Sensors are a basic type of electronic information equipment in the manufacturing industry and are special components of new electronic devices being developed.
The sensor industry is recognized both nationally and internationally as a high-tech industry with great development prospects, due to its high technical content, good economic benefits, strong penetration capacity and broad market prospects.
Driven by the growing electronic information industry, the sensor industry has formed a certain industrial base and made significant progress in technological innovation, independent research and development, achievement transformation and competitiveness, making important contributions to the promotion of national economic development.
With the advent of the information age, sensors have become the main means and method for people to obtain information in the natural and productive fields.
In modern industrial production, especially in automated production processes, various sensors are used to monitor and control various parameters of the production process, ensuring that the equipment operates in a normal or ideal state and produces high quality products. In fundamental research, sensors have an exceptional status.
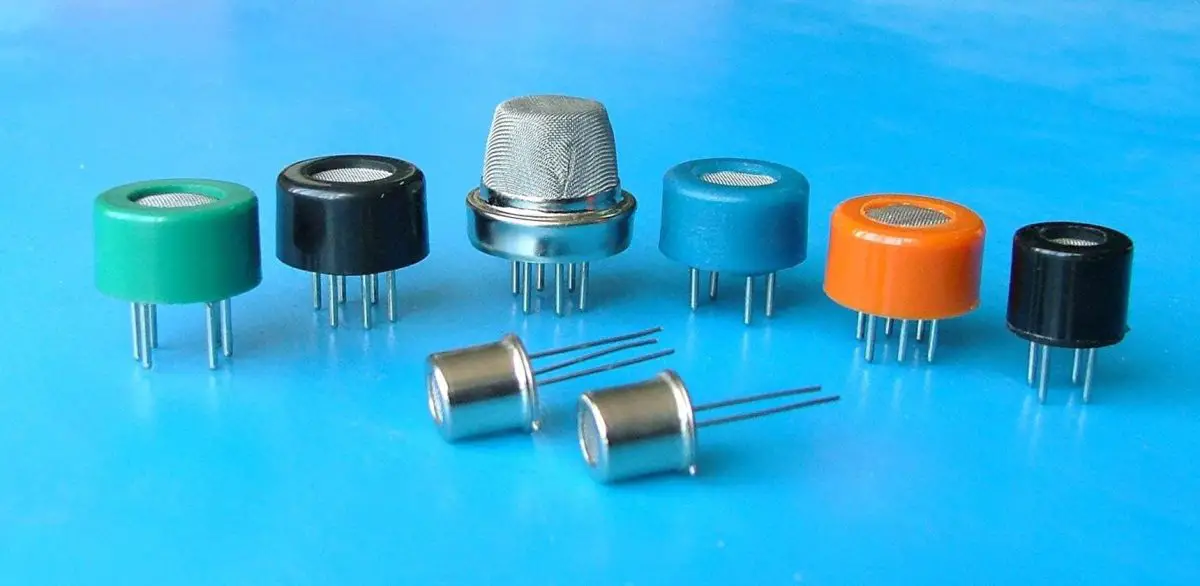
Nowadays, sensors have penetrated extremely wide areas such as industrial production, space development, ocean detection, environmental protection, resource investigation, medical diagnosis, bioengineering and even protection of cultural relics.
It can be seen that the important role of sensor technology in developing the economy and promoting social progress is very obvious. Statistical figures show that the annual revenue of the global smart sensor market will increase at a rate of 10% per year.
Currently, the number of sensor devices installed with processors around the world is 65 million, and this number will reach 2.8 trillion by 2019.
Sensor Selection Key Points
Sensor knowledge is also a relatively large electrical discipline that requires a lot of experience to master proficiently. We will explain more about this in the future, but today we will mainly talk about selection.
1. Determine the type according to the measured object and output conditions
To carry out a specific measurement task, you first need to consider what type of sensor principle to use. This requires careful analysis of several factors to make a determination.
For example, taking a flow meter as an example, there are an electromagnetic flow meter, a vortex flow meter and an ultrasonic flow meter, which depend on the specific target when selecting a flow meter.
In addition, it is also necessary to consult what kind of output mode needs to be used, such as a 2-wire or 4-wire current signal, a voltage signal of 0-20mA, 4-20mA, 0-10V, or some protocol communication .
2. Sensitivity-Based Selection
Generally, within the linear range of the sensor, it is desirable to have a higher sensor sensitivity. This is because only when the sensitivity is high enough, the output signal value corresponding to the measured change is relatively large.
Furthermore, this sensitivity is advantageous for signal processing. However, it is important to note that when the sensitivity of the sensor is high, external interference signals unrelated to the measured object may be amplified by the amplification system and affect the measurement accuracy.
