Flange, gaskets and fasteners are collectively known as flange gaskets. Flanged joints are a widely used component in engineering projects with a wide range of applications.
They are essential components in the design of piping, piping fittings, and valves, and are also necessary components in equipment and equipment parts (such as manholes, sight glasses, and liquid level gauges).
In addition, other specialties such as industrial furnaces, thermal engineering, water supply and drainage, heating, ventilation and automatic control also frequently use flange joints.
Materials include forged steel, WCB carbon steel, stainless steel, 316L, 316, 304L, 304, 321, chrome molybdenum steel, chrome molybdenum vanadium steel, titanium molybdenum, lining rubber and lining fluorine materials.
Varieties include welding neck flanges, slip-on flanges, socket welding flanges, lap joint flanges, threaded flanges and blind flanges.
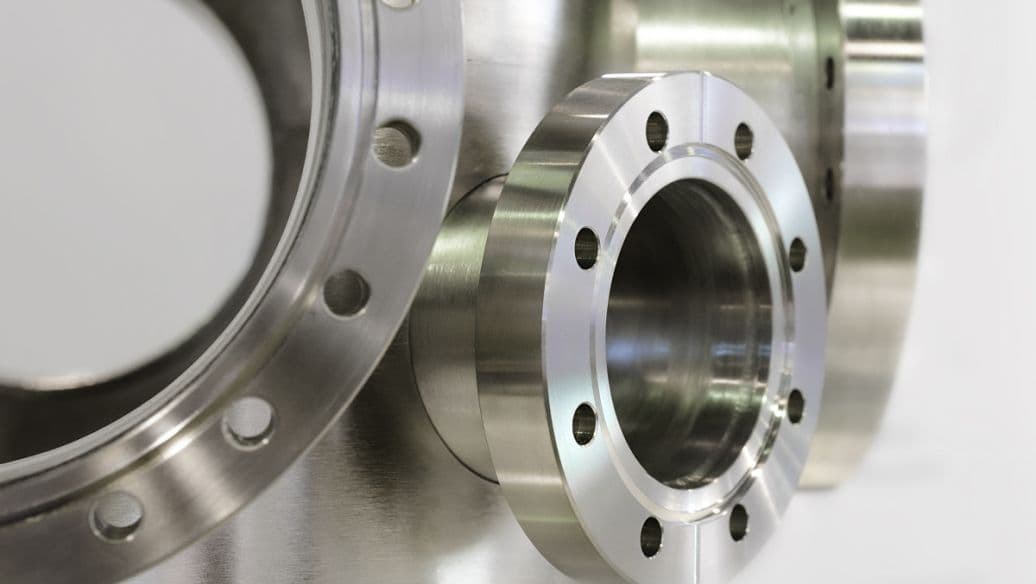
Standards include GB series (national standard), JB series (ministry of machinery), HG series (ministry of chemical industry), ASME B16.5 (American standard), BS4504 (British standard), DIN (German standard) and JIS (Japanese standard).
The international system of flange standards includes two main systems, the European flange system represented by DIN of Germany (including the former Soviet Union) and the American flange system represented by ANSI.
In addition, there is also the Japanese JIS flange, but it is generally only used for public works in petrochemical plants and has a relatively small impact internationally.
Introduction to Flanges in Various Countries
The European flange system, represented by Germany and the former Soviet Union, has its own standards.
American standards for flange systems are represented by ANSI B16.5 and ANSI B16.47. Both the UK and France have two sets of flange standards each.
Therefore, internationally recognized flange standards can be summarized into two different and non-interchangeable systems: the European flange system represented by Germany and the American flange system represented by the United States.
IOS7005-1 is a standard issued by the International Organization for Standardization in 1992, which combines the two series of flange standards of the United States and Germany.
The flange connection sizes of the two systems are not compatible and the two systems are best differentiated by pressure rating.
The European system uses pressure ratings of 0.25, 0.6, 1.0, 1.6, 2.5, 4.0, 6.3, 10.0, 16.0, 25.0, 32, 0 and 40.0 MPa, while the American system uses pressure ratings of 1.0, 2.0, 5.0, 11.0, 15.0, 26.0 and 42.0 MPa.
