I. Weld Joints and Weld Seams
Arc welding joints consist of four parts: the weld seam, the fusion zone, the heat-affected zone, and the base material near the weld seam.
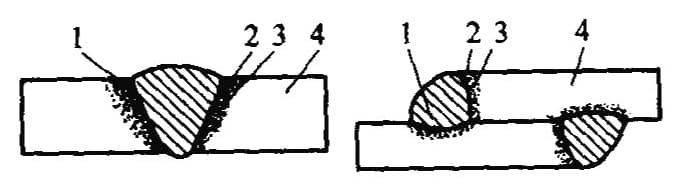
a) Butt joint b) Lap joint
1 – Weld metal
2 – Melted Wire
3 – Heat Affected Zone
4 – Base Material
1. Mechanical Characteristics of Welded Joints
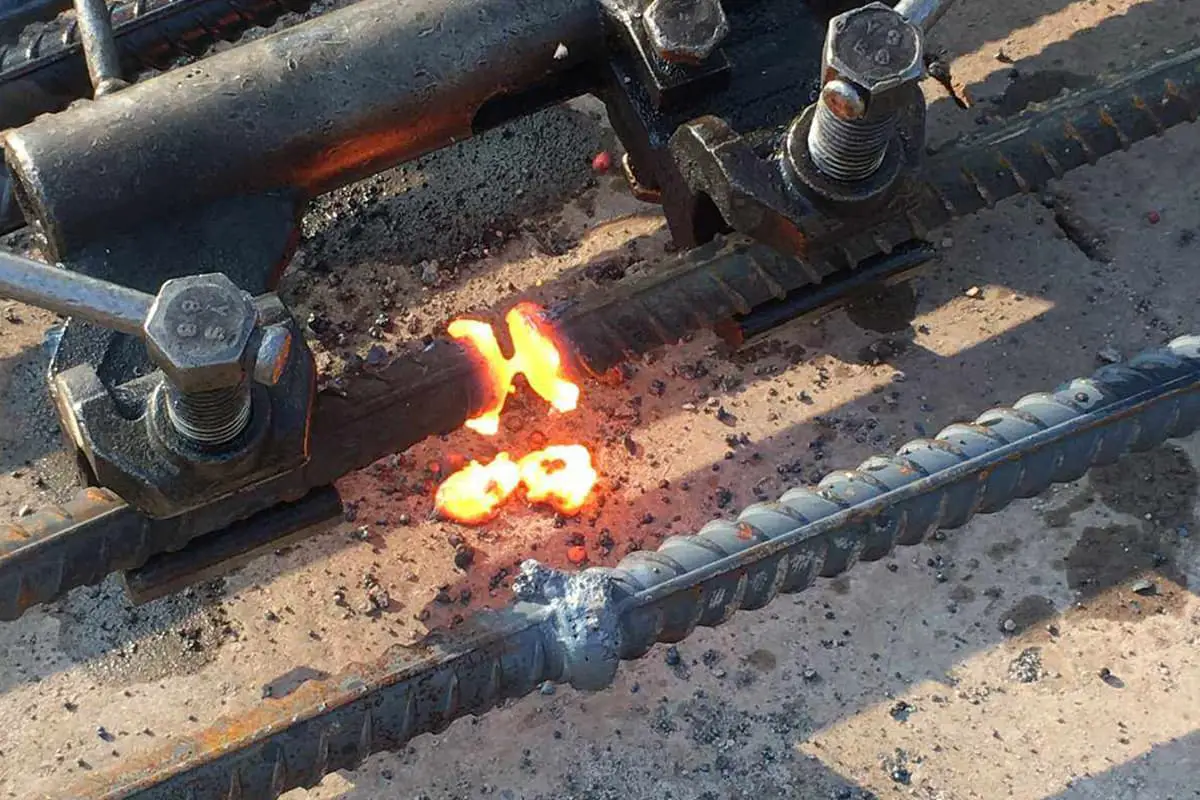
The welding process gives the joint the following mechanical characteristics:
1) Heterogeneous mechanical performance of welding joints
Due to the various metallurgical processes that occur during welding, and due to the different thermal cycles and deformation cycles that affect different areas, significant disparities in the structure and properties of these areas occur. This results in heterogeneous mechanical performance of the entire joint.
2) Uneven distribution and concentration of stresses in welded joints
The geometric discontinuities inherent in welded joints lead to an uneven distribution of working stresses and subsequent stress concentration. When welding defects are present, or when the shape of the seam or welding joint is impractical, the stress concentration intensifies, affecting the strength of the joint, particularly its resistance to fatigue.
3) Residual stress and deformation due to uneven heating during welding
Welding is a localized heating process. During arc welding, the temperature at the weld seam can reach the boiling point of the material, but quickly decreases from the seam to room temperature. This uneven temperature field leads to residual stress and deformation within the weldment.
4) High rigidity of welding joints
Through welding, the seam and components are unified, providing a greater degree of rigidity compared to riveted or contracted joints.
2. Basic Shapes of Joints
Welded Joint (also called Joint): A joint connected by welding.
Commonly used welded joints:
Butt joint, T joint, cross joint, lap joint, corner joint, edge joint, sleeve joint, chamfered butt joint, flanged joint and double V butt joint, among others.
The basic types of welded joints.
Name | Weld seam formation | Name | Weld seam formation |
Butt joint |
![]() |
Terminal connector |
![]() |
T-Joint |
![]() |
Oblique End Connector |
![]() |
Corner joint |
![]() |
Flanged Connector |
![]() |
Lap joint |
![]() |
Sealed end connector |
![]() |
1. Top joint
A butt joint is formed by welding the edges of two workpieces lying in the same plane. This type of joint is the most commonly adopted and the most refined in various welded structures, featuring superior stress handling, high strength and efficient use of metallic materials.
However, because it is an end-to-end connection, the processing and assembly requirements of the connected parts are quite high.
In welding production, the butt joint weld seam is normally slightly higher than the surface of the base material. The presence of this excess height results in a non-smooth surface of the component, causing stress concentration in the transition between the weld bead and the base material.
