As one of the main pieces of equipment in intelligent logistics, mobile handling robots have seen explosive growth in recent years. In the mobile robot market, in addition to the well-known AGV, RGV and IGV also play their role in the automated logistics system.
However, many do not have a clear concept of the differences between AGV, IGV and RGV. Through this article, we will clarify.
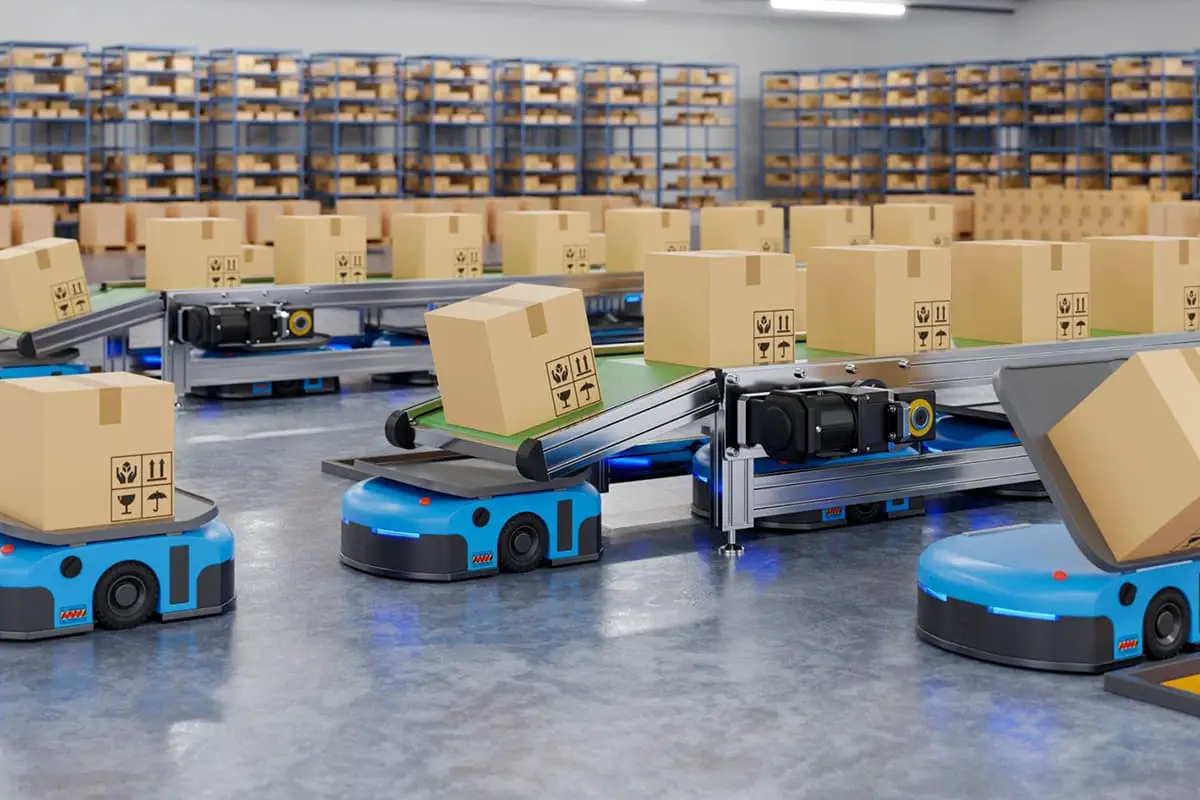
With the rapid growth of intelligent production, the ensuing fourth industrial revolution led to rapid development in the intelligent production industry. Mobile handling robots, as one of the main equipment in intelligent logistics, have shown explosive growth in recent years.
In the mobile robot market, in addition to the common AGV, RGV and IGV have also rapidly emerged in the field of automated logistics.
