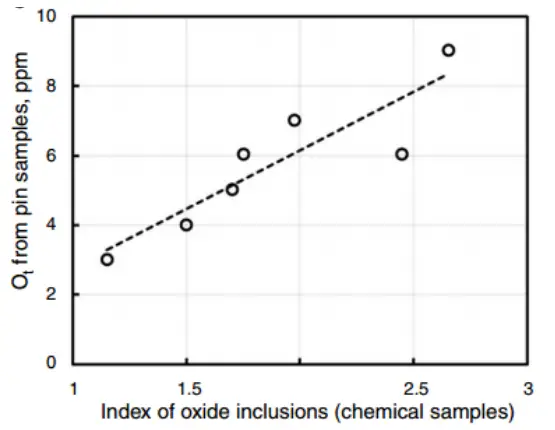
Figure 3
This is a basic illustration of how total oxygen and dissolved oxygen in steel are affected by the amount of oxide inclusions.
In the example, deoxidation begins at point “a” and aluminum is added to the steel, starting with a certain percentage of dissolved oxygen, O i .
Without nucleation conditions at the nucleation limit, aluminum oxide forms at the point where dissolved oxygen and aluminum content reach point “c”.
The total aluminum content in steel corresponds to the dissolved oxygen (O%) in steel. The oxygen that enters the aluminum oxide inclusion remains in the molten steel and corresponds to point “b”.
The deoxidation process from point “a” to point “c” reacts 2Al+3O=Al 2 Ó 3 according to the chemical equation.
Note: Generally, the difference between complete aluminum and acid-soluble aluminum (%Al is ) is small and difficult to measure.
The relationship between the inclusion content and the total oxygen content (%Ot) in steel is established through the literature. Low inclusion and total oxygen content require careful measurement, as illustrated in Fig.
Total oxygen analysis involves determining the density of the oxide inclusions in the chemical analysis sample and counting them using SEM (Scanning Electron Microscopy).
Suitu and colleagues studied the formation of alumina inclusions in a laboratory investigation of supersaturated oxygen.
The use of Si (silicon) as a deoxidizer presents no problems in steelmaking. However, in real foundry operations, heterogeneous nucleation is abundant and conditions observed in the laboratory cannot be replicated in industrial production sites.
The microstructure of aluminum oxide as an inclusion nucleus and its growth in steel is important to study. This is why aluminum silenced steel is crucial for large-scale industrial production.
Several authors have investigated in detail the microstructure of aluminum oxide, its relationship with supersaturated oxygen in steel, and the impact of casting time.
Figure 4, presented by Steinmetz and his collaborators, shows the form of inclusion corresponding to typical deoxidizing and oxygen activity. The figure suggests that supersaturated dissolved oxygen plays a crucial role in the morphology of the inclusion structure.
Recently, Tiekink and co-workers attempted to observe the functional relationship between the aluminum oxide inclusion structure, supersaturated oxygen, and aluminum composition, as shown in Fig. 5. This effort is quite complicated.
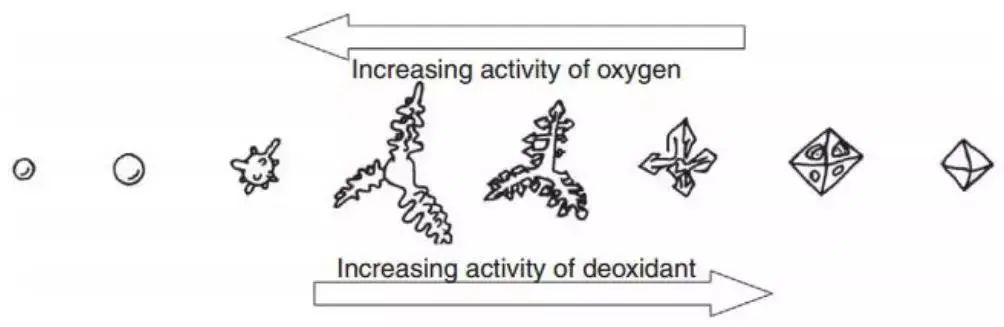
Fig. 4 Functional relationship between regional oxygen activity, aluminum activity and oxide growth
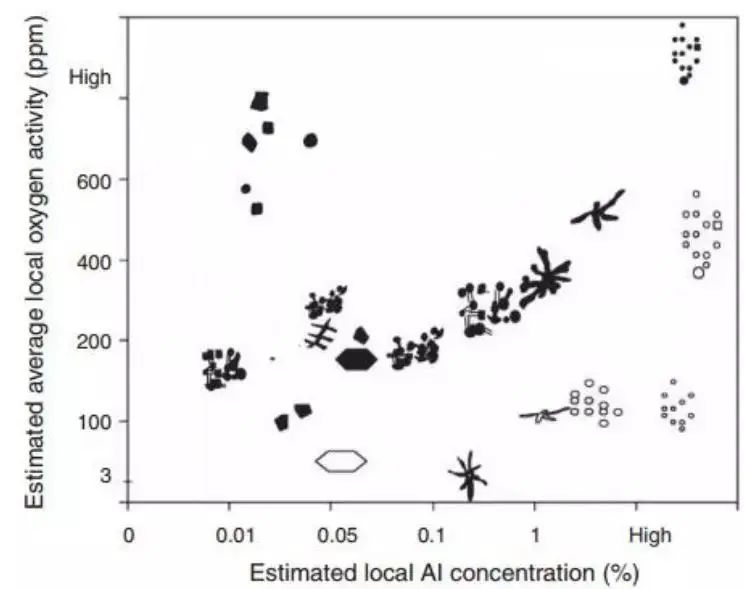
Fig. 5 Overview of the morphology of alumina inclusions corresponding to different oxygen activities and Al content in steel
The structure of the oxide inclusions has an important impact on the properties of the final product. It is important to note that the inclusions formed and grown in the early stages of liquid steel have distinct morphological structures, as shown in Figures 4 and 6, due to the effect of the inclusions on each other (as illustrated in Figure 7). If the refining time is prolonged, the shape of the inclusion will change as a result of surface energy.
