Milling is a form of subtractive manufacturing that involves cutting a stationary flat surface with a rotating tool. Up and down milling are the two main methods used by machinists to mill a part. However, it is often difficult to choose between the two as they both have advantages and disadvantages.
Here we look at the differences, advantages and disadvantages of up milling and down milling. We also provide factors to consider when choosing between the two milling methods so you can make the right machining decisions.
What is downmilling?
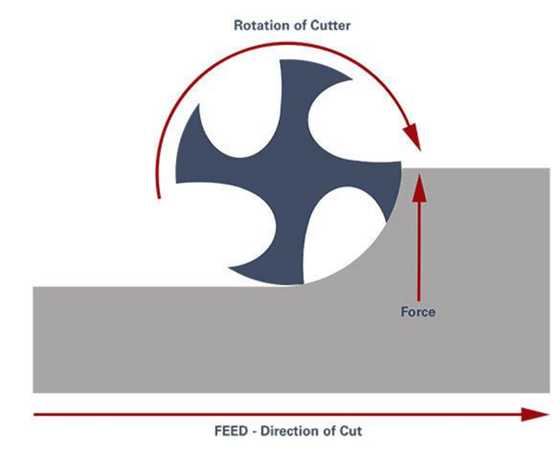
Also known as down milling, it refers to a milling process in which the cutting tool and the workpiece rotate in the same direction. An advantage of downmilling is that there is no possibility of rectification. The reason for this is that during milling, the teeth of the cutting tool move up the workpiece and deposit the cut chips behind the cutter. It is important to note that chip formation in this milling process begins at full thickness, but the thickness decreases as cutting progresses.
What is conventional milling?
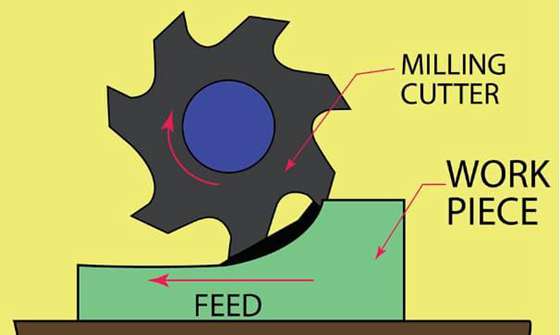
This is the traditional CNC milling process in which the cutting tool rotates in the opposite direction of the workpiece. Also called up-cut milling, cutting occurs in the upward direction during conventional milling.
Unlike down milling, chip formation in conventional end milling starts at zero and gradually increases. Furthermore, the cut chips remain in the path of the cutter due to their upward rotation.
Main differences between down and up milling
What is the difference between up-cut and down-cut milling? Well, there are many differences between the two procedures, from the procedure to the result. However, a fundamental difference between these two milling methods is that tool deflection affects cutting accuracy.
Tool deflection in conventional milling is parallel to the cut, which means better control of the cutting process and less tolerance for errors. However, in down milling, the tool deflection is normally perpendicular to the cut. This direction can decrease or increase the width of the cut, affecting its accuracy.
When roughing a part, it is recommended to try down milling as it produces faster results. Furthermore, the effects of tool deflection on roughing accuracy are negligible because the part becomes more accurate with the finishing pass.
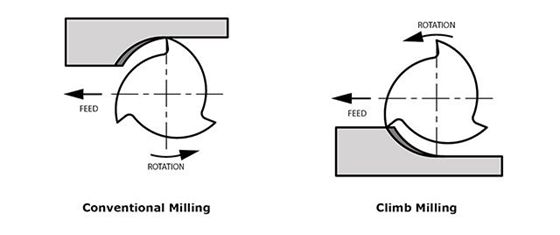
Up vs. up milling counter-rotation milling: advantages
Both methods have their advantages depending on the application. Let's take a closer look at these benefits as they may influence your decision about which process is best for your workpiece.
Advantages of synchronous milling
Improved tool life
The cutting tool used for this process generally has a better service life than tools used in conventional milling. The reason for this is that the tool is not subjected to much stress during the cutting process. A milling tool used for down milling generally produces less heat and less deformation than conventional milling. This results in less wear and tool life is up to 50% longer than conventional milling.
Improved surface processing
Because chip thickness decreases during down milling, there are fewer distractions during the cutting process. Furthermore, with this process, the chips are deposited behind the cutter, preventing cutting and ensuring excellent surface quality on the machined parts.
Low cutting load and heat generation
Down milling produces less heat because the chip width gradually decreases as cutting progresses. Additionally, because the cutting force is directed downward, the overall cutting load and the need for workpiece support are reduced, especially during horizontal milling operations. The downward force of the cutter can also help prevent machining vibrations by holding the part firmly to the underlying surface.
Facilitates the fixing of the part
Down milling applies downward pressure that helps support the workpiece against the underlying surface during face milling, reducing chatter in thin floors.