I. Meanings of RGV, AGV and IGV
RGV, or rail guided vehicle, is commonly used in high-density storage methods for vertical warehouses. The vehicle route can be designed to be as long as necessary, with no additional equipment required to enter the aisle when moving or transporting goods. This results in fast and safe operations that can effectively improve the efficiency of the warehouse system.
It can also be used for connection and transfer between parallel conveyor lines, providing logistical connectivity. Its main characteristic is having a physical track on the ground and traveling this inherent track with relatively unique routes.
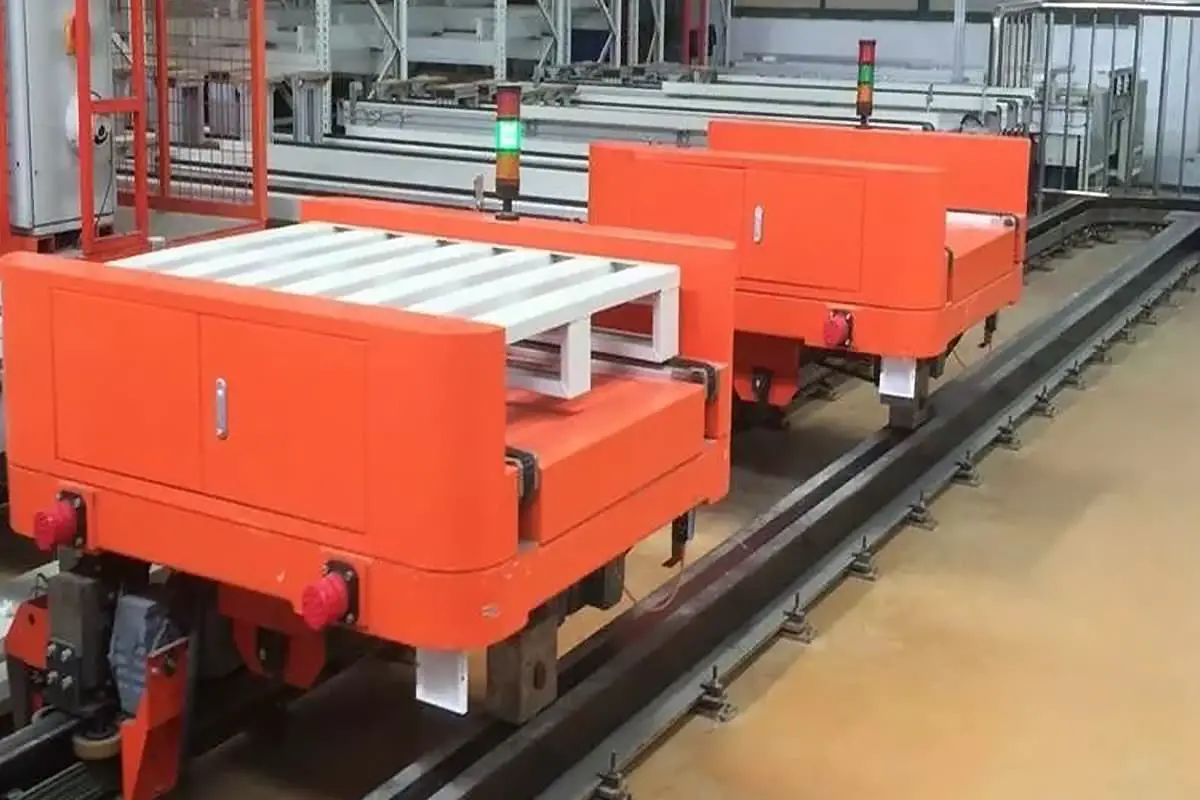
AGV stands for Automated Guided Vehicle . An AGV is a transport vehicle equipped with electromagnetic, optical or other automatic guidance devices. It can travel along a designated guidance path and has safety protection and a variety of transportation functions.
Compared to RGV, its track can go straight, turn, branch, merge and other shapes, demonstrating a certain level of flexibility.
