1. Background
The air duct system is a crucial component in air conditioning and ventilation engineering. Its purpose is to efficiently transport the adjusted air to the final equipment based on the designed flow.
Typically, air ducts have three cross-sectional shapes: rectangular, circular and oblong. Rectangular ducts are generally produced by riveting four steel plates, while round ducts are created by rolling a 137mm wide steel plate on a spiral forming machine. Oblong ducts are relatively uncommon and are typically formed by compression of circular ducts.
Before 1960, rectangular ducts were most commonly used due to their simple manufacturing process and small installation space requirements. However, with the development of large circular spiral duct forming machines, many engineering projects have demonstrated that circular ducts are more economical and perform better in other engineering parameters compared to rectangular ducts.
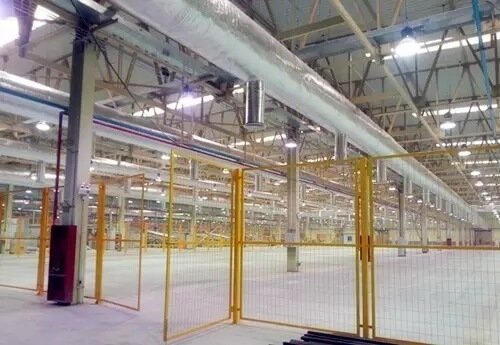
Many fiber fabric air ducts currently available on the market are air distribution systems that combine features such as air vents, air supply ducts, static pressure boxes, thermal insulation materials and shock absorbers. They have gained popularity among users due to their advantages such as precise and uniform air supply, lightweight installation block, attractive appearance, and resistance to bacteria and mold.
Fiber fabric ducts come in various shapes including round, semi-circular, quarter-circle, oval and semi-oval to accommodate the requirements of different building structures.
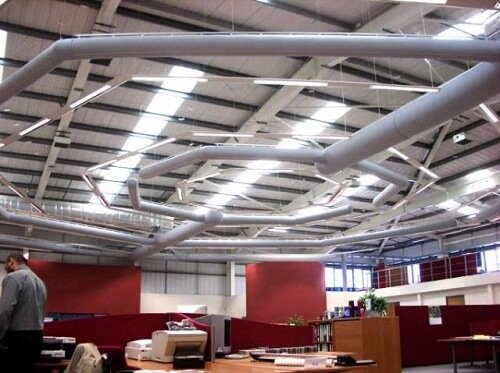
Round Fiber Fabric Duct
Table 1: The market share of circular ducts in each year:
Country | 1960 | 1965 | 1970 | 1975 | 1980 | 1985 | nineteen ninety | 2000 |
Nordic | 5 | 15 | 40 | 60 | 70 | 80 | 85 | 90 |
Germany | 5 | 5 | 10 | 15 | 20 | 25 | 25 | 50 |
France | 5 | 10 | 20 | 30 | 40 | 50 | 50 | 65 |
England | 5 | 10 | 15 | 20 | 25 | 35 | 35 | 55 |
From the point of view of economic analysis, the total cost of an air duct system in a building over its useful life can be divided into:
- Initial investment: Includes design costs, material and installation costs, space costs, commissioning costs, etc.
- Operating costs: Includes staff salaries, energy costs and maintenance costs.
- Renewal cost: Includes the cost of repairing and replacing worn parts.
Foreign research has shown that in many parameters circular duct systems outperform rectangular duct systems.
This article will summarize the findings of these studies and focus on comparing the economics of air duct systems.
It should be noted that under normal circumstances, the cost of renovation constitutes a small portion of the total cost and will therefore not be considered in this discussion.
2. Initial investment
The reasons why the initial investment required for a circular duct system is lower than that for a rectangular duct system are the following:
- Round ducts are easier to manufacture and transport.
- The components and accessories of circular ducts have been highly standardized.
- Circular ducts are structurally better able to withstand pressure without deformation, while rectangular ducts require screws, rivets, support beams and other additional strengthening measures.
- For the same hydraulic diameter, a circular duct requires less metal than a rectangular duct. The greater the aspect ratio of the rectangular duct, the greater the metal consumption.
- The suspended structure of circular ducts is easier to install compared to rectangular ducts. According to GB50243-2002 “Code for Construction and Acceptance of Ventilation and Air Conditioning Works”, the distance between supports for rectangular ducts with long sides greater than 400mm is 4m, while the distance between supports for spiral ducts is increased to 5m .
