Support structures are an essential component for the successful manufacturing of 3D printed parts.
Although one of the main advantages of 3D printing is its ability to create complex, free-form geometric shapes, much of the design freedom offered by 3D printing is difficult to achieve without the use of support structures.
They are crucial for preventing distortion and collapse of parts, among other uses; therefore, understanding and designing support structures is a necessary skill for any additive manufacturing engineer.
This article discusses the requirements, pros and cons, removal, and how to minimize the use of support structures in various printing technologies.
The importance of support structures in 3D printing
Used in conjunction with virtually all 3D printing technologies, support structures play a crucial role in ensuring the printability of parts during the 3D printing process.
The supports help prevent deformation of the parts, fix them to the printing base and ensure their connection to the main body of the printed parts. Much like scaffolding, these supports are used during the printing process and removed afterwards.
Printing parts with complex design features such as protrusions, holes and bridges presents significant challenges.
Take metal 3D printing as an example; When printing includes protrusions or bridge structures, deformation, even collapse, may occur during the process if support structures are not used.
These support structures help prevent the collapse of parts formed during printing, greatly increasing the printing success rate. However, not all overhanging structures require additional support.
If the vertical angle of the overhang is less than 45 degrees, no support is needed.
When the vertical angle of such a structure is less than 45 degrees, the 3D printer has minimal horizontal displacement in successive layers, allowing each layer to provide support for the next level.
Therefore, 45 degrees is a critical angle, below which no support is needed. Of course, this also depends on the performance of the printer and the properties of the materials used. If printer performance is poor, support may be required even for angles less than 45 degrees.
Furthermore, technologies such as metal 3D printing often involve high-temperature processes, during which the support can also serve as a heat sink.
This is because the support structures added during the metal additive manufacturing process help move heat away from the part, preventing the formation of residual stresses due to high temperatures during printing and preventing defects such as warping, warping and cracking.
Of course, it's not just metal 3D printing that considers adding supports; Almost all 3D printing technologies need to include, to some extent, support structures.
The following table illustrates the differences in support usage between various 3D printing methods:
Technical Principles | Materials | Is support needed? |
Selective Laser Melting (SLM) Direct Metal Laser Sintering (DMLS) Direct Energy Deposition (DED) Electron Beam Melting (EBM) | Metallic Materials | Yes |
Stereolithography (SLA) | Photopolymer | Yes |
Selective Laser Sintering (SLS) | Powder Materials | No |
Blasting of materials | Powder Materials | Yes |
Fused Deposition Modeling (FDM) | Thermoplastic Plastic | Yes |
Adhesive spray | Powder Materials | No |
Powder bed fusion (SLM, DMLS, EBM)
Support structures are indispensable in metal 3D printing. Although the components formed by powder bed fusion technology are surrounded by loose powder, which provides some support, these technologies always require support to ensure their fixation to the base and to mitigate the effects of residual stress.
Without support structures, protruding or tilted components, as well as internal metal stress, can damage the printed object itself, leading to print failure. Generally, the supporting structures in powder bed-based printing technology are mainly divided into two types:
Linear support: This type of support consists of vertical columns connected to the entire protruding structure. However, this type of support is more difficult to remove.
Tree-like support: This type of support resembles tree branches in shape. It is used to support the protruding parts of the component. It is only connected to the protruding positions.
Its advantage is that it is easier to disassemble and does not cause damage to the component itself.
However, it should be noted that tree-shaped support structures are only suitable for non-flat overhangs. For flat ledges, they cannot provide enough support.
Support can be added to the contact area between the bottom of the printed part and the print bed, where residual stress is most concentrated.
This helps move heat away from the part, thus minimizing thermal deformation that can cause cracking, warping, sagging, delamination and shrinkage.
Direct Energy Deposition (DED)
Direct Energy Deposition is a process that manufactures parts by directly melting the material and building it layer by layer.
Unlike parts formed by powder bed fusion that are supported by the surrounding powder bed, parts printed using DED exist independently in three-dimensional space.
Consequently, they also require support structures to ensure part stability, printability of complex features, and heat dissipation.
1. Support project
When designing supports for parts produced using powder bed fusion technology, it is crucial to ensure that they can be easily separated from the main body, otherwise they cannot be removed during post-processing.
Supports for metal parts are typically printed as a grid structure.
