There are several types of cracks: such as cracks in raw materials, cracks caused by heat treatment, and forging cracks, which can be confusing.
Identifying them is an important course of action as it helps to pinpoint where the crack occurred, which can aid in analyzing why the crack occurred.
First of all, we need to clarify the concepts of “raw material cracks” and “forging cracks”. Cracks that occur after forging should be considered as “forging cracks”.
However, the main factors that lead to the formation of forging cracks can be classified into:
- Forging cracks caused by raw material defects;
- Cracks in forging caused by improper forging techniques.
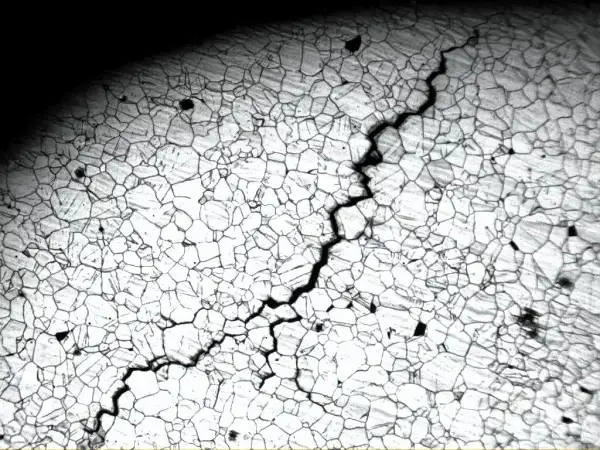
To roughly differentiate, cracks can be classified by their macroscopic morphology. Transverse cracks are generally unrelated to the parent material, while longitudinal cracks require an analysis that combines crack morphology and the forging process.
Decarburization on both sides of a crack indicates that it occurred during forging. As for whether it was caused by the raw material or the forging process, an analysis based on metallography and the process is necessary.
For parts of the same model and the same batch, forging cracks are generally located in the same position and extend relatively shallowly under the microscope with decarburization on both sides. Cracks in the material may not occur repeatedly in the same location and may be of varying depths under the microscope. There is still some regularity to observe and analyze.
The cracks in the material mainly align with the longitudinal direction of the material. There are two types of forging cracks: one caused by overheating and oxidation leading to decarburization near the crack, while the other caused by the tearing phenomenon of web damage during cold forging can be distinguished through metallography.
The purpose of forging is as follows:
- Meet training requirements;
- Improve the internal structure of the material, refine the grain size and homogenize the composition and structure of the element;
- Make the material denser (forging can close internal defects such as unexposed air holes or gaps) and distribute the aerodynamic line more reasonably;
- Serve the next process through appropriate post-forging heat treatment methods.
Therefore, there must be certain defects inside the raw material for forging. Large forgings are often forged directly from steel ingots, which inevitably contain a large number of casting defects. Reasonable forging can also forge these so-called defects.
Therefore, the rationality of the forging process is the main factor that determines whether the forging will crack.
Of course, based on a stable forging process, if explicit control requirements for raw material defect grades are made before forging, and the cracking phenomenon appears due to raw material defects exceeding the requirements during Forging, this can be regarded as “forging cracks caused by defects in raw materials”.
Cracking problems require specific analysis, along with analysis of the forging process and consideration of the existence of a protective atmosphere during the heating process.
Forging should be the process of forging and compacting cracks in the raw material. Oxide scale is generally compact and gray, while loose, dirty debris from the sampling process is black.
Looking under high magnification can reveal the difference, however, power spectrum analysis can always distinguish them when other methods are insufficient.
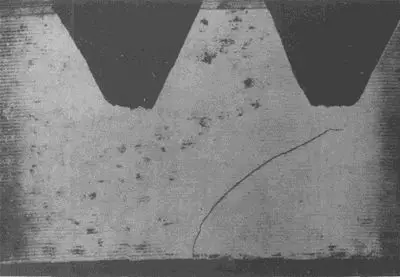
Forging cracks
Forging cracks generally form at high temperatures during forging deformation. When the cracks expand and come into contact with air, under a microscope at 100X or 500X magnification, the cracks can be visualized with oxidation and decarburization scales on both sides, with the structure being mainly ferritic.
The morphological characteristics of these cracks are that they are relatively thick and often exist in multiple shapes, without a clear pointed end, relatively round and pure, and without clear directionality.
