Thread cutting is one of the most important machining processes. It is used to create screw threads used to fasten materials and components to each other.
Tapped holes are widely used in manufacturing. Their versatility and ease of use make them so versatile that they can be found in everything from cars to planes.
However, cutting wires is not as easy as we think. Therefore, it is important to know the different threading machine technologies available so that you can make the best choice for your projects. The following information will help you better understand wire cutting.
What is a tapped hole?
A tapped hole is a hole that has an internal thread. It is a circular hole used for threading and drilling operations. To drill threads into the hole walls, you can use the tapping method. It occurs in areas and places where nuts and bolts don't work, such as metals.
Tapped holes are sometimes also called tapped holes. This type of hole is used when two parts need to be connected using a fastener such as a screw or bolt. The threads in the hole provide strength so the fastener does not loosen over time and also make it easy to remove the fastener if necessary.
What is a tapped hole?
Tapped hole is a type of hole used to make internal threads. It is made by making a hole in the material and then using a tap to cut threads into the walls of the hole. Threaded holes are often found in metal components that need to be connected together, such as nuts and bolts.
The tapped hole has many similarities to a pilot hole. Both are used to drill a thread into a workpiece so that a screw or stud can be inserted. A key difference between the two is that a tapped hole is already tapped and requires only a tool to create the appropriate thread, while a pilot hole must first be drilled before it can be tapped.
The importance of drilling a tapped hole
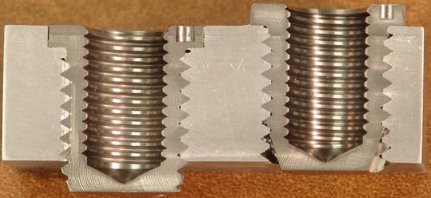
Tapped holes are an essential aspect of machine parts and you can use a CNC machine to add a hole. Thread cutting allows you to create threads in the walls of the drilled hole. Machine screws cannot create their own threads. If you want to screw a screw into a metal material, you will need a threaded hole and add threaded features to a CNC machine process.
Each feature is added to the threaded parts accordingly, and most threads can be selected according to the feature. We will explain why it is important to create a tapped hole.
1. Connection
If you want to screw a screw or screw into metal, you can connect two parts more reliably. Threading allows you to permanently connect a bolt, nut, or screw to a metal.
2. Easy transportation
A threaded hole makes it easier to assemble small parts and products for shipping, significantly reducing labor costs.
3. Easy to use
Provides space for screw caps and threaded holes. You can more easily screw a screw or stud into metal without drilling a pilot hole.
You can create threads on the inside of the hole and it takes less time than drilling a screw, nut or screw into wood. Drilling a hole can meet your project needs, whether you need a through hole or a blind hole.
How do you drill a hole before tapping?

When drilling, the holes must be straight, good and the correct size so that the thread can be cut. In modern machines, the drilling factor (oversizing) is usually eliminated, but it is of great importance in drilling. Therefore, it is important to consider how the hole will be drilled before threading.
A tapped hole was formed using a tap and drill. A pilot drill bit can drill the first hole, while a tap is mainly used to cut the threads in a tapped hole. After inserting a screw, its external thread (male thread) can be transformed into an internal thread. Internal threads can create a thread in a tapped hole.
Some machinists still use the old rules and patterns and drilling tables for tapped holes. An example of threading is using 17/32 dies and 5/8-11 taps. These thread percentages sometimes make the job more complicated. Therefore, it is necessary to clearly understand the thread pattern and the use of various threading tools before drilling the hole.
Before drilling a tapped hole, you can choose between different sizes for the pilot drill and tap. Find a professional who knows threading and understands that different thread sizes can make a big difference in your project.
What are blind and through holes?
There are two types of holes for defining tapped holes. Each hole type requires special considerations to ensure that tapped holes are easy to machine.
blind hole : This hole has a certain depth and cannot pass through the entire piece. Depth must be specified separately. The bottom of the hole may end in a flat surface or a cone.
Through Hole or Through Hole : With a through hole, a hole can pass through the entire workpiece. The depth of a through hole is the thickness of a given wall. When using a bolt, screw and nuts, you should use a through hole to make the process easier.
What are the differences between drilling and tapping?
The main difference between drilling and tapping is the order and execution of the functions and the drill. In this process, a smooth, round hole is first made with a drill. This is called drilling.