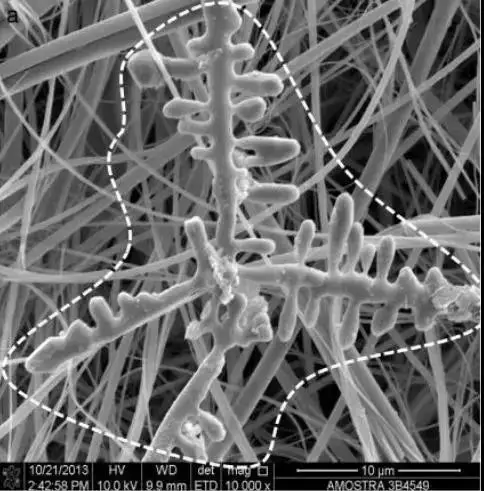
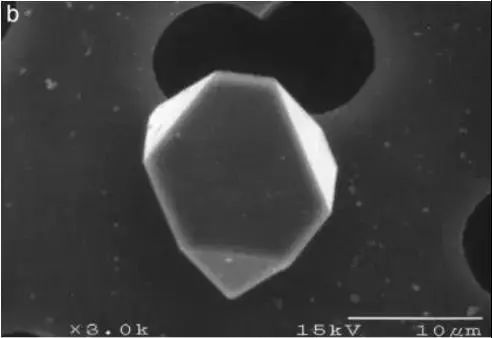
Fig. 6 Structure of some alumina inclusions.
Inclusions extracted from the molten billet matrix are dissolved. The structure of the aluminum oxide tree is represented by the dotted line a. A fibrous filter element is used to retain inclusions during the dissolution process and acts as a backdrop for the inclusions.
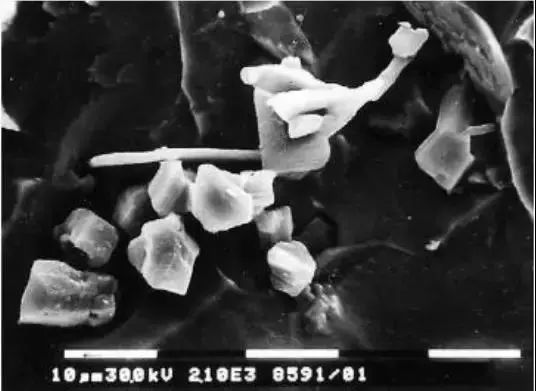
Fig. 7 Alumina cluster sampled in shell, deeply etched with picric acid
3.1.2 Removal of inclusions
The flotation of non-metallic inclusions in a static bath of molten steel can be calculated using a simple method based on the limitations of Stokes' law. At normal ladle depths, the buoyancy rate for small particle inclusions is restricted and it takes considerable time for them to reach the surface of the steel slag. This prolonged float time is not feasible, especially for aluminum oxide inclusions. However, impact polymerization between inclusions helps them float, making their cluster polymerization critical.
The importance of this bottom-up aggregation has been noted online by Emi and her colleagues. They observed the behavior of inclusions at the interface between steel and gas and discovered that aluminum oxide agglomeration occurs quickly under these conditions. On the other hand, calcium aluminate inclusions are difficult to aggregate and complete collision occurs only in the liquid.
Wikstrom and his collaborators expanded the online observation of the steel slag surface and inclusions in the slag and confirmed Emi's findings at the steel slag interface. Emi and his colleagues also noted that when the phenomenon occurs at the gas-steel interface, such as at the surface of bubbles, it does not directly indicate how liquid steel assembles into clusters, which is particularly significant for liquid inclusions. Other forces may be relevant in this case.
Regardless of whether the inclusion is solid or liquid, it plays a crucial role in cluster polymerization. For a long time it was believed that agitation promoted the agglomeration of inclusions, but the most important factor for inclusions is submerging them in the refining slag and refractory on the ladle wall. Lindskog and his collaborators used radioactive tracer to test and track this crucial inclusion in the refining slag and ladle wall.
Due to current limitations, BaO is the only suitable tracer that can be used to evaluate final captured refining slag and mold flow in steel and its impact on steel cleanliness. The use of BaO tracers is highly effective in determining the effect of ladle refractory corrosion on the cleanliness of thermal number steel.
IRSID developed the use of the element lanthanum as a marker for oxide inclusions. La 2 Ó 3 is very stable and when added to steel, existing alumina inclusions can be identified by lanthanum. Exogenous inclusions, originating from mold flow, can be traced using alkaline oxides. Mold flux is typically only used in the continuous casting process and contains noticeable alkaline oxides.
The majority of inclusions removed during the ladle refining period are deoxidized products and pass through three stages: production/clustering of separate inclusions, movement toward the refining slag or refractory ladle wall, and absorption by the refining slag and refractory. The movement of inclusions has two crucial factors: the agitation of the weld pool and the movement of upward bubbles.
Most ladle refining results show that the size of argon stirring bubbles in the ladle is too large to effectively remove inclusions and reduce them in the steel unless a large amount of argon is used. However, Zhang and Taniguchi's calculations indicate that argon stirring is effective when the molten steel flow velocity is high and the bubbles are small.
