The gear is the most important component of the gearbox. During operation, the tooth surface bears the contact stress, while the tooth root bears the bending stress. Consequently, the failure ways of gears are mainly categorized into pitting and scaling corrosion due to tooth surface fatigue and tooth fracture caused by tooth root fatigue.
Carburizing and tempering are the most used and developed processes for high-speed and heavy-duty gears.
This method can simultaneously improve the contact fatigue resistance of the tooth surface and the bending fatigue resistance of the tooth root. However, the carburizing and quenching process is complicated, and various types of defects may occur during heat treatment, which may lead to early gear failure.
During the fatigue resistance test of a transmission assembly newly developed by our company, one of the gears broke.
Design specifications require gear material to be 8620H. It went through carburizing and quenching and was then tempered at low temperature. The effective depth of the hardened layer is 0.8 to 1.3 mm, the surface hardness is 58 to 64HRC, and the core hardness is 30 to 45HRC.
To determine the cause of tooth fracture, we perform tests and analyze the morphology of the fracture, the material and the quality of the heat treatment.
1. Physical and chemical tests and analysis
(1) Macro observation
Figure 1 illustrates the general appearance of the failed gear. Several teeth are broken at the root and the number of broken teeth exceeds half of the total number of teeth.
The macromorphology of the fracture is shown in Figure 2.
Based on fracture morphology, most fractures have obvious characteristics of fatigue fracture. The source of the fracture is located at the root of the tooth.
The area of smooth, outward-radiating fatigue expansion accounts for approximately 1/3 to 1/2 of the total root area.
The fracture surface of the transient fracture area is rough and dark gray.
In addition to fatigue fractures, some gear fractures do not exhibit fatigue fracture characteristics and result from single overload fractures.
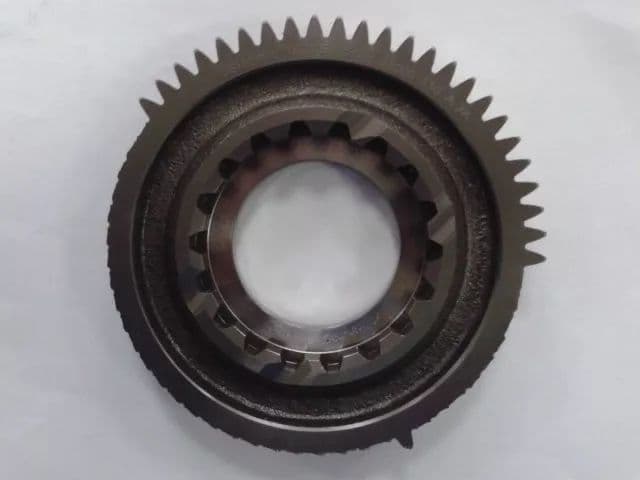
Fig. 1 Overview of broken teeth
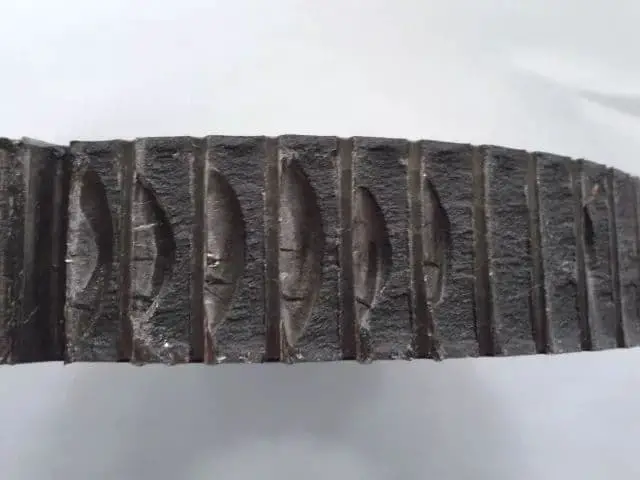
Fig. 2 Fracture morphology
(2) Fractography
After sampling, the fracture morphology was observed under a scanning electron microscope.
Figure 3 shows what the crack source looks like.
