Lithium-ion batteries are a complex system that includes positive and negative electrodes, separators, electrolytes, current collectors, binders, conducting agents and more.
The reactions involved in its production include electrochemical reactions of the positive and negative electrodes, lithium ions and electron conduction, and thermal diffusion.
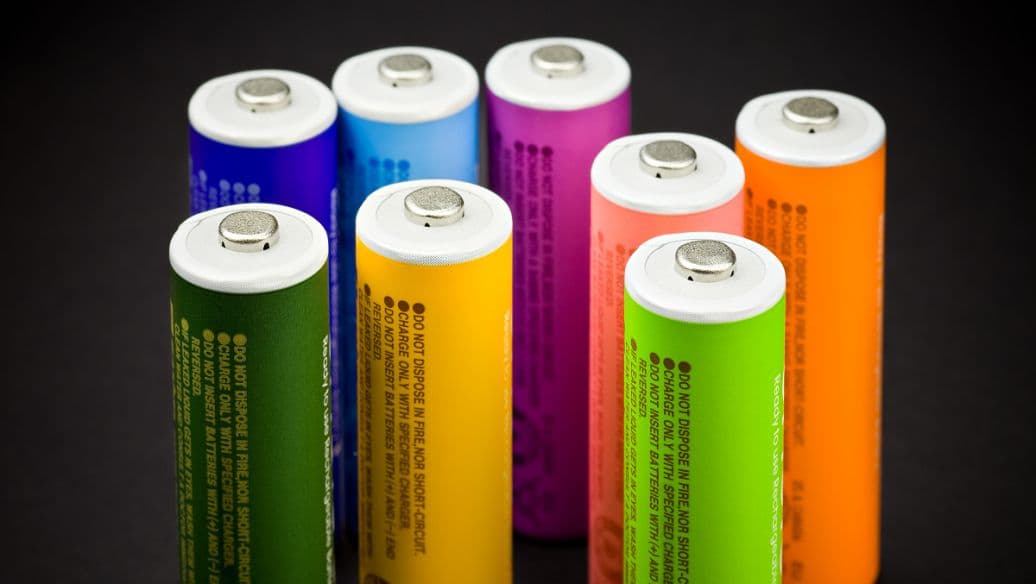
The lithium battery production process is quite long, involving more than 50 steps.
Lithium batteries can be categorized by their shape, such as cylindrical, square and pouch cells, and their production processes differ slightly. However, the overall process can be divided into three steps: the initial process (electrode sheet manufacturing), the intermediate process (cell synthesis), and the final process (forming and packaging).
Due to the high safety requirements for lithium-ion batteries, precision, stability and automation are highly demanded for lithium equipment during the manufacturing process.
Lithium equipment is process equipment used to manufacture and produce positive and negative electrode materials, separator materials, electrolytes and other materials through an orderly process.
Lithium equipment has a significant impact on the performance and cost of lithium-ion batteries and is one of the determining factors. Depending on different manufacturing processes, lithium equipment can be categorized into front-end, mid-end and back-end equipment, with a value ratio of approximately 4:3:3 in the lithium-ion battery production line.
Machines and equipment used in the lithium battery manufacturing process
The objective of the initial process is to manufacture positive and negative electrode sheets. The main processes in the initial process include mixing, coating, laminating, slitting, plate cutting and die cutting. The equipment used in this process includes mixers, coaters, laminators, cutting machines, plate cutting machines and die cutting machines.
Vacuum Mixer
Mixing the electrode materials (using a vacuum mixer) produces a paste by evenly mixing the solid-state battery materials for the positive and negative electrodes with a solvent. The mixing of electrode materials is the starting point of the initial process and is the basis for subsequent processes such as coating and lamination.
coating machine
Coating (using a coating machine) is the process of evenly coating the mixed paste on a metal sheet and then drying it to form the positive and negative electrode sheets. As the core process of the initial stage, the quality of the coating process has a profound impact on the consistency, safety and service life of the finished battery. Therefore, the coating machine is the most valuable equipment in the initial process.
Rolling machine
Lamination (using a lamination machine) is the process of further compacting the coated electrode sheet to increase the energy density of the battery. The smoothness of the electrode sheet after rolling directly affects the effectiveness of subsequent processes such as slitting. The uniformity of the active material in the electrode sheet also indirectly affects battery performance.
Laminating machine principle:
Unwinding → Unwinding with correction → Opposed rollers → Winding → Winding with correction
Cutting machine
Cutting (using a cutting machine) is the process of cutting a wide roll of electrode sheet into several narrow strips of the required width. During the cutting process, the electrode sheet experiences shear force and may fracture, affecting the quality of the resulting narrow strips. The smoothness of the edges of narrow strips, including the absence of burrs and wrinkles, is a key factor in evaluating the performance of the slitting machine.
Cutting machine principle:
Unwinding → Unwinding correction → Process correction → Traction → Main drive → Winding → Winding correction.
Sheet Cutting Machine
Sheet cutting (using a sheet cutting machine) includes welding tabs to the narrow strips of electrode sheet, attaching backing paper, encapsulating the tabs, or using laser cutting to form the tabs. These tabs are used in the subsequent winding process. Die cutting (using a die cutting machine) is the process of cutting the coated electrode sheets into a specific shape for use in subsequent processes.