Advantages of conventional milling
The main advantages of conventional milling over climbing include:
Greater stability
While in downward cutting the part tends to be pulled towards the operator during downward cutting, in conventional milling this happens in the opposite direction. Therefore, it offers the driver more control, resulting in more stability. Compared to down milling, there are no excessive vibrations in conventional milling. In terms of stability, conventional milling wins the argument of synchronous milling over conventional milling.
No game
One factor that distinguishes conventional milling is the absence of backlash. This is because conventional milling does not pull the table upwards, which guarantees optimal stability.
Optimal control
In conventional milling operations, there is a greater tendency for the cutter to deviate from the part. This distraction ensures that the chance of accidental cuts is minimal. And even if these cuts occurred, their depth would be insignificant. Therefore, in terms of optimal control, conventional milling wins the debate between down milling and conventional milling.
Up vs. up milling Counter-rotation milling: Disadvantages
Both synchronous milling and conventional milling have their advantages, but also their disadvantages. Here are some of them.
Disadvantages of synchronous milling
Setback
This is a major disadvantage of down milling in the conventional versus down milling debate, especially when the milling forces are strong enough. Let's explain in more detail.
During down milling, a downward force is exerted. This force often acts not only on the workpiece, but also on the table, pulling it into the cutting tool.
So if there is a game, the table is tied with the same game. This also means that if there is enough play, the risk of the table breaking is very high, which can cause injury to the operator. This is especially true when the cutting tool operates at high capacity.
However, nowadays milling machines are equipped with a backlash eliminator. This helps reduce backlash so machinists can take full advantage of the benefits of down milling.
Excessive vibrations
During synchronous milling, strong vibrations occur at high feed rates or when machining thick parts. The cause of these vibrations is the impact of the cutting tool on the part. These vibrations are harmful because they often cause deflections in the tool that can affect accuracy. They can also damage the workpiece.
Not ideal for harder materials
Since the chip thickness in down milling is greater at the beginning of the cut, this process would damage the cutting tool in harder materials. This can happen with cutting tools made from steel, cast iron, titanium and other hard materials. When milling harder tools, up milling wins the down milling versus up cutting debate.
Disadvantages of conventional milling
Uneven surface
The upward cutting used in this process makes it difficult to obtain a smooth surface. This is due to the number of deflections the workpiece and cutting tool undergo, resulting in a rougher surface.
However, this deflection rate also makes conventional milling ideal for machining harder materials such as steel and cast iron.
Process generates excessive heat
Another disadvantage of conventional grinding is the heat generated during the process. This heat occurs because chip formation here occurs gradually, which often leads to overheating of the cutting tool. A consequence of overheating of the cutting tool is a reduction in its useful life.
Tool damage
Conventional milling creates friction and upward forces that often result in excessive heat. Furthermore, excessive heat will damage the tool, shortening its service life and reducing the precision and accuracy of the workpiece.
Tips and tricks for synchronous milling compared to conventional milling
Would you like to machine your product? Here are some tips and tricks that you might find useful:
If you want to remove rough material, it is better to use conventional milling. Avoid conventional milling in the final cut as it creates a rough surface.
When using a manual milling machine, it is best to always use conventional milling as this will achieve great results.
Cutting depth and tool life are opposites, so it is best to find a balance between them. You should note that increasing the cutting depth reduces tool life and vice versa.
If you use a conventional machine for down milling, make sure it has a backlash compensation feature to avoid accidents.
Avoid down milling on oxidized material or the first pass on a rough surface.
WayKen Custom CNC Milling Services
One way to ensure consistent CNC machining results is to match the right tool with the right experience. For this reason, you should outsource your up and down milling projects to reputable manufacturing companies.
Simply upload your CAD file. We will analyze your project and send you a quote within 12 hours. This looks great. So contact us today for your CNC milling project.
University Degree
Climb milling versus conventional milling is a debate that has long raged among new and experienced machine operators. However, both procedures have their advantages and disadvantages.
In this article, we'll discuss the differences and the pros and cons of these techniques so you can make informed decisions about which is right for your project.
Common questions
Why is down milling called milling?
The name synchronous milling comes from the fact that when milling with this technique, the milling teeth descend onto the surface of the part. This causes chips to accumulate behind the cutter and reduces grinding frequency.
Why does downmilling produce a better surface finish?
There are two main reasons why down milling produces a better finish. First, in this cutting process, the cutting chips are behind the cutter, reducing undercutting. The second reason is that down milling reduces cutting forces, resulting in less tool deflection and a better finish.
However, it should be noted that if there is strong tool deflection, conventional milling will produce a better surface result.
Is a climbing mill or a conventional mill better?
Which method is best depends on the type of machine, preferences, and material requirements. However, conventional machining is a better choice than manual machining, especially when using a machine without backlash compensation.