Importance of press brake operator safety
As operators have to work very close to the brakes and hold the sheet metal tightly with their hands, their safety is continually at risk.
Therefore, it is important to minimize operator exposure to injury as much as possible.
Modern press brakes are equipped with safety systems with fixed photoelectric shields and laser protection systems to prevent operators' fingers from being crushed between the sheet metal and the punch tip.
For this reason, the safety devices on press brakes must always be active.
However, operators must pay special attention during work phases when safety devices do not stop the press brake automatically in case of danger.
During setup of the press brake, the machine must always be locked to ensure that accidental pressure on the pedal does not activate the upper beam, which must be in the neutral position.
During the work phases, operators must properly support and handle the plate; They must also avoid dangerous actions or actions that could impede the normal movement of the plate.
Operators must pay particular attention to ensure that they do not hold the sheet in such a way as to risk crushing their fingers between the edges.
sheet metal and the tip of the punch.
The correct way to hold workpieces:

Correct operation of the press brake
To start
Open the power switch → Hold the pedal to start the pump → Turn on the start switch → L-axis reset → D-axis reset → Commissioning
Install Punch & Die
First install the punch and then the die. To align them, loosen the two screws under the guide rail.
First increase the height of the punch and then slowly step on the pedal to check whether the mold is concentric. Always check the pressure gauge to ensure the pressure does not exceed the range.
Collecting and placing the workpiece
Do not place your hands between the bent part and the die to avoid pinching your fingers. When aligning the mold, keep your hands and any part of your body away from the space between the upper and lower mold.
When bending large pieces, be aware of the projection of the workpiece, as this may cause injury to your face.
If the press brake is being operated by two or more people, one of the operators must have control over the pedal and operate it carefully.
Safety Rules for CNC Press Brakes
Strictly comply with safety standards for machine tool workers and use the necessary protective equipment.
Before starting the press brake, carefully inspect the motor, switch, wires, and ground to ensure they are operating properly and safely. Make sure that the equipment control parts and buttons are in the correct positions.
Check the alignment and stability of the upper and lower dies and ensure that the positioning devices meet manufacturing requirements.
If the upper slide plate and position axes are not in the original state, restart the program.
If you hear an abnormal sound or experience a breakdown within 1-2 minutes after starting the press brake or after the upper slide plate has completed 2-3 movements, stop the press brake immediately. Only restart the press brake operation when everything is confirmed to be working normally.
During operation of the press brake, only one person must be in control. This requires close cooperation between the operator and power suppression personnel to ensure that the bend signal is given only after all personnel are in a safe position.
Adjust the slider stroke and select the upper and lower die and bending force based on the thickness and shape of the sheet to be bent. Choose the width V of the bottom die and check the bending force of the workpiece according to the bending force chart of the press brake on the right side of the machine. The bending force must not exceed the nominal force.
When adjusting the gap between the upper and lower molds, the slider must be parked at neutral. The gap must be adjusted from large to small.
The initial gap between the upper and lower molds should generally be 1mm greater than the thickness of the plate, with the gap greater than the thickness of the plate to avoid damage to the molds from insufficient clearance.
When folding with two people, designate one person to apply the brakes and turn off the power when exiting the machine.
Do not perform unilateral and single-point loads.
The sheet must be compacted to avoid warping and injuries during bending.
Do not place gauges or other objects between the upper and lower molds.
Cut the power and stop the press brake when adjusting the dies.
Ensure correct selection of bending dies and proper clamping of upper and lower dies to avoid injury during installation.
Do not allow material to touch the lower die when changing the opening of a variable die.
Choose the correct bending pressure, with eccentric loads being 1/2 less than the maximum pressure.
The length of the bending part should not be less than 1/3 of the length of the work table under maximum bending pressure.
Do not stand behind the press brake during operation.
Do not apply pressure to just one end of the sheet material.
If the workpiece or mold is misaligned during operation, stop the press brake and make corrections. Do not use manual correction during operation to avoid injury.
Do not bend ultra-thick iron sheets, hardened steel plates, advanced alloy steels, square steel or materials that exceed the performance of the press brake to avoid damage to the press brake.
Regularly check the alignment of the upper and lower molds and the pressure gauge indication.
If any abnormal situation occurs, stop the press brake immediately, investigate the cause, and notify relevant personnel for immediate troubleshooting.
