A milling tool is a metal cutting tool used to remove material from the surface of a workpiece. These tools come in different shapes and sizes. Their differences arise from their use for different purposes to achieve different types of projects. Therefore, using milling tools requires precision and careful selection of the right types to achieve the best possible results.
In this article, we will introduce the different types of milling tools, tell you the materials used for these milling tools, and provide instructions on how to choose the right milling tool for your milling operations.
How is the cutter used in milling machines?

Milling machines are rotating tools commonly used in subtractive manufacturing technology, essential to the metal and plastic manufacturing process. Furthermore, when milling it is advisable to change the tool to obtain the desired design.
Milling machines perform the cutting process by removing material from a part by rotating the cutter and moving it into the part. Insert the workpiece into a multi-point rotary cutter on a rapidly rotating milling machine to quickly cut metal or plastic. The milling machine can contain one or more cutters at the same time to speed up the cutting process and quickly create the desired shapes.
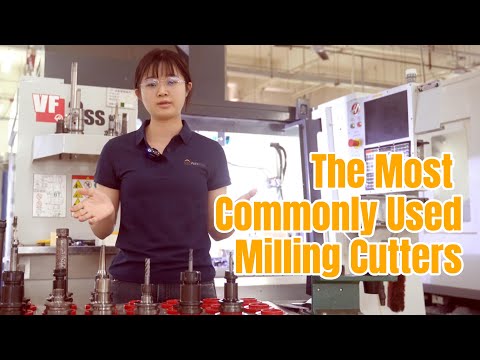
Types of Milling Tools
There are different types and categories of milling tools, each with different purposes and cutting capabilities. Here are the common types of milling tools.
Categories#1: End mills
End mills are milling tools that cut in all directions. Therefore, they differ significantly from drilling tools that cut only axially. Manufacturers use end mills for cutting tool steel and other milling processes, including plunging, reaming, grooving, drilling, face milling, profiling, etc. There are common types of end mills.
1.1 Ball milling cutter
These end mills have a ball tip. Due to their round cutting surface, they are ideal for milling contour surfaces.
1.2 Square cutter
These end mills are used for full milling and have a 90 degree profile. They are also known as flat shank cutters and are ideal for milling jobs such as plunging, profiling and grooving.
1.3 Radius cutter
These end mills have rounded corners. These corners are ideal for cutting a given radius more evenly, preventing tool wear and extending tool life.
1.4 Undercutting on end mills
Also called a lollipop router, this versatile CNC milling tool offers maximum versatility. Its shape makes it the ideal choice for working in recesses.
Rounding Cutter 1.5
This milling tool has reinforced ends. Its main purpose is to mill rounded edges.
1.6 Corner radius cutter
This tool, known as a pork mill, has multiple grooves and leaves a rough surface. Its ability to quickly remove large amounts of material sets it apart.
Categories #2: Face Milling Tool
This tool is used for face milling. What is face milling? This involves removing parts of a workpiece. A face milling tool is used to obtain excellent surface finish. There are cutting edges on the sides of this tool that cut in a horizontal direction, unlike end mills that cut vertically. Furthermore, a face milling tool is mainly used to cut the outside of the blank.
Categories#3: T-Slot Cutters
T-slot cutters have teeth perpendicular to the outer diameter. These cutters, also known as Woodruff cutters, are best suited for cutting T-shaped grooves in parts and workpieces. This type of cutter is ideal for milling grooves used in screw heads and supports in wall panels.
Categories #4: Saw Cutting Tool for Metal Cutting
These saws are used in various industries due to their unique geometry and rigidity. However, industries such as automotive, precision engineering, and construction generally use them to cut non-ferrous metals and steel materials. Here are the different types of metal cutting saws.
4.1 Simple metal cutters
They are CNC cutting tools with only peripheral cutting edges and a side concavity to prevent the cut from being pulled.
4.2 Groove cutter with side teeth
This type of circular saw has lateral and circumferential teeth. This feature allows you to maintain a constant cutting width when removing chips.
