CNC machining tolerances are important parameters in product manufacturing, regardless of intended use. Today, most industrial and consumer products require consistency to meet manufacturing standards.
Therefore, product manufacturers rely on CNC machines in their manufacturing projects to achieve high precision. However, it is important to understand the concept of machining tolerances, their types, standards and their measurement methods, as the dimensions of CNC machined parts vary from theoretical values due to the type of material, machining processes and design.
This article explains CNC machining tolerances, their meaning, and the general machining tolerance table. Read on to learn more about CNC machining tolerance standards and various factors that affect CNC tolerances.
What are CNC machining tolerances?
CNC machining tolerances refer to the allowable variation in the dimensions or nominal value of a part. Machining tolerances represent the level of precision required in manufacturing a product. Product manufacturers examine a part's form, fit, and function to determine its tolerance criteria.
Machining tolerances are often preceded by a “±” symbol. For example, if a 3.0-inch part requires a tolerance range of ±0.0010 inches, the finished part must have a height between 2.999 inches and 3.001 inches to pass quality inspections.
Smaller tolerances mean a tighter tolerance, which means the part requires more precision. A larger tolerance, on the other hand, means the part requires less precision. Close or zero tolerance machining involves higher costs because it requires more adjustments, longer machining cycle times, and specialized tools.
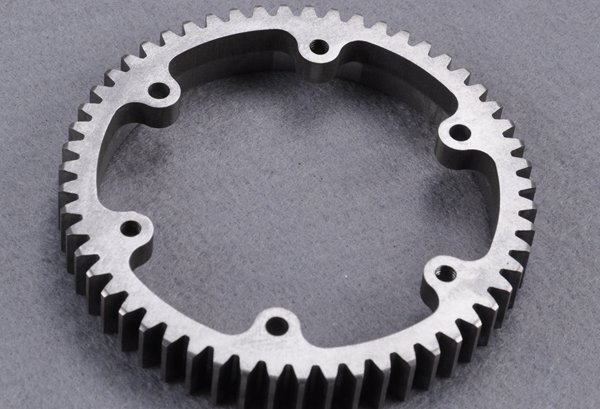
Why are machining tolerances important?
All CNC machined parts and components have some degree of inherent variation. However, tolerances help control these variations, ensuring consistency and optimal performance of machined parts.
Improve part fit and function
CNC tolerances are essential to ensuring that one part in an assembly interacts perfectly with another. Clearly defining your tolerances helps ensure that CNC parts are compatible with other components. Likewise, some features of a part ensure that it will perform well in its intended application. Therefore, any deviation from the permissible limits makes them defective and unusable.
Consider a margin of error
Every manufacturing process has a certain degree of variation. However, machining tolerances take this variation into account, determining the limits within which a part can function. When tolerances are established from the beginning, there is less chance of a part failing or needing to be reproduced.
Control processing costs
In general, tighter tolerances increase the cost of CNC machining. Parts machined to tighter tolerances require additional processing such as grinding and precision machining. However, you can finish a product to tighter tolerances using basic machining processes.
By defining tolerances, unnecessary cost increases can be avoided when processing parts with tighter tolerances. At the same time, setting tolerances on parts with tighter tolerances can avoid extreme accuracy costs.
Ensure the final appearance of the product
High-precision tolerances improve the final appearance of machined parts. For example, if two parts fit together perfectly with no visible gaps, strict tolerances must be set for both parts from the beginning to ensure a perfect fit.
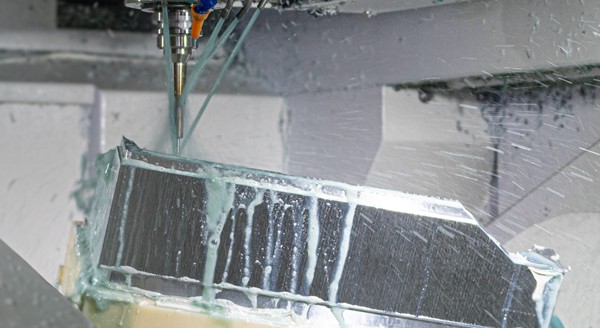
Types of tolerances used in CNC machining projects
Due to different machining methods and part geometries, manufacturers in different industries often use different tolerances for CNC machining of parts. We discuss typical CNC tolerances.