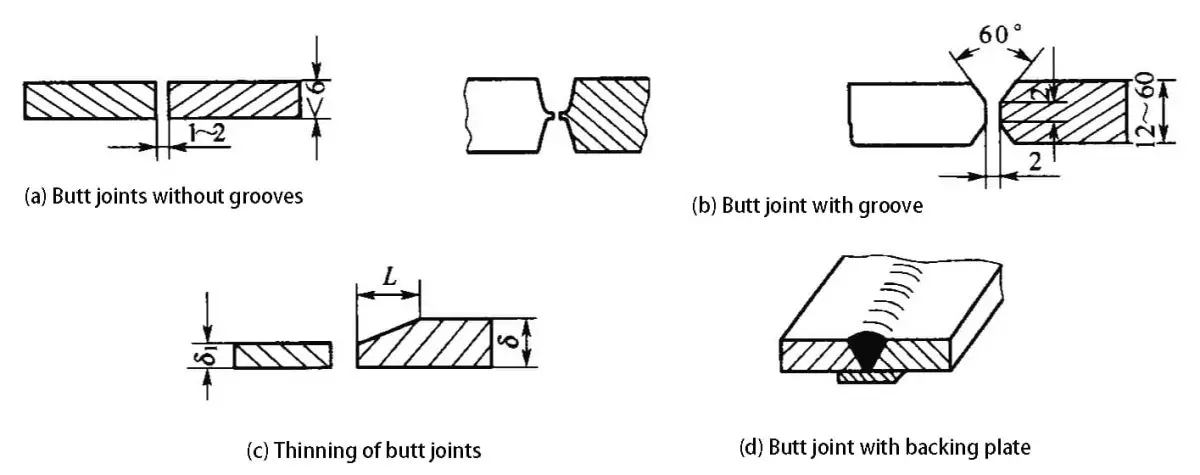
2. T-Joint
A T-joint (or cross joint) is formed by connecting perpendicular pieces using a fillet weld. T-joints can withstand forces and torques from various directions. This form is most commonly found in box structures and is also prevalent in the manufacture of pressure vessels, including tube-casing connections and the joining of manhole reinforcing rings to the vessel body.
Due to the sharp transition from the weld seam to the base material at T-joints, there is significant distortion of the line of force under external forces, leading to a very uneven and complex stress distribution. This results in substantial stress concentration at both the root and base of the fillet weld. Ensuring full penetration is a crucial measure to reduce stress concentration in T-joints.

3. Lap joint
A lap joint is created by overlapping two plates and then conducting a fillet weld on the end or side, or adding a tongue or groove weld. Due to the misalignment of the two plate centerlines at the lap joint, an additional bending moment is generated under load, which can affect the strength of the weld.
Consequently, lap joints are not normally used for the main pressure supporting elements in boilers and pressure vessels.
The significant change in the shape of the components due to lap joints leads to a more complex stress concentration compared to butt joints, resulting in an extremely uneven stress distribution across the joint.
In lap joints, based on the different stress directions acting on the lap fillet weld, these welds can be categorized as front, side or diagonal fillet welds.
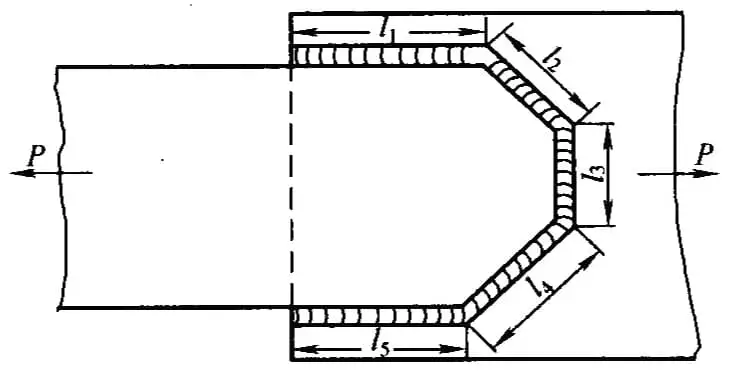
In addition to welding two steel plates stacked at the end or side, lap joints also involve groove welding and plug welding (round holes and elongated holes). The structure of a groove welded lap joint is shown in the figure.
First, the part to be connected is drilled into a groove, and then the groove is filled with weld metal. The cross section of the groove weld is rectangular and its width is twice the thickness of the connected component. The length of the groove should be slightly less than the length of the lap.
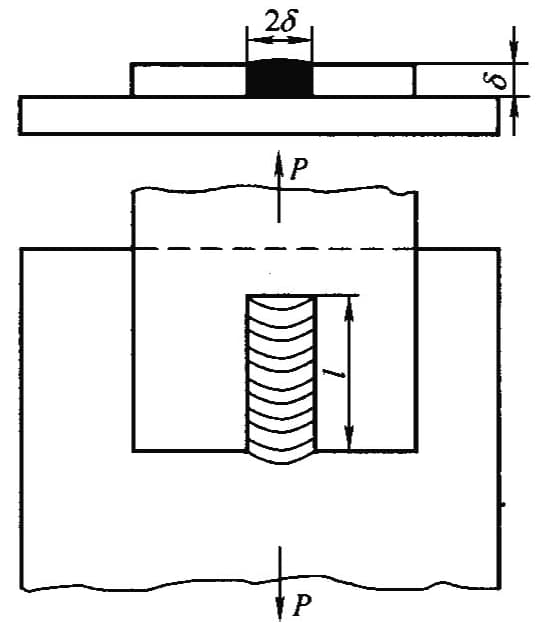
Plug welding involves drilling holes in the plates to be joined, substituting slot-for-slot welding, and using weld metal to fill these holes, thus connecting the two plates. Plug welding can be divided into two types: circular hole plug welding and elongated hole plug welding, as shown in the figure.