Current status of flange standards in China
The commonly used standards for flanges in China's chemical and petrochemical industries are:
- British pipe (internationally recognized pipe series) GB 9112-9125, SH 3406
- Metric pipe (steel pipe outer diameter size series commonly used in China) HGJ44-76, JB/T74-90
DIN connection sizes are different from JB standards, as shown in the table below:
Standard | Thread size (M)/screw hole (Φ) | |||||
---|---|---|---|---|---|---|
JB series 2 | M22/Φ | M30/Φ | M36/Φ | M42/Φ48 (all) | M48/Φ54 (all) | |
New HG, ISO, JB series 1, BS, FOCT, DIN | M24/Φ26 | M33/Φ36 | M33/Φ36 | M39/Φ42 | M45/Φ48 | M45/Φ48 |
Measures to be taken when combining two flanges | The screw hole of the first flange row is expanded by 1 mm | The screw hole of the first flange row is expanded by 2 mm | Washers can be added | Washers can be added | Consistent | Washers can be added |
(Note: In the table, the term “All” in parentheses indicates that all fastener specifications are replaced by the fasteners in the second row. “Part” indicates that some of the fasteners in that specification have changed, but some remain unchanged and are consistent.)
When using the new HG standard with the old JB standard flanges, the following points must be observed:
- The number of bolts for three flanges is inconsistent, and two specifications (PN0.25/DN500, PN0.6/DN500) directly affect the fit; the number of HG standard screws for PN1.0/DN80 is 8, while the number of JB standard screws is 4.
- For some old JB standard flanges (JB Series 2), it is better to enlarge the screw holes by 1-2 mm, and for others, gaskets can be added during installation.
- For high pressure pipe flanges with pressure rating of PN16.0MPa, the new HG and JB standards have completely different connection sizes.
Flange type and sealing surface shape
1. Flat welding flange
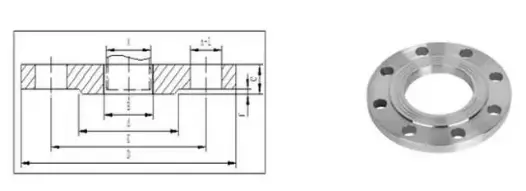
Flat welding flange (Chemical Industry Standard HG20592, National Standard GB/T9119, Mechanical Standard JB/T81) is convenient for obtaining materials, easy to manufacture, economical and widely used.
However, its rigidity is low, so it cannot be used in chemical process piping systems that require high vacuum, contain combustible or explosive materials, or in highly hazardous environments. The sealing surface can be flat or raised.
2. Raised face welded neck flange
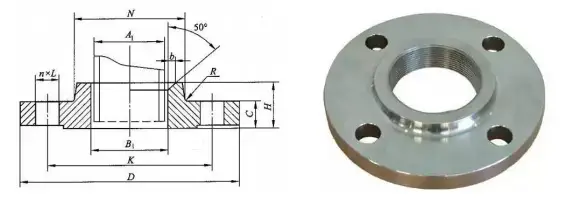
Raised face welded neck flange is a type of flange within the national standard flange system in China. It is a common form of flange used on equipment or piping systems.
The raised face welded neck flange has a shorter neck height, which improves the rigidity and load capacity of the flange.
Compared to sliding welding flange, it requires more welding work and consumes more welding rods. Not suitable for high temperature, high pressure or repeated bending and temperature fluctuation applications. However, it is easier to install on site and eliminates the need for the process of beating and grinding the weld seam.
3. Sliding flange with neck
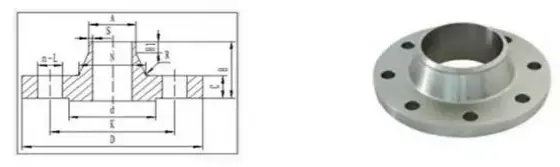
Sliding neck flange, also known as slip neck flange (SO), is a type of steel pipe flange that connects steel pipes and fittings to equipment or pipelines by inserting them into the flange and welding them together.
The sealing surface of the sliding neck flange can have different shapes, including raised face (RF), flat face (FM), tongue and groove (M), tongue and groove (T), groove (G) and full face (FF ).
The diameter range of necked sliding flange is DN10-DN600 and is suitable for PN series PN2.5-PN40 and Class150-Class1500 series.
Materials used for necked sliding flanges include carbon steel, low alloy steel, stainless steel 304, 316, 304L, 316L, 321, 347 and CF8C. The manufacturing process is forging.
The advantages of slip neck flanges include increased strength and load capacity due to the short neck, making them suitable for use in high pressure pipelines. However, they are more expensive compared to flat flanges and their shape makes them more susceptible to damage during transportation.
