Abstract: This article introduces several common bolt anti-corrosion methods in offshore projects, analyzes the problems encountered in actual construction, and introduces a new bolt anti-corrosion method.
EU Introduction
Bolted connection is a common connection method for offshore projects.
It is simple in structure, reliable in connection and convenient in construction and disassembly, so it is widely used.
However, due to factors such as installation location, installation method and degree of attention, the anti-corrosion of screws is often ignored.
The anti-corrosion coating of screws is easy to be damaged and difficult to repair during installation.
In the maintenance phase of the project, screws also need to be checked and replaced regularly.
After repeated screw disassembly and assembly, the original anti-corrosion layer is easily damaged.
In marine environments, screws are often surrounded by water vapor trapped in the screw holes.
In this way, the screws and surrounding metal structures will form corrosive galvanic cells, resulting in extreme corrosion of large cathodes and small anodes.
Because the anode is small, the corrosion rate of the screws is very fast.
The corrosion that occurs in the screw hole can hardly be seen on the screw surface in the early and middle stages, and only in the later stages can there be obvious corrosion products on the surface.
Therefore, the corrosion of screws has strong concealment, which will cause great potential safety hazards.
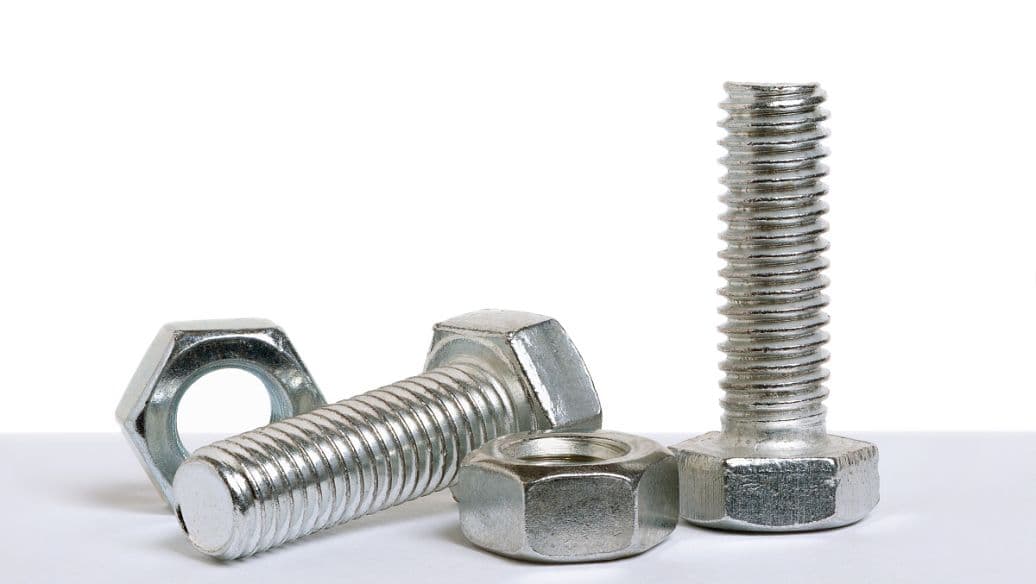
1. Common screw anti-corrosion methods
Common anti-corrosion forms of screws include electroplating, hot-dip coating, chemical surface treatment, paint, ceramic protective film, etc.
1.1 Electroplating
Electroplating consists of using the principle of electrolysis to attach a uniform coating layer with good adhesion to the screw surface.
The coatings are mainly zinc, chromium and other materials that can be used as sacrificial anodes.
When the coating is in good condition, the coating can isolate the screw from the corrosive environment and inhibit corrosion;
When the coating is damaged, the coating can be used as a sacrificial anode to protect the screws.
1.2 Hot dip coating
Hot dip plating is a process to dip the screw into the molten coating metallic liquid and then take it out for cooling to form a metallic coating on its surface.
The anti-corrosion principle of hot-dip coating is similar to that of electroplating, but compared with electroplating, the thickness of the coating is thicker, the adhesion between layers is better, and the corrosion resistance is stronger.
The common form of hot-dip galvanizing is hot-dip galvanizing.
1.3 Chemical surface treatment
Chemical surface treatment consists of placing the screw in some specific chemical solutions to change the surface of the screw and modify the surface of the screw to form a protective layer.
It can be divided into phosphate passivation, chromate treatment and oxidation treatment.
Chemical surface treatment is mainly used for stainless steel screws.