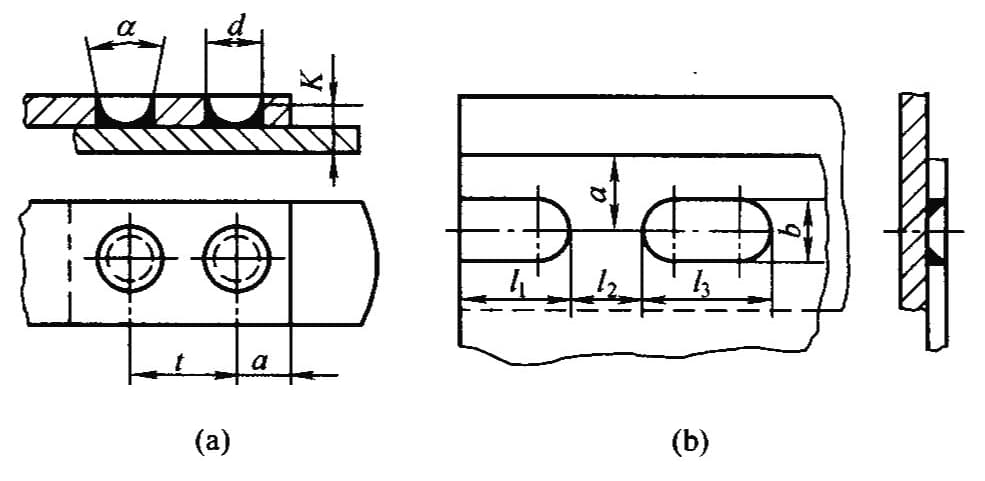
4. Corner joint
A corner joint is formed when two plates are welded at their edges at a certain angle. Corner joints are commonly used in box structures, saddle tube joints, and connections to cylindrical bodies. The connection between fire tubes and covers in small boilers also takes this form.
Similar to T-joints, one-sided corner joints have extremely low resistance to reverse bending moments. Unless the plates are very thin or the structure is not critical, the chamfers generally must be made for double-sided welding, otherwise the quality cannot be guaranteed.
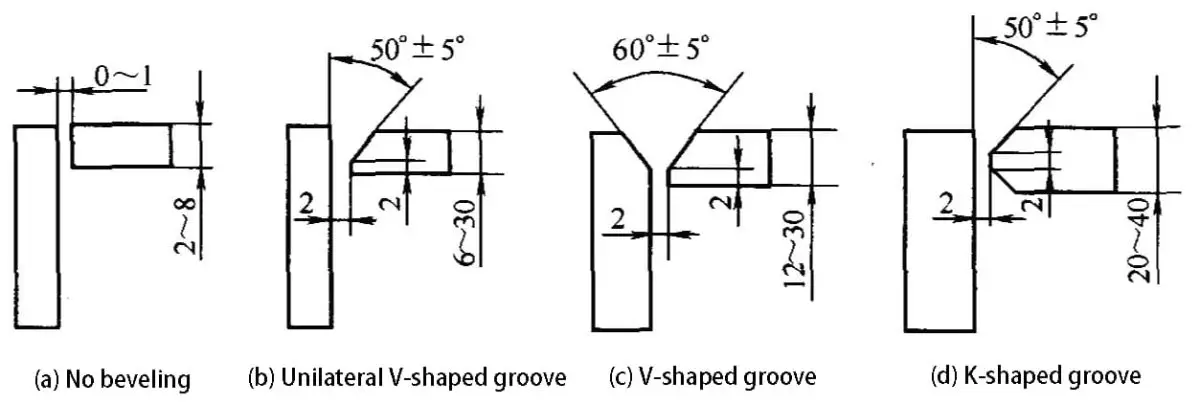
When selecting the gasket type, primarily consider the product structure as well as factors such as stress conditions and processing costs.
For example:
Butt joints are widely used because they distribute stress evenly and save metal. However, butt joints require precise cutting and assembly dimensions.
T-joints mainly support small shear stresses or serve only as connecting welds.
Lap joints do not require high assembly precision and are easy to assemble, but their load capacity is low, so they are generally used in non-critical structures.
The requirements for weld quality, weld size, weld position, part thickness, geometric dimensions and working conditions in the design of welded joints determine the diversity in the selection of welding methods and formulation processes. Reasonable design and selection of welded joints not only ensures the strength of welds and the overall steel structure, but also simplifies the production process and reduces manufacturing costs.
Main factors in the design and selection of welded joints:
1. Make sure the welded joint meets the usage requirements.
2. The shape of the joint can accommodate the chosen welding method.
3. The shape of the joint should be as simple as possible, with flat welding and automatic welding methods used whenever possible. Avoid overhead and vertical welding and do not place maximum stress on the weld.
4. The welding process must ensure that the welded joint can function properly at the designed temperature and in corrosive media.
5. Welding deformation and stress must be minimized to meet the technical, personnel and equipment conditions required for construction.
6. Design the weld to serve as a connection weld whenever possible.
7. The welded joint must be easy to inspect.
8. Welding preparation and welding cost should be low.
9. Avoid choosing and designing oversized weld angles for fillet welds. Tests show that large fillet welds have a lower load capacity per unit area.
Table 1-2: Comparative Design of Welded Joint Shapes
Joint Design Principles | Failure-prone design | Improved design |
Increase front angle weld | ![]() |
![]() |
The designed position of the weld seam should facilitate welding and inspection | ![]() |
![]() |
To reduce the stress concentration in the overlapped weld seam, it should be designed as a joint with certain stress relief. | ![]() |
![]() |
Cut the sharp corners of the reinforcing ribs | ![]() |
![]() |
Weld seams must be distributed | ![]() |
![]() |
Avoid cross-welded seams | ![]() |
![]() |
Weld seams must be projected on or near the neutral axis in a symmetrical position | ![]() |
![]() |
Weld beads subject to bending must be dimensioned on the tension side and not on the non-welded compression side. | ![]() |
![]() |
Avoid placing weld seams where stress is concentrated. | ![]() |
![]() |
Weld seams should avoid areas with maximum stress. | ![]() |
![]() |
The processing surface must be free from welding seams. | ![]() |
![]() |
The position of automatic welding seams must be designed in such a way that the adjustment of the welding equipment and the number of turns of the part are minimized. | ![]() |
![]() |
3. Basic Shapes of Welding Seams
A weld seam is the joint formed after welding parts.