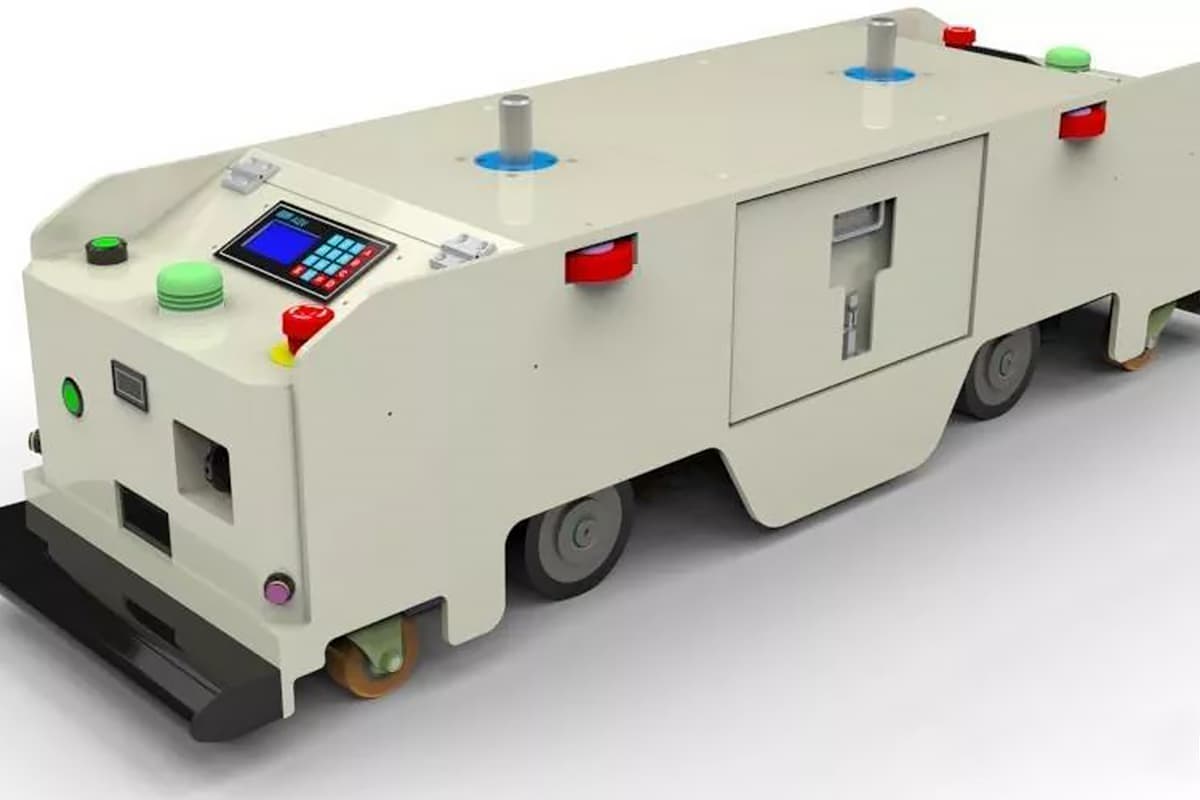
IGV, Intelligent Guided Vehicle , is a new concept that has been proposed in recent years. Compared to AGV, IGV has a greater degree of flexibility. You don't need fixed markers to drive and your path is flexible and changeable. It can be flexibly scheduled according to actual production needs, is simple to plan and meets the needs of most factories.
