To solve the problem of cracking in wire-cut carbide products, the microstructure of the alloy surface was analyzed by adjusting the wire-cut processing parameters based on the current situation of the company's products. Through experimental comparison, the main factors causing cracks were identified and solutions were proposed.
1. Preface
WEDM (Wire Electric Discharge Machining) is widely used in processing carbide as mold material and wear-resistant parts, mainly for parts that are small in size, complex in shape and unsuitable for grinding wheel machining. This process improves processing efficiency compared to traditional methods.
However, when using WEDM for machining alloy parts with complex structures, the impact on the alloy surface microstructure area is often ignored. This can result in significant changes to the microstructure of the machined surface, affecting the performance of the carbide part.
Research has shown that WEDM can cause microcracks and other defects on the surface of die products, impacting their performance. To solve this problem, the researchers proposed improvement measures, such as the use of compound cutting fluid in the first two cuts and kerosene in the final finish. This has been shown to reduce surface roughness (Ra) to less than 1 mm for YG8 carbide.
Liu Yike analyzed the test results of WEDM machining of carbide molds based on the EDM principle and found that although increasing the pulse width improves machining efficiency, cracking may occur beyond a certain value. Luo Binhui and others conducted a comparative test on EDM processes that can affect cracking in carbide milling cutters and found solutions to the cracking problem.
This post builds on previous research and the company's experience to better analyze the mechanism of cracking in carbide products caused by wire cutting. By changing the electrical parameters of wire EDM, the impact of wire cutting electrical parameters on microstructural cracks on the alloy surface is analyzed and methods to reduce and prevent cracks are proposed.
2. Crack generation mechanism
Wire cutting is different from conventional cutting because it does not come into direct contact with the workpiece. Instead, it relies on the continuous pulsed spark discharge that occurs between the cutting edge and the workpiece. This discharge uses the high temperature generated during the partial and instantaneous spark to gradually wear away metallic materials.
Spark discharge is carried out in an isolated liquid medium, such as an emulsion. The current density in the discharge area during wire cutting can reach 10,000 A/mm2, and the temperature can reach 10,000-12,000 ℃. The dielectric liquid used in the process cools quickly.
EDM energy creates a non-uniform, time-varying temperature field at the surface of the material, leading to significant thermal stress and strong thermal shock properties. In WEDM, the machining surface undergoes rapid heating and cooling, causing uneven expansion and contraction of the material and potentially leading to large thermal stress.
This is particularly problematic when machining hard, brittle materials such as carbide and cermet, and can result in surface cracks if the electrical parameters are not chosen correctly and the thermal stress exceeds the material's strength limit.
Microcracks often appear on the surface due to the generation of tensile stress caused by the instantaneous high temperature and rapid cooling during EDM. These cracks generally occur only in the molten layer, but can expand into the heat-affected layer when the pulse energy is high (during rough machining).
The discharge energy received by the part has a significant impact on microcrack formation: higher energy results in wider, deeper cracks, while lower pulse energy leads to narrower, shallower cracks and smaller, smaller hole distributions.
The sensitivity of different part materials to cracking varies according to the thermal conductivity of the material, with brittle materials such as carbide being particularly prone to surface microcracks.
A visualization of the wire cut discharge process is shown in Figure 1.
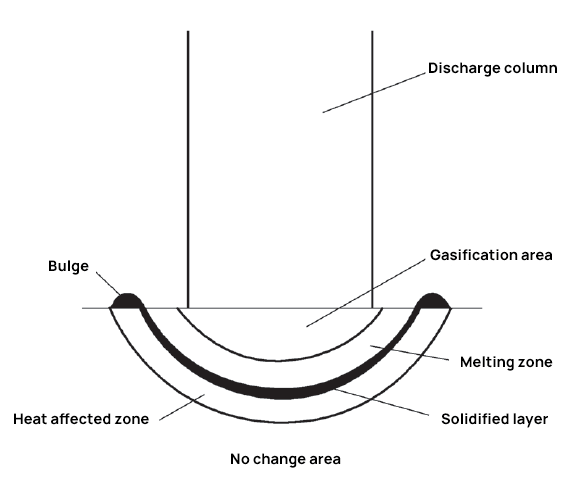
Fig. 1 wire cutting discharge
According to the thermal stress model, the peak stress is directly proportional to the amount of heat entering the material. This relationship is consistent across similar conditions and is directly related to the input energy of the electrical pulse.
As the input power increases, the material absorbs more heat.