Principle of die cutting machine:
Unwinding → Stamping → Die cutting → Traction → Winding.
The purpose of the intermediate process in lithium battery production is to manufacture the cell. Different types of lithium batteries have different technical routes and equipment in the intermediate stage process.
The intermediate stage process is essentially an assembly process that involves the orderly assembly of the positive and negative electrode sheets made in the front process with the separator and electrolyte.
Due to the different energy storage structures of square (pouch), cylindrical (laminated) and pouch cells, there are significant differences in the technical routes and equipment used in the intermediate stage process for different types of lithium batteries.
Specifically, the intermediate stage process for square and cylindrical cells mainly includes winding, injection and packaging, which require equipment such as winding machines, injection machines and packaging equipment (shell insertion machines, groove rollers, sealing machines and solder).
The intermediate stage process for pouch cells mainly includes stacking, injection and packaging, which require equipment such as stacking machines, injection machines and packaging equipment.
Rolling machine
Winding (using a winding machine) is the process of winding the electrode sheets produced in the front process or the narrow strips of electrode sheet made by a roll-to-roll die cutting machine onto the cell of a lithium-ion battery. This process is mainly used in the production of square and cylindrical lithium-ion batteries.
Winders can be divided into square winders and cylindrical winders, which are used for the production of square and cylindrical lithium-ion batteries respectively. Compared to cylindrical winding, the square winding process requires greater tension control, making the technology for square winders more challenging.
Stacking Machine
Stacking (using a stacking machine) is the process of stacking individual electrode sheets made in the die-cutting process into the cell of a lithium-ion battery, mainly used in the production of pouch cells.
Compared to square and cylindrical cells, pouch cells have significant advantages in energy density, safety and discharge performance. However, the stacking process involves multiple subprocesses and complex mechanisms that must work in parallel, making it challenging to improve stacking efficiency through complex dynamic control.
In contrast, winding speed and the efficiency of a winding machine are directly linked, with relatively simple ways to increase efficiency. Currently, there is a gap in production efficiency and yield between stacked and wounded cells.
injection machine
An injection machine (using an injection machine) is equipment used to inject a precise amount of electrolyte into the cell of a lithium-ion battery.
Injection machine principle:
Electrolytic ring insertion → Battery assembly → Electrolyte injection into battery → Vacuum extraction → Battery discharge.
Encapsulation equipment
Cell encapsulation (using encapsulation equipment such as shell insertion machines, groove rollers, sealing machines, and welding machines) is the process of placing the rolled cell into the outer casing of a lithium-ion battery.
Shell insertion machine principle:
Cell feeding → Insulation sheet feeding → Shell feeding → Assembly → Shipping.
Groove Roller Machine Principle:
Loading → Traction tape suction → Flow to lamination groove → Lamination → Unloading.
Sealing machine principle:
Material recycling → Feeding → Vacuum extraction → Punching → Packaging.
Welding machine principle:
Assemble the device → Laser welding → Tear off the protective film → Collect the internal resistance of all units → Check the tightness of all units.
The production objective of the back-end process is to complete the formation and packaging of the lithium-ion battery. At the end of the intermediate stage process, the functional structure of the battery cell has been formed, and the meaning of the back-end process is to activate it and form a safe and stable lithium-ion battery through testing, classification and assembly.
The main processes of the back-end process include forming, capacity classification, testing and sorting, and the equipment involved mainly includes loading and unloading machines and testing equipment.
Unloading equipment
Forming (using charging and discharging equipment) is a process of activating the battery cell by first charging it. During this process, an effective solid electrolyte interface (SEI) film is formed on the surface of the negative electrode to initialize the lithium-ion battery.
Capacity rating (using charge and discharge equipment) is used to measure battery cell capacity according to design standards after the forming process.
Charging and discharging the battery cell is an essential part of the capacity formation and classification process, which makes charging and discharging equipment the most commonly used main equipment in the back-end process.
The minimum working unit of a loading and unloading machine is a “channel”, and a “unit” (BOX) is made up of several “channels”. Multiple “units” combined form a loading and unloading machine.
Test Equipment
The testing process (using testing equipment) is carried out before and after charging, discharging and idle state, while classification is based on the test results to classify and select batteries after the capacity formation and classification process according to certain standards.
The importance of the testing and classification process is not only to eliminate defective products, but also to select batteries with similar performance, as cells are often combined in parallel and series in actual use, which helps to optimize the overall performance of the battery.
Conclusion
The production of lithium-ion batteries relies heavily on lithium-ion battery production equipment. In addition to the materials used in batteries, the manufacturing process and production equipment are important factors that determine battery performance.
At first, China relied on imported lithium-ion equipment, but after several years of rapid development, Chinese lithium-ion equipment companies have gradually caught up with Japanese and South Korean equipment companies in terms of technology, efficiency, stability and other aspects.
Chinese companies also have advantages in terms of cost-benefit and after-sales maintenance.
At present, China has formed a cluster of lithium-ion equipment companies, and they have become a calling card of high-quality equipment entering the international market. With the vertical alliance and expansion of lithium-ion leaders and their production abroad, the lithium-ion equipment industry is expected to enter a new period of rapid growth due to the downstream expansion of production.