I. The Principle and Application of Carbon Arc Gouging
1. The Basic Principle of Carbon Arc Gouging
Carbon arc gouging relies on the high temperature generated by an electric arc between a carbon rod and a metal workpiece to locally melt the metal. The compressed air flow is then used to blow away the molten metal, allowing grooves to be created in the workpiece. This process is represented in Figure 8-1.
1 – Carbon Rod
2 – Carbon arc gouging clamp
3 – Compressed Air
4 – Electric Arc
5 – Workpiece
2. Characteristics of Carbon Arc Gouging
1) Does not require large operating space, offering a high degree of flexibility and ability to work in all positions.
2) Allows a clear view of the shapes and depths of defects, thereby increasing the welder's repair approval rate.
3) Carbon arc gouging has low noise levels, high efficiency and low labor intensity, requiring simple equipment.
4) It can cut metal materials that are difficult to cut with an oxyacetylene flame.
5) Disadvantages of carbon arc gouging include substantial smoke, dust pollution, and intense arc light radiation. It also requires a high-power DC power supply, which can be expensive and requires a high level of operational skill.
3. Carbon Arc Gouging Applications
1) It is mainly used for double-sided welding of low carbon steel, low alloy steel and stainless steel materials, for root removal.
2) For important metal structures, atmospheric vessels and pressure vessels, where there are unacceptable weld defects that exceed the standard, the carbon arc gouging process can be used to remove these defects before repair.
3) Manual carbon arc gouging is commonly used to prepare chamfers for small parts, single parts or irregular welds, particularly U-shaped chamfers, which highlights the advantages of this process.
4) It is used to remove casting burrs, burrs, channel systems, risers and surface defects of castings.