Categories:
1. Based on spatial positioning, it can be divided into: flat weld seams, horizontal weld seams, vertical weld seams and overhead weld seams.
2. Based on the joining method, it can be categorized into: butt weld seams, corner weld seams and plug weld seams.
3. Based on continuity, it can be classified into: continuous weld beads and intermittent weld beads.
4. Based on load bearing, it can be divided into: working welding seams and contact welding seams.
The weld seam is a crucial component of the welded joint. The basic shapes of the weld seam are the butt joint weld seam and the corner joint weld seam.
1. Butt weld seams:
Butt weld seams are formed along the joint between two parts. They can have an ungrooved (or I-groove) or grooved configuration. The surface shape of the weld seam can be convex or flush with the surface.
2. Corner welding seams:
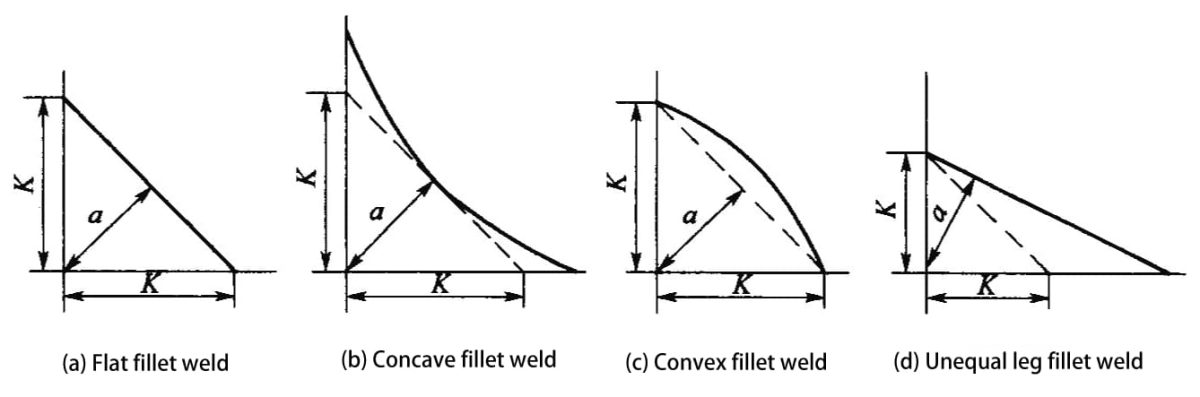
4. Working welding seams and contact welding seams
Working weld seams (also known as load-bearing weld seams)
These are weld seams that, in series with the welded parts, mainly support loads. If these seams break, the steel structure will immediately suffer serious damage.
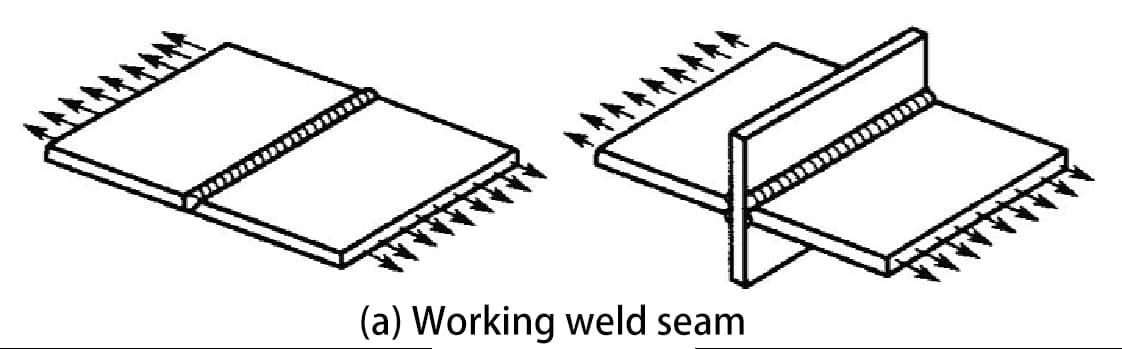
Contact weld seams (also known as non-load-bearing weld seams)
These are weld seams that unify two or more welded parts in parallel (that is, providing connectivity). These seams are not directly load-bearing and are subject to minimal force during operation. If such a seam were to rupture, the structure would not fail immediately.

5. Basic Groove Shapes
1. Types of grooves
A groove is a trench formed by machining certain geometric shapes into the to-be welded parts of a part according to design or process requirements.
Groove preparation:
The process of machining the groove using mechanical, flame or electric arc methods.
Purpose of groove preparation:
(1) To ensure that the arc penetrates deep into the root of the weld seam for complete fusion, to obtain optimal weld seam formation, and to facilitate slag removal.
(2) For alloy steels, the groove also adjusts the ratio of base metal to filler metal (i.e. melt rate).
Depending on the thickness of the plate, the welding edges of butt weld seams can be rolled, squared or machined into V-shaped, X-shaped, K-shaped and U-shaped grooves.
