Product designers and machinists use different types of holes in manufacturing various modern products. Blind holes are often used for machining because they provide broad manufacturing benefits, including space utilization, improved product aesthetics, and strength. Standard design features are depressions of varying shapes and depths that do not lead to the opposite side of a workpiece.
This article discusses blind holes in technology and mechanical engineering, their meaning and application. You will also learn more about other types of holes in mechanical engineering and technology and receive useful tips on how to successfully machining blind holes. Let's start!
What is a blind hole in technology and mechanical engineering?
A blind hole or blind hole is a depression/hole that does not lead to the opposite end of the part material. This hole can be countersunk, milled or drilled to a certain depth without completely penetrating the material to the opposite side. Therefore, the hole is usually closed at the bottom, creating a recess for fasteners, screws, dowels, grooves and other components. The blind hole got its name because you can't see through it.
Machinists often use blind holes in metal and wood projects to ensure the fit is tight enough to accommodate and hide screws or parts, creating a unique appearance. Milling blind holes in parts also allows the production of high-quality products with complex features or shapes in industries where precision and greater strength are required.
Label symbol of a blind hole

Product engineers and machinists often use standardized symbols to communicate design requirements on the factory floor. The blind hole symbol shows the desired location, thread pitch, fastener size, diameter, and depth specification on the technical drawing. Therefore, this symbol helps machinists and product engineers understand the design intent and drill the hole accurately.
How to make blind holes step by step
To achieve accurate depth and alignment, holes in components must be carefully drilled. Below is a step-by-step guide to drilling precise and accurate blind holes.
Prepare the workpiece
First you need to firmly fix the workpiece with a vice or clamps. Make sure the workpiece is securely positioned to avoid any distractions or movement during the process. Then mark the center of the hole on the surface of the workpiece with a pointed tool or center punch. This creates a starting point for the bit and helps prevent deflection.
Choose the right drill
Since there are different types of drill bits, the size of the drill bit must match the specifications of the hole you want to drill. After selecting a suitable drill bit with the appropriate radius, insert it into the chuck and tighten it firmly. Also, make sure it is properly aligned to avoid shifting or wobbling while drilling.
Determine drilling depth
Set the drilling depth and calculate the required distance between the drill tip and the desired end of the blind hole. Create a visual guide by marking this depth with a pen or a piece of tape on the drill bit, which will serve as a depth indicator.
Start drilling and monitor drilling depth
Place the drill bit in the marked center of the center hole. Moderate and constant downward pressure should then be applied, maintaining a stable drilling speed. For easy and efficient blind hole machining, drill slowly first to make a pilot hole, then gradually increase speed as the hole gets deeper.
When drilling, stop periodically and check the depth of the hole with a depth gauge or a piece of tape attached to the drill bit.
Remove dirt
During drilling, chips may form in the hole because drilling produces chips. Therefore, it is important to remove the drill occasionally to remove chips. This prevents splinters or splinters from affecting the accuracy of the hole.
A drill or handheld compressed air gun is often used to remove chips during drilling. You can use cleaning techniques such as compressed air and high-pressure liquid refrigerant jet.
Complete and inspect the blind hole
Drill the hole until it reaches the desired depth as marked. You can use various post-processing processes to smooth the hole or achieve a fine finish.
Also check that the blind hole is the specified diameter and depth after drilling. Also look for any edges or burrs that may require additional processing.
What are the advantages and disadvantages of blind holes?
Advantages of blind holes
Blind holes offer broad advantages in technology and machining in various applications. Here are some of the expected benefits of blind holes:
Improved aesthetics
Blind holes improve the aesthetics of manufactured components by hiding fasteners and making them visually appealing without protruding visibly like traditional fasteners. This property is fundamental in industries where aesthetics are crucial, such as consumer electronics and automotive.
Increase your strength and reduce stress levels
Milling blind holes in a part increases its strength by evenly distributing weight and improving the overall stability of the workpiece. Blind holes avoid possible points of failure and guarantee longer product life, reducing stress concentration.
Reduce weight and save space
In applications such as electronics or aerospace, where space is limited, blind holes allow for more compact products to be manufactured. This allows manufacturers to optimize available space and produce thin, lightweight products.
Limitations on blind holes
Blind holes have several limitations, although they are useful in many applications. Here are the most common disadvantages of blind holes:
Possible trapped debris
Dirt or chips can easily get stuck at the bottom of the blind holes because these holes do not extend to the other side of the material. Most importantly, inspecting and cleaning holes can be difficult because it is impossible to see through blind holes.
Unlock complexity
Challenges can arise when tapping a blind hole, as it can be more complex than threading through holes. It would not be easy to guarantee the uniformity and precision of the threads in a blind hole.
Deformation or deformation of the material
The integrity of the material around a blind hole can be compromised when machining blind holes in materials such as ABS, aluminum and low-carbon steel, which are particularly susceptible to deformation under heat or pressure.
Various Applications of Blind Holes
Blind holes are widely used in various applications due to their greater strength and aesthetic benefits. Typical blind hole applications are:
aviation
Manufacturers in this field often intentionally use blind holes in the design of various aircraft components to save weight without compromising the primary strength of the aircraft part.
Electrical and electronic components
Engineers and machinists often use blind holes in electronic circuit boards to create attachment points for components such as connectors, spacers, and spacers. These holes allow for secure attachment without damaging traces or components on the other end of the board.
Architecture
Blind holes serve aesthetic purposes in metal and woodwork, as well as other crafts. Manufacturers use these features to create visually appealing designs by filling them with contrasting materials such as epoxy and metal inlays.