- The measuring point for measuring the air volume of a circular duct is smaller than that of a rectangular duct, so when the duct system is balanced, the commissioning cost will also be lower than that of a rectangular duct.
- Circular ducts can significantly reduce the introduction of low-frequency noise into the room, thereby reducing the need for noise reduction equipment.
We designed two ventilation system schemes for a large room using circular and rectangular ducts and compared the system pressure loss and related economic parameters. The results, based on Nordic market prices for the year, are presented in Figure 1.
Calculations showed that, under the same final equipment conditions, the overall installation cost of the circular duct system was only half that of the rectangular duct system, and the material cost of the circular duct system was 80% of that of the of rectangular ducts. system.
![]() |
![]() |
Total pressure loss (Pa): 150.0
Total installation cost: 0.51R Total material cost: 0.8 million (A) |
Total pressure loss (Pa): 165.4
Total installation cost: R Total material cost: M (B) |
Figure 1: Comparison of pipeline design schemes
(A) Circular duct (B) Rectangular duct
The economic analysis of the space occupied by the duct system is challenging due to its dependence on the structure and purpose of the building.
It is generally believed that rectangular ducts save space, but in reality, for rectangular ducts with close aspect ratio, the actual area they occupy is larger than that of circular ducts. This is mainly because rectangular ducts require flanges for connection, and the height of the flange edges is typically greater than 20 mm, as shown in Figure 2 (A).
However, modern spiral air ducts can be connected with standardized flexibility as shown in Figure 2 (B), which not only saves space but is also easier to install. Therefore, for rectangular air ducts with an aspect ratio close to 1, the advantages of circular ducts cannot be neglected.
![]() |
![]()
|
(A) | (B) |
Figure 2: Duct Connection Schematic Comparison
(A) Rectangular duct (B) Circular duct
For rectangular ducts with large proportions, they can be replaced by several circular ducts, as shown in Figure 3. This alternative can greatly facilitate air volume control and also reduce installation costs. Although the cost of materials may increase, research has shown that in this scheme the initial investment is almost the same as that of the rectangular duct.
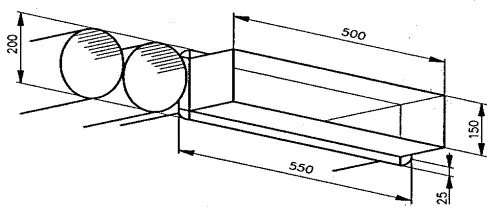
Figure 3: An alternative plan for the 550 mm × 150 mm rectangular duct to be replaced by two D = 200 mm circular ducts
3. Operating Costs
Under normal circumstances, the largest part of the operating costs of air conditioning systems is energy consumption. This includes the energy needed to heat or cool the air and also to transport the air to the final equipment. If the entire duct system is well insulated, the amount of air leakage from the ducts becomes a significant source of excessive energy consumption.
For the duct system, the fan provides circulating power, and the fan wind pressure normally does not exceed 650Pa. Excluding pressure loss in the air handling unit end equipment, the available pressure of the entire duct system is about 200-300Pa.
Therefore, it is crucial to minimize pressure loss in the air duct system. At the same time, the level of air leakage also directly affects the fan power selection. According to the fan theorem, fan power is proportional to the cube of air volume. That is, if the air duct leakage rate is 6%, the fan power will increase by 20%. The leakage rate of circular air ducts is much lower compared to rectangular air ducts.
3.1 Air Leakage Rate
The air duct leakage rate can be calculated by the following formula:
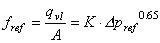
- f reference = area leakage rate
- q vl = air leak
- A = surface area of the duct
- K = air leak constant
- △p reference = pressure difference between the duct and the outside
In Europe, the tightness of air ducts is divided into four levels (A, B, C, D) according to the air leakage constant.
Table 2 Shows the maximum air leakage constants allowed for the respective grades.
Class A | KA = | 0.027×10 -3 i 3 is -1 i -2 Dad -0.65 |
Class B | KB = | 0.009×10 -3 i 3 is -1 i -2 Dad -0.65 |
Class C | KC = | 0.003×10 -3 i 3 is -1 i -2 Dad -0.65 |
Class D | KD = | 0.001×10 -3 i 3 is -1 i -2 Father -0.65 |
Table 2: Air tightness rating for European duct systems
Comparison with circular ducts shows that rectangular ducts require significantly more screws and rivets for connection, leading to much greater air leakage.