5) It is used to cut high alloy steel, copper, aluminum and their alloys.
Carbon arc gouging should not be used on low alloy steel plates that are sensitive to cold cracking.
II. Equipment, tools and materials for carbon arc gouging
1. Carbon arc gouging equipment
The main equipment for carbon arc gouging includes a power source and a compressed air source.
2. Carbon arc gouging tools
1. Requirements for carbon arc gouging pliers
The carbon arc gouging pliers must meet the following three basic requirements.
(1) The carbon rod must be securely fixed and must be easy to replace.
(2) The pliers must have good electrical conductivity and accurately supply compressed air.
(3) The design should be compact and easy to operate.
2. Types of carbon arc gouging torches and their pros and cons
Disadvantage: can only glide in one direction, left or right.
Advantage of air planing clamp with circumferential air supply: The nozzle is isolated from the workpiece, with compressed air sprayed around the carbon rod, allowing uniform cooling, and is suitable for operations in all directions.
Disadvantage: It has a complex structure and the screw that secures the carbon rod can easily short circuit with the part.
The new carbon arc planing clamp with side air supply is shown in Figure 8-3.
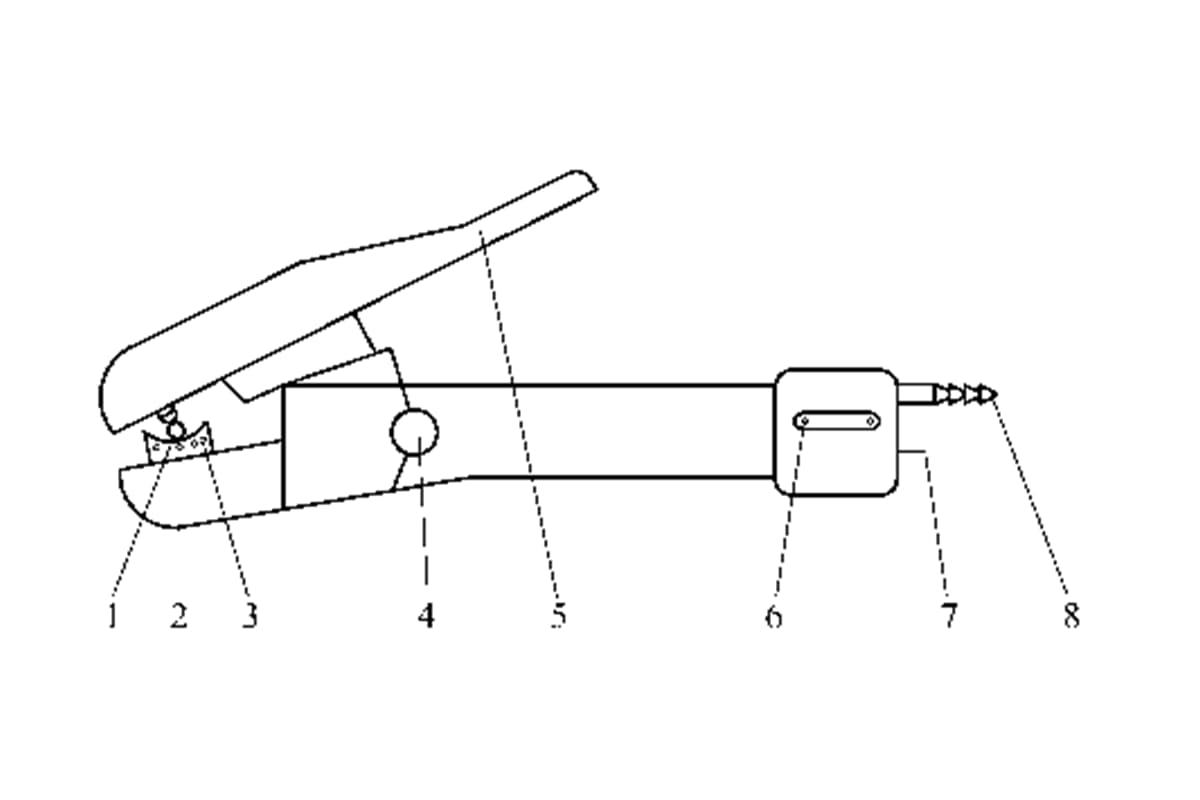
1 – Carbon Rod
2 – Air Hole
3 – Adjustable Angle Plier Mouth (Conductive Nozzle)
4 – Air Switch
5 – Fastening strap
6 – Cable fixing screw
7 – Cable Interface
8 – Compressed Air Connector
3. Combined Electric-Air Hose
The new Electric Combination Air Hose is shown in Figure 8-4.
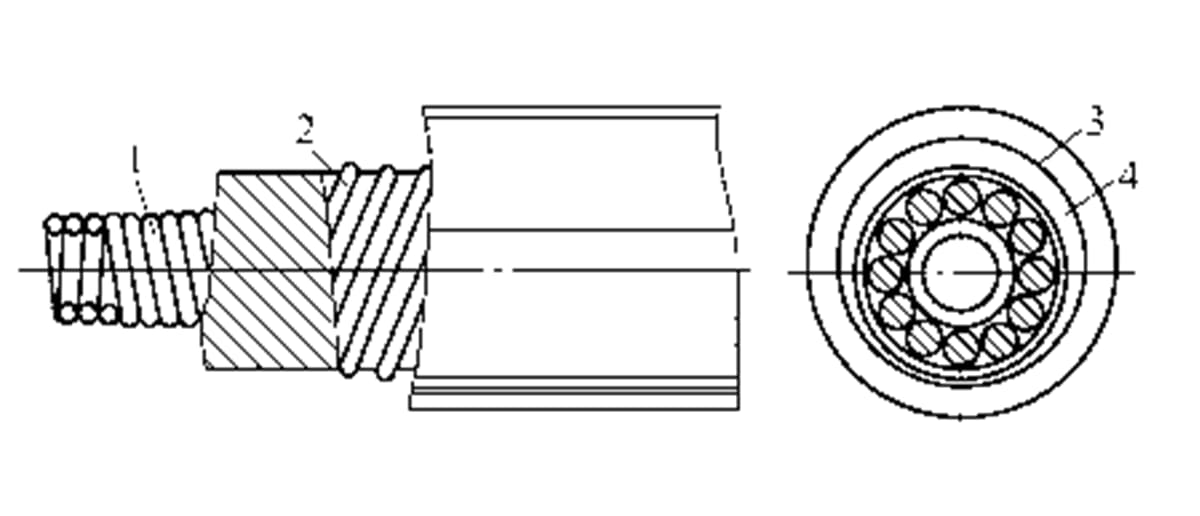
1 – Spring Tube
2 – External Additional Steel Wire
3 – Fixing Rubber Tube
4 – Multi-strand Conductor
3. Materials for carbon arc gouging
Carbon rod is the main consumable material in carbon arc gouging operations. It serves to conduct electricity and light the arc.
