Quenching is the most crucial step in the heat treatment process and determines the internal quality and extent of distortion in the quenched components.
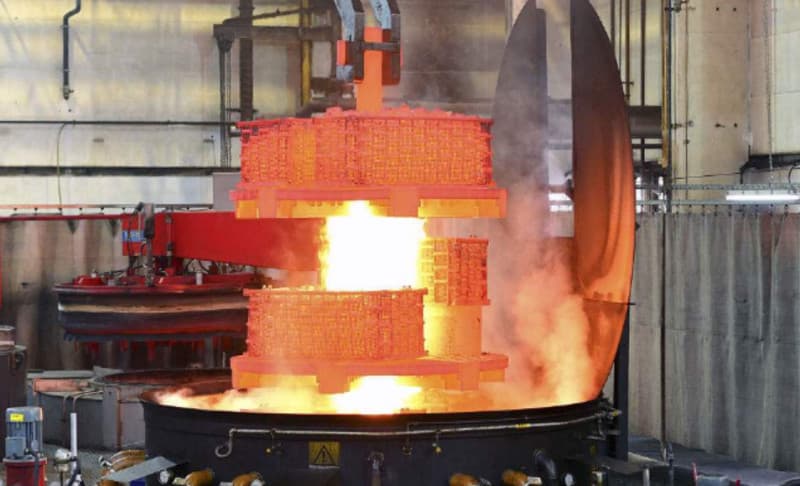
Quench cooling technology has seen continuous advancements with the advancement of heat treatment technology. However, despite this progress, the cooling process remains complex and challenging due to its instantaneous nature and observation and measurement limitations. As a result, cooling extinction remains a mystery.
For many years, the machinery industry has been guilty of “emphasizing cold and neglecting heat,” placing more emphasis on cold processing and neglecting the importance of hot processing. However, the heat treatment industry tends to “emphasize heat and neglect cold,” placing greater emphasis on heating and ignoring the crucial role of cooling. This is an unusual and problematic phenomenon.
With my extensive experience in heat treating, I would like to share my insights into understanding and selecting cooling media for quenching.
1. Basic properties of quenching cooling medium
(1) Optimal cooling rate
The term “optimal cooling rate” refers to the expected cooling rate at the nose of the C curve for a specific material and part that has been quenched. This rate must be higher than the critical cooling speed, which is the minimum speed necessary to ensure that the part is successfully subjected to martensitic transformation.
In other temperature ranges, especially during martensite transformation (Ms → Mf), cooling must be carried out more slowly. This is often referred to as the principle of “fast cooling at high temperatures and slow cooling at low temperatures”.
Each type of steel and part has its own unique requirements for “fast” and “slow” cooling. The concept of “ideal quenching cooling medium” exists theoretically, as illustrated in Fig.
It should be noted that the C curve for different types of steel may vary.
Unfortunately, it is not possible to find a single “ideal quenching cooling medium” that is suitable for quenching all types of steel and parts of different sizes.
Instead, the appropriate quench cooling medium must be selected based on specific conditions in order to obtain a hard quenched part with minimal distortion and good metallography.
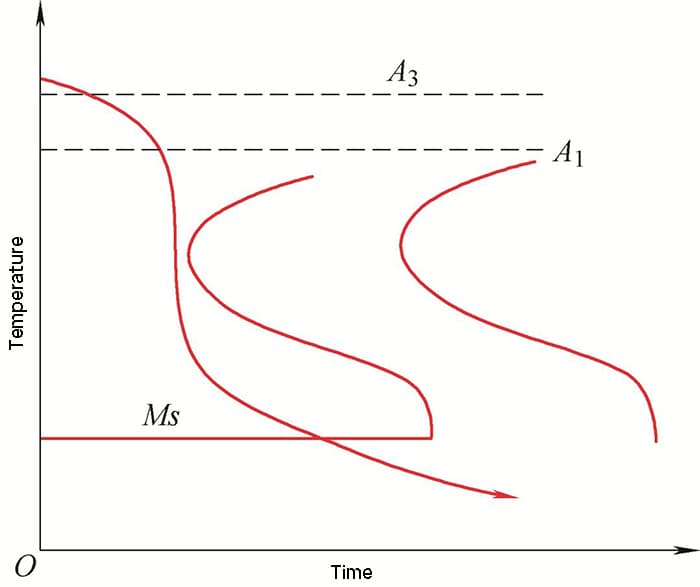
Fig. 1 Optimal Quench Cooling Media Curve
(2) Good stability
The quench cooling medium used must be stable and not subject to decomposition, deterioration or aging during use.
