Servomotors are widely used in automated equipment, mainly for position control. Most servomotors from different brands have this capability.
The controller sends pulses to control the operation of the servo motor, with the number of pulses determining the rotation angle and the pulse frequency determining the speed (which is related to the adjustment of the electronic gear).
When the parameters of a new system don't work, start by setting the position gain to ensure the motor runs as smoothly and noiselessly as possible. The moment of inertia relationship is also critical. It can be referenced by the set number through self-learning, and then set the speed gain and speed integration time to ensure continuous, low-speed operation and controlled position accuracy.
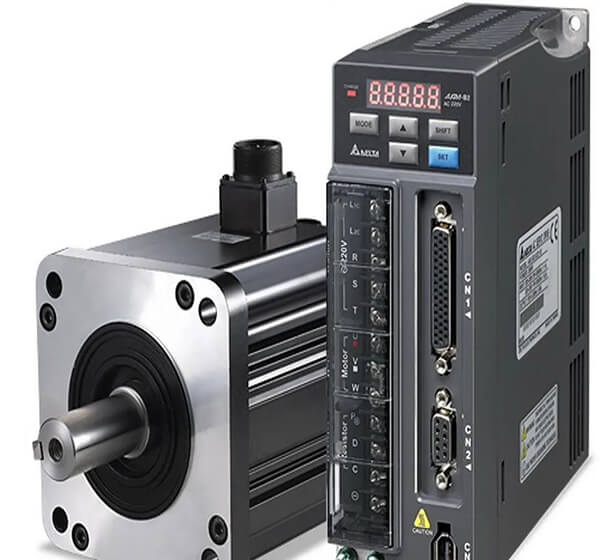
(1) Proportional position gain
Set the proportional gain of the position control regulator. The higher the gain, the higher the stiffness and the lower the position delay under the same frequency command pulse. However, setting it too high can cause flickering or overshoot. The parameter value is determined by the specific servo system model and the load.
(2) Position feedforward gain
Set the position control feedforward gain. When the set value is larger, the position delay under any frequency command pulse is shorter, the feedforward gain of the position circuit is larger, and the high-speed response characteristics of the control system are improved. However, this can cause system instability and oscillation. When high response characteristics are not required, this parameter is usually set to 0, with a range of 0 to 100%.
(3) Proportional speed gain
Set the proportional gain of the speed regulator. The gain value increases with a higher setting, making the system stiffer. The parameter value must be determined based on the specific servo drive system model and load. Generally, the greater the inertia of the load, the higher the set value. Try setting a higher value while ensuring that the system does not produce oscillation.
(4) Speed integral time constant
Set the integral time constant of the speed governor. The lower the setting value, the faster the integration speed. The parameter value is determined based on the specific model and load of the servo drive system. In general, the greater the inertia of the load, the higher the set value. As long as the system does not generate oscillation, try to set a lower value.
(5) Speed feedback filter factor
Set the characteristics of the velocity feedback low-pass filter.
The higher the value, the lower the cut-off frequency and the lower the noise generated by the motor.
If the load inertia is large, the set value can be increased accordingly.
If the value is too high, the response will be slow, which may cause oscillation.
The lower the cutoff value, the faster the response.
If a higher speed response is required, the set value can be reduced accordingly.
(6) Maximum output torque setting
Set the internal torque limit value of the servo driver.
The setting value is expressed as a percentage of the rated torque.
This limit is always in effect and defines the range of positioning completion pulses in position control mode.
This parameter provides a basis for the driver to determine whether positioning is complete in position control mode.
When the number of pulses remaining in the position deviation counter is less than or equal to the set value of this parameter, the driver considers positioning complete and the on-site switch signal is on. Otherwise, it's off.
In position control mode, the positioning completion signal is output and the set value of the acceleration and deceleration time constant determines the motor's acceleration time from 0 to 2000 RPM or the deceleration time from 2000 to 0 RPM.
The acceleration and deceleration characteristics are linear and the arrival speed range is defined. In positionless control mode, if the servo motor speed exceeds the set value, the speed arrival switch signal will be on, otherwise it will be off.
This parameter is not used in position control mode and is independent of the direction of rotation.
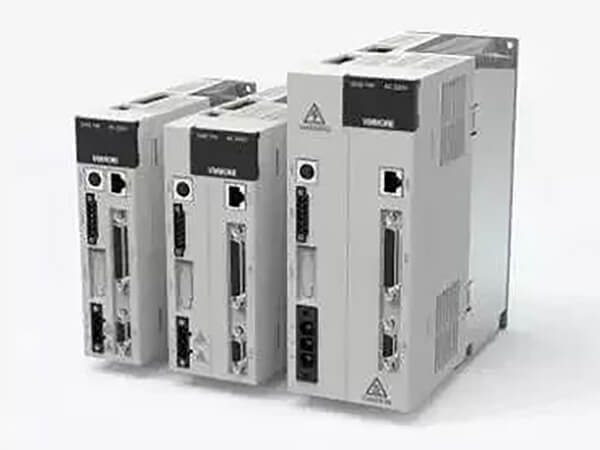
(7) Manually adjust gain parameters
Adjust the KVP value of the proportional speed gain
After installing the servo system, the parameters must be adjusted to ensure stable rotation. Start by adjusting the KVP value of the speed proportional gain. Before making any adjustments, set the integral gain KVI and differential gain KVD to zero and gradually increase the KVP value. Observe whether there is any oscillation when the servo motor stops and manually adjust the KVP parameters to see if the rotation speed is noticeably fast or slow. If the KVP value causes the problems mentioned above, reduce the KVP value to eliminate the oscillation and stabilize the rotation speed. This value will be the value of the parameter determined preliminarily. Repeat the correction process as necessary to achieve the ideal value.
Adjust the integral gain KVI value
Gradually increase the KVI value of the integral gain to produce the integral effect. As mentioned in the introduction to integral control, the KVP value and integral effect can cause oscillation and instability when they reach critical values. Similarly, reduce the KVI value to eliminate the oscillation and stabilize the rotation speed. This value will be the value of the parameter determined preliminarily.
Adjust the differential gain KVD value
The main purpose of differential gain is to smooth out speed rotation and reduce overshoot. Gradually increasing the KVD value will improve speed stability.
Adjust position proportional gain KPP value
If the KPP value is adjusted too much, the motor positioning will overshoot, causing instability. In this case, reduce the KPP value to reduce overshoot and avoid instability, but be careful not to set it too small, as this will reduce positioning efficiency.
(8) Automatically adjust gain parameters
Modern servo drivers are computerized and most of them offer an automatic gain adjustment feature, which can handle most load conditions. During parameter adjustment, you can first use the automatic parameter adjustment function and then make manual adjustments if necessary. Automatic gain adjustment also has several options. Typically, the control response is divided into different levels such as high, medium and low response, and users can configure it according to their needs.