Chemical surface treatment is irreversible and once damaged, it is difficult to repair.
1.4 Paint
Painting is the most common and widely used anti-corrosion method.
It can be applied to the surface of screws with different construction methods to form a solid film with firm adhesion, certain strength and continuity.
The film can isolate the screw from the surrounding environment and can also play a role in cathodic protection if the coating contains zinc and other elements.
1.5 Ceramic protective film
The principle of ceramic protective film is to use the characteristics of high melting point, high hardness, wear resistance, corrosion resistance and good insulation of ceramics to spray molten state ceramic material particles on the surface of screws by spraying, forming a layer of ceramic film.
However, compared to other anti-corrosion methods, the construction of ceramic protective film is more difficult and expensive, which makes it difficult to popularize it in a large number of projects.
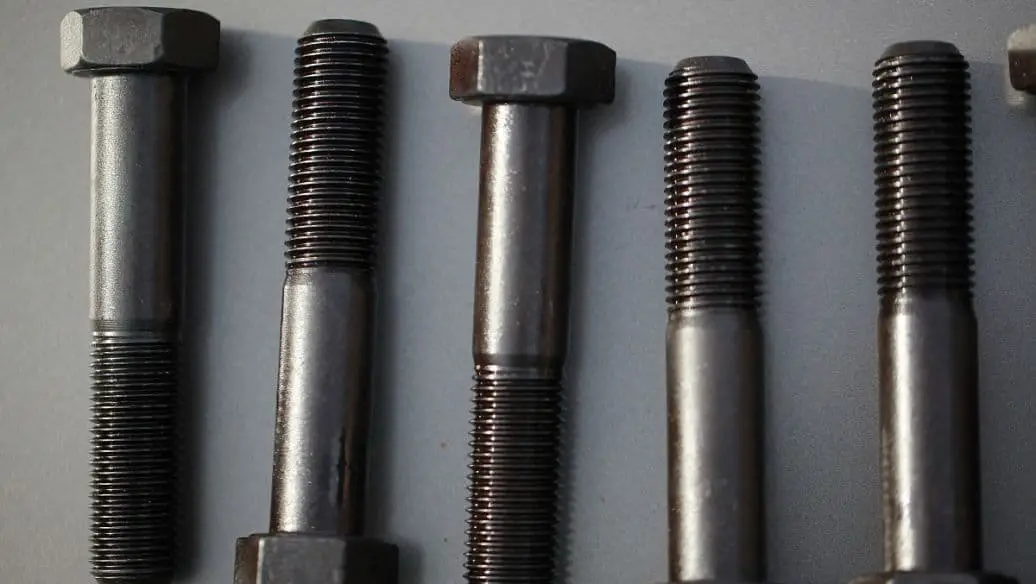
2. Screw anti-corrosion methods commonly used in offshore engineering
In the field of offshore engineering, bolts, as a common connection method, are widely used.
Therefore, when selecting the anti-corrosion shape of screws, it is necessary to consider not only the anti-corrosion performance, but also the cost and maintenance costs.
At present, in China's offshore engineering field, the most widely used anti-corrosion form of carbon steel bolts is generally zinc penetration.
Zinc penetration is prepared by embedding the screw in zinc alloy powder and holding it for a period of time after reaching a certain temperature, which will produce a metallurgical diffusion effect between zinc and iron.
Due to the special porosity of the zinc coating surface, it is necessary to seal the zinc coating surface within 2 hours after the zinc coating is completed.
Compared with zinc, zinc atoms diffuse into the screw surface, changing the composition and structure of the surface layer, making the zinc coating very uniform and dense, with strong adhesion and difficult to peel off under impact.
However, in the process of transportation, storage and installation, screws will inevitably cause irreversible damage to the zinc coating on the surface.
Damaged zinc siding is usually repaired with zinc-rich primer before installation.
However, the anti-corrosion performance of the repaired part is much worse than that of the original zinc penetration layer, so it is easy to form a galvanic corrosion cell with a large cathode and a small anode after screw installation, and corrosion often occurs here.
These repairs are only applicable prior to installation. During installation, the screws need to meet a certain tightening torque.
Therefore, the zinc coating is easy to be damaged during installation, and this damage cannot be repaired.
This buried the hidden danger of screw corrosion at a later stage.
3. A recommended anti-corrosion method for screws
In combination with the special offshore engineering service environment, the anti-corrosion method of zinc penetration coating and sealing paint is adopted, which has strong anti-corrosion performance and good resistance to mechanical impact.