The formation of a threaded hole is completed with a tap and a drill, where the pilot drill first forms the hole and then a tap can be used to cut the thread. Taps can process most types of materials such as aluminum, alloy steel, steel and cast iron.
In this process, a round and smooth hole is made, while on the other hand, when drilling a hole, a thread is cut by placing a tap inside the hole.
In addition to these methods, creating threads on the outside of a cylindrical object can be done using a punching tool. A screw thread is an example of a punching tool.
Three types of threading taps
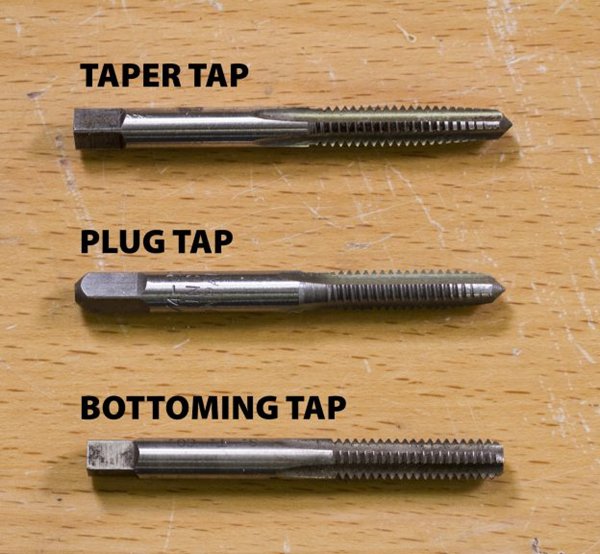
The main types of taps are finishing taps, tapered taps, and bottom taps.
These types are used and designed to serve a specific function or purpose and can be targeted to any hole in them.
Conical faucet
A cone has a tapered tip and a slight angle to the thread, also known as a chamfer. Typically, the first seven to ten strands are not fully formed. The tapered angle of the thread makes it much easier to drill the thread than with a floor cutter. This type of tap is generally used to tap a new thread into a hole.
If the hole to be threaded is very large or the material is very hard, the use of a threader is not recommended. In these cases, it is best to use a twist drill. Pre-cutters are also not recommended for blind holes (holes that do not go through the entire material).
Drain taps
Taps are an intermediate form of conical tap and sub-tap and are therefore also called “second tap”. However, taps require more force to turn because they cut multiple wires at the same time.
Faucets are the best example of thread repair that requires small fixings. They are perfect for drilling deeper holes than tapered drill bits.
In some cases, using a tap is not recommended. An example of this is when the hole where the line is cut is very close to the edge of the material. The faucet can easily break if it touches the edge during use. Additionally, using a tap on very small diameter holes can be difficult and may break the tap.
Turn down the tap
The bottom tap is a type of tap that starts at the bottom of the hole. It is used when there is not enough space to start the tap from above. Under tapping allows threads to be cut to the bottom of a through hole. This type of touch is also useful for correcting mistakes made when playing from above. It is mainly used for:
Poking or hitting a shallow blind hole
Deep thread and shallow hole
Drill a new hole
A floor faucet is a specialized tool and may not be available in all sizes. Therefore, it is important to check this before starting a project.
Tips and advice on tapped holes
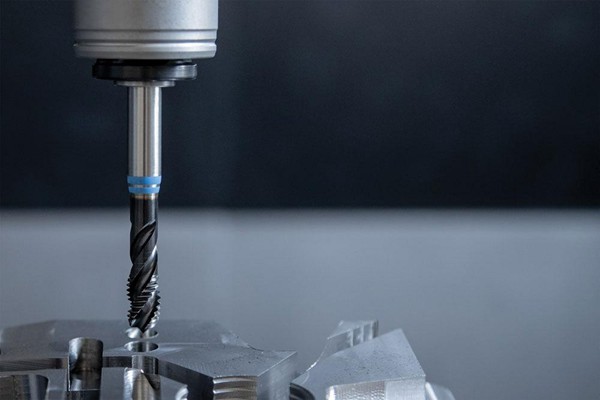
Threaded holes are considered essential for the addition of parts mechanically fixed using machines. If you try to add them the wrong way and create waste, you can seriously damage your CNC machined parts. Therefore, careful consideration and planning before machining a tapped hole is essential and will help avoid unnecessary problems.