Standard Tolerances
Standard CNC tolerances are the typical tolerances that machinists apply to commonly manufactured products. Most machinists use CNC milling tolerances of about +/- 0.1mm unless customers specify preferred tolerance values. Various international organizations such as the American Society of Mechanical Engineers (ASME), the American National Standards Institute (ANSI), and the Organization for Standardization (ISO) define the scope of these standards.
Limit tolerances
A limiting tolerance is specified as a range of values within which the machined part is acceptable, provided its dimensions are within the desired range. For example, 15 – 15.5 mm is a limiting tolerance for CNC machining, which means that the dimensions of the CNC part must be between the lower and upper limits (15.5 mm as the upper limit and 15 mm as the lower limit).
One-sided tolerances
One-sided tolerances allow deviations in one direction, whether only negative or positive. For example, a tolerance of +0.00/-0.03 mm means that the machined part can be approximately 0.03 mm smaller, but not larger, than the specified dimension.
Product designers often use these tolerances in designs where one component must fit perfectly into another. Additionally, a piece will not serve its intended purpose if it is too large or too small. Therefore, make sure the finished piece does not exceed the desired dimensions.
Bilateral tolerances
The deviation from the defined dimension can be positive or negative when using bilateral tolerances, allowing a slight increase or decrease in the size of the part. For example, a tolerance of +/- 0.05 mm means that the part can be 0.05 mm longer or shorter than the specified dimension. These specifications generally apply to external dimensions.
Geometric Dimensioning and Tolerance (GD&T)
GD&T is a versatile system for detailing and communicating standard machining tolerances. It is more complex than typical tolerance systems. It uses feature control structures to specify specific shapes and dimensional tolerances of parts.
Geometric dimensioning and tolerances ensure that the final dimensions of a part remain within specified limits. The geometric properties of the part are also specified, including flatness, concentricity, and true position. In particular, GD&T symbols guarantee the dimensional accuracy of part features in some parts with higher processing requirements.

General Tolerance Standards for CNC Machining
CNC machining involves several processes with different tolerances due to different types of cutting tools. Below are standard tolerances for typical CNC processes:
Law Suit | Tolerance standards |
Milling (3 axis) | ±0.13 mm or 0.005 inches |
Milling (5 axis) | ±0.13 mm or 0.005 inches |
lathe | ±0.13 mm or 0.005 inches |
routers | ±0.13 mm or 0.005 inches |
Milling cutters (tools for cutting joints) | ±0.762 mm or 0.030 inches |
recording | ±0.13 mm or 0.005 inches |
Screw machining | ±0.13 mm or 0.005 inches |
Steel strip drilling | ±0.381 mm or 0.015 inches |
Rail Cutting Tolerances | ±0.762 mm or 0.030 inches |
Surface Finish | 125RA |
However, if you compare these values to alternative machining technologies, you will find that these CNC machining methods have tighter tolerances.
Different terms for measuring CNC tolerances
There are several terms associated with CNC tolerances. Understanding them will give you a better idea of how tolerances are measured in machining. Below are typical terms you should know.
Basic size
The basic size of a part is the size specified in the technical drawing. Product engineers know that manufacturing techniques often require a certain level of tolerance. Therefore, product designers use the basic size and pay attention to possible deviations during processing.
Current size
The actual size of a part refers to its dimensions after the machining process is complete. The actual size therefore represents the practical realization of the final product, while the basic size represents its theoretical values.
However, product manufacturers are working to bring these two values into the same range, although it is nearly impossible to match the actual size to the base size.