However, sealing paint is used to seal the gaps of zinc penetration coating, which does not play an anti-corrosion role.
Zinc penetration coating itself is a sacrificial and consumable anti-corrosion coating, which will gradually dissolve in the marine environment and is subject to corrosion in the subsequent period.
Therefore, a new recommended practice is presented, namely coating with paint based on original zinc penetration plus sealing paint in the same anti-corrosive form.
Before installing the screws, the screws must be coated and reserved at both ends.
Paint both ends of the bolt and nut after installing the bolt.
3.1 Basic anti-corrosion requirements for screws
Before leaving the factory, screws must be galvanized and sealed with paint in accordance with standard requirements;
After arriving on site, installation and painting must be completed.
3.2 Surface treatment
Before priming is applied to the seal paint, all oils, greases, lubricants and other surface contaminants on the bolt surface must be removed with solvent.
3.3 Construction method
Can be sprayed or brushed on. Considering the particularity of the screw coating, it is recommended to adopt the brushing method to reduce unnecessary paint losses.
3.4 Coating system
The painting system for screws and nuts must refer to the surrounding service environment.
If it is a high temperature environment, the high temperature paint painting system should be selected.
3.5 Construction suggestions
To coat the screws, it is recommended to follow the following steps, as shown in Figure 1 and Fig.
3.5.1 Single Head Nut Bolt
(1) Cover the 2 thick places of the nut.
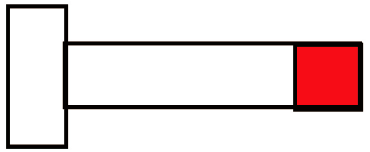
(2) Other parts must be painted with primer.
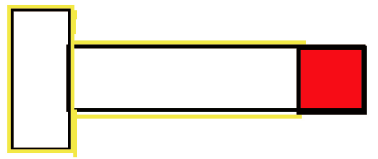
(3) Contact parts must be coated with intermediate paint and top coat paint.
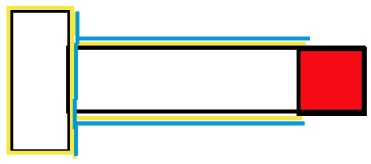
(4) Remove the cover.
After installing the nut, remove the grease from the surface, and do the rest according to the specified painting system (bottom, middle and surface).
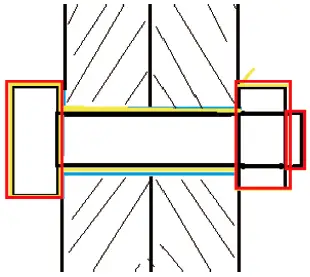
Fig. 1 Single-head nut screw
3.5.2 Nut screw
(1) Cover the 2 thick places of the nut.
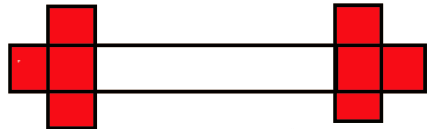
(2) Paint primer on other parts

(3) Contact parts must be coated with intermediate paint and top coat paint.
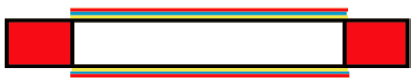
(4) Remove the cover.
After installing the nut, remove the grease from the surface, and do the rest according to the designated coating system (bottom, middle and surface).
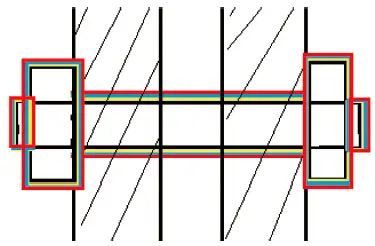
Fig. 2 Single-head nut screw
3.6 Advantages
With this anti-corrosion method, a layer of anti-corrosion coating can be formed on the surface of the sealing paint to resist some corrosion before the zinc coating begins to be consumed, which greatly reduces the consumption rate of the zinc coating.
At the same time, because the nuts of exposed parts are coated after installation, this may play a certain role in clogging the screw holes and reducing the ingress of water vapor.
The coating's double-layer protection and zinc penetration can effectively delay corrosion and reduce subsequent maintenance.
4. Conclusion
In short, this new recommended method of bolt anti-corrosion increased the cost of labor and materials in the construction phase of the project, although compared to other anti-corrosion ways, it increased the on-site casing construction process.
However, compared to the huge investment, super-long service time, high reliability and high safety of the entire offshore engineering project, it is completely feasible and recommendable from the overall project point of view.