Whether it involves manual operations or equipment processing, a growing number of sheet metal processing companies are now integrating fillet processing into their parts processing process chain.
Rounding the edges of parts is crucial not only to avoid industrial accidents, but also to ensure good processing of the parts, especially after precise rounding.
Here are five practical tips for fillet machining:
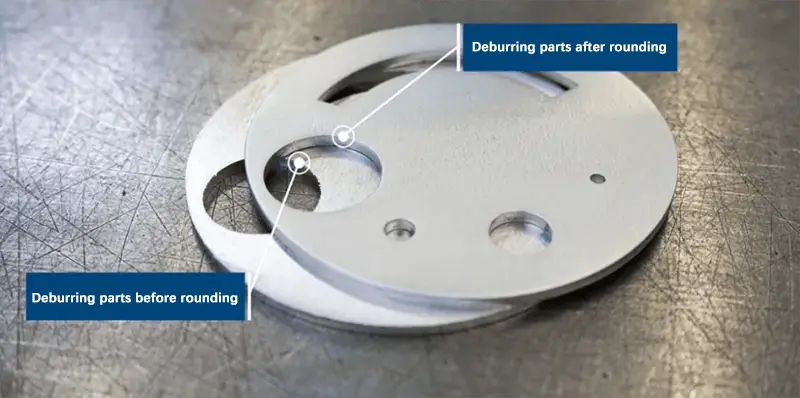
1. Cost calculation
In recent times, sheet metal processors have become increasingly aware of the advantages of fillet machining in simplifying subsequent machining processes.
Some pieces are polished, brushed and buffed by hand, while others use angle grinders for these operations. But which method is better?
Firstly, it is essential to calculate the cost of consumables involved in burr processing for your company. Although many companies have integrated fillet treatment into their process chains, they are often unaware of the real costs, such as labor, abrasive tools and machine energy consumption.
Therefore, it is important to ask several critical questions, such as the amount of labor and man-hours required for deburring and whether deburring is necessary for both sides of the parts.
2. Reduce labor hours and resources for deburring
If you need to integrate the deburring process into your production process, you must also consider how to optimize the logistics process before and after fillet machining.
For example, you need to reasonably organize processes such as material flow, manipulator, online operation or rotary parts transportation.
It is also essential to save working hours and resources and reduce the work intensity of operators, as lifting and turning parts weighing less than 25 kg requires considerable physical strength.
Furthermore, manual deburring can cause workers' hands to vibrate for a long time, which can negatively affect their health.
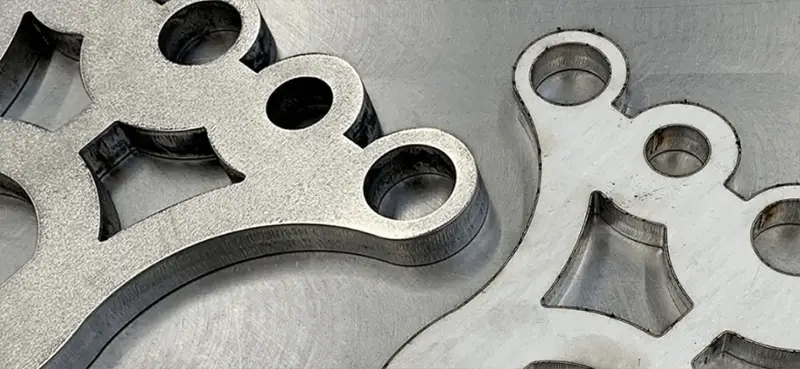
3. Make a reasonable choice and focus on the important deburring process
The term “deburring” generally encompasses various sheet metal processing operations, including removing slag, burrs, fillets, and oxide layers from sections, as well as providing final surface treatments to parts.
Therefore, it is crucial to accurately define the requirements of the deburring process before selecting equipment.
For example, if you need deburring and light filleting of 80% of the parts, you should prioritize this main requirement when formulating the processing process. It is not advisable to simultaneously integrate the remaining 20% of surface treatment requirements into the production chain.
4. Process according to actual needs
If you intend to manufacture high-quality sheet metal parts, rounding the sheet metal edges is an essential process. This process ensures that the burr is removed, thus reducing the risk of industrial accidents during operation and optimizing the next processing steps, such as welding or spraying.
Before starting fillet treatment, it is necessary to determine the precision of the fillet machining of the part. For example, you can determine specific machining accuracy based on the required anti-corrosion performance. Generally, fillet machining can be carried out according to actual needs.
However, it is important to follow the “less is more” principle when meeting machining requirements. This is because doubling the machining depth would require four times the cutting capacity, resulting in an increase in the cost of grinding consumables.
5. Unborn things do not need to be removed
The application of deburring technology in sheet metal processing has led some processors to mistakenly believe that they can operate carelessly when cutting or stamping plates, assuming that deburring treatment will resolve any burrs that may occur. However, this view is a big mistake.
In fact, careful cutting and stamping processes can reduce the occurrence of burrs on parts, saving subsequent man hours and reducing wear on deburring machines.
For example, an advanced plasma cutting machine can produce sheet metal parts with fewer burrs, but only if the cutting speed, operating current, and plate spacing are set correctly. Therefore, deburring treatment should be seen as a complementary rather than a corrective step.
Improve part quality through fillet treatment
Sheet metal processing companies should not only focus on integrating advanced cutting technology into their production process, but also include deburring and fillet treatment in their process chain planning.
By integrating deburring technology perfectly tailored to their production needs, companies can improve product quality and sustainability at a low cost. This technology can be seamlessly integrated into your processing line to play a positive role in the overall production process.