Aluminum alloy has high specific strength, good corrosion resistance, high toughness and easy processing.
It is widely used in various high-strength structural parts of aircraft, missiles and rockets.
It is an important material in the aerospace field.
A certain product model is extruded from 7A04 aluminum alloy.
After heat treatment of the product in an oven, it was found that there were defects at the bottom of the bullet.
There was delamination and slag falling into the muzzle from the bottom of the bullet.
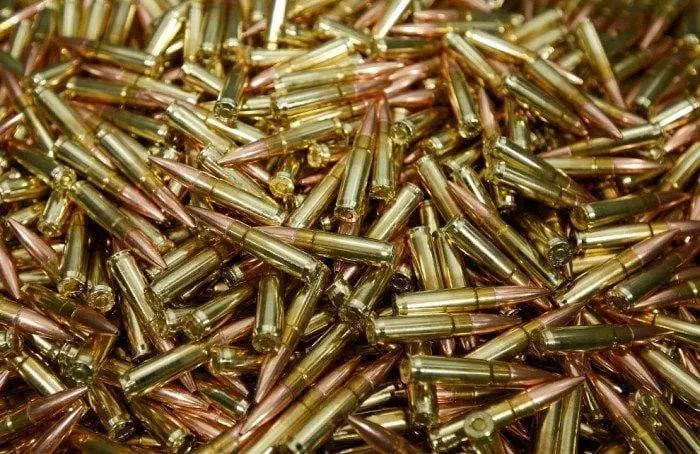
Circular cracks formed along the circumference were visible on the conical part of the outer surface, and circular cracks formed along the circumference were also found at the arc transition of the inner hole.
To find out the causes of defects in the bottom of the bullet, the causes of defects in the bottom of the aluminum alloy casing are analyzed.
1. Fault analysis and location
In combination with the bullet bottom processing process, the cartridge bottom defects are analyzed according to the fault tree analysis method.
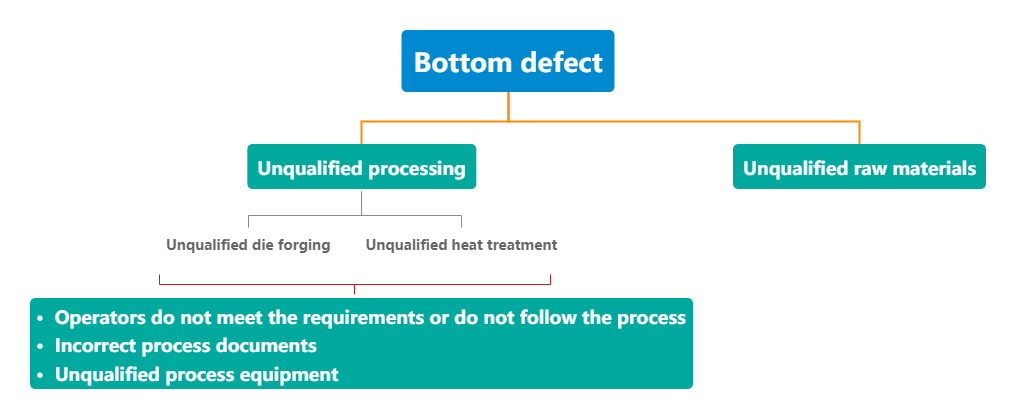
Figure 1 Projectile Lower Defect Fault Tree
(1) Personal
After training and assessment, the operators assumed their positions with certificates and are all experienced operators.
(2) Raw materials
The raw material is 7A04 bar, and the chemical composition, mechanical properties, metallographic structure and macrostructure of the received acceptance are all qualified.
(3) Crafts
Ammunition bottom processing technology has been used for many years, and the process parameters are reasonable and effective.
Process flow: preparation before production → feeding → forging → rough machining → heat treatment → finishing machining;
The heat treatment method of aluminum alloy is T6 treatment, in which the solution treatment quenching temperature is 470 ℃.
(4) Equipment
After checking the heat treatment equipment, the operator was informed that the color of the part was red when the bottom of the furnace pump came out, which had not happened before.
(5) Fault location
Combined with the fault tree for troubleshooting and analysis, the possible personnel, materials and technology problems were eliminated, and it was basically determined that the defects at the bottom of the pump were caused by problems in the heat treatment equipment.
2. Physical and chemical inspection
To discover the cause of the defect, the anatomy of the bottom of the bullet with obvious defects was selected for physical and chemical inspection.
(1) Macro observation
Cut along the axis of the bottom of the shell.
According to the requirements of GB/T 3246.2-2012 structural inspection methods for deformed aluminum and aluminum alloy products Part 2: Inspection methods for macrostructure, the macrostructure of the failed aluminum alloy shell bottom was analyzed.
After engraving, it was found that there were a large number of cracks on the test surface and cracks extending inward at the inner wall arch transition.
At the same time, a coarse-grained ring with a depth of 2.5 mm was found on the surface of the outer cone.
There were cracks at the interface between the coarse-grained ring and the substrate, and longitudinal cracks in the lower central part.
