1. Annealing
1. Stress relief annealing
To eliminate residual stresses in the casting, stabilize its geometric size and reduce or eliminate distortions after cutting, it is necessary to perform stress relief annealing in the casting.
See too:
- 10 Different Types of Casting Process
- What is annealing? (7 types of annealing process)

The composition of the cast iron must be taken into consideration when determining the stress relieving annealing process.
When the temperature of gray cast iron exceeds 550 ℃, graphitization and granulation of part of the cementite may occur, causing a reduction in strength and hardness.
The presence of alloying elements can increase the temperature at which cementite begins to decompose to around 650℃.
Normally, the stress relieving annealing temperature of gray cast iron is 550℃, while low-alloy gray cast iron is annealed at 600℃ and high-alloy gray cast iron can be annealed at 650℃. The heating rate is generally 60 to 120 ℃ per hour.
Retention time is determined by factors such as annealing temperature, size and complexity of the casting, and stress relief requirements.
The following figure illustrates the relationship between retention time and residual stress at different annealing temperatures.

Fig. 2 Relationship between annealing temperature and time and internal residual stress
a) Composition (mass fraction) (%): C 3.18, Si 2.13, Mn 0.70, S 0.125, P 0.73, Ni 1.03, Cr 2.33, Mo 0.65;
b) Composition (mass fraction) (%): C 3.12, Si 1.76, Mn 0.78, S 0.097, P 0.075, Ni 1.02, Cr 0.41, Mo 0.58;
c) Composition (mass fraction) (%): C 2.78, Si 1.77, Mn 0.55, S 0.135, P 0.069, Ni 0.36, Cr 0.10, Mo 0.33, Cu 0, 46, V 0.04.
The cooling rate during annealing of stress relieving castings must be slow to avoid the development of secondary stress. The cooling rate is normally controlled at a rate of 20 to 40 ℃ per hour, and the temperature must be cooled below 150 to 200 ℃ before allowing the air to cool.
The following table shows stress relief annealing specifications for some gray iron castings:
Table 3 Stress-Relieved Annealing Specification for Gray Cast Iron Castings
Type of cast | Casting mass/kg | Casting wall thickness / mm | Charging temperature /°C | Rate of temperature rise / (C / h) | Heating temperature / C | Waiting time /h/ | Slow cooling speed (C/h) | Discharge temperature /C | |
Common cast iron | Low alloy cast iron | ||||||||
General casting | <200 | ≤200 | ≤100 | 500~550 | 550-570 | 4-6 | 30 | ≤200 | |
200-2500 | ≤200 | ≤80 | 500~550 | 550~570 | 6-8 | 30 | ≤200 | ||
>2500 | ≤200 | ≤60 | 500-550 | 550-570 | 8 | 30 | ≤200 | ||
Precision casting | <200 | ≤200 | ≤100 | 500-550 | 550-570 | 4-6 | 20 | ≤200 | |
200~3500 | ≤200 | ≤80 | 500-550 | 550-570 | 6-8 | 20 | ≤200 | ||
Simple or cylindrical castings, precision castings in general | <300 | 10-40 | 100-300 | 100-150 | 500~600 | 2-3 | 40-50 | <200 | |
100-1000 | 15-60 | 100-200 | <75 | 500 | 8-10 | 40 | <200 | ||
Complex structure and high precision casting | 1500 | <40 | <150 | <60 | 420~450 | 5~6 | 30~40 | <200 | |
1500 | 40-70 | <200 | <70 | 500-550 | 9-10 | 20-30 | <200 | ||
1500 | >70 | <200 | <75 | 500-550 | 1.5 | 30-40 | 150 | ||
Textile machinery small casting machine small casting machine large casting machine | <50 | <15 | <150 | 50-70 | 500-550 | 3~5 | 20~301 | 50-200 | |
<1000 | <60 | ≤200 | <100 | 500-550 | 3-5 | 20-30 | 150-200 | ||
>2000 | 20-80 | <150 | 30-60 | 500-550 | 8-10 | 30-40 | 150-200 |
2. Graphitization Annealing
The objective of graphitization annealing for gray iron castings is to decrease their hardness, improve their machinability and increase their plasticity and toughness. If the casting does not contain eutectic cementite or has only a small amount, low-temperature graphitization annealing can be performed. However, if the amount of eutectic cementite is substantial, high-temperature graphitization annealing is necessary.
(1) Low temperature graphitization annealing.
The graphitization and granulation process of eutectoid cementite in gray cast iron will occur when the material is annealed at low temperatures. This process will result in a reduction in hardness and an increase in plasticity.
Low temperature graphitization annealing of gray cast iron involves heating the casting to a temperature slightly below the lower limit of A C1 holding it at this temperature for a specified period of time to break down the eutectoid cementite and then cooling it at the oven.
The process curve is as follows:

Fig. 4 Low temperature graphitization annealing process curve of gray cast iron
(2) High temperature graphitization annealing.
The high-temperature graphitization annealing process of gray cast iron involves heating the material to a temperature above the upper limit of AC1 . This process decomposes the free cementite in cast iron into austenite and graphite. The material is then held at this temperature for a specified period of time and cooled in a specific manner depending on the desired matrix structure.
If a ferrite matrix with high plasticity and toughness is desired, the process specification and cooling method are as follows:

