Aerospace fasteners are probably one of the most underrated components in the aviation industry. While they may not be in the spotlight, they play a crucial role in keeping a plane in the air.
An interesting note highlights this point: an airplane has about 1 million fasteners!
Now that we know how important they are, we can enjoy this discussion of fasteners even more. In this article, we will look at the different types of aviation fasteners and their requirements.
What are aerospace fasteners?
Fasteners in the aerospace industry are used to connect various components of the aircraft fuselage. Its function is crucial not only for performance, but also for passenger safety. Think of the devastating consequences if an engine fails or a door opens during flight – negligence is not an affordable luxury for aerospace engineers, even when it comes to fasteners!
The aerospace industry includes a wide range of products such as commercial aircraft, military aircraft, spacecraft, and even rocket technologies. Consequently, the topic of aircraft fasteners covers this entire range of applications.
Furthermore, they must be designed specifically for the intense and versatile environments in which they are used and are quite different from the usual fasteners with which we are generally familiar. We will now discuss all these points in detail.
Desired Properties for Aircraft Fasteners
As highlighted above, aerospace fasteners must have excellent physical properties. The most important requirements are:
High strength
Airplanes are subject to enormous stresses and strains during their operation. Fasteners must have high tensile and shear strength to withstand these loads. As dynamic loads such as turbulence frequently occur, good fatigue resistance is also an important prerequisite.
Thermal resistance
Spacecraft and military aircraft are exposed to extreme temperatures that can lead to thermal failures. Fasteners must be able to maintain their performance under such conditions.
Corrosion resistance
There is generally a general requirement to operate aircraft in wet environments.
Light
As mentioned above, an average aircraft can have over a million fasteners. While a single clasp may not seem that heavy, a million of them certainly weigh a lot. Therefore, lightweight fasteners are very important to the performance and efficiency of an aircraft.
Common Standards for Aerospace Fasteners
Standardization efforts in the aircraft fastener industry date back to the World War II era, when many of these developments in the aviation industry began.
Some of the most well-known industry standards are briefly highlighted below.
SAE AS9100 is one of the oldest families of standards in the aviation industry. It is involved in the design, development, production, installation and maintenance of aerospace components, including fasteners.
ISO/TC 20/SC 4 is an ISO technical committee specifically concerned with aerospace connection systems. Its standards provide detailed information on connection designs and materials.
General Aerospace Fasteners
Some types of aircraft fasteners work in the same way as the general-purpose fasteners we use in our daily lives. We'll cover this before moving on to specialty fasteners designed specifically for the aerospace industry.
Aircraft Bolts
Aircraft screws are externally threaded fasteners used for non-permanent connections. They offer excellent clamping strength and resistance to dynamic loads. In the aerospace industry, they are usually made of high-strength steel or aluminum alloys coated with corrosion-resistant materials.
Airplane nuts
Aircraft nuts are the female counterparts of bolts or nuts. Therefore, they have an internal thread. The properties of their materials must match those of their counterparts.
In addition, they also have features such as self-locking and sealing, essential for aerospace structures that are subject to high vibrations during flight.
Aircraft screws
Screws are the most common fasteners in aerospace structures. Like screws, they also have external threads, but the threads are more pointed, burr-shaped and have a taller spiral. Several categories of screws with different materials, coatings, screw heads and designs are used in aircraft assembly.
Construction screws have similar tensile and shear strengths to screws and are ideal for heavy-duty applications.
Machine screws are also used in aircraft assembly. They are available with different head shapes like round head, flat head, countersunk head, etc.
Aircraft rivets
Aircraft rivets are pin-like structures that are plastically deformed at one end to create a permanent connection. They are most commonly used to join the metal sheets that make up an aircraft's fuselage. They provide strong support and are a relatively inexpensive option among aerospace fasteners.
Special fasteners for the aerospace sector and its applications
Aircraft fasteners have highly specialized applications and standard designs are not sufficient in many cases. Therefore, engineers have developed several innovative designs to deal with such applications.
Blind screws/rivets
Blind screws and blind rivets are extremely useful when one side of the connection is inaccessible. Therefore, they are often found in hard-to-reach places on planes. This is also the reason for the “Blind” in his name.
The fastener is inserted into the hole and tightened. With blind rivets, the rivet head plastically deforms to ensure stable fastening. Blind screws are tightened into a pre-positioned collar that expands into the hole and holds the assembly in place. Blind fasteners provide excellent strength and vibration resistance.
lock screw
Lockbolts, or Huck Bolts as they are sometimes called, are a unique mix of screws and rivets. They consist of two parts, one of which is very similar to a regular screw. At the other end, special collars are used that are pressed into the grooves of the lock screw shaft or tightened onto its threads to form the connection.
In some cases, a weaker section is machined into the pin and the additional protruding part of the shaft is removed after assembly.
Lockbolts are easy to install and provide good clamping strength. Therefore, they are a lighter alternative to other common aerospace fasteners. They are also used in the assembly of structural components in landing gear, wing connectors, etc.
Hi-Lok Pens
Hi-Lok screws are two-part fasteners consisting of a grub screw and a collar. Its distinctive feature is the ability to maintain a constant preload, which is achieved by releasing part of the pin at a certain preload value.
The uniform pretense makes them reliable and allows for smooth quality control. Furthermore, they have good resistance and durability.