Limits
Limits are the minimum and maximum allowable dimensions of a part. The minimum dimension allowed is the “lower limit”, while the maximum dimension allowed is the “upper limit”. However, a part is considered unusable if it exceeds these limits.
Detour
Deviations are the deviations of the maximum allowable size from the basic size. As there are two types of permitted limits, two types of deviations arise – lower deviation and upper deviation. However, it is easier to calculate these deviations:
- Lower deviation = lower limit – basic size
- Upper deviation = upper limit – basic size
Date
Datum is a physical term denoting an imaginary line or plane arbitrarily chosen as a reference point for measuring tools. It is also common in many areas of geometric dimensioning and tolerancing.

What factors influence machining tolerances?
Machining tolerances are mandatory when defining part dimensions. A product is manufactured to general tolerance standards unless specific tolerances are specified by the customer. However, several factors affect tolerances in production.
materials
CNC machining materials have different properties that can influence the tolerances achievable in CNC machining. These material properties include abrasiveness, hardness, and thermal stability.
- Abrasiveness : Extremely rough and coarse materials significantly affect CNC milling machines and can lead to faster tool wear. Achieving strict dimensional accuracy with these materials is often challenging because machining accuracy decreases as cutting tools change.
- hardness : It is more difficult to machine less dense materials with high precision because their dimensions can change upon contact with cutting tools. Therefore, it is best to be patient when working with softer materials.
- Thermal stability : This is a common problem with nonmetals. These materials gradually lose their shape as heat increases during the machining process. Therefore, this factor limits the compatible processes for such materials.
Editing processes
The choice of a machining method can affect the tolerances of machined parts, as different machining methods result in different surface characteristics and roughness. For example, manufacturing processes such as turning, milling, and grinding have different options and limitations.
Additionally, multi-axis CNC machines can handle different basic tolerances and determine the type of parts they can machine. However, understanding the capabilities and limitations of the machining process helps you achieve accurate tolerances, especially when machining complicated designs or tight CNC tolerances.
surfaces
Finishing operations such as painting, anodizing and galvanizing are other machining processes that can affect machining tolerances. These surface treatments can change the dimensions of machined parts. Therefore, when choosing surface processing, it is useful to ensure that the dimensions of the machined part do not fall outside the desired tolerance range.
CNC cutting tools
The types of CNC cutting tools that machinists use in CNC machining affect machining tolerances. High-quality cutting tools with the correct geometry, coating and sharpness influence the precision of machined parts. Furthermore, the material to be machined and the desired tolerances determine the tool design and material.
budget
In general, the available budget determines the choice of machining tools and materials. Tighter tolerances require more time and labor require specialized machines and tools that are often expensive. However, investing in specialized machining tools can ensure that the machined part is within the required tolerance range and has excellent surface quality.
Machinist skills
The skills and experience of the machining specialist are crucial factors that affect machining tolerances. An experienced operator can take necessary measures such as: B. Select appropriate cutting tools, program the CNC machine, optimize machining parameters, and ensure a smooth machining process to ensure the required tolerances.
Considerations and Tips for Selecting CNC Machining Tolerances
Here we discuss practical tips on how to properly approach CNC manufacturing processes to achieve the tolerances required in your project.
Consider the material you choose
The standard machining tolerance for metal parts is +/- 0.005 inches, for plastic parts it is +/- 0.010 inches. Additionally, some parts can require incredibly tight tolerances to fit together perfectly.
However, it can be difficult to obtain accurate dimensions for some materials, such as copper and steel, as they expand and contract with changes in temperature and humidity. Therefore, it is advisable to set the new tolerance based on this factor.
Investigate the applications of your products
The application of a product often determines the required tolerances that govern its production. For example, not all parts need to be machined to tight tolerances. Parts that do not fit or connect to others require less milling precision. Tight tolerances are therefore only used when necessary.
