Regarding the alloying elements such as Si, Mn, S, P, Cr, AI, Ti, Mo and V contained in the welding wire, what is the impact of these alloying elements on the welding performance? The following are explanations for each element:
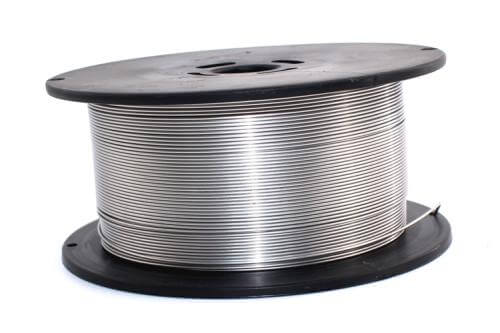
Silicon (S i )
Silicon is the most commonly used deoxidizing element in welding wires. It can prevent iron from combining with oxygen and can reduce FeO in the molten pool.
However, when silicon is used alone for deoxidation, the resulting SiO2 has a high melting point (approximately 1710℃) and the particles produced are small and difficult to float out of the weld pool. This can lead to slag entrapment in the weld metal.
Manganese (Mn)
The function of manganese is similar to that of silicon, but its deoxidation ability is slightly lower than that of silicon. When manganese is used alone for deoxidation, the resulting MnO has a higher density (15.11g/cm 3 ) and is also difficult to float out of the weld pool.
In addition to its deoxidizing function, manganese in welding wire can also combine with sulfur to form manganese sulfide (MnS), which can be removed (desulfurized), thereby reducing the tendency of hot cracking caused by sulfur.
Because it is difficult to remove deoxidation products when silicon or manganese are used alone for deoxidation, a combination of silicon and manganese is commonly used to form a silicate composite (MnO·SiO 2 ) during deoxidation.
MnO·SiO 2 has a lower melting point (approximately 1270°C) and a lower density (approximately 3.6g/cm 3 ). It can coagulate into large slag blocks and float out of the molten pool, achieving good deoxidation effect.
Manganese is also an important alloying element in steel and an important hardenability element. It has a significant impact on the toughness of the weld metal.
When the Mn content is less than 0.05%, the weld metal has high toughness. When the Mn content is greater than 3%, the weld metal becomes brittle. When the Mn content is between 0.6% and 1.8%, the weld metal has high strength and toughness.
Sulfur (S)
Sulfur in steel is often present in the form of iron sulfide, which is distributed in a mesh pattern along grain boundaries and significantly reduces the toughness of the steel. The eutectic temperature of iron and iron sulfide is relatively low (985°C).
Therefore, during hot working, since the initial working temperature is generally between 1150-1200 ℃, the iron eutectic and iron sulfide have already melted, causing cracking during the working process.
This phenomenon is known as “sulfur heat brittleness”. The property of sulfur makes steel prone to hot cracking during welding.
Therefore, the sulfur content in steel is strictly controlled. The main difference between ordinary carbon steel, high-quality carbon steel and advanced high-quality steel is the amount of sulfur and phosphorus.
As mentioned previously, manganese has a desulfurizing effect because it can form high-melting point (1600℃) manganese sulfide (MnS) with sulfur, which is distributed in granular form within the grains.
During hot working, manganese sulfide has sufficient plasticity to eliminate the harmful effects of sulfur. Therefore, it is beneficial to maintain a certain amount of manganese content in steel.
Phosphorus (P)
Phosphorus can be completely dissolved in ferrite in steel. Its strengthening effect on steel is second only to carbon and increases the strength and hardness of the steel.
Phosphorus can also improve the corrosion resistance of steel, but it significantly decreases its ductility and toughness. This effect is particularly severe at low temperatures, known as the “phosphorus cold brittle” phenomenon.
Therefore, it is harmful to welding and increases the steel's susceptibility to cracking. As an impurity, the phosphorus content in steel must also be restricted.
Chromium (Cr)
Chromium can increase the strength and hardness of steel, while decreasing its ductility and toughness to a lesser extent. Chromium has strong corrosion and acid resistance ability, so austenitic stainless steels generally contain more than 13% chromium.
Chromium also has strong antioxidant and heat-resistant properties. Therefore, chromium is also widely used in heat-resistant steels such as 12CrMo, 15CrMo and 5CrMo. Chromium is present in steel in certain quantities.
Chromium is an important component of austenitic steel and a component of ferrite. It can improve the oxidation resistance and mechanical properties of alloy steel at high temperatures. In austenitic stainless steel, when the total amount of chromium and nickel is 40% and the Cr/Ni ratio is 1, there is a tendency to hot cracking.
However, when the Cr/Ni ratio is 2.7, there is no tendency to hot cracking.
Therefore, in general, when the Cr/Ni ratio is around 2.2-2.3 in 18-8 type steel, chromium can easily form carbides in steel alloys, reduce thermal conductivity, and cause welding difficulties due to to the formation of chromium oxide.
Aluminum (IA)
Aluminum is one of the strong deoxidizing elements. Therefore, the use of aluminum as a deoxidizer can not only reduce the production of FeO, but also facilitate the reduction of FeO, effectively suppressing the chemical reaction of CO gas produced in the molten pool and improving the ability to resist CO porosity.
In addition, aluminum can also combine with nitrogen to form a nitrogen fixation effect, reducing nitrogen porosity.
However, the use of aluminum for deoxidation results in the formation of high melting point AI 2 Ó 3 (approximately 2050 ℃), which exists in a solid state in the weld pool and is easy to cause slag entrapment in the weld metal.
At the same time, aluminum-containing welding wire is prone to spatter, and excessive aluminum content can reduce the resistance of the weld metal to hot cracking.
Therefore, the aluminum content in the welding wire must be strictly controlled and must not be too high. If the aluminum content in the welding wire is properly controlled, the hardness, yield point and tensile strength of the weld metal will be slightly improved.
Titanium (TI)
Titanium is also a strong deoxidizing element and can also combine with nitrogen to form TiN, playing a role in nitrogen fixation and improving the ability of weld metal to resist nitrogen porosity.
If appropriate amounts of titanium and boron (B) are present in the weld metal structure, the weld metal structure can be refined.
Molybdenum (Mo)
Molybdenum can increase the strength and hardness of alloy steel, refine grain size, prevent quench brittleness and overheating tendency, and improve high temperature resistance, creep resistance and durability.
When the molybdenum content is less than 0.6%, it can improve ductility, reduce the tendency to crack and increase impact resistance. Molybdenum also has a tendency to promote graphitization.
Therefore, the molybdenum content in heat-resistant steels such as 16Mo, 12CrMo, 15CrMo, etc. is generally around 0.5%.
When the molybdenum content in alloy steel is between 0.6% and 1.0%, molybdenum can reduce the plasticity and toughness of alloy steel and increase its tempering tendency.
Vanadium (V)
Vanadium can increase the strength of steel, refine grain size, reduce grain growth tendency and improve hardenability.
Vanadium is a relatively strong carbide-forming element and the carbides it forms are stable below 650°C.
It also has age hardening effects. Vanadium carbides have high temperature stability and can improve the hardness of steel at high temperatures. Vanadium can also alter the distribution of carbides in steel, but it is prone to forming refractory oxides, making welding and cutting difficult.
Generally, when the vanadium content in the weld metal is around 0.11%, it can play a role in nitrogen fixation, turning an unfavorable situation into a favorable one.