Therefore, the sensor itself must have a higher signal-to-noise ratio and interference signals introduced from outside must be reduced as much as possible.
The sensitivity of the sensor is directional. When the measured object is a single vector and requires high directionality, another sensor with lower sensitivity in other directions should be selected. If the measured object is a multidimensional vector, the cross sensitivity of the sensor should be as low as possible.
3. Determine the frequency response characteristics
The frequency response characteristics of the sensors determine the frequency range of the measured object, which must be maintained without distortion within the permissible frequency range.
In practice, there is always a certain delay in the sensor's response, and it is preferable for the delay time to be as short as possible. The greater the frequency response of the sensor, the greater the frequency range of the signal that can be measured.
In dynamic measurement, response characteristics must be based on signal characteristics (steady state, transient, random, etc.) to avoid significant errors.
4. According to sensor stability
After using the sensor for a certain period of time, the ability of the sensor to maintain its performance is called stability. The factors that affect the long-term stability of the sensor are not only related to the sensor structure, but also mainly related to the sensor's usage environment.
Therefore, to ensure that the sensor has good stability, the sensor must have strong environmental adaptability.
Before selecting a sensor, the usage environment must be investigated and appropriate sensors must be selected based on the specific usage environment or appropriate measures taken to reduce the impact of the environment.
5. Sensor range and accuracy are the most difficult pair to coordinate
Accuracy is an important performance indicator of sensors and is an important link related to the measurement accuracy of the entire measurement system. However, the sensor's accuracy is limited by its range.
Generally, the greater the range, the lower the accuracy, but it is very likely that high-precision sensors will have insufficient range. This makes long-range, high-precision sensors very expensive.
Therefore, adjustments need to be made when selecting sensors according to these considerations.
When selecting a sampling sensor, it is necessary to ensure that the device meets the basic operating conditions of the application (you can consult the technical data sheet provided by the manufacturer).
The 6 most important operating conditions include:
- Temperature range;
- Specification;
- Level of protection;
- Voltage range;
- Discrete or analog output;
- Parameter changes, i.e. “whether changeable parameters are beneficial”.
When considering using sensors with IO-Link, there are also 6 other things to consider:
- Response speed;
- Detection range;
- Repetition accuracy;
- Electrical connection;
- Type of installation;
- Visual display: if there is a need for a visible display on the sensor for the application.
In modern industrial production, especially in automated production processes, various sensors are used to monitor and control various parameters of the production process, so that the equipment operates in a normal or ideal state and the products achieve the best quality.
Therefore, it can be said that without many excellent sensors, modern production will lose its foundations. Below, we will provide a detailed introduction to several of the most common types of sensors in manufacturing, along with some application techniques and insights.
The most common types of sensors
1. Proximity sensors
Proximity sensors detect the presence of objects nearby without physical contact. They are discrete output devices.
Typically, magnetic proximity sensors detect whether an actuator has reached a specific position by detecting a magnet located on the actuator.
It is generally not a good idea to buy an actuator from one company and a magnetic proximity sensor from another. While the sensor manufacturer may claim that the sensor is compatible with X, Y, and Z actuators, the reality is that changes to the magnets or mounting position can cause sensing issues.
For example, the sensor may energize or not energize when the magnet is not in the correct position. If the actuator manufacturer offers proximity sensors compatible with the actuator, these should be the preferred sensors.
Transistor-based proximity sensors have no moving parts and have a long service life. Spring-loaded proximity sensors use mechanical contacts, have a shorter lifespan, but are cheaper than transistor types. Spring-loaded sensors are best suited for applications that require AC power and those that operate in high-temperature environments.
2. Position sensors
Position sensors have analog output and display the position of the actuator based on the position indicator of the magnet mounted on it. From a control perspective, position sensors offer a lot of flexibility. Control engineers can establish a series of set point values corresponding to component changes.
Since these position sensors are based on magnets (like proximity sensors), it is best to purchase sensors and actuators from the same manufacturer (if possible). With the IO-Link functionality, data can be obtained from position sensors, which can also simplify control and enable parameterization.
3. Inductive Sensors
Inductive proximity sensors use Faraday's Law of Induction to measure the presence or position of an object. The most critical factor when selecting an inductive sensor is determining the type of metal the sensor will detect, thus determining the detection range.
Compared to black metals, the detection range of colored metals is reduced by more than 50%. The manufacturer's product manual should provide information on selecting the required sample.