In this way, they act as heat sinks, transferring heat from the part, allowing it to cool in a more controlled manner and avoiding distortions, in addition to saving material costs and construction time.
Adding more supports generally results in more accurate parts, but it also increases costs and post-processing time. Interestingly, Dutch company MX3D has created a metal 3D printing tool that combines a multi-axis robotic arm with a welding machine, allowing the printing of metal parts without the need for any supports.
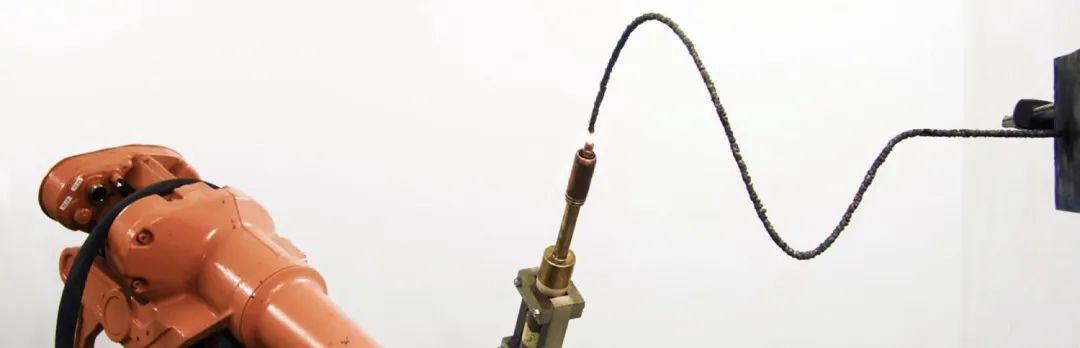
2. Removal of support
Removing supports from metal parts is generally more challenging than polymer-based processes and typically requires cutting tools.
Additionally, if the appearance of the finished part is important, post-processing (such as polishing) of the metal part is necessary to obtain a smooth surface finish.
During model disassembly, most supports are easy to remove if the method is correct. First, you can gently open the brackets with your fingers where you can manipulate them manually.
For special positions, we may choose to use tools to dismantle the supports, including needle-nose pliers, scrapers and carving knives.
Stereolithography (SLA)
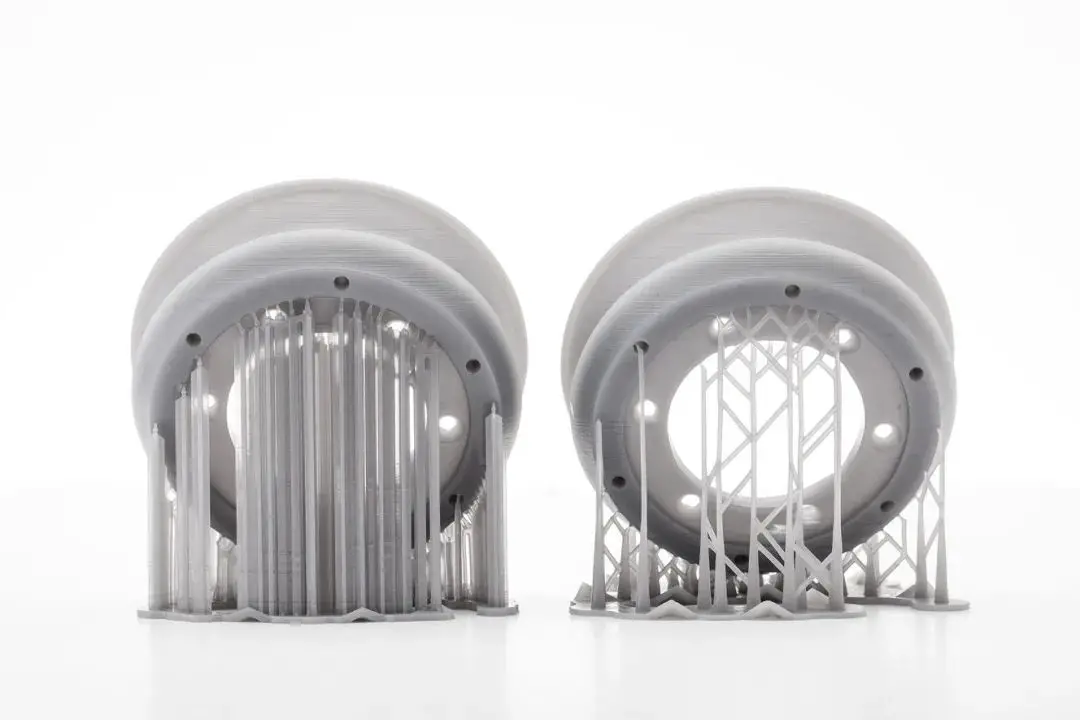
Stereolithography works by using a light source to solidify liquid resin. This technology requires support structures to firmly attach parts to the print base and prevent warping.