In addition to these typical shapes, finer forging cracks can sometimes appear. The decarburization around the crack is not complete, but partial.
Typical examples of forging cracks include:
More oxide at the edges of the crack.
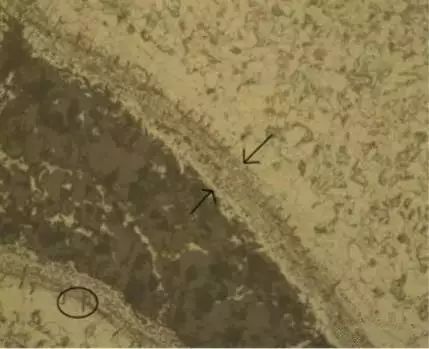
Forging cracks are formed during the steel forging process and can be attributed to several reasons. Predominantly, they can be divided into two main categories: forging cracks caused by defects in the raw material and those induced by the forging process itself.
Raw material defects include residual shrinkage holes, steel inclusions, subcutaneous blisters, shrinkage pores, white spots and laminations. These defects may already exist in the steel prior to forging and, if not removed or treated, can lead to cracks forming during the forging process.
Improper handling during the forging process is also a significant cause of forging cracks. These include overheating, excessive burning or too low a final forging temperature, as well as cooling too quickly after forging. All of these factors can lead to excessive internal stresses in the forging, thus triggering cracks.
To prevent the occurrence of forging cracks, several measures can be taken. For example, the selected billet must be thoroughly cleaned of all surface defects and subjected to an appropriate high-temperature homogenization treatment to eliminate residual internal stresses and grain segregation, thereby increasing the plasticity of the metal.
Furthermore, improving the forging process, such as appropriately increasing the fillet radius, reducing shear stress, and limiting deformation areas in the final stage of die forging, can also help prevent crack formation.
For existing forging cracks, certain methods can be employed for repair. For example, submerged arc welding is an effective crack repair technique, capable of automatically completing the welding process under the flux layer, effectively repairing the cracks.
Furthermore, shallow transverse cracks on large forgings can be removed upon detection by flame cleaning to prevent the cracks from widening in subsequent forging.
Heat Treatment Crack
The cracks produced during the quenching and heating process present significant differences in nature and morphology compared to those formed during the forging and heating process.
For structural steel, the heat treatment temperature is generally much lower than the forging temperature.
Even for high-speed steel and high-alloy steel, the heating and insulation time is much shorter than the forging temperature. Early cracking may occur during the heating process as a result of excessively high heat treatment temperatures, producing cracks distributed along coarser grain boundaries.
When the heating rate of the part is very fast, early cracking may also occur, with slight decarburization on both sides of the crack, but oxidation scales are present inside and at the tail of the crack.
Sometimes, due to instrument malfunction, extremely high temperatures can cause the material to become coarse-grained in structure, with the crack distributed along the stubby crystalline edge.
A typical example of crack tempering is the following:
Under a microscope at 500X magnification, the crack appears serrated, with a wide starting edge and a small ending fracture. There is no abnormal metallurgical inclusion or decarburization present in the crack, which extends in a serrated shape, having characteristics typical of tempering cracks.
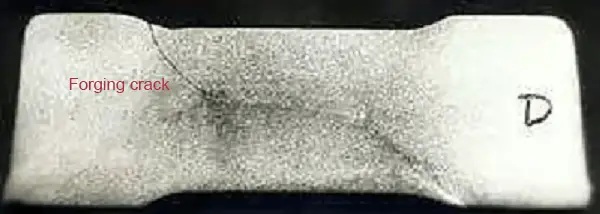
Reasons for forging cracks and heat treatment cracks
Causes of forging cracks:
During the forging process, steel may crack due to defects on the surface or within the material, such as hairline cracks, sand holes, inclusions, subsurface bubbles, shrinkage holes, white spots, or laminations.
Improper forging processes or inappropriate operations such as overheating, excessive burning or too low final forging temperatures, as well as too rapid cooling after forging, can also cause forgings to crack.
Causes of heat treatment cracks:
Tempering cracks are macroscopic cracks caused mainly by macroscopic stresses. In actual production, steel parts are often due to the structural design being irrational, inadequate material selection, insufficient temperature control during quenching, or inadequate cooling rates, which on the one hand increases the internal stress during quenching, leading to the expansion of the formed microcracks to form macroscopic tempering cracks.