The most commonly used type is copper-coated solid carbon bar.
There are two shapes of carbon rods: round and flat. Round carbon rods are mainly used for cleaning welding roots on the back of weld beads or for removing defects during weld repair. Flat carbon rods, with wider gouges, can be used to bevel or cut cast iron, alloy steel and non-ferrous metals.
The requirements for carbon rods are:
1. Good electrical conductivity
2. High temperature resistance
3. The carbon rod must have a certain degree of strength.
III. Carbon Arc Gouging Process
1. Carbon Arc Gouging Process Parameters
The process parameters for carbon arc gouging include power source polarity, carbon rod diameter and current, carbon rod diameter and plate thickness, carbon rod protrusion length, carbon rod inclination angle , compressed air pressure, arc length and gouging speed.
1. Power Source Polarity
For carbon arc gouging of low carbon steel, low alloy steel and stainless steel, direct current reverse polarity is used.
2. Carbon rod diameter and current
3. Carbon rod diameter and plate thickness
The relationship between carbon bar diameter and plate thickness is shown in Table 8-3.
Relationship between carbon rod diameter and plate thickness (unit: mm)
Steel sheet thickness | Carbon Rod Diameter | Steel sheet thickness | Carbon Rod Diameter |
3 | 8-12 | 6-7 | |
4-6 | 4 | >10 | 7-10 |
6-8 | 5-6 | >15 | 10 |
Ideally, the diameter of the carbon rod should be 2 to 4 mm smaller than the required groove width.
4. Carbon Rod Extension Length
The length of the carbon rod extension refers to the distance from the conductive nozzle to the end of the carbon rod, as shown in Figure 8-6. Typical extension length ranges from 80 to 100 mm.
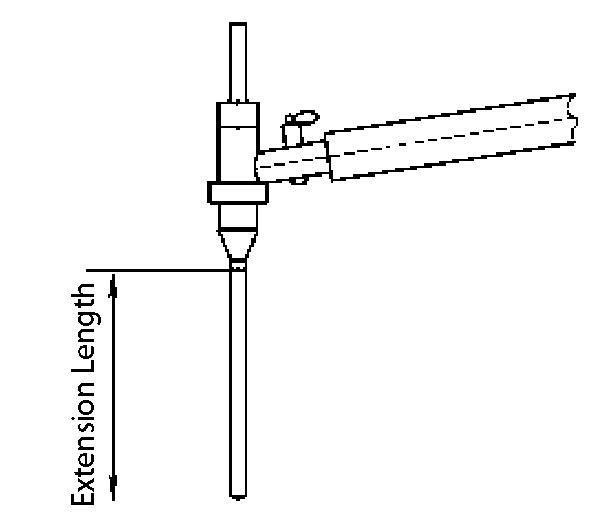
5. Carbon rod inclination angle
The angle between the carbon rod and the workpiece along the direction of carbon arc gouging is called the inclination angle of the carbon rod. Generally, manual carbon arc gouging uses a tilt angle of approximately 25° to 45°. The inclination angle of the carbon rod is illustrated in Figure 8-7.