The supports used in SLA are very thin and lightly touch the parts to save materials. This means they can be easily removed manually, by hand or with pliers. However, as removing the supports will leave marks on the final piece, it is necessary to sand it to ensure a smooth surface finish.
1. Support project
SLA is often used for applications that require aesthetics or smooth surface finishes, such as visual prototypes, molds, and hearing aids.
If this is the case, it is critical to design the parts to ensure that the front area of the print does not come into contact with the support structures. This is where part orientation design comes into play.
Part orientation is a crucial consideration in the design phase because repositioning parts can help reduce the amount of support needed. For example, tubular pieces, if placed horizontally, will take up more space and therefore require more support.
On the other hand, positioning the same part vertically ensures that it connects to the build plate with minimal support.
Fused Deposition Modeling (FDM)
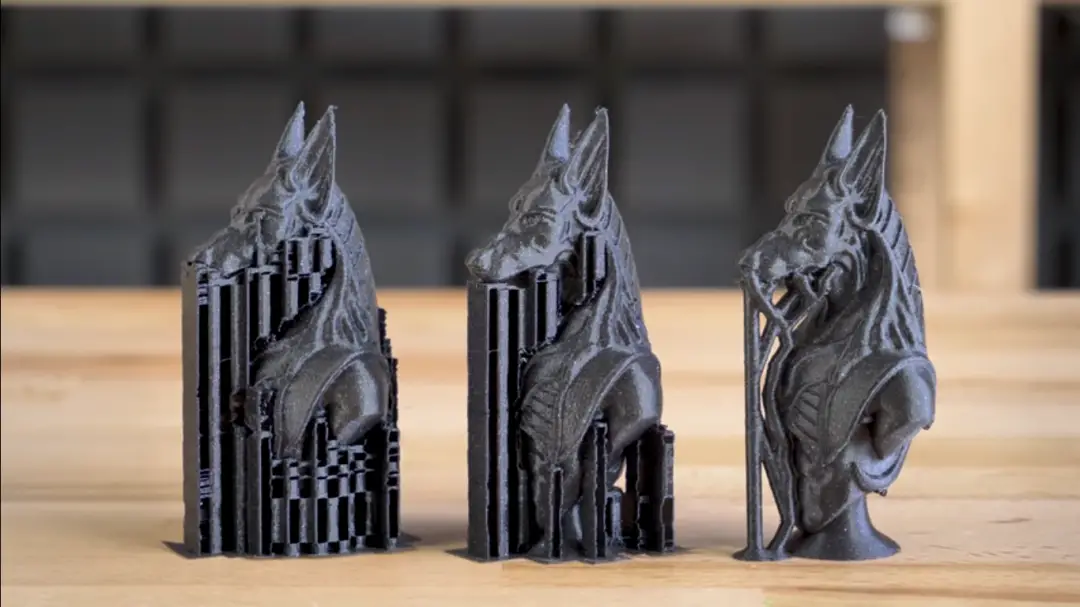
Fused Deposition Modeling (FDM) technology creates parts by extruding heated filaments layer by layer, each of which bonds to the previous one after cooling and solidifying.
1. Support project
In the FDM process, each layer protrudes slightly so that it can extend beyond the width of the previous layer. This means features can be created at angles of up to 45 degrees without support.
However, when the overhang of an FDM part exceeds 45 degrees or the part includes features such as bridges and protruding surfaces greater than 5 millimeters, support is required. Support in FDM can take the form of a truss structure or a tree-shaped structure.
2. Removal of support
One technique for removing supports from FDM prints is through a chemical dissolution solution.
Typically, industrial FDM 3D printers (with two print heads) use soluble support materials such as Polyvinyl Alcohol (PVA) and High Impact Polystyrene (HIPS). These materials can be deposited into the model using a separate extruder.