The source of the crack is located at the root of the tooth. From the figure, it can be seen that the origin of the fracture crack is not converging to one point, but is linear.
The surface of the crack source is smooth due to repeated friction and extrusion.
Upon further examination, abnormal black structures are visible at the origin of the crack (see Fig. 4).
Observation of the microscopic morphology of the fatigue growth zone at 1000x magnification is shown in Fig.
At high magnification, fatigue striations and radial prisms can be seen.
Figure 6 illustrates that the appearance of the transient fracture zone is a ripple + quasi-cleavage fracture, indicating good toughness of the gear center.
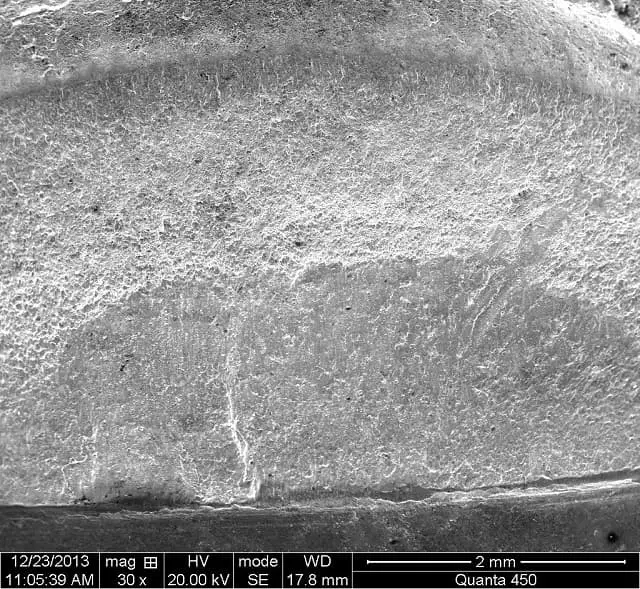
Fig. 3 Crack Source
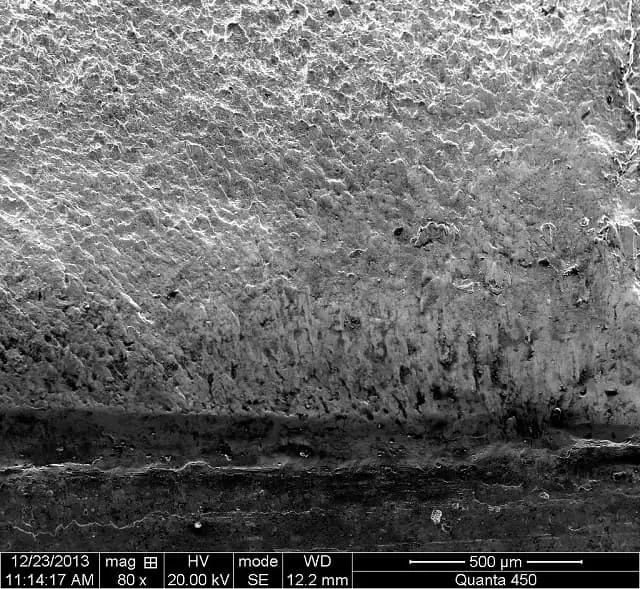
Fig. 4 Black Crack Source Structure
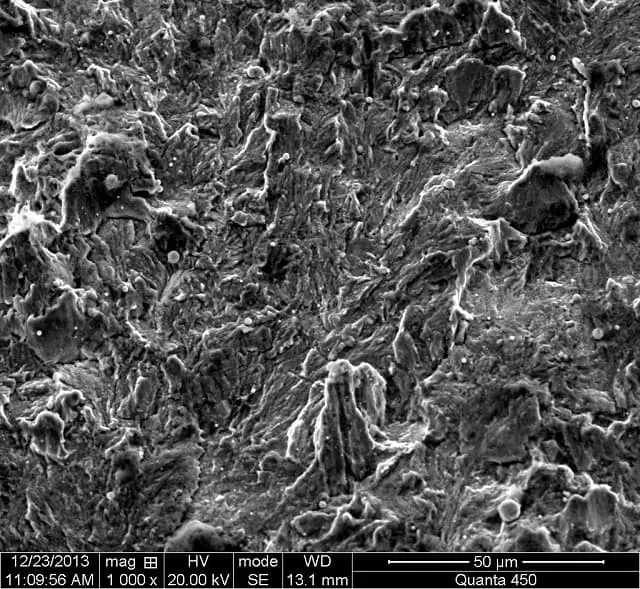
Fig. 5 Fatigue Propagation Fracture
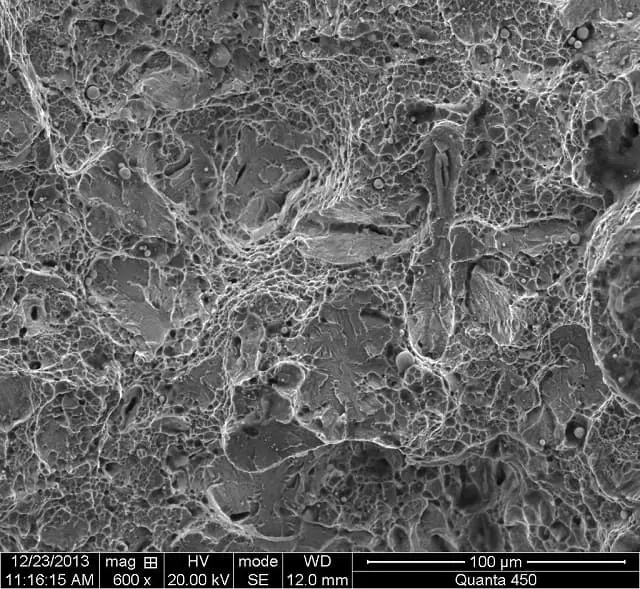
Fig. 6 Morphology of ripple + quasi-cleavage in the transient fracture zone
(3) Gear material inspection
Samples were taken from the broken gear for chemical composition analysis and the results are presented in Table 1.
According to the analysis, the chemical composition of the gear meets the technical requirements of the SAEJ1268 standard for 8620H steel.
Table 1 Results of chemical composition tests (mass fraction) (%)
Element | W | s | P | Yes | Mn | Cr | No | Mo | Ass |
Standard value | 0.17~0.23 | ≤0.040 | ≤0.030 | 0.15~-0.35 | 0.60~0.95 | 0.35~0.65 | 0.35~0.75 | 0.15~0.25 | ≤0.35 |
Detection value | 0.22 | 0.017 | 0.010 | 0.28 | 0.87 | 0.58 | 0.45 | 0.18 | 0.086 |
(4) Gear heat treatment quality inspection