Different quenching oils and organic solvents have varying degrees of aging and it is important to adjust, refresh and maintain them regularly.
(3) Cooling uniformity
It is crucial to cool the different parts and surfaces of the part as evenly as possible to avoid the formation of weak spots and blocks during the quenching process.
(4) Non-corrosive
After quenching, it must be kept clean and easy to clean, and must not corrode the workpiece.
(5) Eco-friendly
During the quenching process, no significant amounts of smoke, toxic or irritating gases will be produced, and residual liquid from quenched parts will not result in environmental pollution.
(6) Security
The cooling medium used in the tempering process is neither flammable nor explosive, making it safe to use.
(7) Economy
The cooling medium used in quenching must not only be of high quality, but also reasonably priced. However, if it is too expensive, it may not be well received by heat treatment companies.
2. Factors affecting the cooling performance of quenching cooling medium
There are several factors that can impact the cooling performance of quench cooling medium, which can be categorized into nine types.
(1) Temperature
The cooling capacity of the quenching cooling medium changes as the temperature changes. The cooling capacity of water and water-based cooling media decreases as the temperature increases, while that of oil and salt baths increases.
As the temperature increases, the fluidity of the medium improves, promoting heat dissipation and increasing its cooling capacity. As a result, it is essential to understand the specific cooling temperature requirements of the part.
(2) Surface tension
Surface tension has a direct impact on the cooling rate. Typically, the low surface tension quench cooling medium is in close contact with the surface of the quenched parts, allowing rapid heat dissipation and better cooling capacity.
(3) Stir
Shaking the quenching cooling medium can increase its heat transfer coefficient, quickly break the vapor film, accelerate the cooling speed, and ensure that the quenched parts cool evenly.
(4) Thermal conductivity
Thermal conductivity, also known as thermal conductivity, is a physical property that represents the ability of a substance to conduct heat. The higher the thermal conductivity, the greater the cooling capacity of the material.
(5) Specific heat capacity
The higher the specific heat capacity of the quenching cooling medium, the faster the cooling speed.
(6) Viscosity
Viscosity represents the force of friction between liquid molecules within a liquid during its flow. Quench cooling media with high viscosity have low fluidity, making convective heat dissipation difficult and resulting in low cooling capacity. On the other hand, quench cooling media with low viscosity have a better cooling effect.
(7) Heat of vaporization
The term “heat of vaporization” refers to the amount of heat required to convert a unit mass of liquid to gas at constant temperature.
Water has high chemical stability and high thermal capacity, which is 8 times that of steel at room temperature.
Despite its low boiling point, the heat of vaporization of water decreases as the temperature increases.
As the temperature increases, the cooling capacity of the water decreases significantly.
However, once the water temperature reaches 80°C, its cooling capacity remains relatively stable and maintains a quenching intensity of approximately 0.72.
(8) Additive
The addition of additives is used to change refrigeration performance. If a small amount of salt or alkali is added to water, it can significantly increase its cooling capacity.
When polyvinyl alcohol is added, a thin plastic film forms on the surface of tempered parts, reducing the cooling speed due to its low thermal conductivity.
Adding oil and soap to water creates a suspension or emulsion that improves the formation of a vapor film, increases its stability, and decreases its cooling capacity.
Additionally, oxidizers, brighteners, rust inhibitors, and antiseptics are often added to modify other properties of the quench cooling medium, each having varying effects on cooling performance.
Overall, the addition of additives often serves multiple purposes.
(9) Environment
The impact of the environment on cooling capacity is often ignored. The cooling effect of a medium at the same temperature may vary between winter and summer, and the cooling effect may differ between day and night.
3. Basic principles for selecting quenching cooling medium
Numerous evidence shows that many heat treatment quality incidents are related to the choice of quench cooling medium. Improper media selection or operation can result in wasted hardened parts.
For this reason, proper use of quench cooling media is essential to ensure product quality. Regardless of the medium chosen, it is crucial to achieve uniform quenching effects:
- Achieve high, uniform surface hardness and adequate hardening depth.