On the other hand, increasing the number of microscopic cracks decreases the material's resistance to SK brittle fracture, increasing the probability of crack formation extinction.
Factors affecting tempering
There are many factors that affect quench cracking and here we present just a few common cases encountered in production.
- Quenching cracks caused by pre-existing defects in the raw materials: If there are cracks or inclusions on the surface or inside the raw materials, and they are not found before quenching, quenching cracks may form.
- Cracks caused by inclusions: If there are severe inclusions inside the parts, or if there are hidden cracks due to severe inclusions, cracking may occur during quenching.
- Cracks caused by poor original structure.
- Quenching cracks caused by inadequate quenching temperature: There are generally two cases of cracks caused by inadequate quenching temperature:
(1) The indicated temperature of the instrument is lower than the actual temperature of the furnace, resulting in a higher quenching temperature, causing the part to overheat and break during quenching. The metallographic structure of superheated and quenched cracking always contains coarse grains and coarse martensite.
(2) The actual carbon content of the steel is higher than the content specified by the steel type. When quenched according to the normal quenching process of the original grade, it is equivalent to increasing the quenching temperature of the steel, which can easily cause overheating and grain growth of the parts, as well as increasing the stress during quenching, causing cracks.
- Quenching Cracks Caused by Inadequate Cooling During Quenching: Inadequate cooling during quenching can also cause parts to crack.
- Quenching cracks caused by machining defects: Due to poor machining, rough and deep tool marks are left on the surface of parts. Even for simple parts or areas without stress concentration, cracks may occur during hardening or premature failures during service.
- The influence of part geometry on crack hardening: The irrational geometry of parts or the large thickness difference in the excessive section are easy to cause cracks due to the stress concentration during hardening.
- Cracks caused by failure to temper in a timely manner after quenching: Failure to temper in a timely manner after quenching can cause cracking due to residual stress from quenching.
Methods for distinguishing cracks
It is important to distinguish whether these are tempering cracks, tempering cracks, forging cracks or grinding cracks, to identify precisely in which process the cracks occurred and analyze the reasons for their formation.
First , pay attention to the differences in the morphology of quenching cracks and grinding cracks. To distinguish between quenching cracks and grinding cracks, which may not be detected during quenching but are found after grinding, pay attention to the shape of the cracks, especially the direction of crack development.
Grinding cracks are perpendicular to the grinding direction, appearing in a parallel line or tortoiseshell pattern. Grinding cracks are more superficial, while tempering cracks are generally deeper and larger.
Tempering cracks are not related to the grinding direction and often appear as straight cracks similar to knife cuts.
Second , pay attention to where the cracks occur. Sharp corners, hole edges, inscriptions, stamping or surface mechanical defects and other areas where cracks occur are mainly temper cracks.
Thirdly, distinguish quenching cracks from forging cracks or cracks caused by other conditions by observing the fracture surface of the part.
If the surface of the crack is white, dark white or light red (caused by water rust during water quenching), it can be determined to be a quenching crack. If the surface of the crack is dark brown, with uniform oxide scales, it is not a quenching crack; is a pre-existing crack that formed during forging or rolling and expanded during quenching.
As quenching cracks are formed below the MS point, their surfaces cannot be oxidized.
Fourth , in the microstructure, quenching cracks fracture along grain boundaries. If they are not along the grain boundaries but within the grains, they are fatigue cracks.
Fifth, if there is decarburization around the cracks, it is not a quenching crack, but a pre-existing crack before quenching, because quenching cracks are produced during quenching and decarburization does not occur.
What are the latest techniques for preventing forging cracks?
The latest techniques for preventing forging cracks mainly include the following:
Optimizing materials processing: By improving issues such as the transverse segregation of harmful low-melting impurities such as S, P, Sb, Bi, Pb, Sn in the forging module, or the presence of transverse microcracks, the creation of quenching cracks can be effectively avoided. This involves adjusting the chemical composition and heat treatment of the material before forging to minimize the impact of these impurities.
Improve forging processes: For the quality control of bends and cracks in aluminum alloy forging, the principle of prevention is emphasized and a method combining process technology and production management is proposed. This means that during the forging process focus must be placed on equipment selection, mold design and optimization of forging parameters to reduce the occurrence of cracks.