The SEN submerged nozzle and the long continuous casting ladle nozzle have a remarkable effect on preventing secondary oxidation, and some advantages have also been observed in the RH vacuum treatment riser steel flow. Agitation of the ladle promotes inclusion to float on the slag in clumps. Research has shown that increasing stirring power (using electromagnetic stirring) means increasing the kinetic energy constant to remove the inclusion (measured by the total oxygen content in the steel).
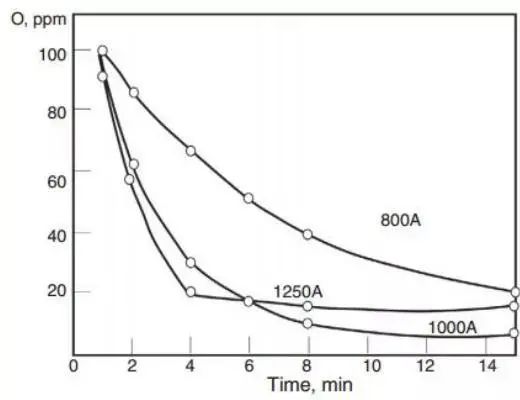
Fig. 8 Total oxygen content in the ASEA-SKF ladle refining furnace is a function of stirring current and processing time.
The final oxygen content is determined by the residual aluminum content in each furnace.
Industrial observations suggest that inclusion removal will reach its maximum value at a specific mixing energy.
Suzuki and his team were the first to report this observation.
Their findings are presented in terms of the specific work of energy mixing, highlighting the importance of energy mixing. The reduction in the effectiveness of refining to remove inclusions is probably due to the addition of refractory to the steel after corrosion, or to the surrounding of the steel with slag as CaO and MgO type inclusions increase under strong agitation. These results are illustrated in Figure 9.
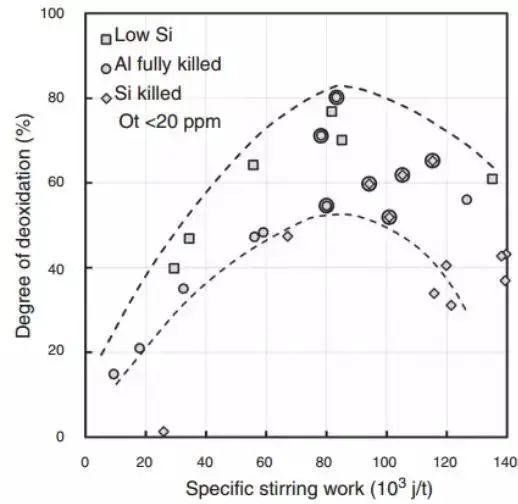
Fig. 9 The influence of mixing power on the degree of secondary oxidation. Circle point reached below 20 ppm total oxygen content
Later, Neifer and his team, along with Ek and his team, used computational fluid dynamics and physical models to investigate the removal of oxide inclusions. The relationship between the argon flow rate in the ladle and inclusion removal was treated as a functional relationship.
The results of the Neifer model indicated that the removal efficiency of metallic inclusions was improved through optimization of the gas flow. However, they observed that increasing the gas flow rate had no effect on reducing the total oxygen content in the steel, which they attributed to secondary oxidation of the molten steel in contact with the atmosphere. These conclusions are in line with the Suzuki team's findings.
The Ek team found that the influence of argon flow rate on removing inclusions was quite low and suggested using a lower flow rate to remove inclusions and clean the molten steel. However, the Neifer team's industrial measurements indicated that the total oxygen content in the steel decreased with increasing gas flow. They recommended using natural convection transport in industrial experiments to obtain optimal results. However, due to limited measurement data in industrial field ladle tests, it is challenging to draw definitive conclusions.
Recently, Zhang and Thomas collected many kinetic constants for use in the functional relationship between oxide inclusion removal and stirring power, as shown in Figure 10. They gathered measurement data and tried to determine the optimal mixing scheme. They also performed numerical simulations to reproduce the expected behavior data of the surrounding part in Figure 10.
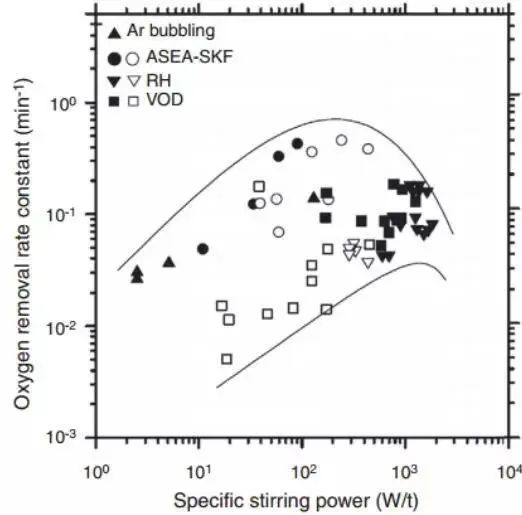
Fig. 10 The oxygen removal constant is a function of the stirring power in different secondary metallurgical reaction vessels in the formula d% Ot/dt=- kt
The Suzuki team highlighted that optimizing the mixing process could result in secondary oxidation. Excessive mixing can lead to slag opening at the top of the ladle, exposing the molten steel to the atmosphere and causing slag coating on the edge of the opening.
Figure 11 illustrates the change in the chemical composition of non-metallic inclusions during the desulfurization process with strong agitation. The presence of Ca and Mg in the inclusions confirms that the slag was emulsified.