4. Pressure and vacuum sensors
Make sure pressure or vacuum sensors can measure the pressure range in both imperial (pounds per square inch) and metric (bar) measurements. Specify the most appropriate shape and size for the allocated space.
When installing equipment, consider whether the sensor should be configured with indicator lights or a display for operator ease of use. If quick changes to set values are required, pressure and vacuum sensors with IO-Link configuration can be considered.
5. Flow sensors
Just like pressure and vacuum sensors, flow sensors can be selected based on flow range, size and variable set values. Display options can be specified when ordering sensors.
Flow sensors with relatively low flow rates can be selected for a specific area of the equipment or for the entire equipment.
6. Optical sensors
The most common types of optical sensors are photoelectric scattering, reflection, and direct beam. Laser sensors and fiber optic sensing devices also fall into the optical sensor category.
Photoelectric sensors are mainly presence sensors that detect objects by reflecting or interrupting a beam of light. Due to their low cost, versatility and high reliability, these sensors are among the most used in the manufacturing industry.
Diffuse photoelectric sensors do not require reflectors. They are cost-effective sensors used to detect the presence of nearby objects.
Direct beam photoelectric sensors can provide the greatest detection range. These sensors have separate transmitting and receiving units installed at two points. Garage door safety sensors are beam sensors. Disruption of the beam indicates the presence of a target.
Slot-type photoelectric sensors are an interesting direct beam variant; they combine a transmitter and receiver in one compact unit. Slot-type sensors are used to detect the presence and absence of small parts.
Reflective photoelectric sensors have a sensor and a reflector and are used for mid-range presence detection. In terms of accuracy and cost, these sensors fall between diffuse and direct beam sensors.
Fiber optic sensing devices are used for presence and distance sensing. The parameters of these multifunctional sensors can be adjusted to detect various colors, backgrounds and distance ranges.
Laser sensors can be used for long-range presence detection and are the most accurate for short-range measurement applications.
Vision sensors can be used for barcode scanning, counting, format checking, and more. Vision sensors are a cost-effective and efficient visual application that can be used in situations where camera systems are expensive and complex.
Vision sensors are used for reading barcodes, tracking individual components, and performing custom process steps for the component. Sensors can check the functionality of the number of parts present in the component. Vision sensors can determine whether a specific curve or other shape has been achieved.
Because these sensors deal with light, it is crucial to test the sensors in conditions as close as possible to the operating environment, taking into account ambient light and background reflectivity.
In most applications, it is recommended to place vision sensors inside a box to isolate them from external light sources. Seeking help from the vision sensor manufacturer when testing the sensor is a good idea. Also, remember to ensure that you select the appropriate fieldbus.
Signal converters convert the analog output signal from a sensor into a binary signal in the converter or convert it into IO-Link process data.
7. Other sensors
(1) Magnetic switch:
It is a specialized name for sensors used in cylinders, mainly used to detect the position of cylinder pistons. It is normally provided by the cylinder supplier according to the customer's use. As the name suggests, the magnetic key detects the target object through electromagnetic induction, so its detection accuracy is relatively low.
(2) Proximity switch:
The proximity switch is also designed and manufactured based on the principle of electromagnetic induction, so it can only measure metal target objects, and there is a slight difference in detection distance for different metals.
At present, the commonly used sensing distances for proximity switches are as follows: 1mm, 2mm, 4mm, 8mm, 12mm, etc. There are generally two types of proximity switches: embedded and non-embedded.
The so-called embedded type refers to the fact that the proximity switch detection head does not detect the metal target in its circumferential direction, only detects the metal target in front of it, and the sensor detection head can be installed without exposing the metal mounting brackets.
The so-called non-embedded type means that the sensing head of the proximity switch will detect both the metal target in front of it and the metal target in its circumferential direction at the same time, and the sensing head of the sensor must expose the metal mount support for a certain distance, and there should be no metal targets within a certain range in the circumferential direction to avoid incorrect judgments.
The detection accuracy of proximity switches is higher than that of magnetic switches. Proximity switches are generally used in situations where position accuracy requirements for assessing the presence or absence of products and the positioning of fixtures are relatively low.
(3) Photoelectric switch:
The photoelectric detection method has the advantages of high precision, fast response and non-contact, and can measure various parameters. The sensor structure is simple and flexible, so photoelectric sensors are widely used in detection and control.
There are approximately three types of photoelectric switches that we usually mention: one is a reflective photoelectric sensor, another is a direct beam photoelectric sensor, and the other is a photoelectric sensor that uses a reflective plate to reflect light.
The latter two are detected by shading due to the target object, while the first is achieved by reflecting light through the target object.