(2) Microstructural analysis
Take the metallographic sample at the arc transition from the bottom of the bomb.
According to the requirements of GB/T 3246.1-2012 inspection methods for microstructure of deformed aluminum and aluminum alloy products Part 1: inspection methods for microstructure, after grinding the sample, use mixed acid aqueous solution for etching.
The microstructure is shown in Fig.
After observation, the remelted eutectic phase appears in the microstructure of the sample, and there are many structural features similar to the remelted triangle, which are enriched at the grain boundary.
It has the characteristics of widening grain boundaries and is a typical overfired structure.
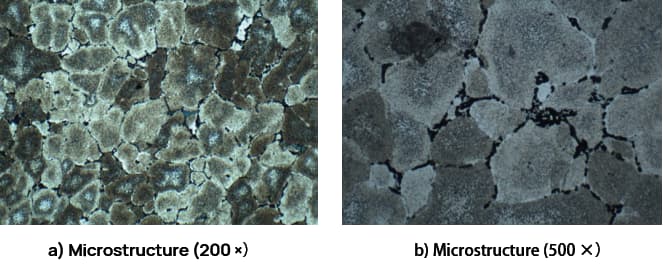
Fig. 2 microstructure of the bullet bottom
3. Oven temperature detection
In order to find out the cause of excessive burning, the temperature field in the heat treatment furnace during charging is detected according to the method GB/T 9452-2012 for determining the effective heating zone of the heat treatment furnace.
The No. 5 measuring point of the test equipment is connected to the thermocouple, and the other 5 measuring points are placed on the workpiece.
The positions of the measuring points are shown in Fig.
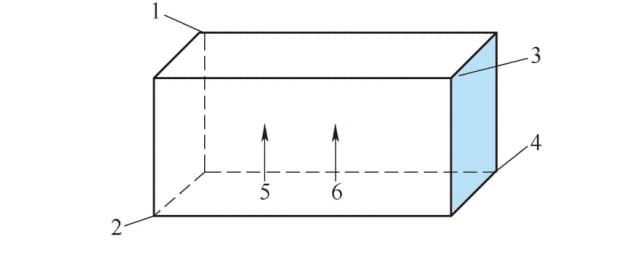
Fig. 3 Oven temperature detection position
Note: 1~6 are temperature measurement points
Place measuring points according to Fig. 3 to test the temperature field in the heat treatment furnace.
The oven temperature is set at 470℃ and the temperature is maintained for 70 minutes.
Record the temperature change of each measurement point.
See Table 1 for test results.
Table 1 heat treatment furnace temperature detection results (℃)
To point | Maximum | Minimum |
1 | 507.68 | 488.61 |
two | 475.77 | 473.93 |
3 | 521.13 | 502.29 |
4 | 504.43 | 488.89 |
5 | 525.04 | 500.33 |
6 | 491.57 | 481.32 |
Equipment temperature setting | 470 |
Test results: the difference between the maximum temperature and minimum temperature in the oven exceeds 50℃, and the temperature fluctuates greatly.
The temperature measured in the oven is inconsistent with the set temperature, and the temperature in the oven is higher than the set temperature.
Immediately, the heat treatment furnace was renovated.
It was found that the lining plate on the right side of the inner wall of the oven was cracked and the gap was large.
The furnace fan was loose and the speed was very slow.
4. Analysis and discussion
The maximum temperature of the heat treatment furnace is 525.04 ℃, which is 489 ℃ higher than the melting point of aluminum alloy 7A04, Al + T eutectic low melting point (Al 2 mg 3 Zn 3 ), which will make causing the grain boundary of the aluminum alloy and the insoluble phases such as Al 6 (MnFe) and AlMnFeSi in the crystal to form clusters and form molten balls again with the insoluble phases agglomerated as the core at the local grain boundaries, resulting in structure burned.
The burnt structure makes the grain boundaries of the aluminum alloy brittle and reduces strength.
In the subsequent quenching and cooling process, it is subjected to high-strength stresses and produces cracks, which reduces the fatigue and corrosion properties of the part.
Therefore, aluminum alloy parts after heat treatment cannot suffer from excessive burning, and coarse dendritic segregation can also form a band structure in subsequent processing, resulting in part failure in the process of use.
It can be seen from the analysis process that the reason for the defects at the bottom of the pump is that the abnormal temperature of the heat treatment furnace causes the quenching heating temperature to be too high, which causes the material to be burned too much .
The existence of intracrystalline segregation and redundant brittle phases significantly reduces plasticity and causes the material's strength to decrease.
During water cooling, cracks are formed at stress concentration points such as arc transition, sharp corners and coarse-grained rings, and cracks occur under the action of internal stresses.
5. Conclusion and improvement measures
1) The reason for pump bottom defects is that the temperature in the heat treatment furnace is too high, which leads to excessive burning of materials and early failure of products.
2) Repair the faulty equipment, weld the inner lining of the heat treatment furnace, replace the furnace fan and repair the sealing parts.
3) Strengthen management, regularly check the heat treatment furnace, and use infrared thermometer to test the actual temperature in the furnace before the workpiece is placed in the furnace.