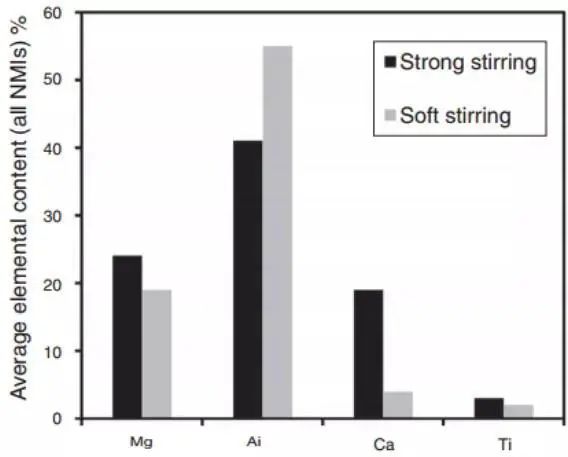
Fig. 11 The relationship between the average composition of all non-metallic inclusions and the stirring intensity was analyzed by sampling the refining furnace, crystallizer and plate.
Kaushik's team found that strong agitation increases slag emulsification during desulfurization. The proof was in the high calcium content in the inclusions. In case of excessive argon agitation and low slag, aluminum oxide inclusions are regenerated. Therefore, it is crucial to optimize stirring power to eliminate inclusions when refining clean molten steel.
The importance of secondary oxidation for cleaning steel cannot be overstated. Nadif's team reported the importance of controlling secondary oxidation. Steelmakers have taken several steps in recent decades to regulate secondary oxidation after refining.
SEN submerged nozzle and ladle nozzle are commonly used to isolate the atmosphere in continuous slab casting. In the production of long products, the distributor and crystallizer are protected by inert gas, which has become the norm for the production of high-quality steels.
Special attention must be paid to the design of the inert gas valve to prevent air ingress caused by negative pressure in the valve system. The surface tension contribution of inclusions bound to the refining slag is the highest, followed by the ability of the slag to dissolve inclusions.
Regardless of the composition of the slag, most refining slag and inclusions are wet due to the difference in surface energy between the inclusions and molten steel, and the inclusions and refining slag. This phenomenon has been discussed for many years and summarized by Olette. The liquid fraction in refining slag promotes the removal of non-metallic inclusions, which was known in ancient literature and confirmed by experiments.
However, there are still some inconsistencies in the viscosity of the slag. Nakajima and Okamura proposed a model to explain the process of inclusions passing through the steel-slag interface. Subsequently, many studies have further discussed the topic of inclusion absorption by scum. Nakajima and Okamura suggested that under certain conditions, inclusions enter the steel slag, which may include an interfacial metallic film as a channel, while in other cases, especially with solid inclusions, no such metallic film exists, as shown in Fig. .
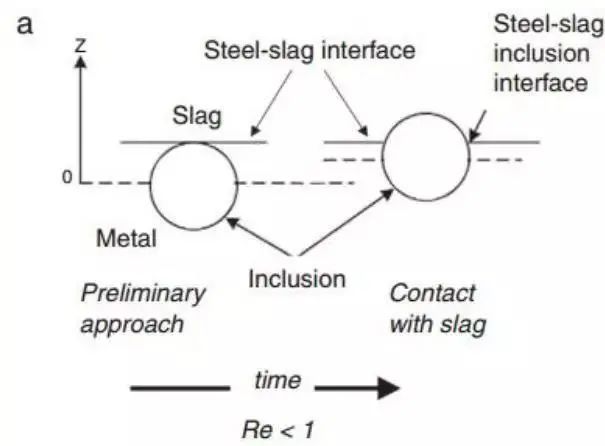
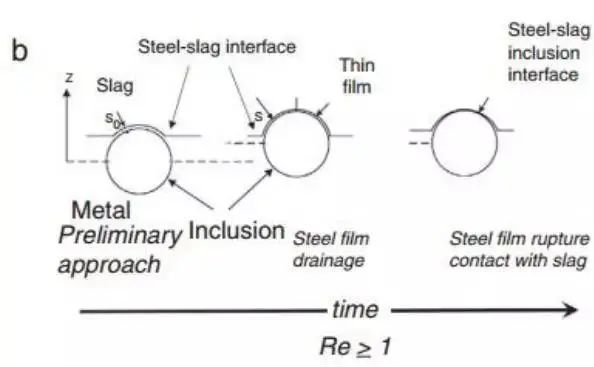
Figure 12 shows two types of inclusions crossing the steel slag interface, introduced from Nakajima. The Reynolds number of inclusions that reach the interface determines their behavior
The conclusion of Sridhar's team is that the viscosity of the slag and the associated surface energy are crucial factors in determining the passage of inclusions across the interface and reducing the likelihood of them returning to the molten steel. This is summarized by the Reynolds number when the inclusion is close to the interface.
Recently, the team observed the streaming channel of this film online, which is a common occurrence. In most cases, the path to inclusion in the slag is extended. Upon exiting the molten steel, the liquid inclusion is immediately dissolved into the slag.
By observing online, the thermodynamics of solid inclusion dissolution can be studied experimentally. In some cases, dissolution is controlled by transport (diffusion in the boundary layer), while in others, such as the inclusion of MgO, the formation of the intermediate layer depends on the chemical composition of the slag and can make dissolution difficult in several chemical stages of refining. This was confirmed by results obtained from previous common technical methods.
Recently, the Yan team estimated the dissolution of MgO in slag and found that all data was controlled by quality transmission.
