The mold manufacturing level is an important indicator to measure the manufacturing level of a country's product, and the mold itself has a high cost, known as “black gold”.
With the development of the automotive industry, especially the rapid development of new energy vehicles in China, the demand for molds has continued to increase, and the requirements for mold quality and service life have become increasingly higher.
Therefore, it is necessary to reasonably choose the mold material, develop the correct heat treatment process, select the appropriate surface treatment method, and research and develop new mold materials.
In this article, we use the actual production of our company's die casting mold material as an example to analyze and discuss the process methods to extend the service life of molds.
Manufacture of molds for pressure casting
Technical requirements
The technical requirements for manufacturing die casting molds are as follows:
- Material: H68M
- Dimensions: 400mm × 910mm × (3000~5000mm)
Production process: Electroslag ingot → Cutting → Heating → Forging → Heat treatment → Machining → Inspection → Shipping.
⑴ Surface hardness requirement: ≤229HBW, single hardness difference: ≤40HBW.
⑵ Forging ratio: ≥5.
⑶ Performance test requirements: Notch impact energy: not less than 25J, non-notch impact energy: not less than 350J.
⑷ UT non-destructive test equivalent to individual defect: ≤1.0mm. Dense defects are not allowed.
⑸ Grit size: finer than level 6.
⑹ Inclusion requirements: See Table 1.
Table 1: Inclusion requirements for mold materials
Class A | Class B | Class C | Class D | Class Ds (Level) |
||||
Thick | Fine | Thick | Fine | Thick | Fine | Thick | Fine | |
≤0.5 | ≤0.5 | ≤1.0 | ≤1.0 | ≤0.5 | ≤0.5 | ≤1.0 | ≤1.0 | ≤1.0 |
⑺ Raw materials are produced in electric arc furnace + refining + vacuum degassing + electroslag remelting. The chemical composition is shown in Table 2, with (H) ≤2.0PPm, (O) ≤25PPm and (N) = 70~170PPm.
