The shaft machining process is an efficient method for producing long, cylindrical engine mechanical components responsible for transmitting power and torque within the devices. These precision shafts come in various designs and are necessary components commonly used in diverse applications and industries, from construction to industrial machinery.
However, it is important to understand everything about shaft machining because each machined shaft must meet the specific requirements of the intended application. This article explains what a machined shaft is and how to process custom machined shafts. You will also learn more about the techniques and considerations for effective shaft machining.
What is a machined shaft?
A machined shaft is a cylindrical or round mechanical part that transmits rotational motion and power between various machine components. Depending on the requirements of the intended application, these machined shafts are often made from metals such as aluminum, titanium, steel or stainless steel.
These shaft parts are important for transmitting rotational force and torque within machines, ensuring smooth operation and greater efficiency. Furthermore, the customized shaft can ensure better performance and functioning of a machine in the intended applications.

How are individually manufactured shafts processed?
Custom shaft manufacturing involves a series of processes that can achieve desired dimensions, precision and surface finish. Therefore, it is best to determine the intended application, working conditions and design requirements to produce functional custom shafts. Here you will find the steps to process custom machined shafts.
Design and programming
The first step in custom shaft production is design and programming. You need to decide the shaft material, diameter and length specifications. You then use CAD software to create a CAD (Computer Aided Design) file for your individually manufactured shaft.
Then, using the CAM (Computer Aided Manufacturing) software package, create toolpaths for the CNC machine according to the requirements of the spindle parts. To do this, you must develop a CNC program (a set of machine-readable instructions known as G-Code) using CAM software. Then load it into the CNC machine controller to control the machining process.
Machine Setup
When setting up a CNC machine to make shafts, you need to select the appropriate machine type, such as: B. a milling machine or a lathe. Then prepare the workpiece and select the correct cutting tool, such as: B. End mills or turning tools. Also, make sure the workpiece is firmly fixed with suitable accessories and use sharp cutting tools.
Shaft Machining Process
It would be best to use CNC machines to cut the custom shafts to your desired specifications. Machinists often use the CNC turning process because of its versatility and high precision when machining cylindrical components such as custom shafts. The cylindrical shaft is rotated while the cutter removes material. However, processing steps must be monitored and machined shafts must be checked to ensure quality.
Surface finishing
After producing your custom shafts, you can choose from a variety of compatible surface treatments. These surface treatments are designed to improve the functionality and appearance of machined shafts and ensure they meet the requirements of the intended application. Sandblasting, anodizing, and passivation are typical examples of compatible surface treatments for custom shafts.
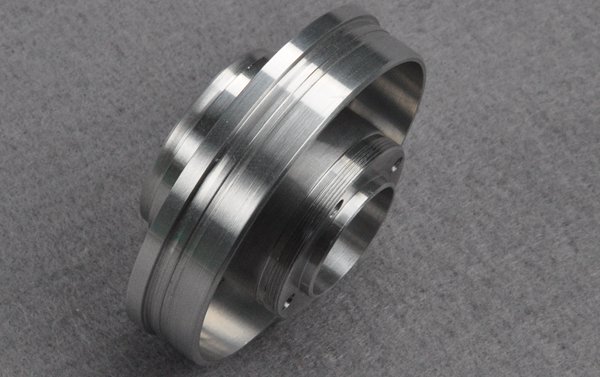
Types of machined shafts and their uses
There are different types of machined shafts, each with different load capacities, speed and use. Common types of waves and their uses include:
Hollow shafts
Hollow shafts usually have a central hole or cavity through which fluids, wires, and other components can pass. Unlike similarly sized solid shafts, they are generally lightweight. Hollow axles are used in racing vehicles and aircraft to save weight. They are also used in transportation systems, pumps and medical devices.
Threaded shafts
These machined shafts have cut internal or external threads that match the threads of a mating part, such as a nut. This type of connection is often found in applications that require frequent attaching or disconnecting, such as electrical or plumbing work. Threaded shafts are also used in lead screws, lead screws, and clamping mechanisms.