Although PVA dissolves in water, it can be affected by temperature changes, causing blockages in the print head. HIPS, on the other hand, dissolves in limonene instead of water and is not easily affected by temperature changes.
The use of soluble supports eliminates the need for manual operations and the need for additional sanding and polishing to remove traces left by the supports. On the other hand, this process can be time-consuming (taking several hours) and expensive.
Blasting of materials
When using a Material Jetting 3D printer, support for protruding structures is always required, regardless of the angle.
However, these supports are usually made of different materials that are water-soluble or can be easily removed later with pressurized water or by immersion in an ultrasonic bath.
Selective laser and binder jet sintering
Selective Laser Sintering and Binder Jetting are powder-based technologies that generally do not require support structures.
This is because in these two technologies the printed parts are encapsulated in loose powder that serves as a support structure.
Disadvantages of brackets
While necessary, support structures increase the overall printing time and material costs of the production process.
Material expenses:
Media generation requires additional material during the printing process, thus increasing time and material costs. Equally important is the fact that the supports are not reusable and are normally discarded, leading to material waste.
Limited geometric freedom:
When removing supports manually, the use of hands or tools must be considered when designing the supports. However, this may limit your ability to design certain geometric shapes that require support but are inaccessible manually or with tools.
Added time:
Designing a part to accommodate support structures and then creating the supports themselves takes more time. Despite the availability of software that automatically generates supports, creating support structures for industrial applications still requires manual modifications and a certain level of design knowledge.
Additional post-processing:
Once the part is complete, the supports must be removed, sometimes manually, thus increasing the time required for post-processing.
Risk of Damage: During the post-processing phase, supports must be removed and the surface of the part must be polished.
Any incorrect handling during disassembly of the supports can cause defects on the surface of the part, affecting its dimensional accuracy and aesthetic appearance.
Additionally, when supports are placed incorrectly, such as in thin structures, structural fractures can occur. They can break along with the supporting structures, leading to complete print failure.
Therefore, the use of support structures has certain disadvantages and should only be added when necessary.
Furthermore, we can also avoid using chamfered brackets. Chamfering transforms the overhang locations into safe overhangs with angles of less than 45 degrees, eliminating the need for supports and ensuring efficient use of the material.
Four Methods for Minimizing Supports
Reducing the number of supports needed is often a sound strategy. Helps save material costs and production time. Here are four essential tips on how to maximize your reduction while saving printing time and materials:
1. Choose the ideal part orientation
Experimenting with the orientation of the pieces is one of the best ways to reduce the number of supports needed. Correct orientation significantly impacts print time, cost and part surface roughness.
Depending on the direction of the piece (vertical, horizontal or angular), fewer or more supports may be needed.
Consider a piece printed in the shape of the letter 'T'. Positioned in its regular direction, both arms of the letter would collapse without support structures. However, if the orientation of the part is inverted – arranged in an inverted “T” position – no support is necessary.
This example illustrates that a part can be constructed in several ways. Each face of the part can have a different surface connected to the print bed, implying different support needs. These needs largely depend on the orientation of the part.
Another example: When designing parts with hollow tubular features, a horizontal orientation takes up more space, while a vertical or angled orientation saves space and reduces the number of supports needed.
2. Optimizing support structures
When supports are unavoidable, they must be optimized to use as little material as possible and speed up the printing process. For example, topology optimization design and truss structure support can be used to reduce the volume of supports, thus saving material.
For many 3D printing processes, conventional support generation techniques are limited to producing strictly vertical structures. They don't save space, especially when there are many areas above the print bed that need support.
Conversely, creating tree-like support structures may be a viable choice. These supports resemble a branching tree and can reduce material usage by approximately 75% compared to straight vertical structures.
Autodesk Meshmixer is one of the software tools available to create such structures for FDM, SLA, and DMLS processes.
3. Using Fillets and Chamfers
Fillets and chamfers can serve as alternative solutions for creating support structures on protruding surfaces exceeding 45 degrees.
A chamfer is an angled or chamfered corner or edge, while a fillet is a rounded corner or edge. Essentially, these features change angles greater than 45 degrees to angles of 45 degrees or less and can be added to the interior or exterior of a part.
4. Segmentation of printed parts
For highly complex 3D models, it often makes sense to print the parts individually and then assemble them. This not only reduces the number of media, but also speeds up the printing process, saving material.