The Holappa team studied the activity of the distributor's coating agent, which is crucial in absorbing inclusions. They observed a complex interplay between the chemical composition, thermodynamic conditions, surface tension and viscosity of the slag when non-metallic solid inclusions are dissolved. The team concluded that more systematic research is needed to gain a deeper understanding of this field and develop optimization methods.
It is good if non-metallic inclusions are adsorbed on the refractory surface of the ladle, but these inclusions can also become a source of inclusions in the next furnace, depending on the composition of the ladle slag.
If inclusions are adsorbed in the molten steel pipeline channel, it may cause significant problems such as long treatment time and high cost due to nozzle blockage in the continuous casting process. This nozzle clogging phenomenon is well described in the references.
It is noted that the flocculent flow in the nozzle is caused by the adhesion and accumulation of aluminum oxide and FeO inclusions, which can form in secondary oxidation. This phenomenon is clearly described in the references.
There is a vast literature on the absorption of primary inclusions by mold powder during continuous casting and ingot casting. The consensus among these sources is that this phenomenon is indeed possible.
The mold flux used in continuous casting and die casting (which is similar to the distributor's covering agent) must have multiple functions and have fluidity. However, it is subject to several restrictions within the mold, such as avoiding the inclusion of mold flow on the surface of the primary green shell. This, to some extent, restricts the movement of inclusions and keeps them within the mold flow. At the same time, it optimizes the flow of molten steel in the distributor and mold, allowing the molten steel to reach the slag interface with inclusions. However, this creates conflicting objectives with other relevant metallurgical goals.
The best way to remove inclusions caused by convection is through ladle refining, and it is also crucial to prevent secondary oxidation from creating new inclusions, which is a crucial aspect of producing clean steel.
Another issue is the movement of primary inclusions in the continuous casting slab. It has been widely recognized that inclusions are distributed asymmetrically in the cross section due to the continuous arc casting process. This asymmetry is often related to clogging of the flake flow in the nozzle.
Sichen recently demonstrated the impact of the secondary refining model, particularly the refining furnace process. The model seeks to explain the interface reaction of steel slag, the opening of the slag transition layer, the generation, nucleation, growth, separation and removal of inclusions by flotation, using most available technologies.
However, Sichen highlighted that the key variables in the ladle refining process, such as mass transfer efficiency, fluctuating inclusion removal rate, slag layer opening with excessive agitation, and argon flow rate, are difficult to determine. simulate due to uncertainties in the industry. production, such as the ladle ventilation plug and gas pipeline leak.
It is challenging to control and detect the speed of argon flow in industrial refining. Camera and image analyzer technology can be used to monitor the opening of the ladle slag layer, while vibration measurement can be used to control the flow of argon. These technologies have already been adopted by some steel companies.
3.2 Secondary inclusions
During solidification, the driving force of secondary inclusion precipitation increases the segregation of solute elements, and the solubility of oxides and sulfides in steel decreases as the temperature drops.
The phenomenon of inclusion precipitation due to changes in steel solubility has been a topic of discussion for some time.
Since the 1960s, the terms “primary inclusions” and “secondary inclusions” have been established and the relationship between inclusion segregation and precipitation has been defined.
At that time, the first model explaining this process was introduced.
Turkdogan and Flemings have made a significant contribution to our understanding of the general impact of solubility changes with decreasing temperature on secondary inclusion segregation.
During the 1980s and 1990s, Nippon Steel and IRSID developed advanced models, which were subsequently applied to nitride precipitation in HSLA microalloyed steel during solidification.
These models paved the way for the study of inclusion engineering.
Today we know that by combining a thermodynamic database and a kinetic database we can simulate solidification and calculate the formation of inclusions.
These calculations begin with the desired chemical composition of the steel, predict the precipitation of inclusions, and guide the design of the refining slag composition during ladle refining to produce clean steel.
The interaction between liquid steel, dendrites and inclusions formed at the solidification front is an important area of study.
In-line observations indicate that solidification conditions play a crucial role in the formation of inclusions that are pushed into the liquid phase at the interface and engulfed by the inclusions.
In theory, these results can be calculated and adjusted to take into account the effects of surface tension and density.
The focus of theoretical research is mainly on the composition of metallic matrices, and findings regarding non-metallic inclusions in steel are also more in line with actual conditions.
The results indicate that the critical growth rate (V) can be represented as V = k/R, where R is the radius of engulfment and repulsion of the inclusion interface, and k depends on the type of inclusion.
The structure of secondary inclusions is significantly impacted by the reactions that occur during precipitation, with carbide precipitation being one of the best examples.
Since Sims first observed the impact of reoxidation on sulfide structure in 1930, he later proposed three distinct types of sulfides, which have been thoroughly described by several authors.
Recently, Ishida's team highlighted that, in addition to the type of reaction that accompanies sulfide formation, surface tension also plays a crucial role in the formation of the sulfide structure.
4. Inclusion denaturation treatment
Gaye's team presented the most comprehensive and insightful explanation of the thermodynamic application of inclusion engineering to steel.
Figure 13 provides a concise illustration in two adiabatic ternary phase diagrams.
Once the necessary inclusions have been identified, the chemical composition of the steel that will produce these inclusions can be determined.
The composition of the refining slag used for refining can then be calculated based on the chemical composition of the steel through a steel slag balance.
The saying “Steel can only be made after smelting slag” is well founded and has been successfully applied in the production of various types of steel.
In steel production, it is important to avoid inclusions composed of hard phase aluminum oxide (such as spinel).
For example, in the production of bearing steel, the inclusion acts as a nucleation nucleus during the phase transformation that occurs during cooling.