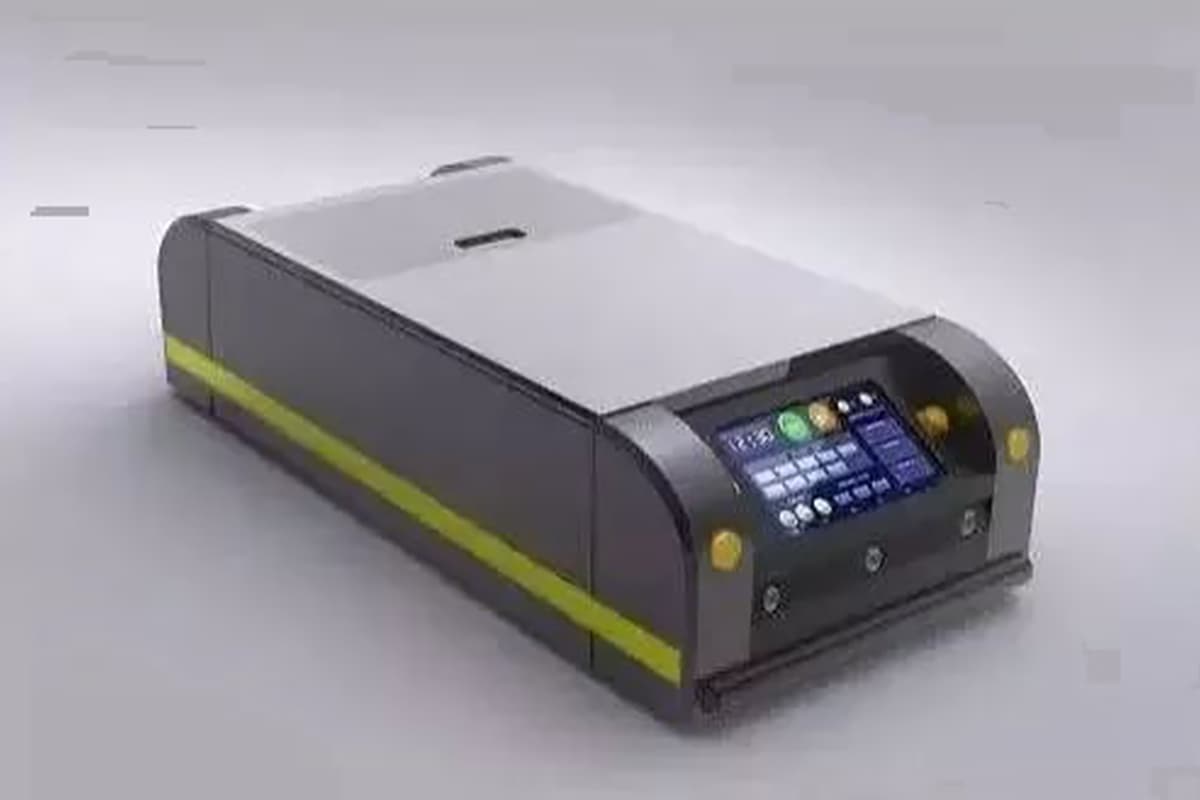
In summary, RGV, AGV, and IGV are all used to achieve automated material handling and transfer. But in terms of automation and intelligence, IGV > AGV > RGV. The RGV moves along the tracks, the AGV partially relies on markers such as barcodes and QR codes, while the IGV operates completely autonomously.
The progression from RGV to IGV also indicates a certain trend in the development of mobile robots: more intelligence, less dependence on auxiliary tools and a greater degree of flexibility.
However, this does not mean that IGV will replace other devices in the future. At least for now, in different application scenarios, they all have their own advantages. There is no absolute rule that high automation will eliminate low automation, or that high intelligence will replace low intelligence.
II. RGV Applicable Features and Scenarios
RGVs are widely used in logistics systems and workstation production lines. They can be automatically connected to other logistics systems such as storage stations, multiple storage stations, conveyors, elevators, line-side workstations and robots.
By transporting materials according to plans and instructions, they significantly reduce transport costs and improve efficiency.
RGVs operate on rails, so their application scenarios are relatively simple. They are commonly classified in two ways: by function, they are divided into assembly RGVs and transport RGVs, mainly used for material transportation and workshop assembly. By movement, they are divided into circular track and linear reciprocating types.