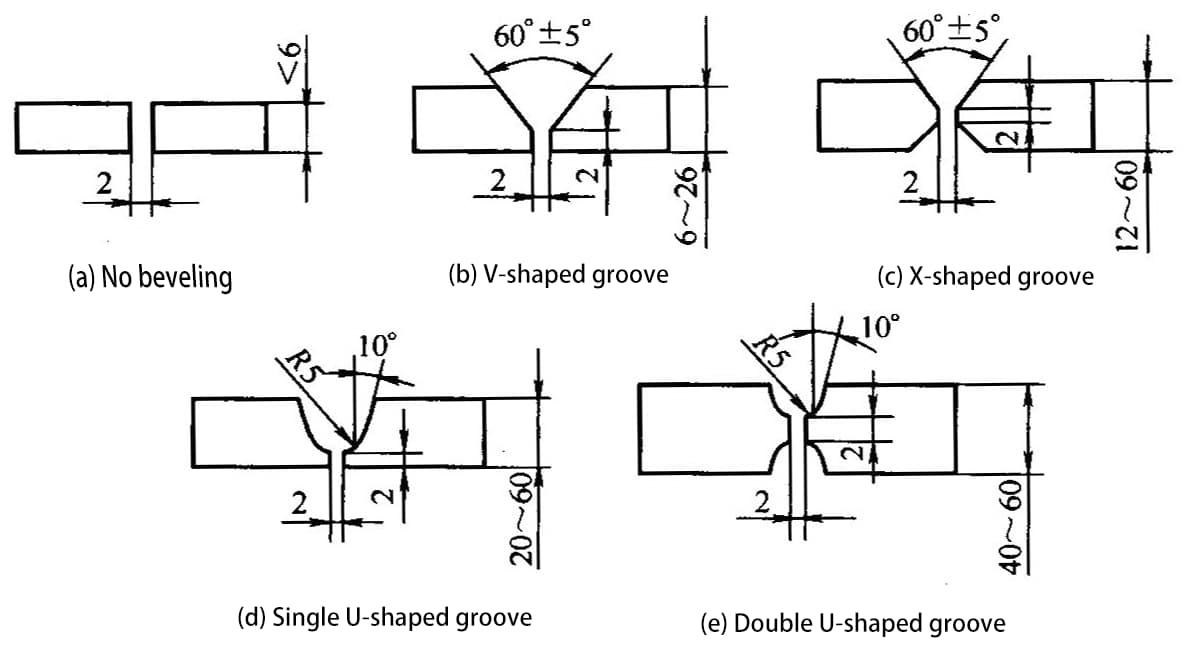
(2) Depending on the thickness of the workpiece, the structure and the load-bearing conditions, the groove shapes for corner joints and T-joints can be divided into I-shape, one-sided V-shape with blunt edge, and K-shape .
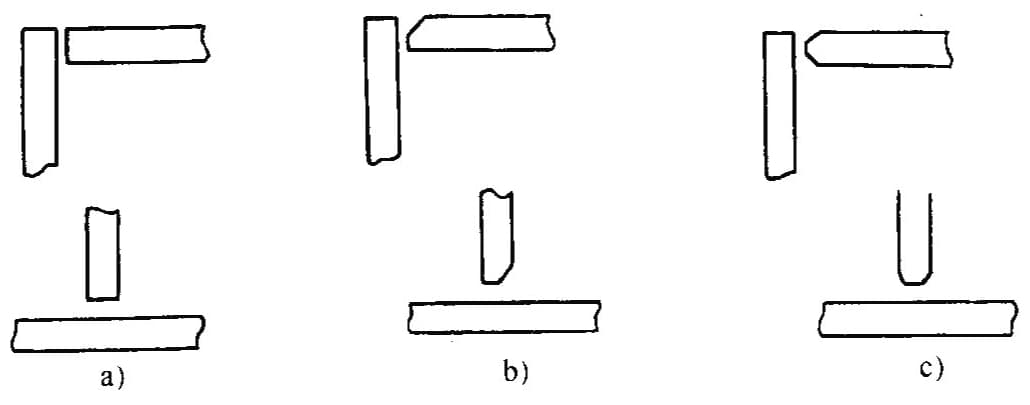
a) I-form
b) One-sided V-shape (with blunt edge)
c) K shape (with blunt edge)
2. Principles for Groove Design
The shape and dimensions of the groove are chosen and designed mainly based on the thickness of the steel structure, the selected welding method, the welding position and the welding process. The project must:
1) Minimize the amount of filler material in the weld seam;
2) Have good weldability;
3) Make sure the groove shape is easy to machine;
4) Facilitate the adjustment of welding deformation;
In general, for welding parts up to 6 mm thick using electrode arc welding, or for automatic welding of parts up to 14 mm thick, it is possible to obtain a qualified weld seam without groove preparation.
However, a space must be maintained between the plates to ensure that the filler metal fills the molten pool, ensuring complete fusion. If the steel plate exceeds the thickness mentioned above, the arc cannot penetrate the plate and groove preparation must be considered.
II. Representation methods for welded joints
To ensure that their designs are manufactured accurately and correctly by manufacturers, designers must comprehensively express the technical conditions of structures and products in design drawings and design specification documents.
For welded joints, designers generally use standardized symbols for weld beads and codes for welding methods. They may also use technical drawing methods, but graphically or textually detailing the welding process requirements and considerations for welded joints can be quite complicated and cumbersome.
Therefore, it is extremely necessary to use standardized symbols and codes to clearly indicate the type, shape, size, position, surface condition, welding method and related conditions of the welded joint.
1. Weld seam symbols and welding method codes
Weld Seam Symbols: Symbols marked on drawings to represent the shape, size and method of the weld seam.
They are regulated by GB/T324-1998 “Symbolic Representation of Weld Seams” (applicable to metal fusion welding and resistance welding) and GB/T5185-1999 “Representation Codes for Metal Welding and Brazing Methods in Drawings .
A weld seam symbol consists of:
- basic symbols
- supplementary symbols
- additional symbols
- weld seam size symbols
- leading lines.
Basic symbols: These symbols represent the shape of the cross-section of the weld bead, approximating the shape of the cross-section of the weld bead.
Names of weld seams | Cross-sectional shape of the weld seam. | Symbol |
I-shaped weld seam |
![]() |
![]() |
V-shaped welding seam |
![]() |
![]() |
V-shaped weld seam with blunt edges |
![]() |
![]() |
V-shaped weld seam on one side |
![]() |
![]() |
V-shaped weld seam on one side without edges |
![]() |
![]() |
U-shaped weld seam with blunt edges |
![]() |
![]() |
Weld seam sealing |
![]() |
![]() |
Weld bead |
![]() |
![]() |
Socket weld or slot weld |
![]() |
![]() |
Flare-V Welding |
![]() |
![]() |
Welding point |
![]() |
![]() |
seam welding |
![]() |
![]() |
Supplemental Symbols: These symbols represent additional requirements for the surface shape characteristics of the weld seam. Supplementary symbols are generally used in conjunction with basic weld bead symbols when there are special requirements for the shape of the weld bead surface.