Calcium treatment transforms the inclusions into liquid inclusions and, together with calcium, modifies the sulfides to prevent clogging of the nozzles.
Although the process of modifying the inclusion may seem simple, it is also a topic of discussion in this chapter.
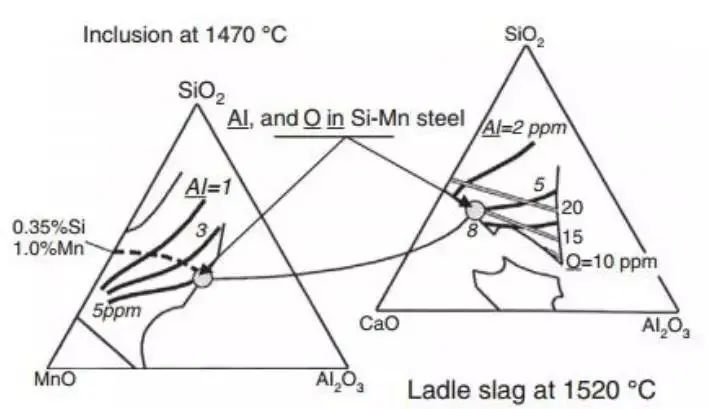
Figure 13 shows the transformation process of inclusions. From a thermodynamic point of view, low melting point Al 2 Ó 3 inclusions are expected to be obtained in steel quenched with Si Mn.
The expected inclusions are shown in the simplified phase diagram of MnO-SiO 2 -Al 2 Ó 3 ternary system.
The diagram on the left shows the system at the 1470 ℃ isotherm. The region is indicated as a 100% liquid phase, confined to the thin line, as illustrated in the figure.
The thick solid isopleth at the specified temperature represents the aluminum content in molten steel with liquid inclusions at equilibrium. The dotted line, on the other hand, indicates the chemical composition of the inclusions in the steel 0.35% Si, 1% Mn at a given temperature, varying with the aluminum content of the steel type.
According to the diagram, if you want to have liquid inclusions, the aluminum content of the steel must not exceed the gray circle (8ppm).
The figure on the right shows the simplified ladle refining slag of the CaO-SiO 2 -Al 2 Ó 3 system.
The 1520℃ isotherm represents the conditions in the refining ladle furnace and shows that the 100% liquid inclusion region is confined to the thin solid line.
At the chosen temperature, the thick line represents the aluminum content of the steel at equilibrium within the slag system. The gray line displays the corresponding oxygen content in the steel under examination.
If liquid inclusions are desired (on the left side of the diagram), the composition of the refining slag should be chosen as indicated in the diagram to ensure that the aluminum content in the steel is less than 8 ppm.
4.1 Wire and steel spring of radial tire
The tire's radial steel wire is made of high-carbon steel that is deoxidized with silicon-manganese.
Similar methods are also used in the manufacture of many automotive spring steels.
Non-metallic brittle inclusions, typically aluminum oxide inclusions or high aluminum oxide inclusions, have a significant impact on both the drawing performance of the steel wire and the quality of the spring steel.
To prevent the formation of aluminum oxide or aluminum oxide-rich inclusions, the composition of the steel must be adjusted. This involves strict control of the aluminum oxide content in the slag, monitoring of raw materials and auxiliary materials to prevent aluminum from entering the steel, and the use of a low alkalinity binary slag system.
This solution was initially contradictory to the refining operations prevailing at the time.
There are numerous excellent examples and articles that address the thermodynamics of controlling the inclusion treatment of radial tires and spring steels.
4.2 Bearing steel
The impact of a single inclusion type on the fatigue life of bearing steel remains a subject of debate. However, it is widely accepted that the size and quantity of inclusions in steel significantly affect the fatigue life of bearing steel.
It is well known that calcium aluminate and spinel inclusions negatively impact the performance of bearing steel.
As a result, some believe that bearing steel production should aim to achieve a very low total oxygen content and a very low sulfur and aluminum content, to keep non-metallic inclusions to a minimum.
Furthermore, the introduction of magnesium from slag can lead to the formation of spinel inclusions, which should be avoided.
To produce high-quality bearing steel, various steel mills adopt different process methods based on their specific conditions.
However, controlling the chemical composition of refining slag is always a critical factor in controlling non-metallic inclusions in bearing steel.
Figure 14 demonstrates the influence of Al, O and Ag contents in 100Cr6 (AISI52100) bearing steel on the slag composition. Comparison of calculated and measured aluminum and oxygen contents in steel is also shown.
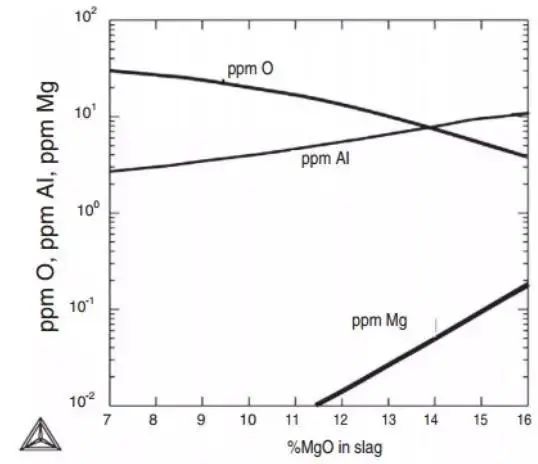
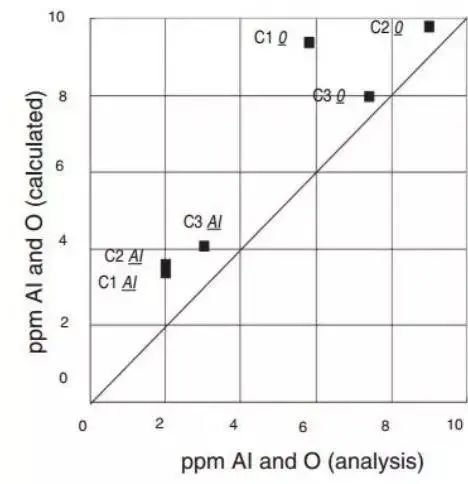
Figure 14
The. Under the equilibrium state of bearing steel, the refining slag %Al 2 Ó 3 =5%, %CaO=48% remain unchanged, and the influence of MgO on Al, O and Mg is calculated using Thermo databases calc and SLAG2 at 1540 ℃.