Table 2: Chemical Composition of Mold Materials (mass fraction, %)
Element | W | Yes | Mn | P | s | Cr | Mo | V |
Minimum | 0.36 | 0.25 | 0.25 | – | – | 4.95 | 2.2 | 0.50 |
Max. | 0.42 | 0.45 | 0.45 | 0.015 | 0.005 | 5.25 | 2.8 | 0.80 |
Production process:
⑴ Use a 12.5t electroslag ingot to remove the sprue and burr from the ingot plate, and then load it into the gas heating furnace. The heating temperature is controlled at 1260°C. After 24 hours of isolation, forging begins using the two-bounce, two-pull process with a forging ratio greater than 6, as shown in Figure 1.
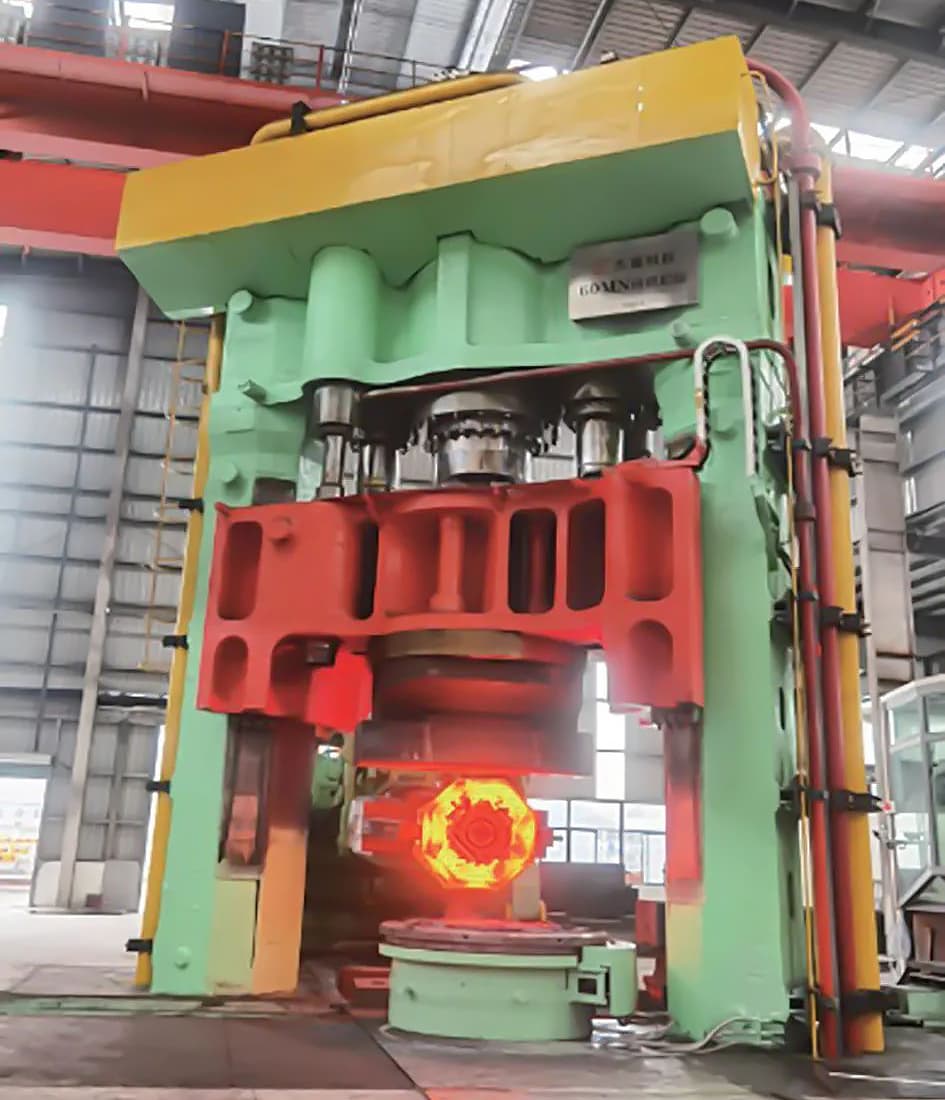
⑵ After forging, adopt air cooling control and timely place it in the annealing furnace for post-forging heat treatment at about 400°C. The heating temperature for heat treatment is 850°C for 20 hours of insulation and then 730°C for 30 hours of insulation. The heating oven is cooled to less than 30°C/h, and the mold is removed from the oven when the oven temperature is below 450°C.
⑶ After heat treatment, carry out machine processing according to the drawing requirements. After processing is complete, run the UT test. Qualified products will be shipped.
The main factors that affect the service life of die casting molds are:
⑴ The purity of the inside of the material.
⑵ Reasonable selection of material manufacturing process.
⑶ The rationality of casting mold design and working conditions.
Process improvement for new die casting mold material H68M
⑴ According to the previous production process, the service life of H68M mold material has not been significantly improved compared with other domestic materials.
Our technical personnel followed and analyzed the casting process, forging process control and on-site heat treatment control to obtain information on purity, structure and grain size, as shown in Figures 2, 3 and 4. This provided experience to further improve the material. control of useful life in the future.