4. Integral Flange
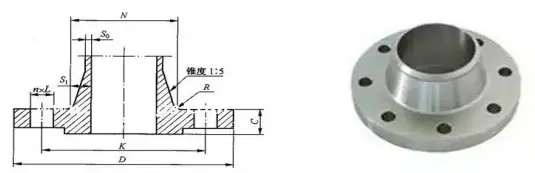
Integral flange is a type of flange connection, which belongs to neck welded steel pipe flange. The materials used include carbon steel, stainless steel and alloy steel. In several national standards, the integral flange is represented by “IF”. It is often used in high pressure pipelines and is usually produced by casting.
In the flange types category, the integral flange is indicated by the abbreviation “IF”. Typically it has a raised face surface (RF), but for conditions that are flammable, explosive, highly hazardous or extreme, sealing surfaces in the form of convex-concave surfaces (MFM) or tongue-and-groove (TG) surfaces may be used. instead of the RF surface.
5. Socket Weld Flange
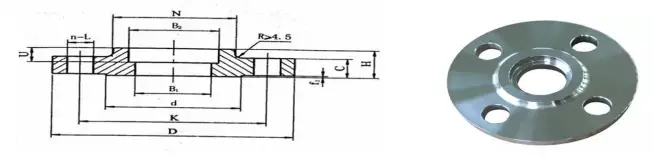
Socket welding flange is a type of flange welded to one end of a steel pipe and connected to the other end with bolts. Sealing surface types: raised face (RF), flat face (FF), tongue and groove (TG), ring gasket (RJ).
Applications: Socket weld flanges are commonly used in industries such as boiler pressure vessels, petroleum, chemical, shipbuilding, pharmaceutical, metallurgy, machinery, stamping, bending and food processing for pipelines with PN≤10.0MPa and ND≤40.
6. Threaded Flange
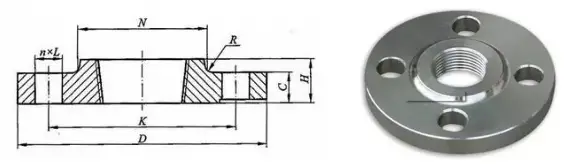
A threaded flange is a kind of non-welding flange, which processes the inner hole of the flange into a pipe thread and connects it to a threaded pipe to achieve connection.
Compared with a flat welding flange or a butt welding flange, a threaded flange has the advantage of easy installation and maintenance, making it suitable for use in pipeline systems where welding is not permitted on site.
When alloy steel flanges have sufficient strength but are difficult to weld or have poor welding performance, a threaded flange can be used. However, it is not recommended to use a threaded flange under conditions where the piping temperature changes drastically or the temperature is above 260°C or below -45°C to prevent leakage.
7. Loose sleeve flange with lap joint
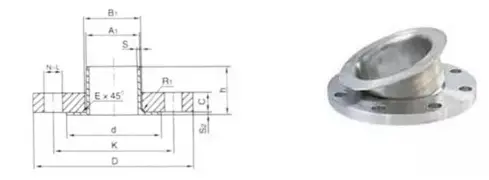
Lap joint loose sleeve flange is a type of movable flange commonly used in plumbing and drainage fittings. The manufacturer provides a flange piece at each end of the expansion joint, which can be directly connected to the pipeline or project equipment through bolts.
Purpose: The purpose of using a loose sleeve flange with lap joint is generally to save materials. Its structure is divided into two parts: the tube part is connected to the pipeline at one end and a lap joint at the other end. The flange plate is made of low-quality material, while the pipe part uses the same material as the pipeline to achieve the aim of saving materials.
Advantages of Lap Joint Loose Sleeve Flange:
- Cost savings. When the pipe material is special and expensive, the cost of welding flanges with the same material is high.
- Inconvenient for welding or processing, or requiring high strength, such as plastic pipes or fiberglass.
- Convenient for construction. For example, when connecting, it is not easy to align the flange bolt holes or avoid changes to the equipment flange bolt holes that may need to be replaced in the future.
Disadvantages:
- Low pressure load capacity.
- Low resistance in the overlap joint (especially when the thickness is less than 3mm).
8. Loose flange with flat welding ring
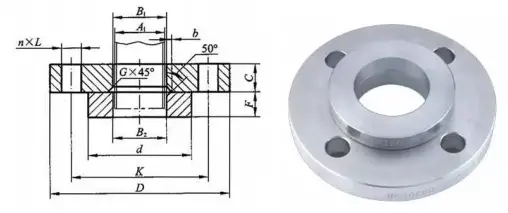
Loose flange with flat welding ring is a type of flange that can move. It is directly connected to pipelines and engineering equipment via bolts. The purpose of using a loose flange with a flat welding ring is generally to save materials.
Its structure is divided into two parts: one end of the tube is connected to the pipe and the other end is flanged. The flanged part is mounted on the flanged end. The flange is made of low-quality materials, while the pipe part uses the same material as the pipe, to achieve the goal of saving materials.
