Many devices today strive for miniaturization and lightness, so there is often a demand for tighter integration between motors and gearboxes. Sometimes the motor is designed to be integrated into a gearbox shaft.
For example, the motor shaft directly serves as the high-speed shaft of the gearbox, connecting directly to the gear.
This design certainly reduces the size of the equipment and simplifies connections. If designed correctly, it can also increase reliability and reduce overall costs.
However, this integrated design presents new challenges to engine manufacturers in terms of design, manufacturing and installation. This article discusses the problems brought by gearmotors in the selection and arrangement of bearings.
For greater convenience in the discussion, we chose to talk about the helical gearmotor with a relatively complex load situation.
The following is a force diagram of a helical gear shaft system (the discussion below assumes that both sides are deep groove ball bearings; situations with other types of bearings require specific analysis following this thought process):
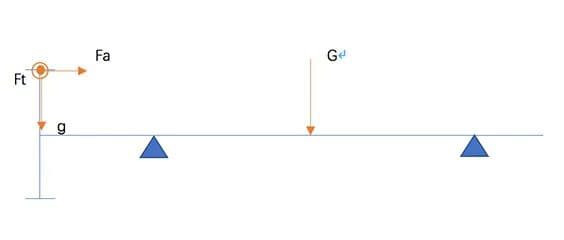
Axial Force Analysis
When designing motors, the tangential force of the rotor part is generally not included in the bearing load calculation. The main reason for this is that the tangential force of the motor rotor is always counterbalanced by an equal but oppositely directed force, so this load is not transmitted to the bearing.
However, the situation is different for transmissions with a gearbox. For example, in the figure above, the motor is directly connected to a helical gear. The gear transfers torque and supports unidirectional tangential force.
Without an opposing force to balance, this tangential force must be included in the bearing load calculation.
Therefore, in the figure above, the radial forces supported by the entire motor shaft system include:
- The weight of the engine rotor, G
- The weight of the gear, g
- The tangential force of the gear, Ft
Meanwhile, as the gear is helical, the motor will bear the axial force, Fa, of the helical gear. Therefore, when checking the service life of the shaft system bearings, all of the above loads must be taken into account.
How should we choose the positioning end and the non-positioning end?
Let's use the illustration above as an example. The image does not represent the markers for the positioning end and the non-positioning end of the axis system.
In previous articles, we discussed that a motor shaft system needs to have a positioning end and a non-positioning end. So, let's try to analyze the bearing arrangement of this helical gear shaft system.
Since the motor shaft is directly connected to the gear, the motor engineer must consider the gear engagement accuracy. If there is a problem with the gears meshing, the consequences could be serious.
In the example above, the most direct factor affecting gear engagement accuracy is the axial and radial runout of the shaft.
The radial runout of the bearing can be approximately guaranteed through the radial clearance of the bearing.
However, the axial deviation of the shaft requires consideration of the positioning relationship of the bearing system.
For example, if the positioning end is placed on the rear bearing as in the diagram, when the motor changes from a cold state to a stable working temperature, the rotor temperature will increase.
The resulting thermal expansion will be transmitted from the floating end of the shaft outward. This transmission directly reaches the gear at the end of the motor shaft. The axial movement of the gear will inevitably affect the meshing.
Therefore, from the perspective of gear engagement, the positioning end should be placed as close to the gear side as possible.
From a maintenance perspective, if the rear bearing is the floating end, the maintenance of the rear bearing and preload spring can be carried out independently without affecting the front bearing. On the other hand, if done another way, the same maintenance would require dismantling the entire engine.
However, placing the positioning edge closer to the gear side also has additional impacts.
Firstly, the size of the bearing. In this structure, there is an apparent difference in the distribution of radial force between the two bearings. The radial load supported by the left bearing is greater than that of the right bearing, so the size selection of the left bearing will be larger.
Secondly, we know that the positioning end of a motor bearing bears the axial force. If we define the left side as the positioning end bearing, the bearing size will further increase under the condition of bearing axial force.
In reality, the design of a single motor shaft system requires consideration of evenly distributing the load carried by the two bearings as much as possible.
However, in this application, due to the special requirements of the front gear, the engine engineer needs to make a compromise.
The above text discusses only one aspect of the gear motor bearing arrangement. In practice, such a design will bring other challenges, such as:
- Bearing sealing problems;
- Bearing lubrication problems;
- If the gear supports a large load, the selection of bearing type must be considered.
When using tapered roller bearings, additional knowledge in the area of gearbox bearing application technology, such as adjusting the bearing preload, is required.
This presents yet another significant challenge for engine engineers. Engine engineers are advised not to blindly “copy” previous engine structures when designing such engine shaft systems to avoid unnecessary losses.