However, keep in mind that if 3D printed parts are assembled, they must be printed in the same orientation to ensure a proper fit together.
3D Printing Supports: Necessary but Frustrating
For a long time, support structures were seen as an inevitable “disadvantage” in 3D printing. However, recent advances in hardware and software are slowly challenging this notion.
Take, for example, Desktop Metal, a manufacturer of metal 3D printers, which recently developed a solution known as “Separable Brackets” for its studio and production systems, securing a patent on the process.
These supports for 3D printed metal parts can be removed manually. Desktop Metal's Separable Supports operate using a layer of ceramic powder as the interface between the part surface and the support structure.
After the sintering process, the ceramic layer dissolves, allowing effortless removal of the part supports.
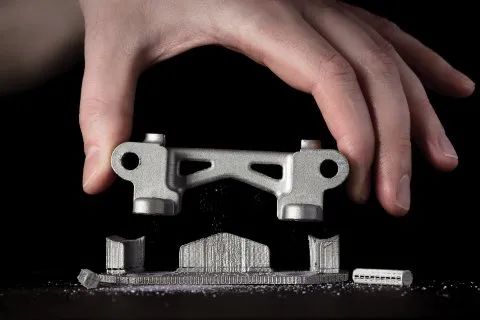

PostProcess Technologies is another company that aims to simplify and speed up the support removal step for 3D printed parts. The company offers a range of automated, hands-free support removal solutions for additively manufactured parts through FDM, SLA, PolyJet and CLIP technologies.
However, one company has gone even further in the realm of support. Velo3D, the company behind the Sapphire powder bed fusion system, offers a technology called Intelligent Fusion for its system, which allows for the printing of complex metal parts, with a focus on achieving nearly support-free printing.
Compared to other metal powder bed systems, the use of Velo3D's proprietary simulation software and closed-loop monitoring can reduce the supports required for part production by up to five times.
In 2021, SLM Solutions launched “FreeFloat Supportless Technology”, which significantly reduces or eliminates the need for support structures in part printing through the unified integration of multiple technologies.
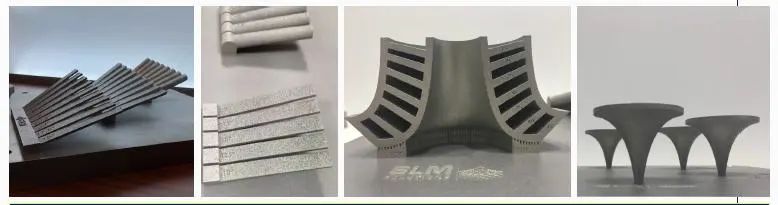
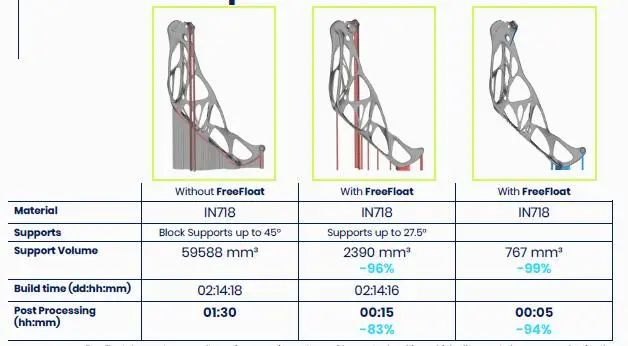
In 2022, EOS experts developed a variety of process optimization techniques for the production of unsupported 3D printed parts such as stator rings, casings, turbine pumps, oil tanks, heat exchangers, valves and impellers, the closed impeller being a particularly typical example.
By optimizing design software and parameter sets, EOS has enabled users to print cantilevers and bridges at much lower angles, sometimes down to zero degrees, requiring significantly fewer supports, or none at all.