Therefore, the greater the power, the greater the tension and the easier it will be to produce cracks. Ignoring energy loss, the energy acting on the workpiece in the machining process can be simplified as wire cutting discharge pulse energy, which is
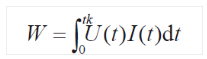
Where,
- W is pulse energy (J);
- U is intermittent instantaneous discharge voltage (V);
- I is the intermittent instantaneous discharge current (A);
- t is the time(s);
- tk is the discharge duration (pulse width, s).
The energy (w) of a discharge pulse during wire cutting is proportional to the discharge voltage (U), the discharge current (I), and the discharge duration (pulse width, tK). It was observed that when the pulse width is constant, an increase in discharge voltage and current will intensify the generation and propagation of microcracks. On the other hand, if the discharge voltage and current are fixed, an increase in pulse width will have the same effect.
3. Test plan
Carbide shaft bushings are highly valued for their hardness, wear resistance and corrosion resistance, which makes them popular in the oil production industry. They are used in various components such as submersible electric pump motors, centrifugal pumps, protectors, separator shafts and plain bearing bushings, motor shaft bushings, piercing bearing bushings, thrust bearing bushings and shaft bushings. seal. These sleeves perform crucial functions such as providing swivel support, stability, thrust, and sealing.
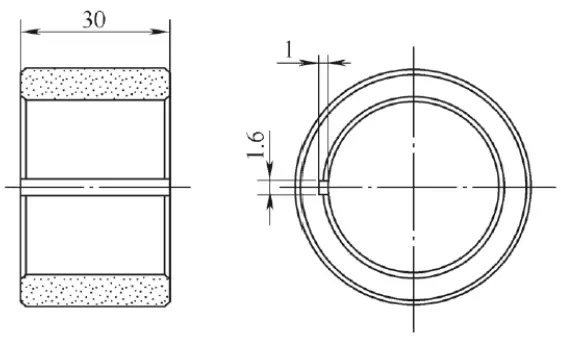
Fig. 2 Conventional carbide shaft sleeve
In the test, the medium wire cutting equipment used was the CTP350.
The cutting fluid used was an emulsion with a concentration of 8% and the cutting wire used was a molybdenum wire with 0.18mm in diameter.
Each time, only one part was clamped for processing.
See Table 1 for wire cutting processing parameters.
Test group No | NO. | Voltage/V | Current/A | Pulse duration/μs | Pulse interval/μs | Wire feed speed/(m/s) |
One | 1 | 100 | 1.5 | 40 | 320 | 15 |
two | 100 | 1.5 | 36 | 282 | 15 | |
3 | 100 | 1.5 | 24 | 192 | 15 | |
4 | 100 | 1.5 | 12 | 96 | 15 | |
Two | 5 | 100 | 3.5 | 20 | 160 | 15 |
6 | 100 | 2.8 | 20 | 160 | 15 | |
7 | 100 | 2.4 | 20 | 160 | 15 | |
8 | 100 | 2.0 | 20 | 160 | 15 | |
Three | 9 | 120 | 2.0 | 20 | 160 | 15 |
10 | 110 | 2.0 | 20 | 160 | 15 | |
11 | 90 | 2.0 | 20 | 160 | 15 | |
12 | 70 | 2.0 | 20 | 160 | 15 | |
Four | 13 | 100 | 2.8 | 16 | 128 | 15 |
14 | 80 | 1.0 | 6 | 48 | 6 | |
15 | 50 | 0.3 | 4 | 32 | 3 |
4. Test result
4.1 Effect of pulse width on microcracks on the alloy surface
1 # ~ 4 # metallographic photos of the product are shown in Fig.
It is observed that as the pulse width decreases, the microcracks on the alloy surface become progressively smaller. With a pulse width of 40 milliseconds, the depth of microcracks reaches 15 millimeters. However, with a pulse width of 12 milliseconds, there are essentially no microcracks present.