Name | Assisted Welding Technique | Symbol | Instructions |
Flat symbol |
![]() |
![]() |
Indicates a level weld surface. |
Concave symbol |
![]() |
![]() |
Indicates a concave weld surface. |
Convex Symbol |
![]() |
![]() |
Indicates a convex weld surface. |
Weld Reinforcement Symbols: These are symbols used to further illustrate certain characteristics of a weld seam.
Name | Form | Symbol | Recommendation |
Symbol with Pad |
![]() |
![]() |
Indicates the presence of a support strip at the bottom of the weld seam. |
Three-sided weld symbol |
![]() |
![]() |
It suggests welding seams on three sides and the opening direction. |
Perimeter weld symbol |
![]() |
![]() |
Symbolizes a weld seam around the workpiece. |
Field symbol |
![]() |
Indicates welding carried out on site or at a construction site. | |
Tail symbol |
![]() |
Reference to the terminal end of the lead line symbol can be made in GB5185-1999 for soldering methods and similar notations. |
Weld Seam Dimension Symbols: These are symbols used to represent the dimensions of groove and weld seam features.
Symbol | Name | Schematic diagram |
σ | Sheet thickness | ![]() |
w | Weld seam width | ![]() |
B | Root gap | ![]() |
K | Weld toe height | ![]() |
P | Blind edge height | ![]() |
d | Weld point diameter | ![]() |
The | Groove angle | ![]() |
H | Weld reinforcement | ![]() |
It is | Effective Weld ThicknessSame Weld Joint | ![]() |
N | Quantity symbol | ![]() |
It is | Weld spacing | ![]() |
I | Weld length | ![]() |
R | Root Ray | ![]() |
H | Groove height | ![]() |
Leader Line: Consisting of a leader line with arrow, two reference lines (horizontal lines) – a solid line and another dashed line, and a tail section.
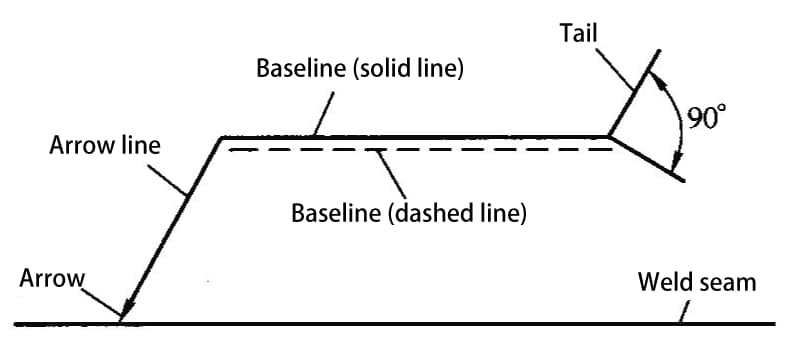
To simplify the annotation and textual explanation of welding methods, codes representing various welding methods such as metal welding and brazing, indicated by Arabic numerals in accordance with the national standard GB/T 5185-1999, can be used.
Welding method notes are located at the end of the guide line.
Name | Welding method |
Arc welding | 1 |
Shielded Metal Arc Welding | 111 |
Submerged Arc Welding | 12 |
Metal Inert Gas (MIG) Welding | 131 |
Tungsten Inert Gas (TIG) Welding | 141 |
Pressure welding | 4 |
Ultrasonic welding | 41 |
Friction welding | 42 |
Diffusion Welding | 45 |
Explosion Welding | 441 |
Resistance welding | two |
Spot welding | 21 |
Seam welding | 22 |
Instant welding | 24 |
Gas Welding | 3 |
Oxy-Acetylene Welding | 311 |
Oxy-Propane Welding | 312 |
Other welding methods | 7 |
laser welding | 751 |
electron beam | 76 |
2. Representation of Welding Joints in Drawings
Schematic Representation of Welds
According to the national standard GB/Tl2212-1990 “Technical Drawing – Dimensions, Proportions and Simplified Representation of Welding Symbols“, when it is necessary to represent welds in a simplified way in drawings, they can be represented by means of views, sectional views, or cross-sectional views, or even axonometric views for illustrative purposes.
Generally, only one type of representation is allowed per drawing.