The efficiency of the RGV ring road system is high and multiple vehicles can work simultaneously. Linear reciprocating systems generally have only one RGV and their efficiency is relatively lower compared to circular track RGV systems.
Structurally, an RGV mainly consists of a frame, drive wheels, trailing wheels, front and rear bumpers, chain conveyors (or rollers), communication systems, electrical systems, and an external cover plate.
Due to the simple structure of RGVs, they demonstrate strong resistance to environmental disturbances and require less specific operation. They have strong operational stability, relatively fewer failures, lower overall maintenance costs and high reliability.
However, since RGVs can only move along the road, once the RGV route is determined, it is difficult and expensive to modify it. Therefore, its adaptability to different locations and its extensibility are relatively poor, although its operational efficiency is high.
III. AGV Applicable Features and Scenarios
AGV (IGV) systems are widely used in e-commerce warehousing and manufacturing industries. They are the best choice for many manufacturing companies to improve production efficiency and reduce production costs.
Compared to RGVs, they have a greater degree of automation and intelligence.
Its routes can be flexibly changed according to warehouse storage requirements and production processes, and the cost of changing operating routes is very low compared with traditional conveyor belts and rigid conveyor lines.
Main advantages of AGV:
- High working efficiency: AGVs can realize automatic loading functions. With safety redundancy considerations, they can operate continuously for 24 hours, significantly improving the efficiency of product material handling.
- Saves management effort: AGVs achieve full digitalization management, effectively avoiding human factors and improving management levels.
- Good system flexibility and scalability: Smart AGVs develop intelligent sensors, in addition to traditional position, velocity and acceleration sensors, they also apply machine vision, force feedback and other multi-intelligent sensor fusion technologies for decision control. Multi-sensor fusion technology has mature applications in existing AGV equipment systems.
- High reliability: Compared with the low efficiency of manual handling and the unpredictability of forklifts and trailers' paths, speeds and safety, the AGV's driving paths and speeds are controllable and stop accurately. This greatly improves material handling efficiency. Furthermore, the central AGV management system can monitor AGVs throughout the entire process, significantly improving reliability.
- High safety: AGVs have a comprehensive capability of safety protection, intelligent traffic route management, safety and collision avoidance, multi-level warnings, emergency braking, fault reporting, etc.
Compared to RGVs, AGVs have a wider range of application scenarios. They play a significant role in machining, storage, assembly and other manufacturing processes, and have even become one of the most symbolic configurations of modern smart factories.
AGV composition
The AGV is typically composed of the following components:
Chassis: Composed of the structure and corresponding mechanical devices, it serves as the basis of the AGV and as a basis for the installation of other components.
Battery and charging devices: Composed of charging stations and automatic charging units, the AGV can complete automatic charging online. Managed by the central control system, it allows continuous production 24 hours a day.
Steering system: Consisting of wheels, reduction gears, brakes, drive motors and speed controllers. It controls the normal operation of the AGV. Operating instructions are issued by the computer or manually, with speed, steering and braking adjustments controlled by the computer. For safety, the brakes are applied mechanically in the event of a power failure.
Guidance System: Receives directional information from the guidance system to ensure the AGV travels the correct path.
Communication devices: Facilitates the exchange of information between the AGV and the control console, as well as monitoring equipment.
Safety and Auxiliary Devices: To avoid collisions when the system malfunctions or when personnel cross the AGV's work route, AGVs often come equipped with obstacle detection and collision avoidance, alarms, visual alerts, and stop devices. emergency.
Transfer devices: Direct contact with the transported cargo, enabling the transfer of goods. Different transfer systems can be selected based on the task and site conditions, with the most common systems being rollers, forklifts and robotic arms.
Central control system: Consisting of a computer, task collection system, alarm system and related software. It mainly consists of a ground control system (upper) and an integrated control system (lower). The ground control system, a fixed piece of equipment in the AGV system, is primarily responsible for task allocation, vehicle scheduling, path management (lines), traffic management and automatic charging. Upon receiving instructions from the higher system, the onboard control system handles AGV navigation calculations, guidance implementation, vehicle movement, and loading and unloading operations.