4.3 Concave cutter
This is a slotted saw used to create a true convex radius. This cutter gives the pieces an even and smooth semicircular shape.
4.4 Cylindrical milling cutter
It is ideal for applications where high material removal is required. This slotted saw has teeth only on the peripheral surface.
4.5 Roll cutter
This type of cutter, also called a plate or surface cutter, has spiral or straight teeth. Furthermore, in cylindrical or circumferential milling, its teeth cut flat surfaces parallel to the milling axis. Plain cutters are ideal for small projects that require light milling work.
Categories#5: Folding knives
These flat milling tool surfaces use one or more single-cut rotary tools. Similar to turning tools, manufacturers mount an impact milling tool in a special holder. It is also important to note that impact cutters are not ideal for heavy-duty cutting operations. Below are the different types of impact cutters.
5.1 Upper cutters
It has long-reaching needle-like tips that are ideal for cutting through densely packed corals. The cuts achieved with this are always clean and precise.
5.2 Rotary carving tool
The main purpose of this tool is to carve hard materials. It is used for carving wood and engraving blown glass.
5.3 Rotary cutting tool
These milling tools cut the fabric of a material without distorting the patterned cutting line. Some professionals use this tool to cut up to eight layers of material in one milling operation.
Categories#6: Shape cutters
This is a milling cutter used to shape irregular contours, both 2D and 3D. These cutters also come in different configurations and shapes. It is ideal for creating helical gears and other complex and intricate surfaces. It is used for slot milling, chamfering and full radius milling. There are three main types of shape cutters.
6.1 Convex cutter
This is a CNC milling and turning machine to produce inwardly curved semicircles. Convex cutters make it easy to create concave shapes.
6.2 Corner rounding cutter
This cutter is used individually or in pairs. These corner rounding cutters, also called radius cutters, make radius milling easier.
6.3 Cutter with indexable insert
When tooth cutters are used, the teeth are welded into place with screws or mechanically attached to the cutter. The tooth material is generally carbide or tool steel. Machined steel, on the other hand, is more suitable for producing the cutter body.
Materials used for cutters
There are different cutting methods that are ideal for different conditions. These differences in processes and conditions require the use of different cutting materials. Here are the most common materials for making milling tools.
Carbon steel for tools
This is a low-cost metallic material with good machinability for manufacturing milling tools. This material contains 0.6-1.5% carbon and generally less than 0.5% manganese and silicon. It may also contain metals such as chromium and vanadium, depending on the grain size and hardness desired by the manufacturer.
Cutters made of carbon tool steel remain sharp for a long time due to their high resistance to abrasion. However, at temperatures above 250 °C, the hardness of this material decreases rapidly. It is therefore ideal for the production of low-speed machining tools such as twist drills, milling tools and forming and turning tools. It is also excellent for machining soft metal materials such as magnesium, aluminum, brass, etc.
High Speed Steel (HSS)
This is carbon steel, but it contains a small amount of molybdenum, tungsten, chromium and other metal alloys, which makes it significantly different from traditional carbon steel. With the addition of these alloys, high-speed steel has greater toughness, wear resistance and hardenability, providing a higher metal removal rate.
To extend the life of this tool, manufacturers sharpen it and use coolant (as it loses its hardness at temperatures above 650°C). This milling tool material is ideal for producing drills, broaches and single-edge turning tools.
Carbide and cermet tool
This powder metallurgy milling tool is extremely hard and can withstand cutting operations at very high speeds. This material made from tungsten, titanium carbide and tantalum remains hard up to 1000°C. Manufacturers use several binders to bond the components of this tool, including cobalt, nickel, and molybdenum.
When the bonding material is nickel and molybdenum, this tool is called cermet and is used for various finish and semi-finish milling operations on various materials, including alloys and stainless steel. On the other hand, tools with low cobalt content are ideal for finishing operations, while tools with high cobalt content are better for rough cutting.