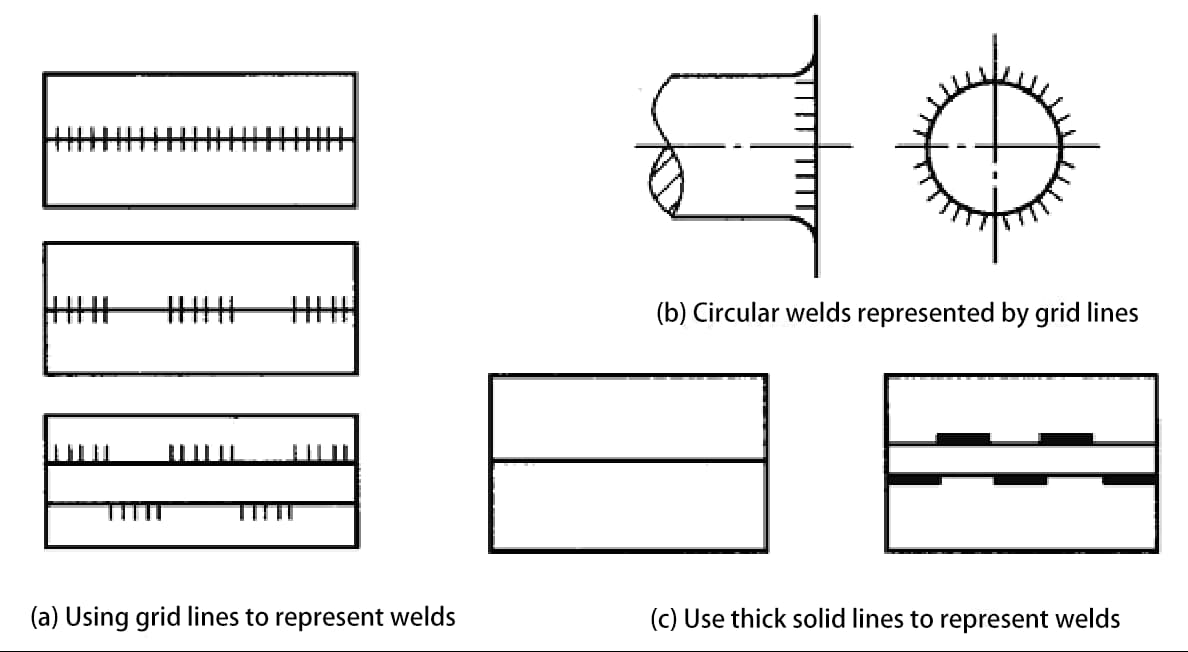
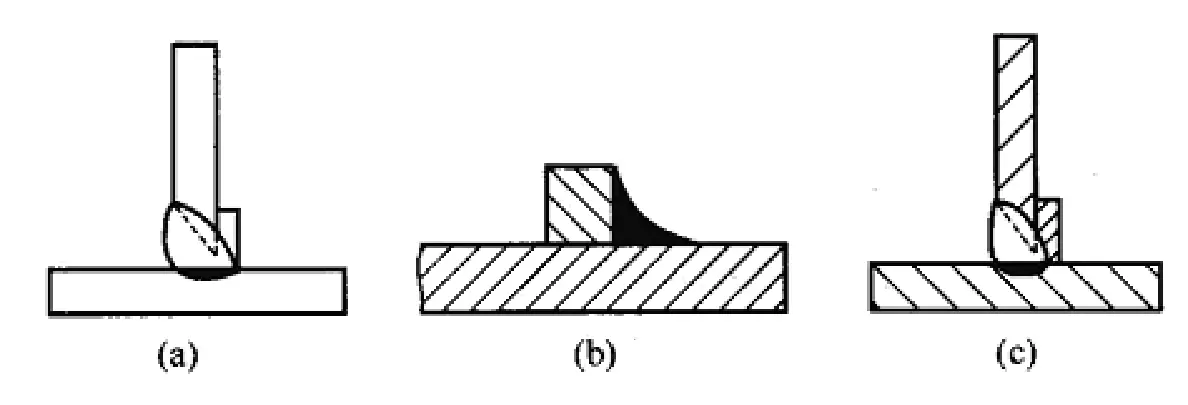
(a) Weld end face view drawing method
(b) Weld seam section view drawing method
(c) Weld profile drawing method
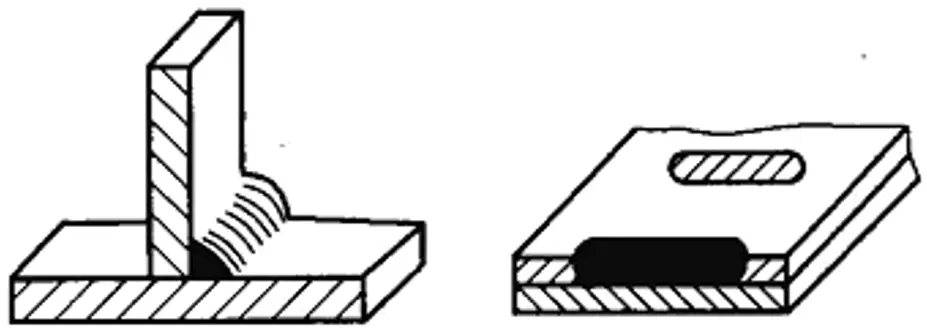
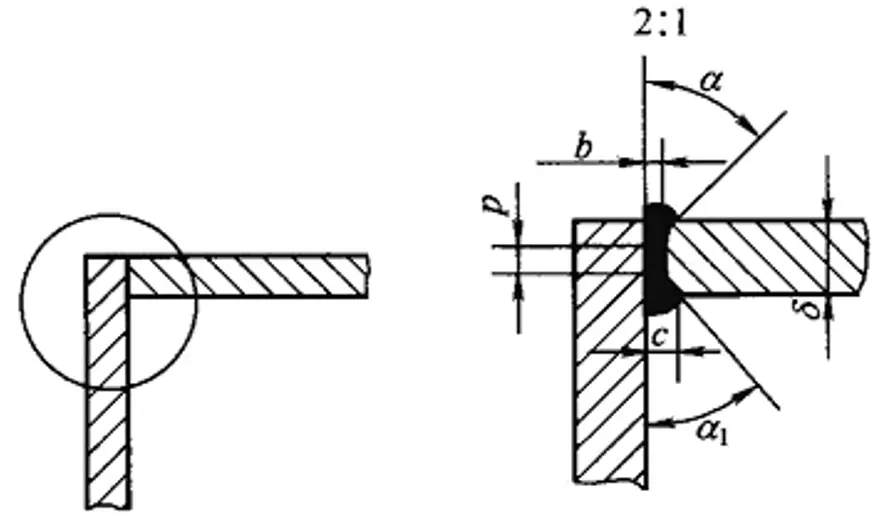
3. Annotation of Welding Symbols
National Standard GB/T324-1988, GB/T5185-1999 and GB/T12212-1990 each stipulate annotation methods for welding symbols and welding method codes.
(1) Welding symbols and welding method codes can be represented accurately and unambiguously through relevant guidelines and regulations.
(2) When noting welds, first note the basic welding symbols on top or below the reference lines, and other symbols shall be noted in their respective positions as prescribed.
(3) There are generally no specific requirements for the position of the arrow line relative to the weld, but when noting V-shaped, single-sided V-shaped, J-shaped, etc. welds, the arrow should point toward the workpiece with the groove.
(4) When necessary, the arrow line can be bent once.