Adopting advanced detection techniques: By carrying out fast and accurate detection on forged parts, possible crack problems can be discovered in time. This includes observing the material's microstructure with high-precision microscopes and using X-rays or other non-destructive testing methods to evaluate the material's overall quality. This allows intervention before a crack forms.
Implementation of strict quality control measures: In forging production, a comprehensive quality management system must be established. From the selection of raw materials to the inspection of finished products, all steps must be carried out strictly in accordance with standards. This includes regular maintenance and calibration of forging equipment, as well as training for operators to ensure they can correctly understand and execute the forging process.
How can we accurately identify and evaluate the impact of raw material defects on crack formation during the forging process?
To accurately identify and evaluate the impact of raw material defects on crack formation during the forging process, it is first necessary to understand the main raw material defects and their impact on the quality of forgings. Internal or surface defects of raw materials, such as composition and structure segregation, non-metallic inclusions, dendritic segregation and porosity, can potentially affect the forming process and the final quality of forged parts. Therefore, identifying these defects is the first step in evaluating their impact on crack formation.
Next, we can analyze the impact of forging parameters (such as speed) on the formation mechanisms of typical defects such as bending defects through finite element simulation and experimental design. This will also allow us to assess the potential risks that these defects pose to the formation of cracks.
Furthermore, the use of ultrasonic control methods and eddy current techniques can effectively evaluate the depth of surface and internal cracks in metal products, providing a basis for the quantitative characterization of crack defects.
Image processing technology is also an important means of identifying and evaluating crack formation. Crack detection and marking methods implemented through software such as Matlab can help identify potential crack areas for further analysis.
Furthermore, deep learning-based methods can further promote automated crack width measurement, thereby more accurately assessing the potential risk of structural damage.
During the forging process, what specific operations can effectively reduce cracks caused by overheating, burning or too low final forging temperature?
During the forging process, to effectively reduce cracks caused by overheating, burning or too low final forging temperature, the following specific operations can be adopted:
Control the heating speed and time:
Use rapid heating methods and minimize heating time in high temperature stages to avoid decarburization defects and overheating defects. This helps to improve the plasticity of the metal, making it easier for large deformations to pass without cracking.
Strictly control the initial forging temperature and final forging temperature:
For different types of steel, such as carbon structural steel and alloy tool steel, the initial forging temperature should be adjusted according to their carbon content. Especially for stainless steel, the appropriate initial forging temperature should be selected and the final forging temperature should not be lower than 950°C to avoid forging cracking.
Protect the billet before heating:
When conditions permit, apply a protective coating (such as glass powder) to the billet before heating it to reduce decarburization and prevent overheating and burning.
Ensure sufficient deformation and correct operating techniques:
During the forging process, the final forging temperature of the last fire must be strictly controlled and sufficient deformation must be ensured to prevent cracking. At the same time, attention should be paid to good operating techniques of the forging process to avoid cracks caused by improper operation.
What improvements and optimizations can be made to the flame cleaning method for transverse cracks on the surface of large forgings?
For the flame cleaning method of transverse cracks on the surface of large forgings, improvements and optimizations can be made in the following areas:
Adopt advanced flame cleaning technology: Based on the analysis of SMS-20 flame cleaning machine, flame cleaning technology can effectively remove surface defects. By optimizing cleaning depth, cleaning efficiency and quality can be improved. Therefore, the introduction of more efficient and advanced flame cleaning equipment and technologies, such as automatic flame cleaning systems, can significantly improve cleaning results.
Optimize the forging process: Because F92 material is prone to surface crack defects during the forging process, especially when the Cr and W alloy content is high, the traditional flame “sweeping” efficiency is very low. Therefore, optimizing the forging process, such as adjusting forging parameters and improving mold design, can, to a certain extent, reduce or prevent the occurrence of transverse surface cracks.
Combine with other cleaning technologies: Although flame cleaning is an effective surface treatment method, it can also be considered to be used in combination with other cleaning technologies for better cleaning results. For example, pickling or blast cleaning processes can further improve surface quality. This multi-technology combination method can have better cleaning effects for certain specific surface defects.
Application of intelligent control technology: With the development of intelligent control technology, the application of these technologies to the flame cleaning process can achieve more precise control and operation, thereby improving cleaning accuracy and efficiency. This includes real-time monitoring of the cleaning process and automatic adjustment of cleaning parameters.