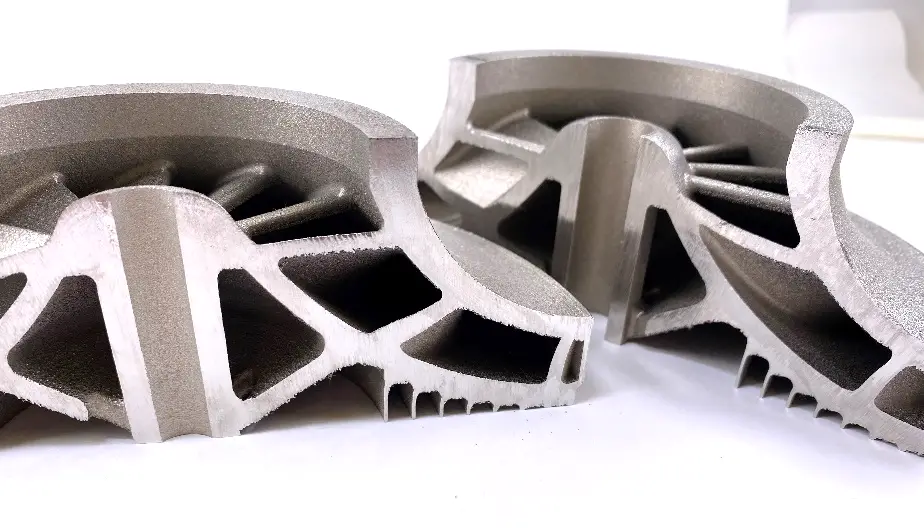
Without a doubt, domestic manufacturers have made notable advances in stand-free printing. Not long ago, it was reported that leading 3D printing company Polite had discovered a solution for unsupported printing: structures overhanging less than 30° do not require support.
Polite met the challenge of standless SLM metal 3D printing technology.
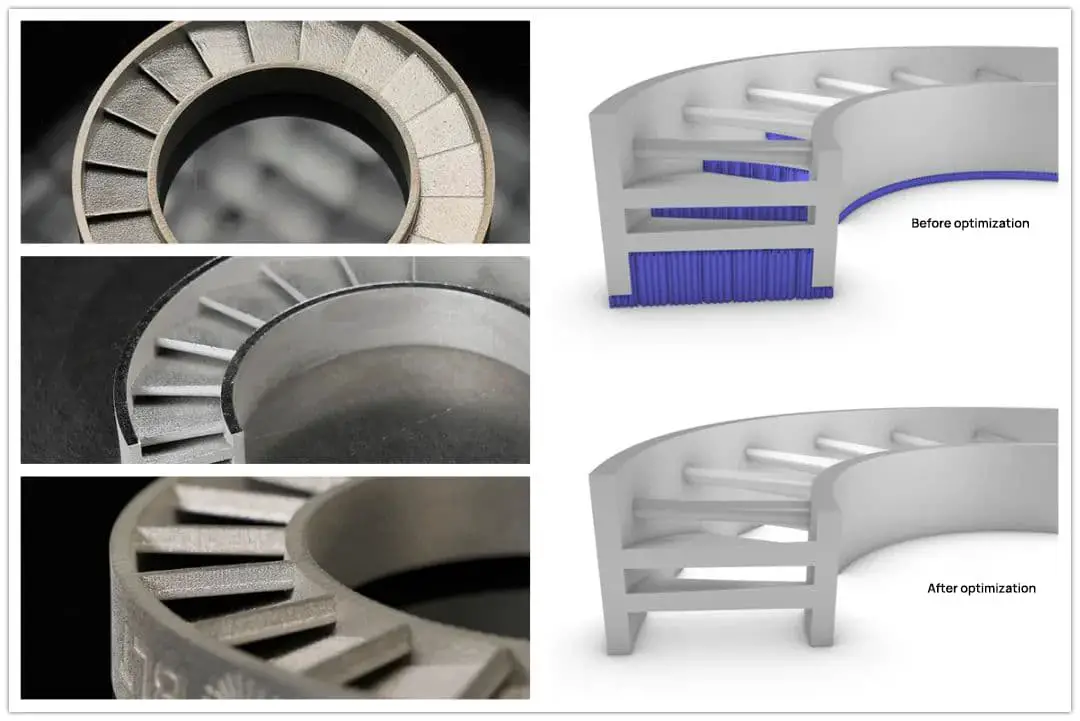
Overall, optimizing support design and removal is a key challenge to making the 3D printing workflow faster and simpler.
As can be seen from the examples above, the additive manufacturing industry is continually developing solutions to overcome this challenge.
However, in addition to technology, professionals need a higher level of skills and knowledge to present better solutions.
We hope this article has expanded your knowledge on how to use support structures more effectively in 3D printing, thus helping to transform them from enemies to allies.