- Avoid overheating or excessive extinguishing.
- Minimize extinction distortion.
The appropriate quenching cooling medium should be selected based on the technical requirements of heat treatment, material, shape and other specific conditions of the quenched parts. The following five basic principles must be considered:
(1) Importance of Carbon Content in Steel
Carbon is a crucial element in all types of steel. Carbon content has a significant impact on the properties and quenching effect of steel.
For low-carbon steel with a carbon content of less than 0.5% (mass fraction), quenching can be done with salt water, alkaline water, organic solvents, etc.
Medium and low alloy structural steels are typically quenched twice or cooled at a relatively slow rate using a medium.
Carbon tool steel, which requires high heat treatment and has poor hardenability, is generally quenched using an alkaline bath or nitrate bath, and oil quenching is rarely used.
(2) Hardenability of steel and quenching cooling medium
The hardenability of steel can be determined by the “C” curve. Steels with low hardenability require faster cooling, while steels with good hardenability require slower cooling.
It is crucial to choose an appropriate quenching cooling medium based on the hardenability of the steel.
(3) Effective diameter of the workpiece
Each type of steel has a critical diameter for quenching. When the surface of the quenched part cools to the point Ms, the cooling rate of the medium decreases significantly and the heat inside the part also decreases. Undercooled austenite within a certain depth on the part surface is difficult to cool below the Ms point.
For thicker parts, a faster cooling speed at low temperature should be selected to achieve sufficient quenching layer depth. On the other hand, for thin parts, a quench cooling medium with a low temperature and low cooling rate can be used. The distribution curve of the maximum allowable cooling speed indicates that thick parts can be cooled at high speed, while thin parts must be cooled at low speed.
(4) Complexity of tempered parts
Based on analysis of the distribution curve of the minimum allowable cooling rate, workpieces with complex shapes, particularly those with internal holes or deep concave surfaces, should be quenched with a cooling medium that has a short vapor film stage to reduce quenching distortion and the need for internal hole hardening.
For parts with relatively simple shapes, a quench cooling medium with a slightly longer vapor film stage can be used. The distribution curve of the maximum allowable cooling speed shows that the allowable cooling speed for parts with complex shapes is low, while it is high for parts with simple shapes.
(5) Allowable Deformation
Quenched parts must have minimal distortion and a narrow range of cooling speeds. When the allowable distortion is large, a wide range of cooling speed is acceptable. A medium that can generally achieve quenching hardness can be used for the allowable cooling speed range. The cooling speed range of the workpiece can be reduced through isothermal quenching or step quenching.
Due to the variety of workpieces and different heat treatment requirements, there are numerous quenching and cooling media options. Even the same type of part quenched with different media can result in the same surface hardness, making it difficult to select the correct quenching and cooling media. Based on the principles of economy and rationality, the most suitable quenching cooling medium is selected.
4. Application examples of quenching cooling medium
(1) Neutral salt quenching for high-speed steel quenching
The so-called neutral salt extinguisher generally refers to two formulations:
The first type: 50% BaCl 2 + 30% KCl + 20% NaCl (mass fraction), melting point 560 ℃, service temperature 580 ~ 620 ℃, suitable for effective diameter ≤ 20 mm, can guarantee the cooling speed within the temperature range of 1000 ~ 800 ℃ of the workpiece ≥ 7 ℃ / s, and prevent eutectic carbide precipitation from affecting tool performance.
The second type: 48% CaCl 2 + 31% BaCl 2 + 21% NaCl, melting point 435 ℃, service temperature 460 ~ 550 ℃.
2. For dosage convenience, the factory changed to 50% CaC12 + 30% bac12 + 20% NaC1, with melting point of 440°C and service temperature of 460-550°C.
Applicable to high-speed steel parts with an effective diameter of less than 40 mm.
The neutral salts of the two formulations are used differently.
It is recommended to use calcium-based salts when the oven is opened continuously for more than five days a week, as these salts have strong temperature absorption capacity and are easily deliquescent in air.
For small seasoned parts and infrequent oven openings, barium salt is an appropriate choice.