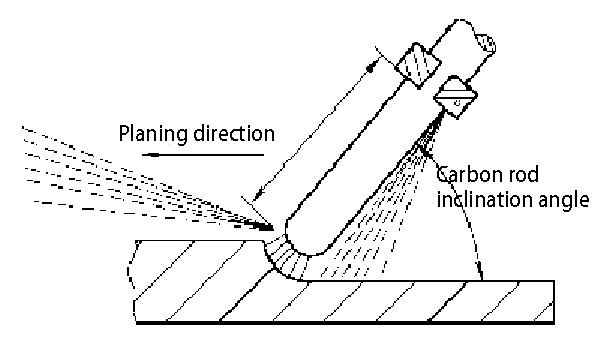
6. Compressed air pressure
The pressure required for compressed air typically ranges from 0.4 to 0.6 MPa.
7. Arc Length
During operation, it is advisable to use a short arc with a typical length of about 1 to 2 mm.
8. Planning speed
A planing speed of approximately 0.5 to 1.2 m/min is generally considered appropriate.
2. Carbon Arc Gouging Operation
1. Basic Operations
(1) Preparations before gouging
(2) Striking the bow
(3) Gouging
2. Beveling
Firstly, the width of the U-shaped groove should be chosen based on the thickness of the plate, then determine the diameter of the carbon rod and the gouging current.
Please note that the centerline of the carbon rod must coincide with the centerline of the bevel. If these two center lines do not coincide, the shape of the gouged bevel will be asymmetrical.
3. Weld root removal
Welders must select suitable process parameters according to different materials and thicknesses. It should be noted that the internal weld seam must generally be welded first to avoid the need to use carbon arc gouging to remove the internal root of the weld.
When removing the outer root of the weld, the molten metal is always blown downwards. When removing weld root on thicker plates, multiple gouging passes may be required to meet requirements.
4. Gouge welding defects
When gouging weld defects, the gouging current used should be slightly lower. During the gouging process, when the defect becomes visible, it should be lightly gouged again until all defects are completely removed.
3. Common Defects in Carbon Arc Gouging
1. Carbon Inclusion
2. Slag Inclusion
3. Copper Stains
4. Irregular size and shape of the gouge
4. Carbon Arc Gouging of Common Materials
1. Carbon Arc Gouging of Low Carbon Steel
After low carbon steel is processed with carbon arc gouging, it does not affect its weldability.
2. Carbon arc gouging of low alloy structural steel
For steel grades with yield strengths between 450 and 600 MPa and those with considerable thickness or structural rigidity, preheating is required before carbon arc gouging. The preheating temperature should be equal to or slightly higher than the preheating temperature during welding.
3. Carbon arc gouging of stainless steel
The uniqueness of carbon arc gouging on stainless steel must be noted. Avoid damaging the media contact surface with carbon arc gouging splashes. Make sure the carbon arc gouging groove is kept away from the media contact surface.
To avoid impacting the intergranular corrosion resistance of stainless steel, ultra-low carbon stainless steel, which is in contact with highly corrosive media, should not use carbon arc gouging for root removal. Instead, angle grinding should be adopted.
V. Safety Operational Techniques for Carbon Arc Gouging
1. Carbon arc excavation hazards
2. Safe operating techniques for carbon arc gouging
1) Operators must use personal protective equipment in accordance with the characteristics and requirements of the work.
2) Check that the welding machine is properly grounded; make sure the insulation at the connection points is good. Inspect that the compressed air piping joints are secure.
3) Carry out a safety check on the part being gouged. Closed tubes and containers must not be torn off. Unknown objects must be pre-inspected and confirmed as safe before operation. The workplace must be thoroughly inspected; Flammable and explosive materials are strictly prohibited within a radius of 10m to avoid fire hazards.
4) The airflow direction should not face people during operation. Outdoor work must be carried out in the direction of the wind. Operation is prohibited in rainy or snowy weather to avoid electric shock.
5) Carbon arc gouging produces considerable dust and smoke. Ventilation must be improved in the workplace. When operating inside a container, ventilation, smoke and dust removal measures must be implemented. A designated person must supervise the operation to avoid poisoning or suffocation.
6) After work is completed, the power supply must be cut off, the air compressor or air pipe switch must be closed, the work space must be cleaned, and only after making sure that there are no sources of ignition, the operator may leave the location.
7) Other safety measures are the same as general electric arc welding.