Before shutting down, place a block of wood under the cylinder at both ends of the lower die and drop the upper slide onto the block.
Upon completion, exit the control system procedures, turn off the power, and clean the work site.
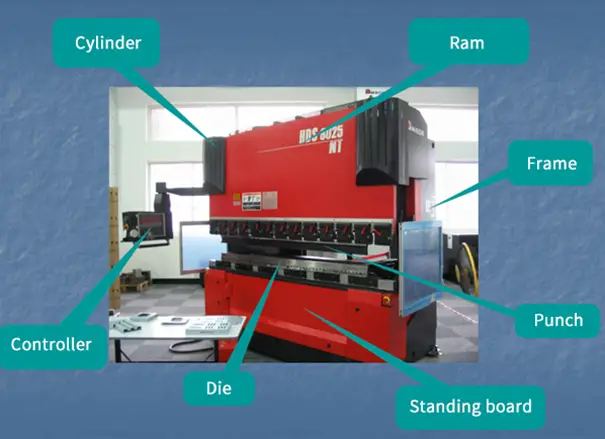
Press Brake Safety Operating Procedures
- Strictly follow machine tool safety operating procedures and use labor protective equipment as necessary.
- Before starting, carefully check whether the engine, switch, wiring and grounding are normal and firm, and check whether the control parts and buttons of the equipment are in the correct position.
- Check the coincidence and firmness of the upper punch and lower dies; check whether the positioning devices meet the requirements of the workpieces.
- When the ram and each positioning axis are not at the origin, run the return to origin program.
- After the equipment is started, it should idle for 1 to 2 minutes and the ram should move full stroke 2 to 3 times. If there are abnormal sounds or faults, stop immediately, eliminate the faults and only work when everything is normal.
- During operation, one person must command to ensure that the operator and the feeding and pressing personnel cooperate closely, and ensure that the coordinating personnel are in a safe position before giving the bending signal.
- According to the thickness and shape size of the bent sheet, adjust the ram stroke and choose the upper punch and lower dies and bending pressure. Select the size of the lower die mouth and check the bending strength of the workpiece. Be sure to refer to the bending force chart on the right side of the machine tool. The working bending force should not be greater than the nominal force.
- When adjusting the clearance between the upper punch and lower dies, the ram should stop at top dead center. The gap must be adjusted from large to small. Initially, the gap between the upper punch and lower dies may be about 1 mm greater than the plate thickness. The gap must be greater than the thickness of the plate to avoid crushing the mold due to no gap.
- When more than two people are bending over, one person must be designated to apply the brakes. Turn off the power when leaving the machine tool.
- Do not perform one-way or single-point loading jobs.
- The sheet must be pressed firmly when bending to prevent the sheet from lifting and injuring people during bending.
- Do not stack miscellaneous items and tools between the upper punch and lower dies.
- When adjusting the sheet pressing mold, turn off the power and stop working.
- Choose the bending die correctly, the clamping positions of the upper punch and lower dies must be correct, and avoid external injury when installing the upper punch and lower dies.
- By changing the variable bottom mold opening, no material can touch the bottom mold.
- Choose the bending pressure correctly. The pressure must be less than half the maximum pressure during discharge.
- The length of the part under maximum bending pressure should not be less than 1/3 of the length of the bench.
- No one may be behind the machine tool while it is in operation.
- It is strictly forbidden to fold the sheet at just one end.
- If the workpiece or mold is incorrect during operation, stop and correct it. Do not correct by hand during operation to avoid injury to your hands.
- Do not bend excessively thick iron plates or hardened steel plates, high-alloy steels, square steels and plates that exceed the performance of the plate bending machine, to avoid damage to the machine tool.
- Regularly check the coincidence of the upper punch and lower dies; whether the pressure gauge indication complies with regulations.
- Stop the machine immediately in case of abnormalities, check the cause and notify the relevant personnel to eliminate the fault in time.
- Before shutting down, place wooden blocks in the lower mold under the two side cylinders and lower the ram onto the wooden blocks.
- After completing the work, first exit the control system program, then turn off the power and clean the work area.
Wrap it up
Safety procedures must always be followed at all times, such as the use of personal protective equipment, namely gloves and clothing suitable for sheet metal work.
At the same time, they must ensure the correct positioning of the hands when supporting and subsequently processing the part, avoiding unnatural actions that impede the normal movement of the sheet.