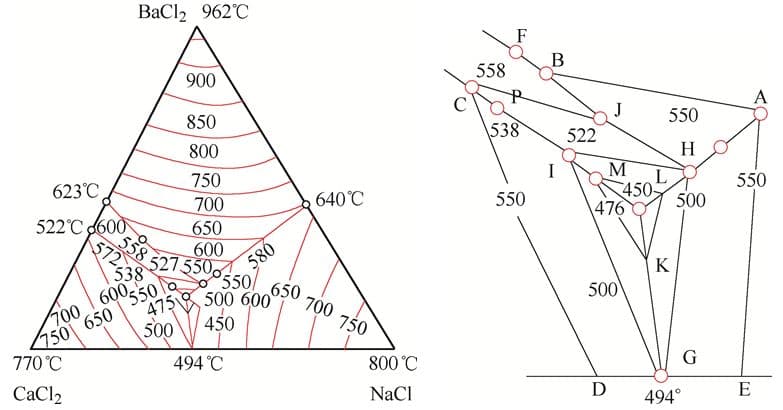
Fig. 2 Ternary phase diagram of CaCl 2 BaCl 2 and NaCl
(2) Quenching in a nitrate bath
Nitrate refers to the four salts of NaNO 3 NO 3 NaNO 2 and KNO 2 .
As a quenching agent, few individual components are used, and two or three mixed salts are commonly used.
The formula and melting point are shown in Fig.
The most commonly used formula is: 55% KNO 3 + 45NaNO 2 melting point 137 ℃, use temperature 160-550 ℃;
50% KNO 3 + 50% NaNO 2 melting point 140 ℃, service temperature 160-550 ℃.
This solution is used for quenching low-alloy steel products and for isothermal quenching of high-speed steel and high-alloy steel parts.
Some companies employ nitrate salt bath as quenching fluid after carburizing large gears, thus solving the challenge of heat treatment of large gears.
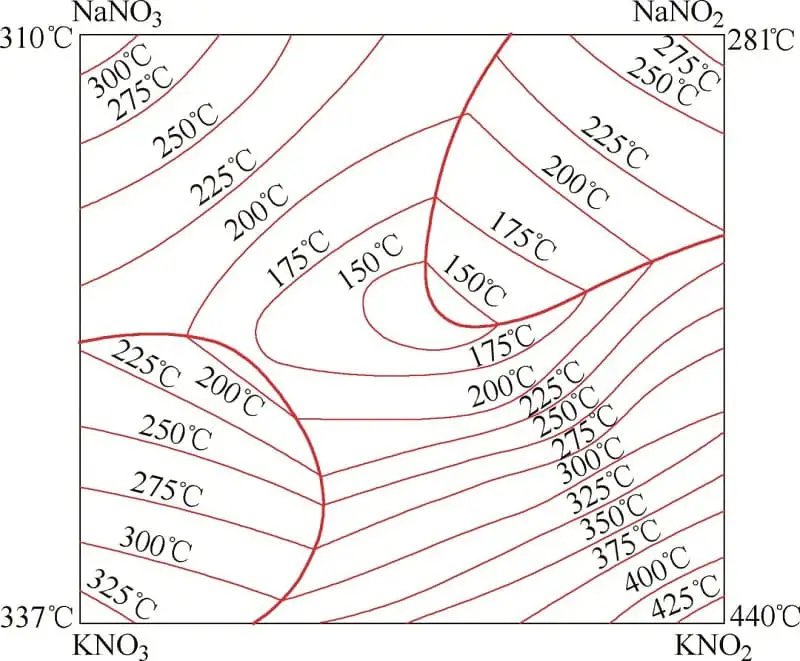
Fig. 3 Nitrate system melting curve
(3) Aqueous nitrate solution quenching
There are mainly two nitrate waters and three nitrate waters.
① Two-nitrate water is 25% NaNO 3 + 25% NaNO 2 + 50% water, and the service temperature is below 60 ℃.
The use of nitrate salt bath for isothermal quenching of 45 cores, dies and small steel parts not only solves the problem of crack quenching, but also ensures relatively uniform quenching hardness.
In industrial production, carbon tool steel molds with sharp corners, grooves and varying cross-section sizes are often found.
The desired hardness level is 59-63HRC, but water quenching can cause cracking and oil quenching is not hard enough, making it difficult to achieve the desired quality using either method alone.
Isothermal quenching in a nitrate salt bath solves this problem. During this process, the surface of the part will exhibit white nitrate bubbles, estimated at 1s/5mm in nitrate water, at a temperature of about 200°C.