(5) The imaginary reference line can be drawn above or below the real reference line.
(6) The reference line should generally be parallel to the bottom edge of the drawing, but under special conditions it may also be perpendicular to the bottom edge.
(7) If the weld and the arrow line are on the same side of the joint, the basic weld symbol will be noted next to the actual reference line; conversely, if the weld and arrow line are not on the same side of the joint, the basic weld symbol will be noted on the side of the imaginary reference line.
When necessary, the basic welding symbol can be accompanied by symbols and size data.
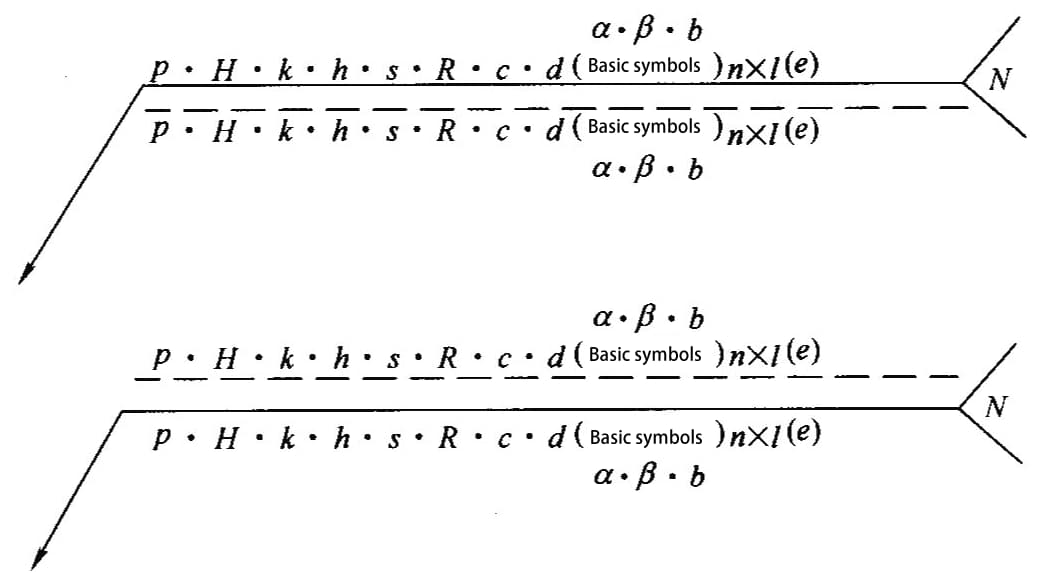
Annotation principles:
1) The dimensions in the cross-section of the weld bead are marked on the left side of the basic symbol, such as: blunt edge height p, groove height H, weld angle size K, residual weld bead height h, thickness effective weld bead S, root radius R, weld bead width C and weld nugget diameter d.
2) The dimensions in the direction of the weld bead length are marked on the right side of the basic symbol, such as: weld bead length L, weld bead gap and number of identical weld beads n.
3) The groove angle α, groove face angle β, root clearance b and other dimensions are marked on the upper or lower side of the basic symbol.
4) The symbol for the number of identical weld beads is marked on the rear end.
5) When there are many dimensions to be marked and they are not easy to distinguish, the corresponding dimension symbol can be added in front of the data.
Name | Schematic diagram | Marking |
Butt weld seam |
![]() |
![]() |
![]() |
![]() |
|
Intermittent fillet weld seam |
![]() |
![]() |
Staggered Intermittent Fillet Weld Seam |
![]() |
![]() |
Spot welding seam |
![]() |
![]() |
Weld seam |
![]() |
![]() |
Plugged weld seam or grooved weld seam |
![]() |
![]() |
4. Simplified weld joint annotation
In GB/T12212-1990, simplified annotation methods for welding joints are also stipulated in certain circumstances.
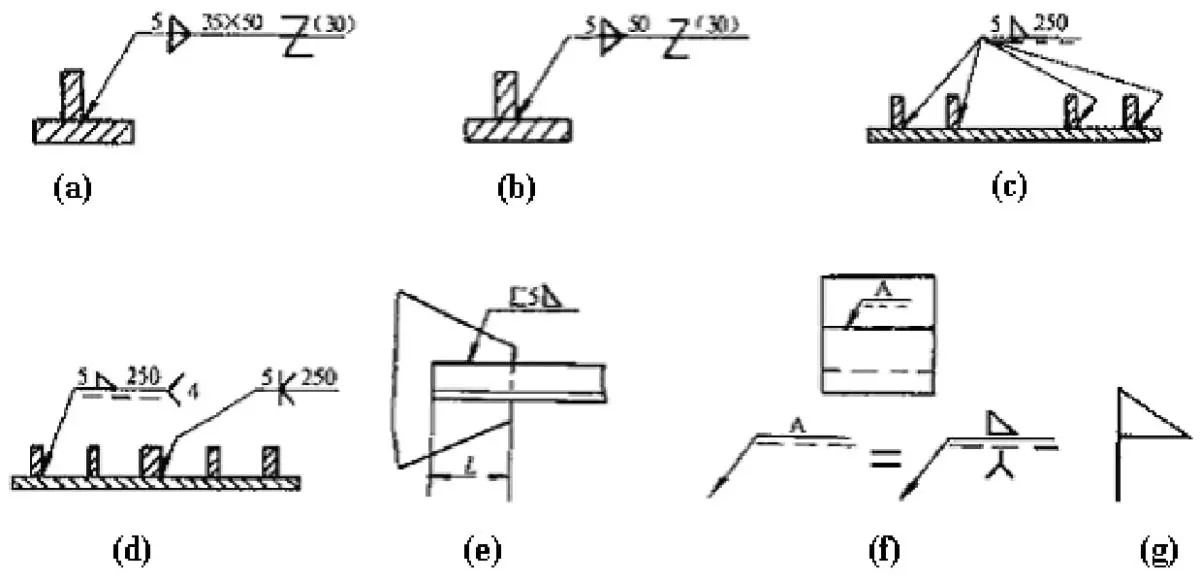