Construction of molds and matrices
Blind holes are used to produce molds and dies for injection molding, forming and casting processes. They provide attachment points for cooling channels, ejector pins and alignment functions, helping to improve molding performance and part quality.
Auto Industry
For secure fastening and to reduce material consumption, car manufacturers use blind holes in engine blocks and transmission parts.
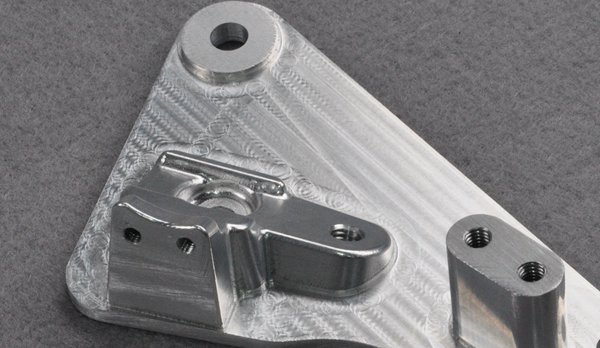
Considerations and Tips for Drilling Blind Holes
To achieve the desired results, attention to detail is required when machining blind holes. Here are some helpful tips for drilling blind holes effectively.
Choosing the Right Drills and Taps
Choose the right drill for the material to be processed. Experienced machinists generally recommend using high-speed steel for threading most metals.
Also, make sure the thread radius matches the desired thread size to achieve an accurate threaded blind hole. Depending on the depth of the blind hole, consider whether the type of tap (cylindrical, conical or basic) is suitable for tapping the blind hole.
Free drilling depth
Measure and mark the desired depth on the drill bit to avoid drilling holes that are too deep, as this weakens the material and increases the risk of material breakage. You can also control the drilling process by using adjustable depth collars or depth stops on the drill bit.
Most importantly, by consistently checking the depth clearance before drilling, you can avoid damaging the workpiece. Also, follow design specifications for drilling blind holes at the correct depth.
Hole placement and orientation
Hole placement and orientation significantly affect the manufacturability and usefulness of parts. To accurately drill blind holes, mark hole locations using layout tools such as layout angles and center punches. When creating blind holes, ensure their orientation matches the desired function of the final product or assembly to allow for smooth integration of designs.
hole diameter
The required hole diameter determines the ideal drill size. The drill chart is a reliable reference for selecting an appropriate drill size for the hole. Also, be sure to test fit the drill bit into the scrap material before drilling the final blind hole.
Clean blind holes
Use the appropriate cutting fluid or lubricant to reduce heat build-up and friction during drilling. Remove dirt from the blind hole using a cleaning brush or compressed air. However, it is important to inspect the blind hole and make sure it is clean and unobstructed before cutting the line.
Blind Hole vs. through hole: What are the differences?
Besides the names, the differences between blind holes and through holes are in the process and results. Blind holes do not penetrate the workpiece; they are only drilled to a certain depth, which is a fraction of the total thickness of the part. A through or through hole is created to reach the other side of the workpiece.
Machine operators drill blind holes in the workpiece to create recesses for fasteners. These blind holes often offer aesthetic benefits and are suitable for automotive, architectural, and consumer product applications. Through holes are often used in assemblies where components must be securely fastened and aligned. However, a blind hole is the perfect choice in situations where it is not possible to compromise the functionality or appearance of the part on the opposite side.
Additionally, through holes are compatible with fasteners such as bolts, screws or pins that pass completely through the material and can be secured on the opposite side with washers or nuts.
Other types of holes in machining
Blind and through holes are the most common types of holes used in product manufacturing. Other types of holes in manufacturing include:
Simple hole
A simple hole is the most commonly used hole in engineering and mechanical engineering. It is generally straight, cylindrical and has a constant diameter that extends through the entire thickness of the material. These holes are perfect for mounting, spacing and positioning purposes.
Drilled hole
A milled hole is smoothed and brought to a precise diameter, with the desired finishing done by a special CNC tool called a reamer.
hole
This is a tapered hole created by drilling into a workpiece to ensure that a screw or screw can sit flush with the surface of the material. Machinists cut a countersink into a workpiece to give it a flat surface and prevent a screw or stud from protruding.
Countersunk hole
A counterbore is a flat-bottomed hole drilled larger and deeper than the existing hole in the workpiece. It involves drilling a cylindrical depression in a material to create a flat surface around the hole. The recess has a larger diameter at the top that accommodates the head of the screw or bolt.
Threaded hole
A tapped hole is a hole into which a thread is cut using a special tool called a tap. Thread cutting involves cutting threads to the desired depth in the part material. Threaded holes are used for components such as screws or studs that require a secure fastening mechanism.
Conical hole
A tapered hole is another hole commonly used in engineering. It is characterized by a gradual change in diameter from one end to the other. This hole is used in a variety of applications, such as press fittings, to hold two components tightly together in an assembly.
WayKen editing capabilities for multiple holes and complex structures
Concluding
Blind holes are essential for the proper fit and function of many complexly shaped components. Machine operators use this feature to support fasteners, improve surface aesthetics, and strengthen machined parts.
Common questions
What is a threaded blind hole?
A threaded blind hole is a type of threaded hole that does not completely pass through the workpiece. The thread is cut into the hole to provide a secure and reliable connection between mating parts.
What material can blind holes be machined in?
Machine operators create blind holes in various materials such as plastics, metals and composites. However, material properties can determine appropriate machining methods and tools.
What are the standard measuring and testing procedures for blind holes?
Product engineers often use several quality control methods to ensure accuracy when machining blind holes for reliable part assembly. Measuring tools and testing procedures, surface profilers, non-destructive testing, and coordinate measuring machines are typical devices that help obtain accurate results for blind holes.