Lately, I've noticed a lot of colleagues debating whether someone should learn 2D drafting software or 3D modeling software to pursue a career in mechanical design. This subject must be approached taking into account specific sectors in the field of mechanical design.
Firstly, we must recognize the fact that both 2D and 3D software are incredibly useful; otherwise, software companies would not invest heavily in its development. The creation of such products is driven by market demand.
Therefore, when considering whether to master 2D or 3D software, it is more crucial to consider the specific requirements of different industries rather than making generalizations.
Many educational institutions now emphasize training students in 3D modeling software, often neglecting 2D drafting software.
One reason for this bias may be that learning 3D software is inherently more challenging and appears to produce tangible educational results. It also looks more sophisticated and effortlessly appeals to those who lack independent critical thinking.
In contrast, learning 2D software is relatively simpler and neither instructors nor students want to “waste” a lot of effort and time on it. Unfortunately, this reflects a misconception of our higher education, which is disconnected from practical realities.
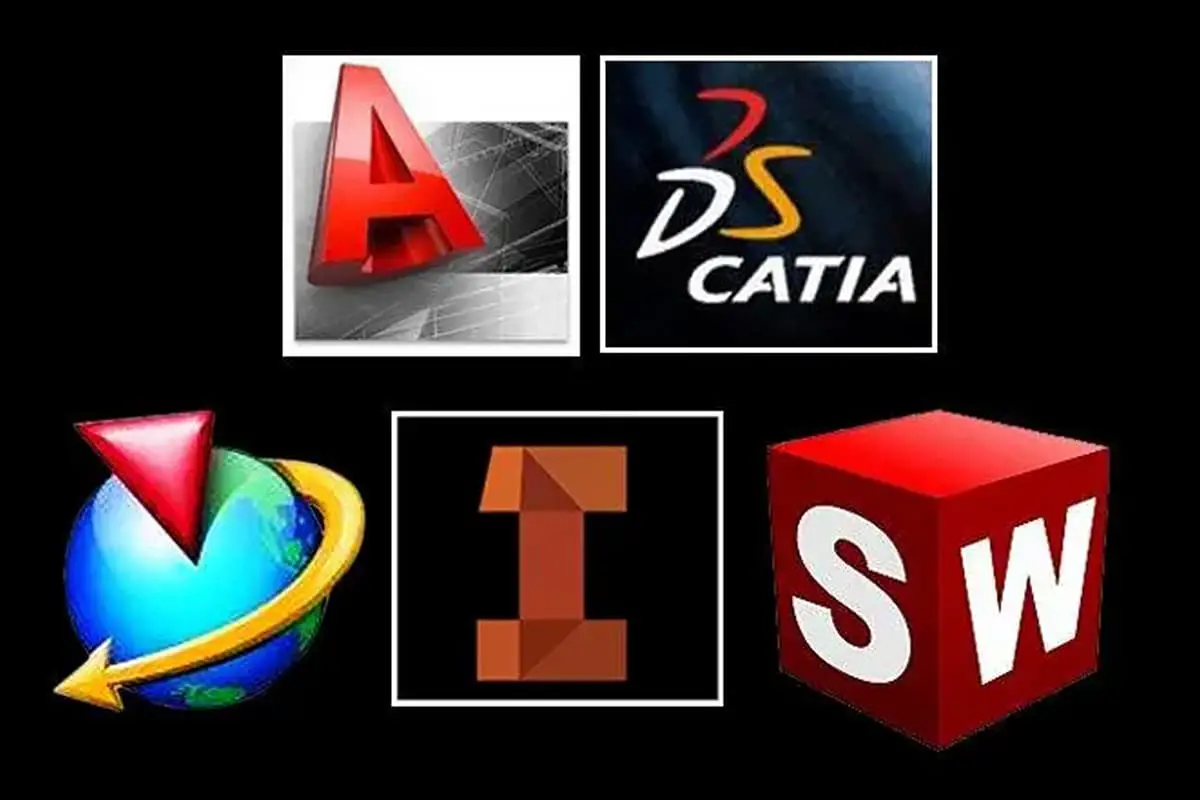
Let's examine the suitability of drawing software in various domains:
(1) 3D software
Well-known 3D software includes Pro/E, UG, Solidworks and Catia, predominantly used in areas such as mold manufacturing, automotive design and aerospace.
3D design capabilities such as surface modeling, aesthetic modeling, and parametric driving have significantly altered professionals' design habits and thought processes, firmly connecting the design phase to the final product.
This not only greatly increases design speed but also the quality of products. Additionally, 3D software features such as assembly simulation, interference checks and weight calculations ensure the integrity and consistency of designs.
The manufacturing processes characteristic of these industries, which produce parts mainly by stamping and injection molding, dictate the dominance of 3D software. In these sectors, we are not so much designing a part, but rather the cavity of a mold.
Guaranteeing part quality does not require a clear representation in a 3D model; Verbal and written communication with mold makers is often sufficient.
