Generally, we consider the components of a bearing to include: the inner ring, outer ring, rolling element, cage, seals and lubrication. In fact, during previous lectures for engine engineers, the clearance of an engine bearing was listed as one of the components of a bearing.
Of course, clearance is an air gap, not a physical component, but the attention engineers pay to clearance in design, installation, use and maintenance is no less than any physical part of the bearing.
What is the clearance of an engine bearing?
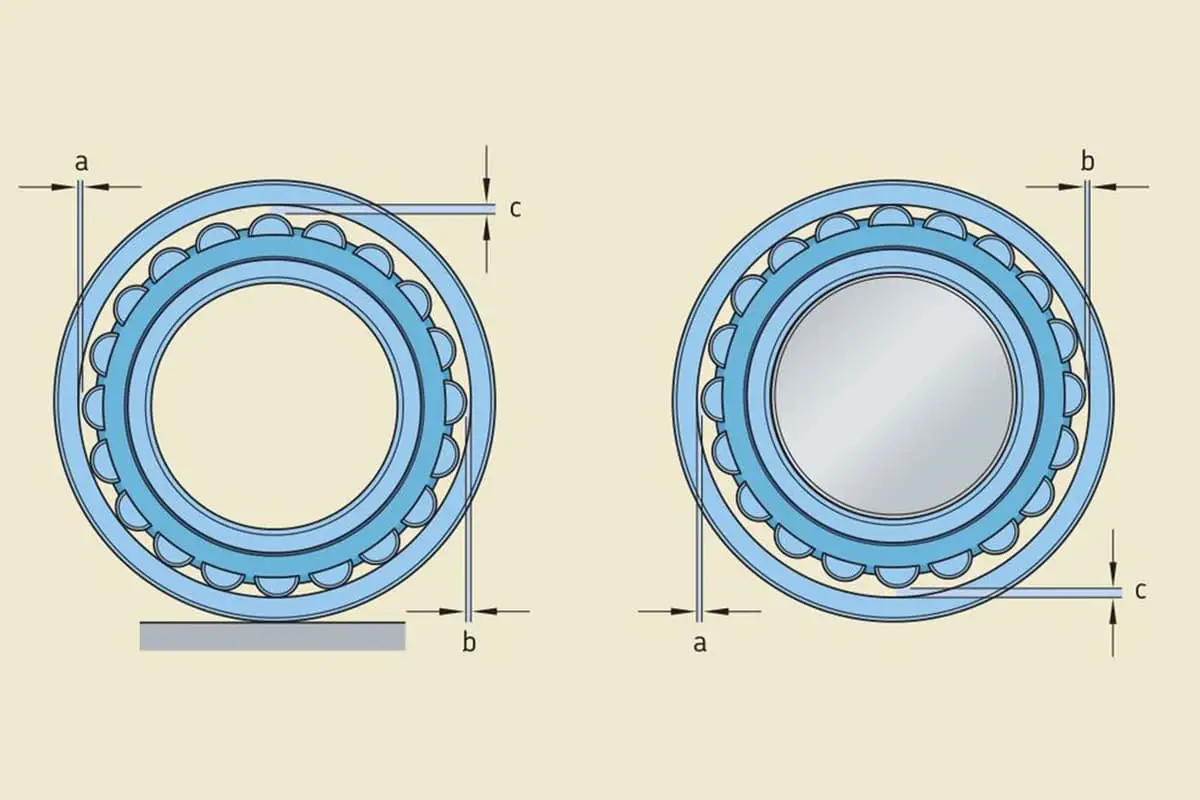
Bearing clearance typically refers to the movement of a ring relative to a fixed ring in the bearing. If this movement is axial, it is called axial play; if it is radial, it is called radial clearance.
The following figure shows the radial and axial clearance of a deep groove ball bearing:
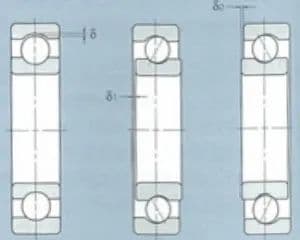
In the figure:
- Bearing radial clearance = δ
- Bearing axial clearance = δ1 + δ2
Clearances for bearings are governed by corresponding national and international standards. For example, the commonly used radial clearance for bearings, GB/T4604-93, categorizes clearances as follows:
- Group 2, a smaller release group than Group 0
- Group 0, the default authorization group
- Group 3, a slack group larger than Group 0
The standard also specifies other slack groups. In practical applications, the most commonly used clearances for industrial engine bearings are from the standard clearance group (Group 0) and Group C3.