To test the quality of heat treatment, place the intact gear next to the broken one.
The surface hardness is 61 HRC and the core hardness is 45 HRC.
The surface structure comprises martensite and retained austenite, with a retained austenite content of approximately 15%. The center consists of lathed martensite and a small amount of bainite.
The effective depth of the hardened layer at the height of 1/2 tooth is 1.01 mm.
The gear has undergone carburizing and quenching, and all heat treatment indexes meet the design requirements specified in the drawing.
To prepare a sample, use a precision cutting machine to cut the gear along the middle of the tooth width, and then examine the metallographic structure of the tooth root on the cutting surface using a metallographic microscope.
In the absence of corrosion (see Fig. 7), severe black tissue can be observed on the root of the tooth, distributed in a network, with an average depth of around 20 μm. The individual depth of black fabrics reaches up to 30 μm.
A straight fissure originates from the black tissue of the tooth root and extends inward perpendicular to the tooth root.
Observation after corrosion (see Fig. 8) reveals that there are normal case-hardened and hardened structures on both sides of the crack.
Metallographic observation of the two end faces of the sample root shows no signs of cracks.
Based on the above inspection, it is inferred that the observed cracks are generated during use, suggesting that the tested teeth developed fatigue cracks that expanded, and the test was stopped before fracture occurred.
If the test continued, fracture would be expected to occur.
According to metallographic analysis, the crack is closely associated with the black tissue at the root of the tooth.