Fig. 5 High temperature graphitization annealing process of ferrite matrix
If a pearlite matrix structure with high strength and good wear resistance is desired, the process specification and cooling method can be carried out according to Figure 6 as follows:

Fig. 6 High temperature graphitization annealing process of pearlite matrix
2. Normalizing
The purpose of normalizing gray cast iron is to improve its strength, hardness and wear resistance, or to serve as preliminary heat treatment for surface quenching and improving the matrix structure.
The specification for the gray cast iron normalization process is shown in the figure below:
Typically, the casting is heated to the upper limit of A C1 , which is between 30°C and 50°C. This causes the original structure to transform into austenite.
After holding for a period of time, the casting is cooled by air (see figure a below).
For castings with complex or important shapes, annealing is necessary after normalizing to eliminate any internal stress.
If the original cast iron structure has excess free cementite, it must be heated to the upper limit of A C1 which is between 50°C and 100°C, to eliminate the free cementite through high temperature graphitization (see Figure b).


The figure below illustrates the impact of heating temperature on the hardness of cast iron after normalization.
Within the normalizing temperature range, the hardness of cast iron increases with increasing temperature.
As such, to achieve high hardness and wear resistance in normalized cast iron, a higher heating temperature within the normalization temperature range can be selected.

Fig. 8 Effect of temperature normalization on the hardness of gray cast iron
Note: The content of the elements in the figure is expressed in mass fraction (%).
The cooling rate after normalization affects the amount of ferrite precipitated and therefore the hardness.
The higher the cooling rate, the lower the amount of ferrite precipitated, resulting in greater hardness.
Thus, the cooling speed can be controlled (e.g. through air cooling, water cooling or mist cooling) to achieve the desired adjustment of the hardness of the cast iron.
3. Quenching and tempering
1. Tempera
The quenching process for cast iron involves heating the casting to a temperature of the upper limit AC1 plus 30-50°C, typically between 850°C-900°C, to transform its structure into austenite. The casting is then held at this temperature to increase the solubility of carbon in the austenite before quenching. Oil quenching is typically used for this process.
See too:
- 10 types of quenching methods in heat treatment process
Here is the revised version:
Castings with complex shapes or large sizes must be heated slowly to avoid cracking due to uneven heating. If necessary, preheating them to 500-650°C can also help prevent cracking.
Table 8.1 shows the effect of heating temperature on the hardness of cast iron. The chemical composition of cast iron listed in the table above can be found in Table 8.2.
Increasing the austenitizing temperature results in greater hardness after quenching. However, higher austenitizing temperatures also increase the risk of deformation and cracking of cast iron, as well as producing more retained austenite, which reduces hardness.
Figure 9 illustrates the effect of retention time on hardness.
Table 8.1 Effect of austenitizing temperature on hardness of gray cast iron after fire (oil itching)
gray cast iron | How to cast | HBW | |||
790°C | 815C | 845°C | 870°C | ||
A | 217 | 159 | 269 | 450 | 477 |
B | 255 | 207 | 450 | 514 | 601 529 |
W | 223 | 311 | 477 | 486 | |
D | 241 | 355 208 |
469 487 |
486 520 |
460 |
AND | 235 | 512 | |||
F | 235 | 370 | 477 | 480 | 465 |
Table 8.2 Chemical composition (mass fraction) (%) of various cast irons
Cast iron | TC | CC | Yes | P | s | Mn | Cr | No | Mo |
A | 3.19 | 0.69 | 1.70 | 0.216 | 0.097 | 0.76 | 0.03 | – | 0.013 |
B | 3.10 | 0.70 | 2.05 | – | – | 0.80 | 0.27 | 0.37 | 0.45 |
W | 3.20 | 0.58 | 1.76 | 0.187 | 0.054 | 0.64 | 0.005 | Trace | 0.48 |
D | 3.22 | 0.53 | 2.02 | 0.114 | 0.067 | 0.66 | 0.02 | 1.21 | 0.52 |
AND | 3.21 | 0.60 | 2.24 | 0.114 | 0.071 | 0.67 | 0.50 | 0.06 | 0.52 |
F | 3.36 | 0.61 | 1.96 | 0.158 | 0.070 | 0.74 | 0.35 | 0.52 | 0.47 |
- CT – total carbon content.
- CC – the amount of bonded carbon.
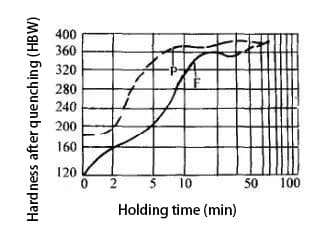
Fig. 9 Effect of the original structure of the cast iron metal matrix on hardness after quenching at 840°C for different retention times
The chemical composition (mass fraction) of this gray cast iron is as follows: 3.34% C, 2.22% Si, 0.7% Mn, 0.11% P and 0.1% S.
The hardenability of gray cast iron is influenced by factors such as size, shape, graphite distribution, chemical composition and austenite grain size.
The graphite in cast iron reduces its thermal conductivity, thus reducing its hardenability. The greater the amount of coarse graphite present, the more pronounced this effect becomes.
2. Temperament
The impact of tempering temperature on the mechanical properties of cast iron can be seen in Figure 10 below.
To avoid graphitization, the tempering temperature should generally be kept below 550°C, and the retention time for tempering should be calculated as t = (casting thickness (mm) / 25) + 1 (h).

Fig. 10 effect of tempering temperature on hardness and strength of quenched cast iron