B. Compare the calculated value and measured value of bearing steel after finishing furnace 3 refining, and Thermo calc® and SLAG2 database is used for calculation.
4.3 Prevention of nozzle clogging by treatment with calcium and inclusion of alumina
Calcium treatment is used to eliminate sulfide inclusions and regulate the anisotropy of hot-rolled or forged materials. It also helps to improve the workability of inclusions.
The practice of using calcium treatment to transform aluminum oxide inclusions into liquid composite inclusions to prevent clogging of nozzle flakes has gained widespread use in recent decades, despite being a controversial method.
The calcium treatment process is complex, requiring consideration of factors such as calcium solubility, yield, and high vapor pressure caused by oxidation during calcium addition. These factors have been thoroughly researched.
Studies have also been carried out on the inclusion denaturation mechanism and the ideal amount of calcium required to achieve the desired result.
The formation of inclusions is a complex process. The outer layer, often composed of oxides, is covered by a sulfur-rich composite coating. This phenomenon and the distribution of individual elements are illustrated in Figure 15.
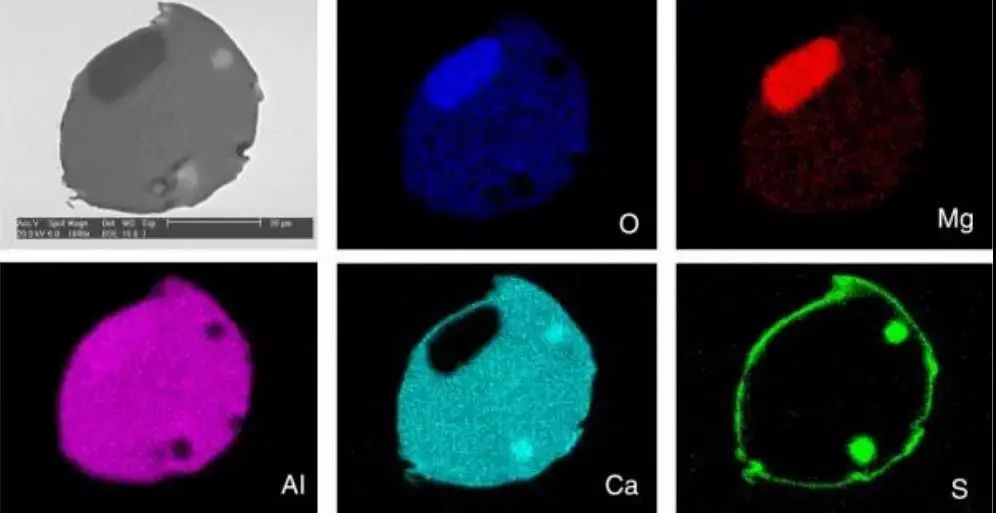
Figure 15
Calcium treatment is used to improve the castability of steel. Dissolves large inclusions of particles composed of calcium aluminate, sulfide and AgO found in the slab during continuous casting.
Magnesium is also reduced from slag to steel during the treatment process.
As a result of the treatment, a significant portion of the inclusions become a liquid phase and will not clog the nozzle during casting.
However, if the temperature of the molten steel is too low, casting will become challenging.
The reaction of non-metallic inclusions formed during solidification is a complex process, as illustrated in Figure 16.
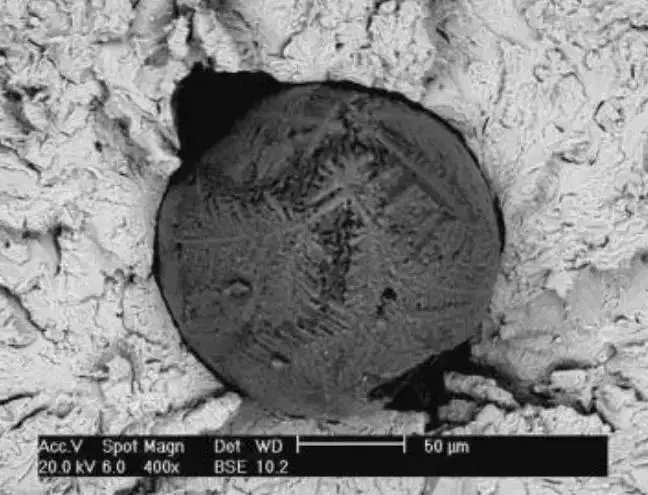
Figure 16
The plate sample contains large broken calcium aluminate inclusions with complex phases, and the inclusion shell exhibits a dendritic solidification structure.
The amount of calcium required to modify calcium oxide inclusions depends on the total oxygen content in the steel.
Unfortunately, there is no current method to accurately determine the total oxygen content of steel in real time, making it difficult to determine the appropriate amount of calcium to add.
This represents a significant challenge for industrial production.