Table 1: Radial clearance of deep groove ball bearings (cylindrical bore) – Unit: µm
Nominal bearing inner diameter | Release | ||||||||||
d mm | C2 | Standard | C3 | C4 | C5 | ||||||
To exceed | For | Minimum | Max. | Minimum | Max. | Minimum | Max. | Minimum | Max. | Minimum | Max. |
25 | 6 | 0 | 7 | two | 13 | 8 | 23 | – | – | – | – |
6 | 10 | 0 | 7 | two | 13 | 8 | 23 | 14 | 29 | 20 | 37 |
10 | 18 | 0 | 9 | 3 | 18 | 11 | 25 | 18 | 33 | 25 | 45 |
18 | 24 | 0 | 10 | 5 | 20 | 13 | 28 | 20 | 36 | 28 | 48 |
24 | 30 | 1 | 11 | 5 | 20 | 13 | 28 | 23 | 41 | 30 | 53 |
30 | 40 | 1 | 11 | 6 | 20 | 15 | 33 | 28 | 46 | 40 | 64 |
40 | 50 | 1 | 1 | 6 | 23 | 18 | 36 | 30 | 51 | 45 | 73 |
50 | 65 | 1 | 15 | 8 | 28 | 23 | 43 | 38 | 61 | 55 | 90 |
65 | 80 | 1 | 15 | 10 | 30 | 25 | 51 | 46 | 71 | 65 | 105 |
80 | 100 | 1 | 18 | 12 | 36 | 30 | 58 | 53 | 84 | 75 | 120 |
100 | 120 | two | 20 | 15 | 41 | 36 | 66 | 61 | 97 | 90 | 140 |
120 | 140 | two | 23 | 18 | 48 | 41 | 81 | 71 | 114 | 105 | 160 |
140 | 160 | two | 23 | 18 | 53 | 46 | 91 | 81 | 1130 | 120 | 180 |
160 | 180 | two | 25 | 20 | 61 | 53 | 102 | 91 | 147 | 135 | 200 |
10 | 200 | two | 30 | 25 | 71 | 63 | 117 | 107 | 163 | 150 | 230 |
200 | 225 | two | 35 | 25 | 85 | 75 | 140 | 125 | 195 | 175 | 265 |
225 | 250 | two | 40 | 30 | 95 | 85 | 160 | 145 | 225 | 205 | 300 |
250 | 280 | two | 45 | 35 | 105 | 90 | 170 | 155 | 245 | 225 | 340 |
280 | 315 | two | 55 | 40 | 115 | 100 | 190 | 175 | 270 | 245 | 370 |
315 | 355 | 3 | 60 | 45 | 125 | 110 | 210 | 195 | 300 | 275 | 410 |
355 | 400 | 3 | 70 | 55 | 145 | 130 | 240 | 225 | 340 | 315 | 460 |
Radial clearance of deep groove ball bearings
(1) Round housing hole tolerance – Unit in micrometers (μm) | |||||||||||
Nominal bearing inner diameter | Release | ||||||||||
d mm | C2 | Standard | C3 | C4 | C5 | ||||||
To exceed | For | Minimum | Max. | Minimum | Max. | Minimum | Max. | Minimum | Max. | Minimum | Max. |
– | 10 | 0 | 25 | 20 | 45 | 35 | 60 | 50 | 75 | – | – |
10 | 24 | 0 | 25 | 20 | 45 | 35 | 60 | 50 | 75 | 65 | 90 |
24 | 30 | 0 | 25 | 20 | 45 | 35 | 60 | 50 | 75 | 70 | 95 |
30 | 40 | 5 | 30 | 25 | 50 | 45 | 70 | 60 | 85 | 80 | 105 |
40 | 50 | 5 | 35 | 30 | 60 | 50 | 80 | 70 | 100 | 95 | 125 |
50 | 65 | 10 | 40 | 40 | 70 | 60 | 90 | 80 | 110 | 440 | 140 |
65 | 80 | 10 | 45 | 40 | 75 | 65 | 100 | 90 | 125 | 130 | 165 |
80 | 100 | 15 | 50 | 50 | 85 | 75 | 110 | 105 | 140 | 155 | 190 |
100 | 120 | 15 | 55 | 50 | 90 | 85 | 125 | 125 | 165 | 180 | 220 |
120 | 140 | 15 | 60 | 60 | 105 | 100 | 145 | 145 | 190. | 20 | 245 |
140 | 160 | 20 | 70 | 70 | 120 | 115 | 165 | 165 | 21.5 | 225 | 275 |
160 | 180 | 25 | 75 | 75 | 125 | 120 | 170 | 170 | 220 | 250 | 300 |
180 | 200 | 35 | 90 | 90 | 145 | 140 | 195 | 195 | 250 | 275 | 330 |
200 | 225 | 45 | 105 | 105 | 165 | 160 | 220 | 220 | 280 | 305 | 365 |
225 | 250 | 45 | 110 | 110 | 175 | 170 | 235 | 235 | 300 | 300 | 395 |
250 | 280 | 55 | 125 | 125 | 195 | 190 | 260 | 260 | 330 | 375 | 440 |
280 | 315 | 55 | 130 | 130 | 205 | 200 | 275 | 275 | 350 | 410 | 485 |
315 | 355 | 65 | 145 | 145 | 225 | 225 | 305 | 305 | 385 | 455 | 535 |
355 | 400 | 100 | 190 | 190 | 180 | 280 | 370 | 370 | 460 | 510 | 600 |
400 | 450 | 110 | 210 | 210 | 310 | 310 | 410 | 410 | 510 | 565 | 665 |
450 | 500 | 110 | 220 | 220 | 330 | 330 | 440 | 440 | 550 | 625 | 735 |