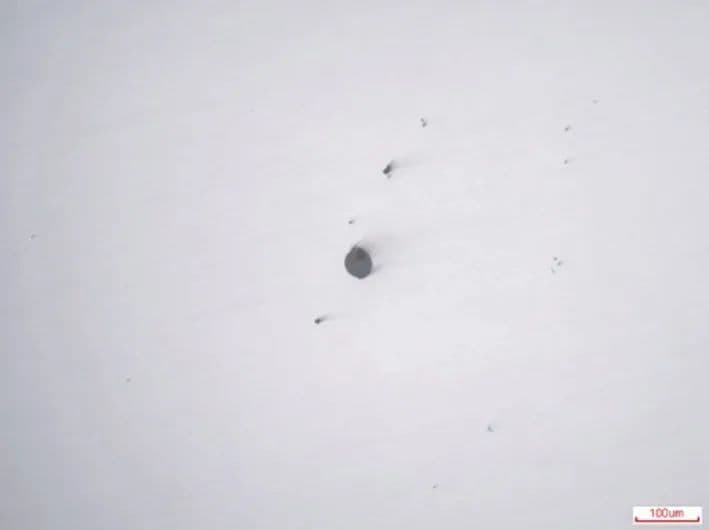
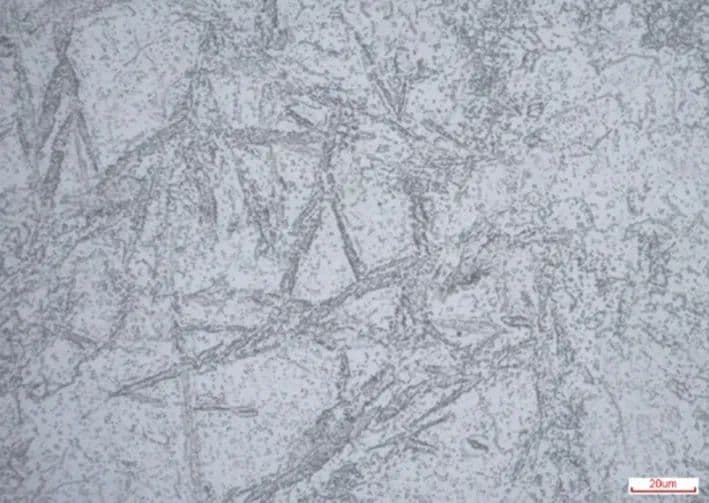

In relation to the above extensive experimental data, our technical research team has analyzed and implemented the following process improvements for casting, forging and post-forging heat treatment.
Improvement measure 1
The ideal microstructure of the base alloy was achieved by reasonable composition design. The improved chemical composition is shown in Table 3.
Table 3 Adjusted Chemical Composition (mass fraction, %) of H68M after Upgrade
Element | W | Yes | Mn | P | s | Cr | Mo | V |
Minimum | 0.36 | 0.20 | 0:30 | – | – | 4.95 | 2,350 | 0.55 |
Max. | 0.40 | 0.40 | 0.45 | 0.015 | 0.005 | 5.15 | 2.65 | 0.75 |
Improvement measure 2
Clean scrap steel and alloys were used as raw materials, and effective measures such as LF refining, vacuum degassing and electrical slagging under protective atmosphere were employed to reduce the content of impurity elements, harmful gases and inclusions in steel.
This resulted in obtaining pure forging billets. In the casting process, the risk of material failure caused by this has been controlled, and the purity of the material can be controlled to the level shown in Table 4. The high magnification image of inclusions is shown in Figure 5.
Table 4 Adjusted high magnification detection data after improvement
Note | Class A | Class B | Class C | Class D | Class Ds (Level) | ||||
H68M | Thick | Fine | Thick | Fine | Thick | Fine | Thick | Fine | |
≤0.5 | ≤0.5 | ≤1.0 | ≤1.0 | ≤0.5 | ≤0.5 | ≤1.0 | ≤1.0 | ≤1.0 |
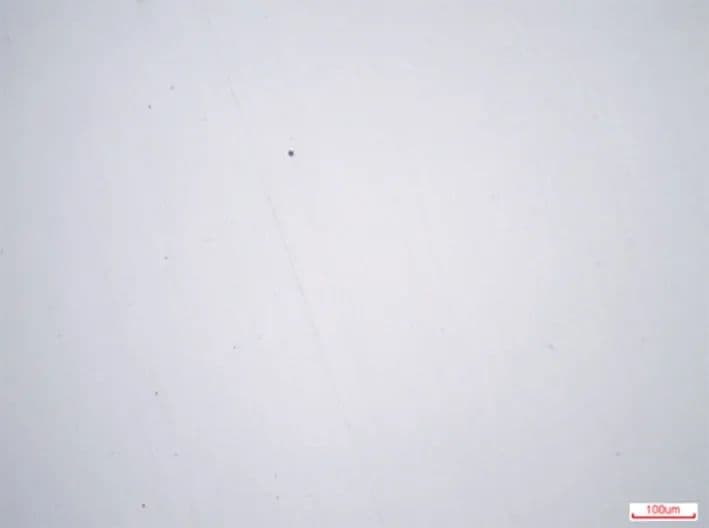
Improvement measure 3
During heating, high temperature diffusion of 1280℃ was employed. The forging process used three-drawing and three-sizing process control and cross grinding process with the amount of final deformation controlled to be greater than 30%.