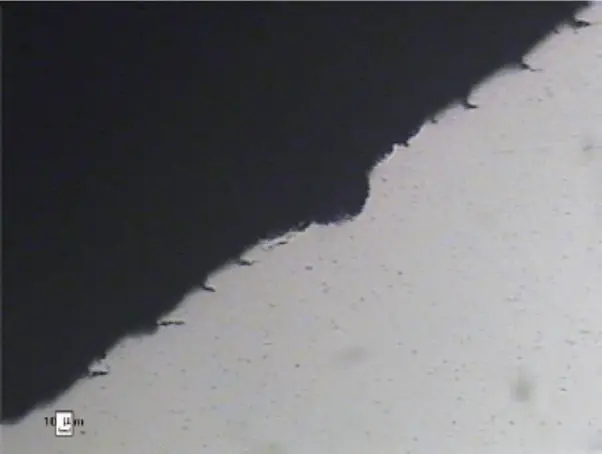
Fig. 3 #1 metallographic photos of products
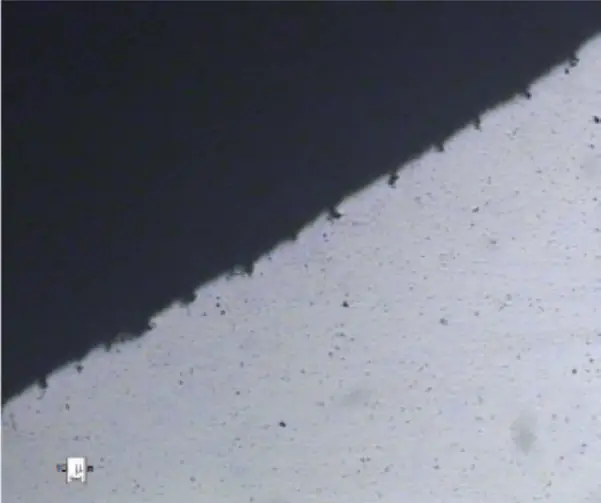
Fig. 4 #2 metallographic photos of products
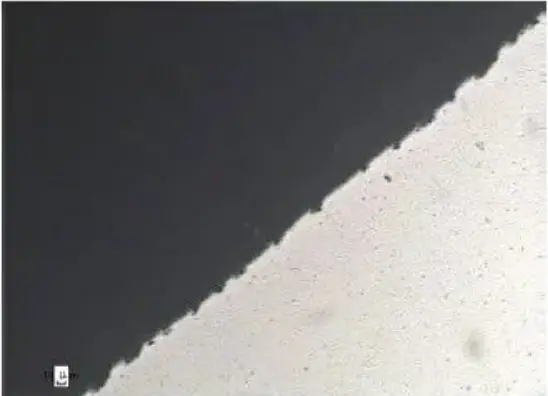
Fig. 5 #3 metallographic photos of products
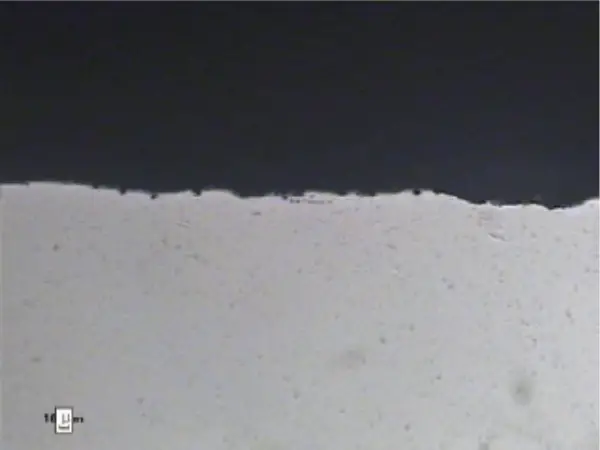
Fig. 6 #4 metallographic photos of products
4.2 Effect of current on microcracks on the alloy surface
5# ~ 8# metallographic photos of the product are shown in Fig. 7 ~ Fig. 10.
It was observed that the crack depth increases as the processing current increases. At 3.5A, the crack depth exceeds 30 mm; when the processing current is 2.8A, the crack depth is equal to 30mm; and when the processing current is 2.4A, the crack depth is 20mm. At 2.0A, the crack depth is shallower, measuring 10 mm.
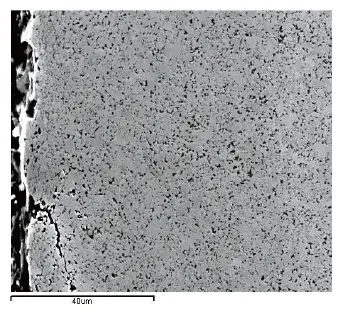
Fig. 7 #5 metallographic photos of the product
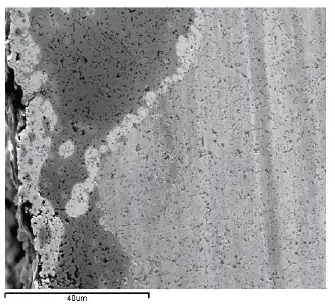
Fig. 8 #6 metallographic photos of products
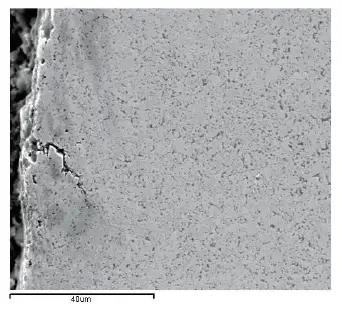
Fig. 9 #7 metallographic photos of products
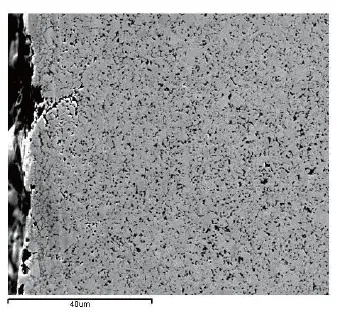
Fig. 10 #8 metallographic photos of products
4.3 Effect of stress on microcracks on the alloy surface
9# ~ 12# metallographic photos of the product are shown in Fig. 11 ~ Fig. 14.