For engine engineers, the most commonly used bearing types are deep groove ball bearings and cylindrical roller bearings. If clearances are required for other types of bearings, they can be obtained from the relevant national standards or manufacturers.
How should the clearance of an engine bearing be selected?
Firstly, the bearing clearance values mentioned in the above standards are initial values, i.e. the clearance values when the bearing was not installed or used. When the bearing is installed, put into operation and in operating condition, the clearance value is a critical factor in the operation of the bearing.
Generally, the fit between the internal rotation motor rotor and the bearing is relatively tight, while the fit between the bearing housing and the bearing outer ring is relatively loose. This way, the bearing's inner ring will expand outward, which will reduce clearance. We call this reducing installation clearance.
When the bearing is in operation, there is generally a temperature difference between the inner and outer rings of the bearing, which leads to different degrees of thermal expansion of the inner and outer rings of the bearing, thereby changing the clearance. We call this temperature-driven clearance reduction.
Therefore, the actual working clearance of the bearing is the initial clearance minus the installation clearance reduction and the clearance reduction caused by temperature.
δ work =δ initial –δ install –δ temperature
The service life of a typical engine bearing is related to its operating clearance as follows:
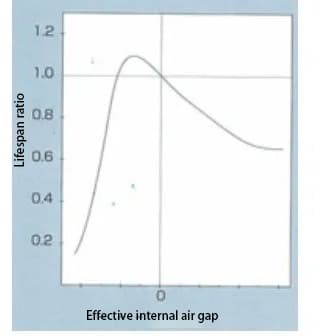
- Vertical Axis: The relationship between the actual life and the expected life of a bearing under various effective clearances (operating clearances).
- Horizontal Axis: The effective clearance (operational clearance) of the bearing.
It is clear that the greatest bearing life occurs when its clearance is less than zero. This implies that, theoretically, when the bearing operating clearance is negative, the bearing life is longer.
However, operating with this clearance value carries a risk. By examining the slope of the curve on both sides, it becomes evident that when the actual operating clearance is less than the clearance at maximum life, the slope of the curve is steep, and with a further decrease in clearance, the life falls. drastically.
In contrast, an increase in clearance results in a much slower decrease in bearing life.
Therefore, if the bearing operating clearance is at the optimum value for maximum service life, any further reduction due to changes in operating conditions will rapidly decrease bearing life. This is what we commonly call a “rolling seizure”.
Considering all this, in real operating conditions, we often choose an operating clearance slightly greater than zero for the bearing. This is a safe value, ensuring that the impact on bearing life, regardless of changes in operating clearance, remains within a controllable range.
Typically, engine engineers opt for Normal or C3 group clearances when selecting bearing clearances. (This is associated with the tolerance setting we normally use and the internal temperature distribution in the engine.)
Of course, if the operating conditions are unique, the bearing clearance value will need to be verified through calculations to ensure that the bearing operates under a safe clearance condition.