One solution is to use thermodynamics to understand flake flow clogging in the nozzle and establish the moldable window for continuous casting.
The dissolved oxygen level can be measured, and this data can also be used to monitor the efficiency of calcium treatment, as demonstrated in Figure 17.
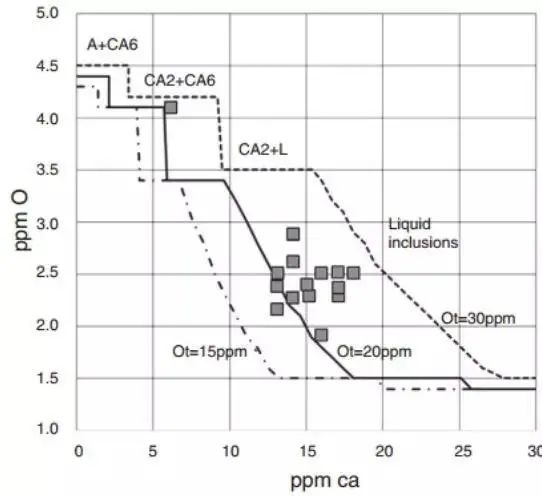
Figure 17
The figure above shows the correlation between calcium content and dissolved oxygen calculated in steel with a composition of 0.025% Al, 0.01% S and varying total oxygen contents of 20, 25 and 30 ppm from left to right, at a temperature of 1540 ℃.
The presence of non-metallic phases is indicated within each composition range.
Calculations were performed using the Thermo-Calc® and SLAG3 databases.
Each point represents the experimental measurement of the dissolved oxygen content in the steel, obtained without any blockage in the nozzle.
4.4 Oxide metallurgy
The final casting process faces a challenge that requires microstructure control and cannot rely solely on hot rolling.
Research has shown that the presence of ferrite in the weld metal positively impacts the formation of non-metallic inclusions.
Inclusion nucleation theory suggests that inclusion formation depletes Mn in the surrounding matrix, which appears to be effective.
Non-metallic oxide inclusions serve as nucleation cores for MnS inclusions and have produced favorable results in applications.
Furthermore, the secondary oxidation of titanium in silicon manganese steel transforms the inclusions into titanium oxide, while the oxide and nitride show high nucleation efficiency in ferrite, as confirmed.
Koseki, Inoue, Suito and Park proved that titanium nitride can effectively act as a nucleating agent, promoting the appearance of large equiaxed grains in stainless steel from continuous casting and welding processes.
Park and Kang have recently made advances in this field.
Thermodynamic calculations and model simulations show that alloy and process design in oxide metallurgy can be highly beneficial.
5. Quantitative analysis of inclusions
In recent decades, the steel industry has encountered the challenge of accurately classifying and quantifying non-metallic inclusions using traditional comparison graphs and images. To improve the quantitative analysis of inclusions, including information on size, volume fraction and composition, new methods have emerged.
In many cases, several methods must be employed simultaneously to obtain a comprehensive understanding of the nature and process of nonmetallic inclusions. Research has shown that certain characteristics depend on the distribution of inclusions, while others depend on other factors. For example, the fatigue performance of steel is influenced by the size of the largest inclusion.
The cleanliness of steel products varies widely, except for low-cost products. The total oxygen content of low carbon aluminum scavenged steel (LCAK) is approximately 40 ppm, while typical bearing steel has a total oxygen content of about 5 ppm. The volume fraction of oxide inclusions is significantly different, but the presence of sulfide inclusions is not mentioned.
Extreme value statistics and their application play a critical role in fatigue analysis. These methods are not widely covered in the general literature, but are included in this literature review with references provided for further reading. The method of inclusion assessment scores using extreme value statistics, proposed by Murakami in the program, has been widely used in the area of fatigue and has produced excellent results.
It is important to note that this method does not take into account the maximum inclusion size in the fatigue analysis. In fact, the volume fraction of inclusions caused by large particle inclusions can increase. This aspect of the method may not meet steelmakers' expectations, as it does not consider the inclusion of the largest particle.
6. Conclusion
The well-established saying “Producing good slag leads to producing good steel” is deeply rooted in the steel industry.
In recent decades, recognition of the impact of non-metallic inclusions on steel properties has moved the steel production process from merely preventing inclusion contamination to optimizing the composition, quantity and distribution of inclusions in steel.
This transformation impacts every aspect of the steel production process, from raw material selection (such as avoiding aluminum contamination), to the design of slag composition, to the optimization of secondary refining conditions (such as process time refining and hydrodynamic conditions) and careful control of distributor and mold operation.
It has become standard practice in the production of many types of steel to carefully control secondary oxidation in all processes.
Thermodynamics plays a critical role in researching the influence of inclusions in steel. Understanding thermodynamics, the chemical composition of steel and refining slag, and the interactions between steelmaking process conditions are now widely studied.
There has also been a significant improvement in modeling tools, allowing for a more science-based approach to controlling inclusions in steel.
These technologies have been widely adopted and continue to evolve in the field of non-metallic inclusion modification. However, there is still a need to continuously improve refining slag and fully understand the role of non-metallic inclusions in steel.
Inclusion modification and oxide metallurgy engineering are now widely used in steel mills, resulting in steel that is at least an order of magnitude cleaner than it was several decades ago. This also presented new challenges for the qualitative and quantitative analysis of non-metallic inclusions.
Quantitative analysis of all inclusions and their impact on the properties and behavior of steel is now a basic requirement, and there is ample scope for discussion and future research.
Despite the advances and insights summarized in this review, the constant challenge in the coming decades will be to continually improve various technologies and improve steel quality.