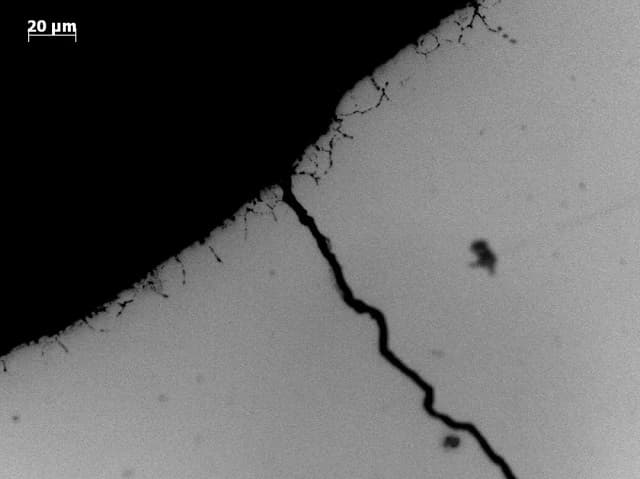
Fig. 7 Black tissue and tooth root crack (500 ×) No corrosion
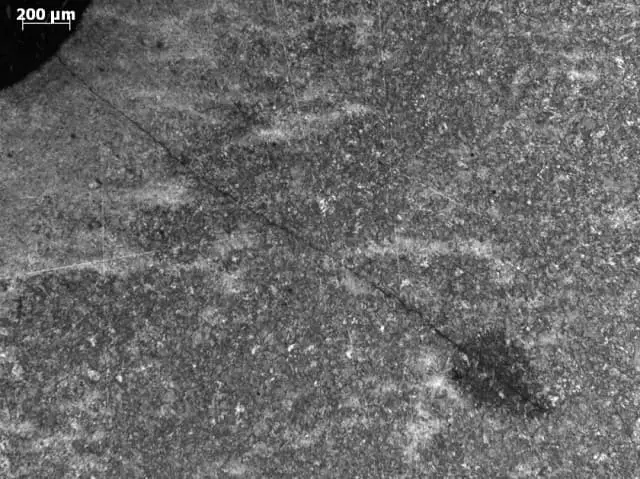
Fig. 8 Structure on both sides of the crack (50×)4% nitric acid alcohol solution
2. Analysis and discussion
Most broken teeth on failed gear are due to fatigue fracture, with the cracks starting at the root of the middle part of the tooth width.
Through metallographic and scanning electron microscope observation of the tooth root, it is evident that the black tissue becomes the source of crack initiation during gear use.
As the number of operations increases, the crack source expands, eventually leading to gear fracture failure.
After carburizing, the surface microstructure of alloy steel generally presents black dotted, reticulated or banded microstructures distributed along the grain boundary.
The reason for this type of structure is that oxygen in the carburizing medium diffuses into the steel, forming oxides of chromium, manganese, titanium, silicon and other elements at the grain boundary. This results in depleted alloying elements at the grain boundary, causing a decrease in local hardenability and the appearance of black austenitic decomposition products such as troostite.
Research carried out both nationally and internationally indicates that the presence of black fabric significantly reduces the surface hardness, flexural fatigue resistance and contact fatigue resistance of parts, negatively impacting their useful life.
As such, many well-known vehicle manufacturers, both domestically and abroad, have set specific requirements for the depth of the black fabric. For example, German car manufacturers such as Benz and BMW require that the depth of the black fabric does not exceed 3μm.
Furthermore, FAW Group is planning to reduce the depth of the black fabric from less than 20μm to less than 3μm.
3. Suggestions for improvement
Through the above inspection and analysis, it is evident that the depth of the black structure in the surface metallographic structure of carburized and quenched parts requires strict control. Black fabric control mainly starts with the following two aspects:
- Improving the purity of the carburizing gas and reducing the oxygen content. This can be achieved by strictly controlling the purity and water content of carburizing agents such as methanol and acetone and regulating the amount of air.
- Adopt more intense quenching and cooling methods, such as using a quenching medium with stronger quenching and cooling performance or employing faster quenching, cooling, and stirring.