Key axes
A keyed shaft is a machined shaft with a keyway used to secure components such as sprockets, pulleys, or gears. Machined keyways are the same width as a diffusion key. The keyway receives the keyway and engages the corresponding teeth of the other component to prevent it from rotating independently or slipping. Key shafts are ideal for maintaining a connection in high torque applications such as motors and pumps.
Splined shafts
These machined shafts have longitudinal grooves or splines machined along their length, which mate with corresponding splined shafts machined into a corresponding component, such as a pulley or gear. This is a strong form of connection that allows for continuous energy transfer as there is no relative movement between the two parts. They are often used in applications that require precise positioning or torque transfer, such as: B. vehicle transmissions or toothed clutches.
Conical waves
A tapered shaft gradually decreases in diameter along its length. Tapered shafts are often used in applications where components such as automotive wheel hubs, pulleys or gears must be securely mounted.
Techniques for producing precision shafts
Manufacturers often use several techniques when precision machining shafts to achieve desired tolerances and surface finishes. Here are the common shaft manufacturing processes.
CNC turning
This process is ideal for machining cylindrical turned parts such as precision shafts. The CNC machine rotates the spindle attached to the chuck while the cutting tool removes excess material from its surface. CNC turning ensures the required diameter and surface finish for machined shafts. Most importantly, CNC turning is your first choice for high-volume production situations where you need to manufacture many shafts quickly.
CNC milling
Milling is an efficient technique that involves cutting a blank using rotating cutters to produce features such as splines, planes and keyways on the surface of precision shafts. In this process, the stationary shaft is cut into the desired shape and size using multipoint rotary tools.
CNC grinding
Precision CNC grinding is a machining technique that uses a rotating grinding wheel to smooth the surface of machined shafts and ensure the shafts have the desired dimensions and tolerances. This process works similarly to CNC machining, although no cutting tools are used. Here, a rotating grinding wheel engages the surface of the shaft to shape it.
CNC Drilling
The CNC drilling process can be used to precision drill holes and channels in shafts so that gears can be attached to the shaft. This technique creates grooves of different diameters and depths so that the machined shaft performs as expected. Drilling is cheap and easier than other techniques.
EDM (Electroerosion)
Spark erosion is a supported technique for precision shaft machining. It uses electricity to cut the blank by evaporation. Electrical discharge machining is used to cut small details from metallic materials. Additionally, spark erosion is an efficient technique for producing complex details on machined solid shafts.
What materials are available for machining shaft parts?
Different materials are suitable for machining precision shafts for different applications. These materials must have excellent strength and fatigue resistance to meet the requirements of the intended application. Common types of compatible materials include:
aluminum
Aluminum is a lightweight and corrosion-resistant material. It is easy to machine and therefore suitable for many applications where weight plays a crucial role. Aluminum is the preferred material when the intended application requires lightweight machined shafts.
stainless steel
Stainless steel is a reliable metal for producing precision shafts. Product engineers often use stainless steel when corrosion resistance is critical. For example, 304 and 316 stainless steels offer excellent corrosion resistance. Therefore, they are often used in applications where they are heavily exposed to water or corrosive elements, such as: B. in chemical processing plants or in marine environments.
Carbon steel
Carbon steel has excellent tensile strength and machinability. It can withstand heat treatment to increase its hardness. It is therefore a widely used material for shaft processing. Grade 1045 is a good example of moderate strength carbon steel, suitable for applications such as pump shafts or motor shafts.
titanium
Titanium is widely used to machine precision shafts for high-performance applications due to its high strength-to-weight ratio and excellent corrosion resistance. Due to its properties, titanium is often used in precision shafts in the aerospace industry.
Alloyed steel
It provides high strength and toughness required for precision machined shafts. 4140 or 4340 steel alloys are typical alloys used to produce precision shafts for heavy-duty applications such as machinery or large industrial engines.
Nickel alloys
Nickel alloys are ideal for shaft machining in highly demanding applications. They offer remarkable corrosion resistance and excellent high temperature resistance. Inconel is a good example of a nickel alloy suitable for precision shafts in turbines or other high temperature applications.