The combination of multidirectional compression forging and EFS (Ultrafine Refining) process was used to obtain refined grains and uniform annealed microstructure.
This allowed a good heat treatment microstructure even after machining and conditioning, which provided a good basis for mold use. The fitted microstructure image is shown in Figure 6, and the grain size image is shown in Figure 7.

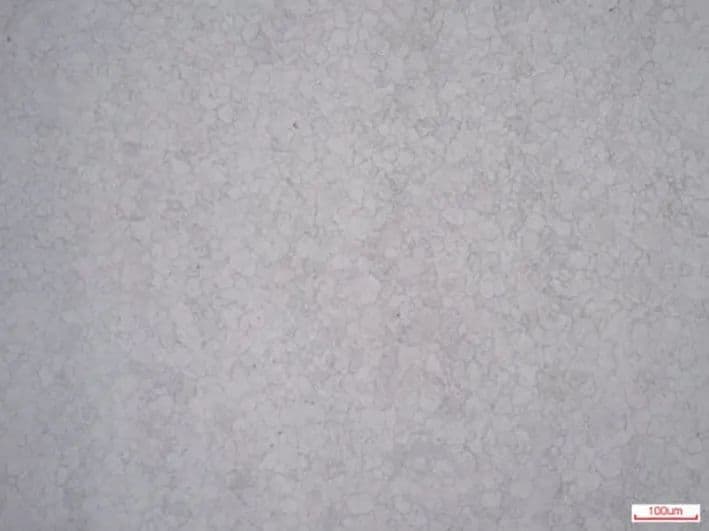
By implementing the above measures, our produced H68M material complies with the standards of the North American Die Casting Association.
The casting mold material should be tested for V-notch impact value to inspect the toughness of the material.
At the same time, the ductility of the material must be tested by testing its impact energy without notching. The H68M complies with the Dievar test requirements and obtains the impact value under hardened operating conditions to 44-46HRC as shown in Table 5.
Table 5 Impact value of H68M material hardened to 44-46HRC under operating conditions
Note | V-shaped (J) | No gap (J) | ||
average value | minimum value | average value | minimum value | |
1.2367 | ≥19 | ≥14.9 | ≥300 | ≥269 |
H68M | ≥25 | ≥18 | ≥350 | ≥300 |
Through the optimized design of the material's alloy composition and strict control of the processes of dosing, casting, electrical slag, forging and post-forging heat treatment during production, H68M material exhibits excellent performance in high hardenability, high red hardness, high toughness and high ductility.
Conclusion
(1) By adjusting the design of the chemical composition of H68M material, it has become a kind of hot work mold steel with high hardenability, high red hardness, high toughness and high ductility.
(2) H68M material has undergone electrical slag, high temperature homogenization, grain refinement treatment and three times of strong drawing and sizing process to exceed customer expectations. The lifetime of 10,000 molds required by customer contract orders can now be increased to more than 20,000, significantly reducing the cost of using molds and creating value for customers.