Figure 4 presents measured data from Belgium, which shows that the average leak rate from rectangular ducts is seven times higher than that from circular ducts.
The “Code for Construction and Acceptance of Ventilation and Air Conditioning Works” GB50243-2002 also states that the allowable air leakage for circular ducts is 50% of that for rectangular ducts.
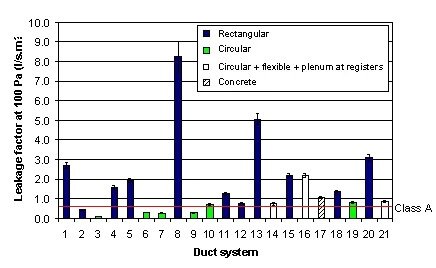
Figure 4: Measurements of air leakage rates in 21 Belgian buildings (Carrié et al, 1999)
3.2 Load Loss
The hydraulic equivalent is used to estimate the pressure loss of the rectangular duct system with the same hydraulic equivalent diameter. Despite their different cross-sectional shapes, they exhibit the same pressure loss along the way.
Figure 5 compares the pressure loss of a circular duct (D = 0.5m, U = 5m/s, Σ = 0.15mm) and a rectangular duct with the same area and flow rate. It is evident that in this case, the pressure loss of the rectangular duct is much greater than that of the circular duct, and as the aspect ratio of the duct increases, the pressure loss increases. This implies that greater fan power is required.
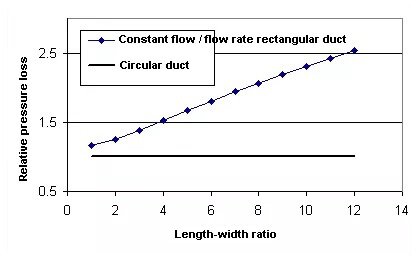
Figure 5: Comparison of pressure loss between rectangular duct and circular duct with constant flow and flow speed (flow = 1m³/s, v = 5m/s)
The concept of “hydraulic equivalent diameter” assumes that the average shear stress along the boundary of a rectangular duct must be consistent. In other words, the isokinetic line must be parallel to the boundary of the air duct. However, actual measurement results show that in a rectangular air duct, the velocity gradient along the diagonal line decays more slowly, and the velocity gradient along the center line decays more slowly.
Therefore, in theory, the equivalent hydraulic diameter should be used with caution in the following two cases:
- The flow is very small and the flow field cannot reach the state of complete turbulence.
- The cross-section of the tube is far from circular, that is, the rectangle has a large length-to-width ratio.
The experimental data also question the universality of the equivalent hydraulic diameter. JONES conducted a series of experiments on pressure loss in smooth rectangular ducts. The reanalysis of their experimental data is shown in Figure 6.
Despite the lack of data for 10
Griggsetal's experiments with rough rectangular ducts had similar results.
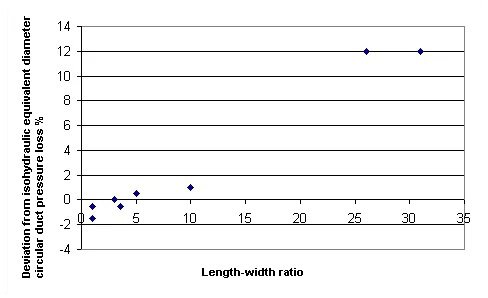
Figure 6: Comparison of pressure loss between smooth rectangular duct and circular duct with different length-width ratios
3.3 Maintenance Costs
To prevent sick building syndrome, you need to regularly clean your air ducts. Cleaning methods include the dry method (using a vacuum cleaner and brush) or wet method (using a long mop). In either case, cleaning circular ducts is easier than rectangular ducts.
4. Conclusions
The economic analysis of air duct systems is a challenging task. You must consider a number of factors, as the useful life of a duct system can often exceed ten years. In this case, a small improvement in design and quality can greatly increase the profitability of the investment.
Therefore, the use of circular ducts is a more economical solution. However, it is important to note that for reasons such as quietness and space, rectangular ducts are still recommended for some large-flow, large-size components of the air duct system, such as fresh air inlet openings and air handling device outlets. .