It was observed that when the current is set at 2A and the pulse width is 20ms, the processing voltage varies from 70 to 120V. No microcracks were found in the alloy in the cut section. This indicates that, with constant current and pulse width, the effect of voltage on alloy microcracking is negligible.
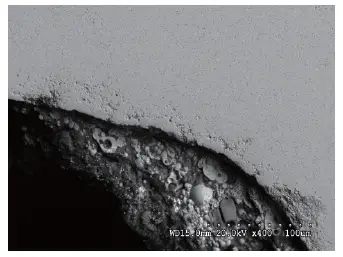
Fig. 11 #9 metallographic photos of products
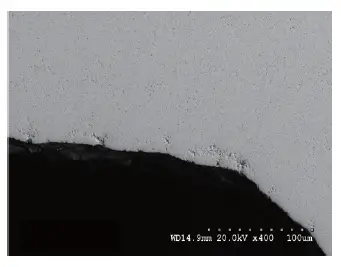
Fig. 12 #10 metallographic photos of products
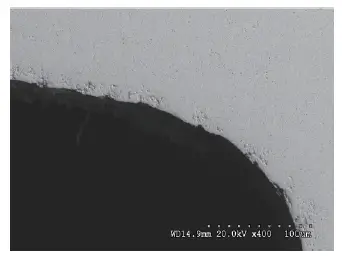
Fig. 13 #11 metallographic photos of products

Fig. 14 #12 metallographic photos of products
4.4 Effect of cutting times on microcracks on the alloy surface
13# ~ 15# metallographic photos of products are shown in Fig.
The surface quality of the products has been significantly improved through multiple cutting processes, reducing the depth of microcracks.
With medium yarn cutting and processing twice, the depth of microcracks in the product is reduced to 15 mm.
And with medium wire cutting and processing three times, the depth of microcracks is further reduced to 10mm.
Two cutting processes met the current requirement that the depth of microcracks in carbide shaft sleeve products should be less than 20mm.
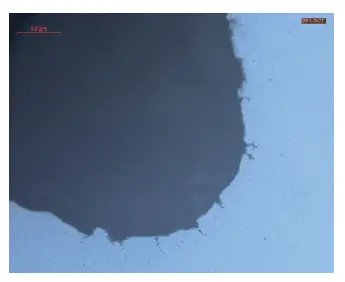
Fig. 15 #13 metallographic photos of products
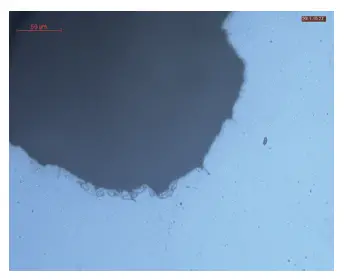
Fig. 16 #14 metallographic photos of products
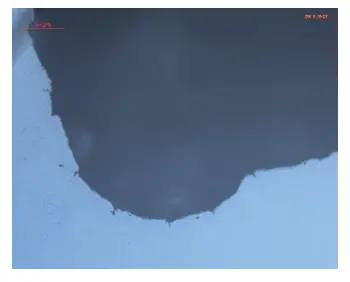
Fig. 17 #15 metallographic photos of products
5. Conclusion
During EDM (electrical discharge machining), the surface of the part undergoes a rapid change in temperature due to the abrupt alternation of hot and cold. This results in a strong transient thermal shock process with fast speed and large amplitude.
When machining brittle materials such as carbide, cracks can be reduced or avoided by reducing the stress amplitude and its time-varying thermal shock. This can be achieved by several methods that limit thermal shock.
Pulse width and processing current have a significant impact on the surface microcracks of the alloy. A wider pulse width and higher current lead to deeper cracks. However, the effect of stress on surface microcracks is not significant.
No microcracks were observed when the pulse width was set to 12 ms. To avoid cracking, it is recommended to avoid processing currents above 2A when selecting electrical parameters.
To minimize thermal stress and its impact on the workpiece, high peak narrow pulse electrical parameters should be used and the temperature field superposition effect should be utilized. This will cause the part material to vaporize, resulting in greater heat of gasification that removes most of the heat and prevents the part surface from overheating.
Multiple cutting is an effective method for reducing and eliminating surface microcracks.