Surface Finish Options for Custom Machined Shafts
Depending on the purpose of the special shafts, surface treatments can reliably improve performance, durability, hardness, corrosion and wear resistance.
Passivate
Custom shaft passivation helps improve the surface finish of stainless steel shafts. The surface of the machined shaft is cleaned with an acidic solution that removes free iron compounds and other contaminants. This creates a passive oxide layer on the surface of the shaft, making it more resistant to corrosive elements.
Anodizing
Anodizing is particularly suitable for machined aluminum shafts. A hard, corrosion-resistant layer is formed on the surface of the machined shaft, which improves its aesthetic appearance and corrosion resistance. Anodized shafts can be treated with various dyes for decorative purposes.
Electroplating
Electroplating is a reliable surface treatment that refines the surface of machined shafts by applying a thin layer of metal such as zinc, nickel or gold. This surface treatment improves wear and corrosion resistance.
pearl rays
Bead blasting is an excellent surface treatment that releases fine steel or glass beads under high pressure to clean the surface of your machined shafts. Bead blasting gives your custom waves a clean finish with a matte or satin appearance.
polishing
Polishing is a surface treatment that protects machined shafts against contamination and oxidation. It uses an abrasive to remove nicks and scratches from the surface of your custom rods, improving their corrosion resistance and reflective properties.
Considerations and Tips for Making Shaft Parts
When manufacturing shaft parts, certain factors must be taken into consideration. Here you will find useful considerations for the successful production of shaft parts.
Determine the expected load and torque
It is critical to determine the expected load and torque that the machined shaft will experience in the intended application. This helps ensure the production of reliable and accurate shaft parts and prevent shaft failures. In particular, this also makes it possible to determine the optimal material and diameter required to produce reliable and functional shaft parts.
Shaft material
Factors such as material thickness, temperature and corrosion resistance are crucial in selecting the appropriate material in the manufacture of shaft parts. This ensures that the shaft and machined parts will last a long time and function correctly in the intended application.
Furthermore, the chosen material must be able to withstand the stresses of the application without failing. Furthermore, each processing material has its advantages and disadvantages. Therefore, choose the material that suits your project needs and budget.
Set the shaft length and diameter
Machine the length and diameter of the shaft and its components according to the requirements of the intended applications to avoid inaccuracies such as deflection and extreme vibration. Most importantly, you must choose a cross-sectional shape that will effectively withstand the stress that the shafts will be subjected to.
Surface Finish
Choosing an appropriate surface finish for your machined shafts is crucial to ensuring their longevity. There are different surface finishes that are compatible with different types of shafts. Shaft parts that have been refined using processes such as anodizing, powder coating or passivation better resist corrosion, wear and friction.
Quality control in shaft processing
Ensuring quality control is important when producing functional machined shafts. Regular quality checks ensure that the dimensions, material properties and surface finish of the machined shaft meet the specified requirements. Therefore, you can use methods such as surface roughness testing, coordinate measurement and hardness testing in quality control.
Additionally, consistent quality controls allow for efficient detection and correction of potential errors, reducing waste and ensuring that the machined shaft meets desired specifications.
WayKen Wave Processing Capabilities
Concluding
Shaft machining uses innovative techniques and technology to machine shafts to design specifications. There are different types of axes, each adapted precisely to the requirements of the respective application.
Common questions
What is the standard tolerance for precision machined shafts?
Tolerances for machined shafts vary depending on the application and specific requirements. However, standard tolerances for the diameter of a machined shaft are between +/- 0.01 mm and +/- 0.05 mm, while standard tolerances for length are between +/- 0.1 mm and +/- 0.2mm.
What is the purpose of a machined shaft?
A machined shaft is an important rotating component in engines or machines responsible for transmitting power from one engine component to another.
Which processing technique is ideal for producing a shaft?
CNC turning is the most suitable machining method to produce a shaft. It is a widely used subtractive process in which a raw material (bars) fixed in mandrels is rotated while a special cutting tool removes material from it to produce shaft parts with desired properties.