AGV value
Characterized by wheeled movement, AGVs offer advantages over walking, crawling or other wheelless robots, including fast action, high work efficiency, simple structure, strong controllability and good safety.
Compared with other equipment commonly used in material transportation, AGVs do not require the installation of fixed devices such as rails or support structures, and are not limited by terrain, roads or space.
Therefore, they can fully demonstrate their automation and flexibility, achieving efficient, cost-effective and flexible unmanned production. Its advantages lie mainly in:
- High work efficiency;
- High level of automation;
- Avoid manual operation, leading to lower error rates;
- Automated loading;
- Convenience and reduced space occupation;
- Relatively low cost;
- Aesthetically pleasing, enhancing visual appeal and improving the company's image.
Key technologies and development trends of AGV guidance technology
As a branch of wheeled mobile robots, the main feature of AGV is automatic guidance. With the development of various technologies, AGV guidance technology is also constantly improving.
Commonly used guidance methods include: electromagnetic guidance, magnetic tape guidance, color tape guidance, laser guidance, inertial guidance, visual guidance, GPS guidance, and coordinate guidance.
Driving modes
The commonly used drive modes of AGV can be summarized into four types: single drive, differential drive, dual drive and omnidirectional drive. Depending on the number of wheels, there are mainly three- and four-wheel models. When choosing a model, it is selected based on actual road conditions and the functional requirements of the workplace.
Power supply
The power supply of traditional AGV is generally provided by batteries as energy storage carriers. The types of batteries that can be used by the AGV include: lead-acid/pure lead, nickel-hydrogen, nickel-cadmium, and lithium-ion batteries.
In recent years, with the maturity of battery technology, the application of supercapacitors in AGVs has been gradually promoted, and with the development of contactless power transfer technology, related products have replaced the traditional power supply mode of AGVs in some areas.
System control
It is mainly divided into ground control systems (upper) and onboard control systems (lower). The superior control system effectively controls multiple AGVs, optimizes task classification, dynamically plans AGV allocation and driving paths, and realizes intelligent traffic management.
The lower control system is responsible for navigation calculations, guidance implementation, vehicle movement, loading and unloading operations, etc., after receiving instructions from the higher system.
Current Status of AGV Market Development
The scale of the AGV market continues to grow. In addition to traditional AGV applications in large industries such as automobiles and tobacco, the electronics and home appliance industries will also lead AGV sales.
In addition, industries such as construction machinery, pharmaceuticals, electricity, chemicals, papermaking, defense and new materials have been promoted and applied.
In addition to storage and handling, the AGV has a wider range of applications in manufacturing companies. Although foreign brands still have a significant advantage, domestic manufacturers are also catching up quickly.
Key considerations and steps for AGV selection
Key points for AGV selection:
- Factoring in cost
- Choosing between AGV or AGC
- Navigation Method Selection
- Evaluating the AGV Control System
- Choosing the Right Service Provider
AGV selection steps
- Identify selection requirements
- Establish a selection committee
- Understand product information, define top supplier list
- Evaluate and bid
4. Characteristics and applications of IGVs
As a product of the continuous innovation and development of AGV technology, IGVs have further improved in terms of precision, safety, flexibility and environmental adaptability.
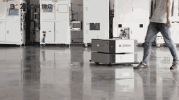
In terms of flexible guidance, traditional AGVs still rely on markers such as QR codes and reflectors. However, IGVs adopt new navigation techniques, relying on real-time scene maps, without the need for other fixed markers, making path changes simple and flexible.
IGVs are suitable for occasions that require greater flexibility. In addition to meeting regular transportation functions, they can selectively transport different functional modules (such as lifting modules, trailer modules, roller line modules, etc.) according to the customer's process flow, achieving the purpose of multi-purpose from a single vehicle.