Therefore, the latter two generally have longer detection distances and greater accuracy. Due to the relatively high detection accuracy of photoelectric sensors, they are generally used in detecting the precise position of products or workpieces, as well as feedback devices for stepper and servo systems.
(4) Optical fiber sensor:
Optical fiber sensor is also a type of sensing element that uses photoelectric signal conversion. Compared with photoelectric switches, it can generally detect smaller target objects, have a longer detection distance and higher accuracy.
Therefore, fiber optic sensors are generally used in more precise sensing applications and positioning feedback devices for stepper and servo systems.
(5) Grid:
The grid is also a sensor that uses photoelectric signals. The sensing area of the grid is large, so it is also called an area sensor. The main area of application of the network is the interlocking and security functions between equipment, mainly for the protection of people.
(6) Thermocouple:
Thermocouples are mainly used to detect the ambient temperature around you.
(7) Laser Detector:
The main function of the laser detector is to accurately measure the external dimensions of the target object.
(8) Industrial camera:
Industrial camera is also commonly known as CCD (Charge Coupled Device) in engineering, mainly used to detect the external shape and position of the target object. With the improvement of current CCD technology, high-resolution industrial cameras can now be applied in precise measurement fields.
(9) Encoder:
According to the working principles, encoders can be divided into incremental and absolute types. Incremental encoders convert the displacement into periodic electrical signals and then convert that electrical signal into counting pulses, where the number of pulses represents the size of the displacement.
The absolute encoder corresponds to a specific digital code for each position, therefore its indication is only related to the initial and final positions of the measurement, and is not related to the intermediate measurement process.
Encoders are generally used in closed or semi-closed loop control systems with stepper motors or servo motors.
(10) Microswitch:
The microswitch is a contact-type sensor, mainly used for connecting equipment or detecting the status of security doors and equipment protection.
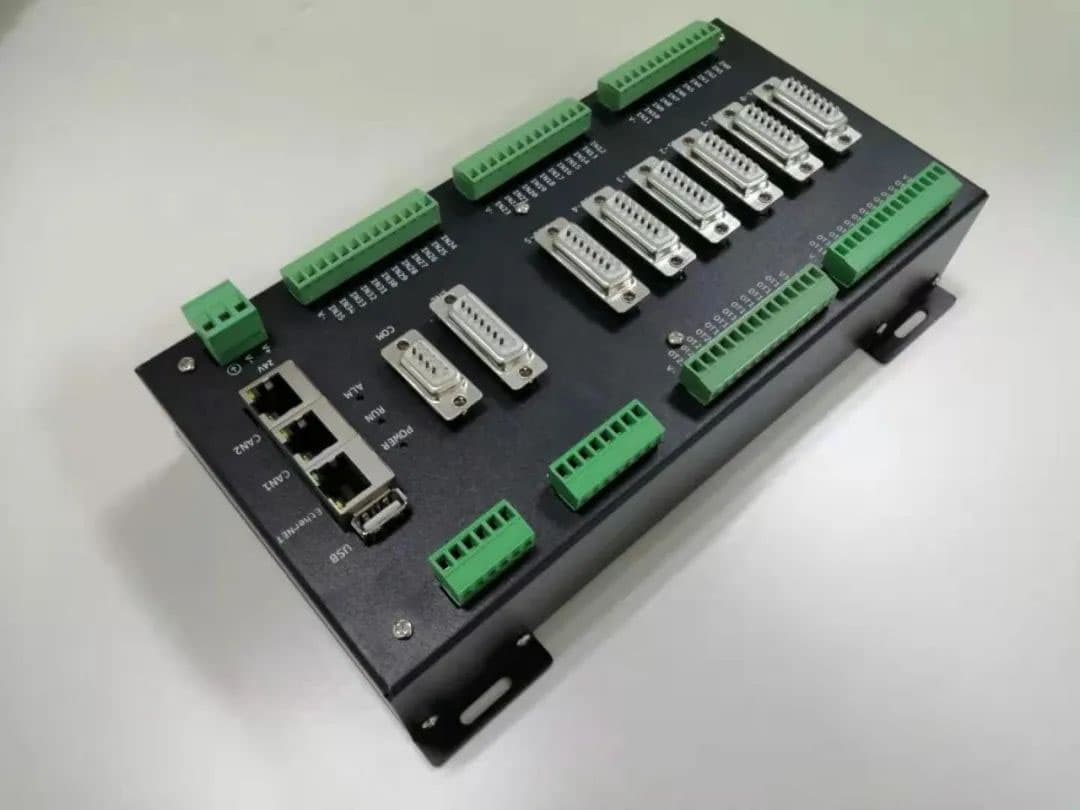