Use of high-performance cutting tools
Factors such as the use of incompatible cutting tools, tools with blunt edges and tool deflections can cause dimensional variations in machined parts. Long-end features such as deep holes and long shanks are often subject to tool deflections.
Additionally, dull cutting tools expose your parts to unwanted complications and compromise spindle accuracy. Using sharp tools and coolants for CNC machines ensures precision.
Find the right CNC machining service
Finding the right expert in CNC machining services can help you achieve ideal machining tolerance. A CNC machining services expert with sufficient knowledge of various machining processes such as CNC milling, turning, and drilling ensures that your machined parts meet tolerances. However, you can save time and costs by specifying tolerances when submitting your manufacturing requests.
When do you not need tight tolerances?
Tight tolerances are critical specifications for the design of your CNC machining product. They indicate the permissible deviation from the dimension specified when manufacturing the product. However, in some cases, strict tolerances are neither practical nor necessary. Below are some examples:
- When machining materials with high thermal expansion or contraction (including aluminum alloys, plastics such as acrylic and polyethylene), strict tolerances are not advisable.
- If the fit between components intended for assembly requires some variability, tight tolerances are not necessary. Tighter tolerances can make part assembly easier and reduce the risk of misalignment.
- For consumer products, tight machining tolerances may be unnecessary as small variations in size are possible without affecting overall quality and performance.
- You should consider not applying strict tolerances to a dimension that will not affect the fit and function of a product. Therefore, strict tolerances are not required for non-critical features that serve decorative purposes.
- Because tighter tolerances result in higher machining costs, the use of tight tolerances is not advisable when cost is a primary factor and tight tolerances do not affect functionality.
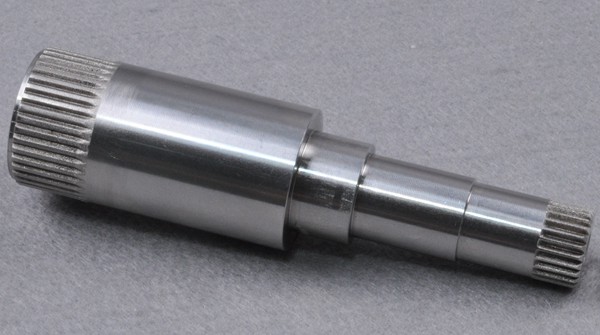
Which industries require precise CNC tolerances?
Precision CNC machining tolerances apply to industries where tight tolerances are required to meet strict design and functional standards. Some of these industries are:
- Medical section
- Aerospace
- Auto Industry
- Defense and military
- electronics
- watches and jewelry
- oil and gas
WayKen meets strict CNC tolerance requirements for your projects
We also provide comprehensive precision machining services, including 5-axis machining and mill-turn machining, as well as various surface treatments for CNC machined parts. As your trusted CNC workshop, our production process includes quality inspections, material certifications, and full dimensional inspections with reports. Contact us today to get started on your projects!
Concluding
CNC tolerances are of central importance for machining processes. These tolerances clarify part specifications and reduce lead time and machining costs. Furthermore, machining tolerances guarantee greater consistency and good performance of machined parts. However, it would be best to understand material selection, part design, and manufacturing processes to ensure your CNC parts meet your desired tolerances.
Common questions
What challenges typically arise when achieving tight CNC tolerances?
Tool deflection, thermal expansion, tool wear and material inconsistencies are typical machining problems that affect tolerances. However, you can resolve these issues through continuous monitoring and adjustments.
What is close tolerance CNC machining?
Although there is no specific range of tight tolerances in CNC machining, any tolerance in the range of ±0.005 inches is considered a tight tolerance. However, the tight tolerance limit can be as low as 0.0001 inch, although this can be very challenging.
Why do you need tight tolerances in CNC machining?
Tight tolerances are essential when machining complex parts for the medical, aerospace and automotive industries. These industries require highly precise tolerances to produce components of an assembly that must fit and function perfectly.