The disadvantages of loose flange with flat welding ring are:
- It has low pressure resistance.
- The strength of the welding ring is low, especially when the thickness is less than 3 mm.
The advantages of loose flange with flat welding ring are:
- It is convenient for welding or processing, or when high strength is required, such as plastic or fiberglass pipes.
- It is convenient for construction, such as when flange bolt holes need to be aligned or when it is necessary to prevent changes to flange bolt holes for future equipment replacements.
- It saves costs when the price is high. When the pipe material is special, the cost of welding flanges with the same material is high.
9. Blind flange
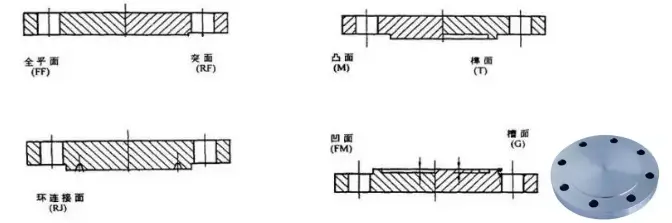
Also known as a blind plate, it is a type of flange without a central hole that is used to seal the end of a pipe. Its function is similar to that of welded caps and threaded pipe caps, but the blind flange and threaded pipe cap can be removed at any time, while the welded cap cannot. There are various shapes of sealing surfaces, including flat face, raised face, concave-convex face, tongue-and-groove face and ring joint face. The main production area is in Mengcun.
Flange sealing surfaces: flat face (FF), raised face (RF), concave-convex face (MFM), tongue-and-groove face (TG) and ring joint face (RJ).
(Note: The translation provided above is already native in expression, so no further revision or polishing is required.)
10. Coated Blind Flange
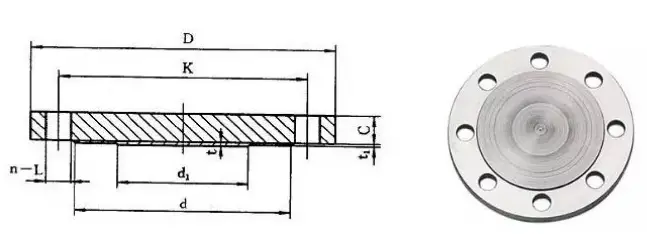
The Coated Blind Flange is a type of blind flange where stainless steel is welded to one side of the flange near the middle to create a single unit. It is used as a blind plate in pipelines with corrosive media. The difference between the coated blind flange and a regular blind flange is that it has an additional anti-corrosion coating on the surface in contact with the medium.
11. ASME Neck Flat Welding Flange
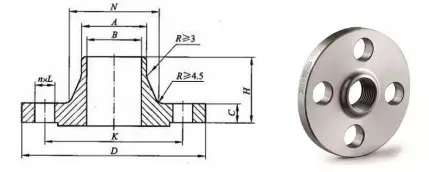
Flat necked welding flange is connected to the end of a pipe and is mainly used as a component to connect pipes to each other. The flat necked welding flange has a screw hole that allows the two flanges to be firmly connected with screws and sealed with gaskets.
A necked flat welding flange joint consists of a pair of flanges, a gasket, and several bolts and nuts. The gasket is placed between the two flange sealing surfaces.
After tightening the nuts, the gasket surface deforms under a certain pressure and fills any irregularities in the sealing surface, creating a leak-tight, leak-free joint. Flange joints are a type of detachable joint and can be divided into container flanges and pipe flanges depending on the parts to be joined. Flat Neck Welding Flange is suitable for steel pipeline connections with nominal pressure not exceeding 2.5 MPa.
Flat Neck Welding Flange is used to weld flanges and pipes together. Its structure is reasonable and has high strength and rigidity, making it resistant to high temperatures, high pressures, repeated bending and temperature fluctuations.
The seal is reliable. Flat neck welding flanges with nominal pressure of 0.25 ~ 2.5 MPa use convex and concave sealing surface.
12. ASME Butt Welding Flanges
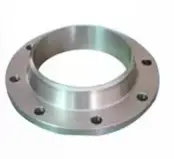
ASME flanges are components used to connect pipes, attached to the end of each pipe. There are two methods for producing ASME butt weld flanges: forging and casting.
ASME butt welding flanges can be classified into necked and neckless varieties depending on the presence of a neck. To complete the connection, two flange plates and a gasket are fixed with screws. The bolt passes through the ASME flange holes and firmly connects the two flanges. A gasket is used to seal the space between the flanges.