1. Methods of making threaded holes: cutting and forming
You can insert an internal thread into tapped holes in two ways:
using a form touch
through the use of a cutting tool
Although both methods produce the same result, it is necessary to consider some factors when choosing either method, such as: B. the size of the threaded hole, the lathes, the hardness of the material and whether it is a blind or through hole.
1: Thread hole size – You can use a mold tap or a traditional cutting tap if the thread hole size is up to M6. You can use a single edge tool to cut the thread hole larger than M6. Because to make threaded holes you need a larger tap to get more performance from the machine.
2: For hard materials – You can use a cutting tap for hard and tough materials. The flutes of the cutting tap ensure that the lubricant can flow along a path and that the metal chips have more space to cut.
3: For soft materials – Use mold cores for soft non-ferrous metals such as brass, lead, steel and aluminum. Molded taps can drill internal threads in softer metals without breaking. This is because the cutting process is slower and more controlled, which helps prevent damage to the material.
2. Use standard thread sizes when possible
The size of the threads used in CNC machines is of great importance. It has a huge impact on the entire editing process. You should try to use standard size lines whenever possible.
There are a few common thread sizes, including 1/4-20, 3/8-16, and 1/2-13. Each of these sizes corresponds to a different diameter and pitch, ensuring that the threads fit correctly into the desired object. There are also metric thread sizes. The most common metric sizes are M6 x 1.0, M8 x 1.25 and M10 x 1.5.
The machining process does not require any special machining tools or materials when standard thread sizes are used. Furthermore, it helps reduce processing time and material consumption, making it a cost-effective process.
3. Suitable thread diameter
You must ensure that the threaded hole diameter is within the part or workpiece. The outer diameter of the threaded hole must be larger than the inner diameter. This means that the inner diameter is smaller than the outer diameter.
Thread breakage can occur from the side of the part if the thread hole is close to the edge of the part. Thread breakage can cause the cutting tool or tap to break, thus destroying the surface finish.
4. Consider angular surfaces
It can be difficult to machine threaded holes in angled surfaces. You can insert a threaded hole into an existing angled surface by milling pockets to create a flat surface. The tapped hole is added from this flat surface.
However, if there is no angled surface, you must first add a tapped hole to the part before machining the angled surface. You need to make sure the depth of the threaded hole is as designed after adding the angled surface.
5. Types of threaded holes
Threaded holes are divided into two types. Both hole types require special considerations when designing the part. This is done to ensure the machining of both threaded holes.
Additionally, this also prevents the threaded holes from colliding with other parts. The main types of threaded holes are:
Blind hole thread
Threaded blind holes do not go completely through a part, but only through certain parts. Blind holes end after reaching a certain depth. When a tapped hole is created with an end mill, the hole may end in a flat surface. If the hole doesn't go all the way through the material, you know it's a drilled hole. However, if it is created with a traditional cutter, it may end up tapered. If the entire thread needs to be extended to the bottom of the tapped blind hole, this will be done using a bottom tap.
Sizing a Blind Hole
To specify the blind hole, the diameter of the hole is specified. Sizing is also necessary to control depth. To check the depth, the remaining amount of material is specified or the hole depth is specified directly.
Through the wire
The through hole completely passes through a part. Threaded holes are present on both sides of the part or part. The thickness of the part is determined when the cutting tool or threaded hole cannot thread the entire deep hole.
If the threaded hole or cutting tool is insufficient to cut a thread on one side of the hole, you will need to consider the following options.
Continue adding lines as long as the cutting tool or tap allows. You should notice that there is no thread in part of the hole.
Continue adding lines on both sides until the cutting tool or tap allows. Note that the threads on both sides may not be aligned.
6. Depth of the hole
Deep tapped holes present unique machining challenges compared to shallower tapped holes. The greater thread depth creates longer contact time between the tool and the workpiece, which generates more heat and requires greater cutting force. These factors increase the risk of tool breakage when machining deep threaded holes. To overcome these challenges, special care must be taken in the selection and use of cutting tools, and the machining process must be closely monitored to ensure that tool breakage does not occur.
Concluding
When it comes to threaded holes, it is important to fully understand the manufacturing process. This way, you can ensure that the parts you manufacture are of high quality. Although it may seem a little complicated, it is best to consult experts in threading techniques.