Ceramics
This material is non-reactive and is harder than its cermet counterparts. It is also more resistant to heat, wear and tear than hard metals. This heat resistance makes ceramic cutters ideal for milling superalloy parts. Hard materials require high heat for ceramic to work properly.
Estelite
This is a non-ferrous alloy material produced only by milling or casting. It contains varying amounts of chromium and cobalt. It may also contain tungsten or molybdenum. Cutting edges made from this material maintain their quality even at extremely high temperatures and speeds.
On large cutters, manufacturers attach stellite teeth to a steel disc; for smaller cutters they use solid stellite. Stellite cutters are ideal for producing automotive engine castings and other mass-produced parts.
Tips for choosing the right milling tool
To choose the right router for your project, there are a few things you need to consider. Here are some tips that can help you:
Cutter size and diameter
The milling depth and width determine the size of the milling tools. Increasing the width and depth at the front of the cutter means increasing the size of the cutter. However, the standard diameter range for index cutters is Φ16~Φ630mm.
When milling parts with a large surface area, it is recommended to use cutters with a smaller diameter. Ideally, 70% of the cutter's cutting edges should be involved in cutting during each milling process.
Another factor that can determine the diameter of the cutter is the diameter of the machine tool spindle. The recommendation for selecting a face mill diameter is D = 1.5d, where d is the spindle diameter.
When milling holes, attention must also be paid to the size of the tool, as if the diameter of the cutter is too large or too small in relation to the hole, damage to the part or tool may occur.
Milling performance
When choosing the correct cutter, cutting performance and the size of the part to be machined must be taken into consideration. For example, when selecting the diameter of a face milling cutting tool, the power requirement of the tool must be within the power range of the milling cutting tool.
In addition, for a small diameter end mill, the main thing to pay attention to is that the maximum machine speed corresponds to the minimum cutting speed of the tool (60 m/min).
Milling tool body selection
When selecting a milling tool, the number of teeth on the tool is an important consideration. A milling tool with dense teeth can have 8 teeth with a diameter of 100 mm, while a tool with coarse teeth has only 6 teeth with the same diameter. Thick metal milling tools are ideal for rough machining due to their large rake surface, which reduces friction between the workpiece, the cutter body and the chip itself.
It should be noted that with a dense-tooth cutter, the cutting performance per tooth is lower than with a coarse-toothed cutter, even with the same feed rate.
Milling blade selection
Using an abrasive blade is the best option for fine milling tools. This type of insert provides greater dimensional accuracy while increasing the positioning accuracy of the cutting edge during milling, allowing for better surface roughness and machining precision. However, it is preferable to use a pressed blade for grinding as it can reduce processing costs.
Furthermore, the use of carbide inserts without sharp rake angles would reduce tool life, especially at small depths of cut and small feeds.
Concluding
Milling tools are important for any milling operation because these tools are attached to a milling machine to remove or cut materials into different shapes used for different operations. These milling tools are available in different versions for different milling purposes. It is recommended to consult a specialist for professional advice.
Do you have more questions about milling or other processes? Simply contact us and receive an offer today!
Common questions
What is the difference between end mill and face mill?
The main difference between a face mill and an end mill is that end mills use both the end and sides of the cutter, while face milling uses horizontal cuts.
How are end mills used?
End mills can be used to mill specific shapes and holes in a part during industrial processes such as milling, profiling, contouring, reaming, reaming, countersinking, and drilling. End mills have cutting teeth on the edges of the face and body. They are great for cutting different materials in different directions.
What is the difference between drills and mills?
There are several differences between a milling machine and a drilling machine. However, understanding their function can be an important clue to accurately distinguishing them. A drill is a perfect tool for drilling holes in a workpiece, so it must have a point angle that helps in alignment while the milling cutter is used to mill the plane so there is no point angle.
Additionally, the drill has a tapered bottom to allow the tool tip to penetrate, whereas the bottom of a milling cutter is flat.