Twist lock
Turnlocks are innovative aircraft fasteners that create a non-permanent connection. They are mainly used to protect doors, control panels and other similar components in aircraft fuselages.
Its particular advantage lies in the quick and easy dismantling of the assembled components, which is done simply by loosening the respective screw.
Adhesive fasteners
These are unconventional fasteners that do not require drilling. Instead, they adhere to surfaces using high-performance aerospace adhesives and feature anchors/hooks to connect components.
They are not as strong as the mechanical fasteners discussed above, but they serve their purpose for low-intensity connections. Its common applications include cable management and sheet metal joining.
Materials available for aerospace fasteners
Aerospace fasteners must withstand extreme operating conditions and must be able to maintain performance throughout their service life. We discuss the desired physical properties of aerospace fasteners.
Now let's take a look at the materials commonly used in its manufacture.
aluminum
It is a classic aerospace material due to its low weight, good strength-to-weight ratio and corrosion resistance.
Aluminum alloys are often strengthened through heat treatments and coatings. For example, the T6-AI70xx series is commonly called “space grade” in most industries due to its composition and heat treatment. Aircraft fuselages are generally made of aluminum alloys.
steel
Different types of steel are often used to produce fasteners. They give connections high strength and durability.
However, steel is generally heavier than materials like aluminum or titanium and requires certain treatments to make it resistant to heat and corrosion.
However, it is certainly a popular group of materials when it comes to aircraft fasteners.
titanium
Titanium alloys are stronger than steel but much lighter. They also have good thermal stability and corrosion resistance.
These properties make it an ideal choice for fasteners. However, the only reason that inhibits its widespread use is its high price. For this reason, they are only occasionally used as replacements for aluminum and steel fasteners for special applications.
Special leagues
The aerospace industry is widely considered to be one of the most innovative industries in terms of product development. This reputation is due in part to their significant contributions to the advancement of materials science.
There are numerous special alloys that outperform the materials discussed above. They have greater resistance, lower weight, better thermal stability and longer service life.
Common specialty alloys used in aerospace fasteners include nickel and chromium. Inconel, NIMONIC, Waspaloy, Hastelloy etc. They are some of the most used special alloys today.
Aerospace vs. Aerospace Fasteners commercial fasteners
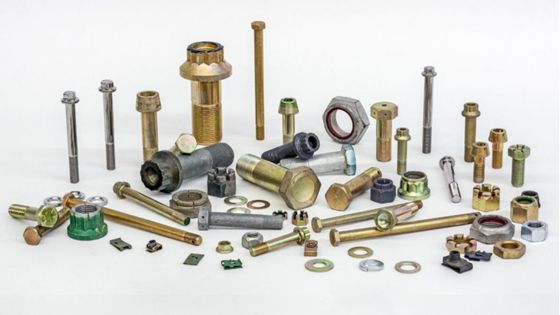
Although aerospace fasteners appear similar to commercial-grade fasteners, they are far superior in terms of performance characteristics. A plane with commercially available fasteners is unlikely to stay in the air for more than a minute.
Below are the main differences between the two types of fixings.
material : Fasteners used in the aerospace industry are made from high-quality steel, while commercial-grade fasteners are generally made from low- to medium-carbon steel.
Strength : Fasteners on aircraft are heat treated and have a tensile strength greater than 800 MPa. In comparison, commercially available fasteners are typically less than 400 MPa.
Material properties : Fasteners on aircraft undergo special treatments to make them more resistant to heat, corrosion and vibration.
Self-locking : As aircraft are subject to strong vibrations, there is a risk of fasteners coming loose. To prevent this, most aircraft nuts and bolts have a self-locking mechanism. On the other hand, commercially available fasteners are generally not self-locking.
Cost : Due to additional features, aerospace fasteners are understandably more expensive than commercial fasteners.
WayKen provides precision machining services for your fasteners
With a team of experts and extensive machining experience, our manufacturing standard can meet our customers' requirements for aerospace fasteners and various precision machined parts. Contact us today for an instant quote and receive DfM feedback. You will receive individual support and a competitive price.
Concluding
Aerospace fasteners are an essential part of any aircraft. They hold the various parts of the aircraft together and ensure that they function properly. Many different types of fasteners are used in aircraft construction and each has its specific purpose. We hope this was an informative read and answered your questions about aircraft fasteners.
Common questions
What material are shutter covers made of?
Covers must protect fasteners from extreme operating conditions. Therefore, they are made of materials such as black oxide, cadmium, zinc, nickel and phosphate.
What surface finishes are optional for aircraft fasteners?
Fasteners can be coated to obtain numerous properties. There are optional surface finishes and coatings for properties such as anodizing, painting and galvanizing, which can improve corrosion resistance, high temperature resistance, wet sealing and aesthetics.
What hole fit tolerances are appropriate for aerospace fasteners?
The hole tolerance range depends on many factors, such as the type of fastener, its material, joining material, working conditions, surface coating, etc. Typically loose fits are used for rivets, while bolted connections have a tighter transitional fit.
1 comment
Srs(a). bom dia !
Poderia cotar o item abaixo, preço e lead time por favor !
• MFPN4-40SCL – PORCA FRENO ENCALCAVEL 4-40, LA 660 – 200 UNIDADES
SDS.