The workpiece is then immediately placed in a nitrate bath at 180°C for isothermal quenching for 30-60 minutes, resulting in a workpiece with no cracks, minimal deformation and meeting the required hardness level.
(4) Quenching in boiling water
Some people have used boiling water quenching for 45 steel as an alternative to quenching and tempering, obtaining positive results.
For 45 steel with a diameter of 40mm to 80mm, heating the steel to 840°C and quenching it in boiling water results in a hardness of approximately 250HBW, which is highly uniform.
Quenching in boiling water can replace the normalization treatment of 45 steel as the final heat treatment step.
High speed steel can also be quenched in boiling water at 850-870°C instead of traditional quenching and tempering treatment.
Bearing steel undergoes a double refining treatment with quenching in boiling water.
Since the cooling rate of boiling water is slower than that of oil, there is no need to worry about cracking caused by the quenching of boiling water.
The process involves quenching the bearing steel in boiling water immediately after final forging, cooling the part to 500-400°C, and water cooling with air. Then annealing the part at 730-740°C for 3 to 4 hours and air cooling after furnace discharge results in ultrafine grains and fine carbides.
There are countless other applications of boiling water quenching, too many to list individually. When used correctly, it can conserve energy and increase efficiency.
(5) Bluish temper
This is a type of factory-prepared quench cooling medium and results in a visually attractive and corrosion-resistant part after quenching.
There are two formulations with different colors:
① 70% NaNO 3 + 20% KNO 3 + 10% NaNO 2 which results in a black piece after tempering.
② 70% NaNO 2 + 20% KNO 3 + 10% NaNO 3 which results in a blue piece after quenching.
The three nitrates are mixed evenly in the specified proportions and then an appropriate amount of water is added to create a supersaturated solution. The solution is then heated to 40-60°C for use.
(6) Water-soluble polymer quench – polyalkylene glycol (PAG)
PAG has a unique characteristic of reverse solubility, which means that its solubility in water decreases as the temperature increases.
The cooling rate can be controlled by adjusting the concentration, temperature and agitation of the solution.
PAG series refrigerants have a quenching capacity between water and oil, making them versatile for use in a wide range of applications.
Since its introduction in the United States in the 1960s, PAG has become a widely used solution in the heat treating industry and has successfully replaced alkaline water and oil for quenching and cooling carbon steel and low alloy steel.
(7) Quenching oil
Quenching oils have been categorized into several types, including common quenching oil, bright quenching oil, rapid quenching oil, quick and bright quenching oil, ultrafast quenching oil, vacuum quenching oil, graduated quenching oil, and quenching oil. isothermal quenching.
Although quenching oil has many benefits as a quenching cooling medium, its disadvantages are also significant. For example, it produces oil smoke that pollutes the environment and poses a risk to human health, is prone to aging and ignition, and disposal of used oil is a challenging issue.
In the tool and die industry, it is suggested to phase out the use of quenching oil and develop and adopt new means of quenching cooling that are energy-saving and environmentally friendly.
(8) gas extinguishing
Highly hardenable steels with small dimensions can be gas quenched.
The cooling capacity of the gas depends on the type, pressure and flow rate of the gas.
High-speed steel mechanical blades with a thickness of less than 20mm can be directly air-cooled after induction heating, resulting in high hardness above 63HRC.
Cr12 type high alloy steel can also be air quenched, and to improve the cooling speed, it can be cooled with a blowing method.
Models with an effective size greater than 50 mm can even be cooled on a water-cooled copper plate.
In recent years, there has been rapid growth in the development of high pressure vacuum gas quenching. Commonly used cooling gases include N 2 He, H 2 and Ar.
H2 has the best thermal conductivity, but it is highly flammable and can cause explosions when mixed with air, making it an unsafe option. It also causes decarburization of steel above 1000°C, limiting its application.
N 2 has a low cooling capacity, but is affordable and safe, which makes it widely used in gas quenching.
5. Conclusion
The choice and use of a quench cooling medium for heat treatment has a significant impact not only on product quality and economic benefits, but also on company survival and growth.
It is important to select the best quench cooling medium based on the material and performance requirements of the company's quench parts, to ensure successful hardening, minimize deformation and achieve the desired performance.