Reliance on 3D software alone can therefore manage the design process in these industries, as responsibility for ensuring part quality is transferred to mold manufacturers.
However, many college students are unaware of these processes and mistakenly believe that simply mastering 3D software equates to competent design.
Even if someone can use 3D modeling software proficiently, they are just drafting technicians with no true design thinking capabilities. True design skill is demonstrated by creating marketable products, not just drawing something and spinning it in software for display.
True design capability lies in understanding the manufacturing process of each part, ensuring the highest quality at the lowest cost and highest speed, and ultimately assembling those parts into a valuable, marketable product.
While 3D software excels at representing appearance and surface design, it falls short in providing comprehensive machining information such as geometric tolerances, tolerances, and heat treatment specifications.
Discussing drawings without this machining information is meaningless. This is my point of confusion with current college education – whether instructors teach students how to denote and explain these tolerances, allowances, and heat treatment requirements.
Many student drawings I have reviewed include only basic dimensions, with all other specifications conspicuously absent, some even missing title blocks and borders. Can they be called drawings?
And yet, they have the audacity to send them off for manufacturing. It's one thing to be shameless, it's another to be openly irresponsible.
(2) 2D software
Among two-dimensional (2D) software, CAD is undoubtedly the most familiar to us. In my previous articles I recommended CAXA, a 2D software that I really like to use.
Let's discuss the advantages and disadvantages of 2D software: The main advantage is the ability to express part dimensions, geometric tolerances, roughness requirements, heat treatment specifications and other technical requirements in a single drawing clearly and effectively.
Process engineers and operators can easily understand all of a part's manufacturing requirements and information from a drawing, allowing them to complete the manufacturing process more efficiently. This is an advantage that is difficult to replace with 3D drawings.
Furthermore, 2D software brings significant benefits during the design phase of a project, which often involves an incessant cycle of modifications – a fundamental aspect of a design engineer's job that is elusive and eternally “painful”.
Modifying a 2D drawing is much more convenient and faster than changing a 3D model (this is my personal opinion, so pessimists, keep quiet).
Therefore, 2D drafting software is indispensable in the structural mechanical design process.
If someone claims they can produce a structural product using only 3D software (without producing 2D drawings), they are being false, as fabrication drawings must include notations for external dimensions, geometric tolerances, roughness requirements, heat treatment specifications, and other details technical. —something pure 3D models cannot provide. For example, take a look at the drawing below:
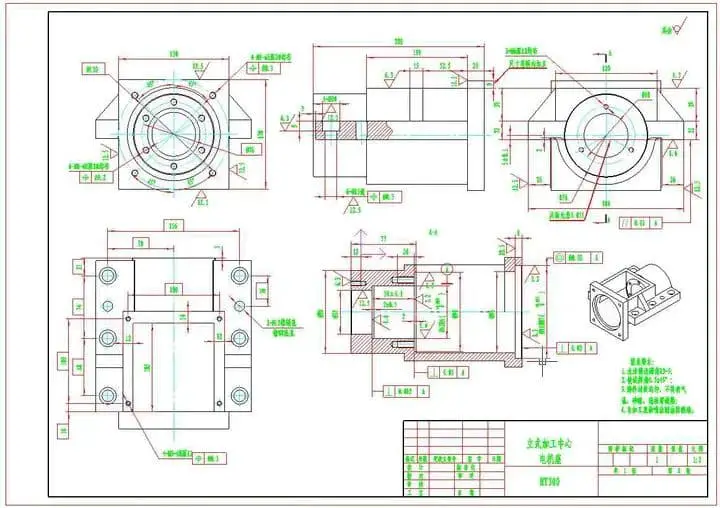
From this drawing, we can clearly understand the part's external dimensions, geometric tolerances, roughness requirements, heat treatment specifications and other technical requirements. However, what can you discern from the 3D model in the bottom right?
Other than a three-dimensional representation, you can't see anything else – you don't know which surface needs to be machined or which hole needs to be drilled, nor do you understand the roughness levels these surfaces and holes need to achieve, their geometric tolerances, or the type of heat treatment that the part must undergo before machining begins.
These details are crucial to the manufacturing of the part and represent the true capabilities of a mechanical design engineer. The ability to define these dimensions, tolerances, roughness and heat treatment specifications effectively, cost-effectively and with high quality is the pinnacle of a design engineer's skills and what differentiates him or her from a draftsman.
So what are the disadvantages of 2D drawing software? See the advantages of 3D design software to find out. The strengths of 3D drafting software are precisely where 2D drafting software falls short.
Therefore, a competent design engineer must be proficient in using both types of software to support their design work and professional development.
Conclusion
Thus, 3D and 2D drafting software are useful, each focusing on different domains and industries. You should train your software skills according to the characteristics of the industry you hope to enter in the future.
But the future is far away and who knows what you will end up doing?
My advice is to learn a little bit of everything – have some knowledge in all areas to avoid finding yourself in the unfortunate situation of realizing the value of knowledge too late.